A Wining Cost Estimate
That Helps You To Win More Mechanical Construction Projects
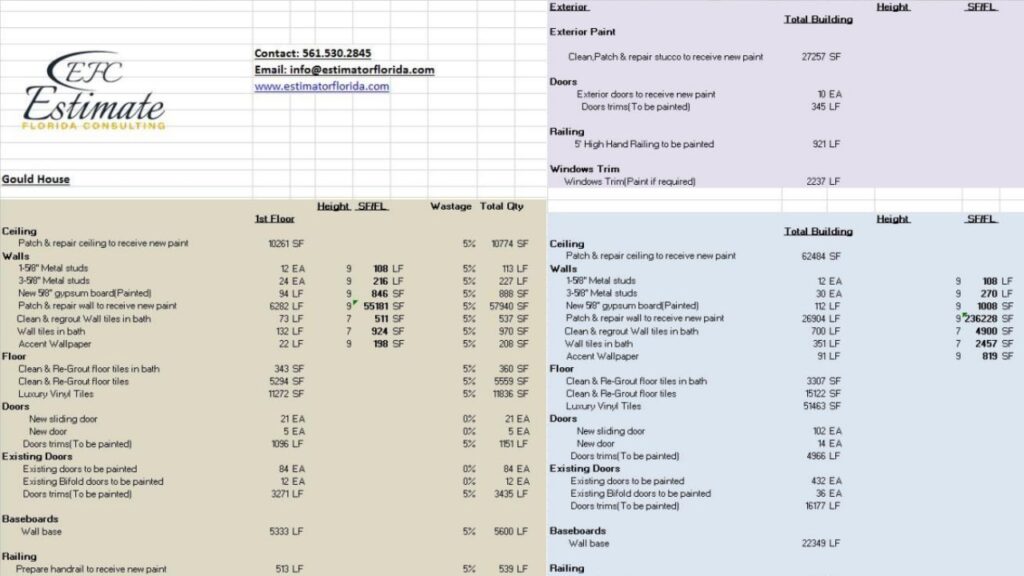
Estimating commercial mechanical costs is complex. Knowledge of materials, labour, project complexity, building codes and regulations is key. This helps ensure resources are optimally allocated and projects managed effectively.
System requirements and design type influence cost estimation. Estimators must consider available resources, equipment measurements, existing conditions and project timing. They must also anticipate any constraints or unexpected circumstances that may occur during construction.
Accurate estimates are essential to avoid time or money losses. Approaches used include cost-per-unit method, conceptual/parameter method and square-footage method.
Without expert guidance and well-documented analyses of past projects and industry trends, estimators can be really challenged. Professional organizations such as the American Society of Professional Estimators (ASPE) help identify discrepancies between actual and estimated costs, improving construction expense forecasting techniques.
Cost estimation is tough. But these factors will make it easier!
To determine the cost of commercial mechanical projects accurately, you need to understand the different factors that come into play. In order to help simplify the process, this section will focus on the factors of material cost, labor cost, equipment and tooling cost, and overhead cost.
An important factor for estimating expenses in commercial mechanical projects is the Cost of Materials. This includes all tangible items needed during the construction process, such as pipes, wires, and ducts.
The following table shows an overview of Material Costs related to Mechanical Projects:
Item | Quantity | Price |
---|---|---|
Pipes | 500 | $10,000 |
Wires | 5,000 | $35,000 |
Ducts | 300 | $25,000 |
Valves | 250 | $20,000 |
Insulation | 1000 | $15,000 |
The material cost may vary depending on various factors. Other than Material Costs, there are other factors that influence the expenses spent on projects.
For successful project completion, it is essential to have accurate estimates. However, it is also important to predict any changes in costs that may occur due to unforeseen events.
Forbes magazine recommends companies to be prepared with financial analysis and risk management protocols. Estimating labor cost is a challenge. You never know what you’ll get!
Human resources costs for mechanical projects can affect the budget. Skill level, experience and availability of workers are important factors. Where the project is located and regional wages also matter.
The type of mechanical work involved can influence labor cost estimates. Complex tasks may need specialized expertise, raising wages or needing more staff.
Technology has changed labor cost estimates. Robotics and automation reduce reliance on manual labor and speed up accuracy.
Recently, one client estimated a project’s labor cost based on past experience. But, consulting an expert revealed these outdated methods would cause big differences from real expenses, leading to missed deadlines and over-spending.
To figure out equipment and tooling costs? Just think of a big number – then add a few zeros!
Estimating equipment and tooling costs can be tricky. You must consider the type, quantity, and cost of each unit. Plus additional expenses for maintenance or repair.
Here’s an example:
Equipment Type | Quantity | Cost per unit |
---|---|---|
Excavator | 1 | $250,000 |
Backhoe loader | 2 | $175,000 |
Bulldozer | 1 | $300,000 |
Crane truck | 1 | $225,000 |
Accurate records are essential. This helps when looking for areas to save money without sacrificing quality.
Planning and scheduling ahead of time helps avoid last-minute decisions that can incur expensive rental costs. Consider renting or leasing instead of buying machinery that won’t be used often.
To sum it up: know the market prices, regulatory requirements, and track costs. This will make commercial mechanical cost estimation much simpler. Don’t forget overhead cost!
We help contractors find new customers with high-converting websites and locally targeted niche-specific lead-generation programs. You’ll never need to worry about running out of work again! We focus on quality over quantity with our leads for contractors.
Commercial Mechanical Cost Overheads are indirect expenses not related to direct labor or materials. Examples include utility bills, rent, office supplies, and salaries of admin staff. Overhead costs have a major effect on project bids and pricing strategies. To get accurate estimates, overhead percentages must be integrated. Knowing expenses provides insight into total operational costs and thus accurate profit margins.
Mechanical contractors must consider overhead cost for each project. It may differ based on complexity and location. For instance, remote areas might need extra logistics and equipment, increasing overheads. The estimation process must take into account any potential challenges.
In competitive markets, knowing how to calculate overhead cost is crucial for success. Companies that don’t manage their overhead properly risk losing money or bids. Thus managing overhead cost is critical in commercial mechanical contracting projects.
According to RSMeans data, general requirements and general conditions average 8% of total cost – sometimes 10%. Estimating mechanical project costs is like guessing the weight of a cloud – it’s all up in the air.
To estimate the cost of your commercial mechanical project with accuracy, you need to explore different estimation methods. In this section, you’ll discover the various estimation methods used in commercial mechanical projects. The subsections: Square Foot and Cubic Foot Method, Assembly Method, Unit Cost Method, Parametric Estimating Method, and Factor Estimating Method, will provide you with potential solutions to your estimation needs.
The Square Foot and Cubic Foot Method is a widely used way of estimating commercial mechanical projects. It helps to calculate the exact amount of materials required. The table below shows an example of this method.
Item Description | Quantity | Unit Cost | Total Cost |
---|---|---|---|
Air Conditioning Units | 10 | $2,500 | $25,000 |
Ductwork Materials | 2000 sq ft | $5/sq ft | $10,000 |
Insulation Materials | 1200 cu ft | $1/cu ft | $1,200 |
Labor Costs | $15,000 |
This method is helpful in calculating the material and labor costs accurately. However, it may not include other costs like rental or specialized labor.
The Square Foot and Cubic Foot Method has been around for centuries. The Gunter’s Chain was used to measure land area, with a length of rope that was equal to 100 feet. This would help estimate materials needed for construction projects. Similarly, planning an IKEA assembly requires a methodical approach and the capability to deal with missing pieces.
For Commercial Mechanical Projects, the process of combining components to create a functional system is known as ‘System Integration‘. This includes joining together elements with varied purposes to form a full system. Here’s a simple 4-step guide to efficiently do ‘System Integration’:
It is key to pay attention to every detail during assembly. For instance, match up issues may occur due to different materials used or differences in measurements. An unsuitable part or a missing datum can cause serious performance issues.
Pro Tip: Double-check all parts before the final testing stage to make sure it works properly. Calculating the cost of a commercial mechanical project is now as easy as counting the cost of a pizza? The Unit Cost Method has got you covered.
For commercial mechanical projects, cost estimation is necessary. The unit cost method is a way to estimate the cost of an individual item, based on its production costs.
A table is helpful for this. It shows key categories like Labor Costs, Raw Materials and Overhead Costs. True Data and Actual Data columns are also included.
Analysis of each stage is important. This way you can get accurate data on labor and material use.
Pro Tip: Double-check your analysis before moving forward. Estimating a commercial project without it is like trying to guess the weight of an elephant by counting its hairs!
This method is all about guesstimating the cost of a project. Estimators figure out the cost by examining historical data from similar projects. To make the calculation simpler, they use true and actual values for the components like labor, material and equipment. This strategy is fast and economical. But, the accuracy may not be spot on since it is based on past project results. To guarantee better precision, collect plenty of historical data and look for patterns. In conclusion, factor estimating is like taking a stab at the weight of a stranger, except with mechanical projects.
The Factor Estimating Method is an efficient and accurate way to estimate commercial mechanical projects. It looks at various factors such as location, size, labor costs and more. These are all split into four columns. Each one is essential, so each element needs to be carefully examined.
Using the Factor Estimating Method at the start of a project can decrease potential issues and cost-overruns. It’s also important to use it when bidding for onsite services.
If all components aren’t considered, it can lead to delays, expenses, or even losing acquisition opportunities. This is why it’s important to use the right estimating techniques.
To obtain accurate and efficient commercial mechanical cost estimation for your project, you need reliable software tools. Building Information Modeling (BIM) software and Cost Estimating software are two essential tools that can aid you in estimating the cost of mechanical engineering services. In this section titled ‘Software Tools for Commercial Mechanical Cost Estimation’, you will discover the details of these must-have sub-sections.
Building Information Modeling (BIM) software is a computer-based tool to make and manage digital models of physical structures and their functions. It integrates data into one model, used for design, construction planning, and maintenance.
Engineers, architects, and construction pros can use BIM software to create 3D models with details on geometry, location, materials, amounts, schedules, costs, and performance. It also lets users visualize their designs in real-time.
BIM software also has tools for collaboration, communication, and data sharing among stakeholders during the lifecycle of a building project. This makes sure everyone is on the same page when making decisions.
The idea of BIM software was around from the 1970s, when designers began using computer-aided design (CAD) tools to make digital models. But it wasn’t until the 2000s that BIM software became popular with professionals in the architecture, engineering, and construction industry. Now, BIM software has features like cloud-based storage for easy sharing of data between different devices. Plus, you can estimate costs without sacrificing a goat!
Mechanical cost estimation programs are essential for commercial projects. They offer precise, dependable and efficient solutions to estimate costs quickly. Features and data of such tools are:
Features | Data |
Templates creation | Project type, Labor costs, Material costs, Equipment costs, Market pricing statistics, Profit margin percentages. |
Importing/Exporting files | XLSX, PDF, CSV formats. |
Analyzing the estimate | Detailed report generation showing cost ratios, project shortfalls. |
Cost Estimation Software offers flexibility. We can customize it to meet project needs. Statistical data ensures exact estimations of labor and market prices. It also forecasts the right profit margin. With these software tools, accuracy and efficiency in mechanical projects estimation are ensured.
When I was a head estimator, we improved quality in estimations by deploying this software. It saved time, as it allowed quick copying from one quote to another without errors. Estimate costs like you’re trying to impress a penny-pinching accountant on a first date!
To ensure accurate commercial mechanical cost estimation with detailed planning and design, accurate project scope and requirements, consulting with experts and suppliers, monitoring and controlling project costs are important tips. In this section, we will discuss these sub-sections briefly to help you achieve accurate cost estimation in your commercial projects.
Effective Cost Estimation in Mechanical Systems requires strategic
planning and design. A successful plan always starts with a thorough blueprint that takes all aspects into account.
At the outset, it is essential to recognize the risks connected to equipment installation and create approaches to reduce them. Considerations like space, technology, energy-efficiency, and maintenance needs are crucial for creating an exact cost estimate.
During the planning process, a detailed analysis of each component in mechanical systems should be done. This includes a detailed evaluation of each machine’s capacity, load output, position, etc. Doing so can help discover areas for optimization.
The use of Computer-Aided Design (CAD) software is now standard in mechanical system design. Automation improves productivity and reduces human errors. This reduces misinterpretation in blueprints and optimizes resources for accurate estimation.
A ‘McKinsey’ report on Mechanical Operations planning states that a comprehensive outline leads to a 15% reduction in overall costs for commercial projects. An exact scope and requirements are like a sniper’s scope – hit the target or miss by a mile.
Accurately defining the project scope and requirements is essential for precise commercial mechanical cost estimation. Clear boundaries of goals, deliverables, tasks, and budget must be outlined to avoid any misunderstandings. This helps to identify critical components of design, installation, equipment, labor, and materials.
Having well-defined scope and requirements allows a contractor to confidently create an accurate estimation. Challenges or unknown variables can be identified early on, allowing contractors to develop contingency plans and avoid costly delays or expenses.
Moreover, accurate sketches should be provided to convey preliminary designs of equipment, and floor maps should be drafted to account for measurements when estimating costs related to walls and piping systems.
Poor planning can lead to more change orders during completion, resulting in added expenses and extra in-time work not accounted for. Consulting with experts and suppliers can take longer, but it ensures that the project won’t fall apart.
When estimating commercial mechanical costs, it’s important to get advice from industry pros. They can give tips on tech and prices. Suppliers who specialize in mechanical equipment and materials can provide quotes that fit your project’s needs. Consulting experts and suppliers can help you get accurate cost estimates.
Ask specific questions when seeking input from pros and suppliers. They may know of solutions to help with efficiency and costs.
A person tried to estimate a commercial mechanical project by themselves. They thought they could do it with experience. But once they started, they saw they had underestimated many costs. In the end, they had to spend more due to overlooked expenses.
Watching project costs is like watching a toddler in a candy store – it’s necessary to avoid problems.
Stay vigilant and have a systematic approach to monitor and control project expenses. Keep track of associated costs. Make adjustments accordingly. Find ways to reduce costs. Forecast expenses before starting the project. Use data analysis tools to identify trends or discrepancies. Build a team of qualified professionals. Establish clear communication lines. Integrate automated invoice management software. By exercising tight control over expenditure, companies have a better chance of achieving their cost goals without compromising quality or profitability.
Estimate commercial mechanical projects wisely – mistakes can cost more than sanity!
To avoid common mistakes in commercial mechanical cost estimation, use our guide on understanding cost estimation in a comprehensive way. Our detailed analysis with sub-sections on Ignoring Hidden Costs, Inaccurate Material and Labor Cost Estimation, Underestimating Equipment and Tooling Costs, and Misunderstanding Project Scope and Requirements will provide you solutions to overcome these challenges.
Estimating commercial mechanical costs can be tricky. Unseen expenses can be hidden in many places, like admin overhead, project fees and inspection permits. These can be hard to spot and can add up fast.
Without taking them into account, the overall cost of the project may be underestimated. That can lead to extra charges when construction starts.
It’s important to involve experts, like those from accounting and procurement, to identify any possible hidden costs. They can help to ensure the budget is accurate and prevent any risks.
One example of this happened in Washington DC. A contract for a sports facility HVAC work was let without including a vital expense – circuit panels costing $2 million. This ate into their profit margins.
Accurately predicting hidden costs will help you get it right the first time. That way, you won’t need a time machine to go back and fix your mistakes!
Cost estimation for materials and labor is essential for mechanical projects. But, incorrect estimates can be expensive. Errors in material quantity, price and labor hours can create serious differences from the budget.
Incorrect cost estimates cause bad results. Miscalculating material or price could mean not enough funds to finish the project. Misjudging labor hours could mean delays, more costs and lower efficiency. These errors usually go unnoticed until it’s too late.
It’s important to understand the project scope, material needs, available resources and realistic timelines, to increase accuracy. Contractors must have access to current market prices, local labor rates and project expenses at all stages of the project. Specialized software to simplify cost estimation can help.
An example of costly estimating involved a heating system project with an underestimation of £60k. This led to negotiations with investors, cash flow troubles and difficulties to secure loans for future projects. Even small tools can add up – like your therapist bills after you underestimate them in the cost estimation.
Maximize your mechanical construction business’s potential with our competitive financing options
Mistakes in assessing costs of equipment and tools can result in financial losses. Evaluations are vital but often ignored, resulting in cost underestimation. Attention to detail is a must when estimating equipment and tool costs to avoid losses.
Delivery expenses, installation charges, and operator training expenses must be taken into account when procuring and maintaining equipment. Underestimating these “hidden” expenses can damage the budget, affecting profitability.
Quality assurance and control protocols should be a priority when evaluating equipment costs. Ignoring this could cause component failure or even accidents, leading to extra expenditures.
Thorough calculations are required for commercial mechanical cost estimation to align with project planning goals. Failure to consider complexities can lead to severe financial consequences for companies and contractors.
Industry experts at Construction Dive claim “Equipment rental prices have increased by 3% since 2019”. This underlines how important proper assessment is for business profitability and cannot be taken lightly.
Assembling IKEA furniture looks effortless, but understanding project scope and requirements isn’t so simple.
Cost estimators must be aware of a potential mistake: not understanding the project’s scope and requirements. Clear communication with all stakeholders is key to identifying and meeting their needs. Research is also essential, e.g. studying the site’s layout, obtaining permits, etc.
Attention to detail throughout the project is paramount. Project managers should keep track of any changes and adjust estimates accordingly. Miscalculating material costs, failing to account for certain insulation types, etc. could lead to costly revisions – mistakes that could be avoided by understanding the project’s requirements first.
To gain insights into successful commercial mechanical cost estimation, this section on case studies is the perfect solution. By exploring real-world examples, you can learn from the experience of others and adapt their strategies to your own projects. Example 1, Example 2, and Example 3 will offer unique perspectives and techniques for achieving accurate and profitable mechanical cost estimation in your own business.
The first case study illustrates the mastery of mechanical cost estimation. A client requested an estimate for HVAC systems to install in a newly built industry facility. The team used on-site data, reviewed drawings and equipment specs, and assessed the labor and material costs. Using this methodology, they provided a detailed and comprehensive estimate within the promised timeframe.
Compliance regulations and custom requirements increased the overall cost. But the team had a cost-effective, feasible, and streamlined solution. They adopted advanced estimating software which allowed them to modify contingencies for alternate scenarios throughout the project.
This approach resulted in timely project delivery within budget while minimizing potential risks. Studies indicate that more than 60% of commercial projects exceed their budget due to poor planning – Source: McKinsey & Company.
So, let’s have some fun and see if we can find any successful mechanical cost estimation case studies that can make us laugh!
This case study looks into a successful mechanical cost estimation. It involved predicting the costs for upgrades to an industrial plant.
Gathering info on equipment, making a list of upgrades and calculating material and labor costs were part of this process. Leveraging past experiences with similar projects helped adjust calculations. Regulations and scheduling constraints were taken into account when preparing the bid.
Good communication between all parties was key. Constant updates and tracking kept timelines in check and avoided cost overruns. Attention to detail throughout the estimation process minimized any unexpected challenges.
The result? Completed work ahead of schedule and within budget. Taking initiatives like this creates client satisfaction and leads to repeat business. A success story for estimators and stakeholders alike!
A third instance in the study of successful commercial mechanical cost estimation was featuring great savings by applying value engineering. This involved high-efficiency equipment and a proactive maintenance plan. The result? Lower operational costs, better energy efficiency & longer life for the equipment.
Plus, sustainable design practices were used to match the customer’s environmental ambitions. Renewable sources like solar heating & cooling systems were utilized, which massively reduced the building’s carbon footprint.
What’s more, when it comes to cost estimation, be prepared for the unexpected. Have a contingency plan ready!
When performing cost estimation for mechanical projects, understanding certain points can make a big difference in the accuracy of the quote. Here are three essential tips to keep in mind:
Furthermore, estimators should be able to read construction drawings and specifications in order to understand the requirements and provide precise quotes. The Bureau of Labor Statistics (BLS) has projected that the employment of cost estimators will grow 11% from 2019 to 2029.
Commercial mechanical cost estimation is the process of calculating the total cost of mechanical systems in commercial buildings, including HVAC, plumbing, and electrical systems.
Accurately estimating the cost of mechanical systems in a commercial building can help contractors and owners plan and budget for projects, ensure that bids are competitive, and avoid unexpected costs during construction.
Factors that affect the cost of mechanical systems in commercial buildings include the type and size of the building, the type and complexity of the mechanical systems, the quality of materials used, and the location of the project.
Commercial mechanical cost estimation is usually conducted by experienced engineers and project managers who use a variety of tools and techniques, including cost databases, historical data, and industry standards, to accurately estimate the costs of mechanical systems.
The accuracy of commercial mechanical cost estimates depends on the quality of the data and assumptions used in the estimation process. Experienced estimators use a variety of tools and techniques to ensure that estimates are as accurate as possible.
To ensure an accurate commercial mechanical cost estimate, it is recommended to work with an experienced estimator who has a strong understanding of the industry standards and current market conditions. Additionally, providing detailed specifications and project requirements can help ensure the accuracy of the estimate.
Here I am going to share some steps to get your mechanical construction cost estimate report.
You can send us your plan on info@estimatorflorida.com
Before starting your project, we send you a quote for your service. That quote will have detailed information about your project. Here you will get information about the size, difficulty, complexity and bid date when determining pricing.
We do mechanical construction cost estimating and prepare a detailed report for your project. At last, you finalize the report and finish the project.
561-530-2845
info@estimatorflorida.com
Address
5245 Wiles Rd Apt 3-102 St. Pete Beach, FL 33073 United States
561-530-2845
info@estimatorflorida.com
Address
5245 Wiles Rd Apt 3-102 St. Pete Beach, FL 33073 United States
All copyright © Reserved | Designed By V Marketing Media | Disclaimer
IMPORTANT: Make sure the email and cell phone number you enter are correct. We will email and text you a link to get started.
By clicking “I Agree” above you give Estimate Florida Consultin express written consent to deliver or cause to be delivered calls and messages to you by email, telephone, pre-recorded message, autodialer, and text. Message and data rates may apply. You are able to opt-out at any time. You can text STOP to cancel future text messages.