A Wining Cost Estimate
That Helps You To Win More Framing Construction Projects
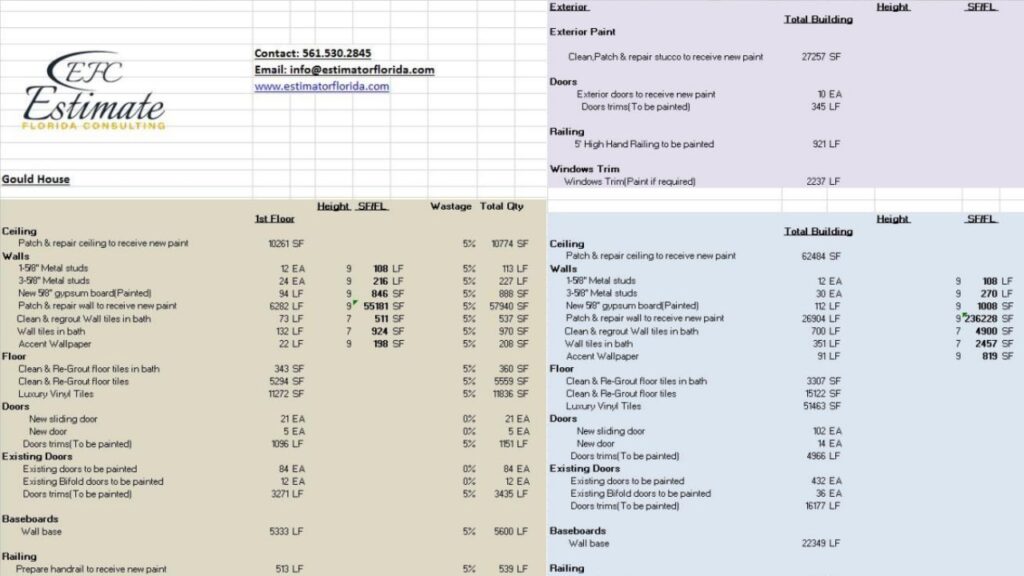
To help you master wood framing estimation basics with a step-by-step approach, the following section focuses on understanding wood framing and giving you an estimation process overview. This will enable you to gain knowledge about the different types of wood used for framing and the tools you may need while estimating.
Wood framing is an essential part of construction. It consists of vertical and horizontal members like walls, floors, ceilings, and roofs. Knowing how to design and estimate costs for each component is key. Estimates must be exact as small miscalculations can cause big financial issues.
The traditional timber frame has been used for centuries. Oak timbers joined by mortise-and-tenon joints instead of nails were used. Keying pieces together created a tight fit supporting weight without spillage or noise. It’s still popular today! Let’s explore the exciting world of wood framing estimation.
Starting with framing estimation requires an organized approach. So, get an overview first. Here’s a table of necessary components:
Required Components | Description |
---|---|
Blueprints | Plan for windows, doors, walls. |
Material List | Materials based on blueprints. |
Labor Cost Estimate | Cost of labor for completion. |
Permits | Docs for construction in certain areas. |
Be prepared for extra costs. Get tips from experienced folks to avoid unplanned expenditure. Aim for accurate framing estimates. Get help from industry professionals. It helps clients and contractors.
Tools you need: Nail guns, saws, hammers. Give it a try!
To estimate wood framing with accuracy, you need to have the right tools and materials. In order to make this process easier for you, we have compiled a list of essential tools for wood framing estimation and materials that you will need. These include the items needed to take accurate measurements, as well as the materials required to prepare for and complete your framing project.
Accurate estimation of wood framing requires certain tools and materials. We’ve outlined them in a table below. Also, specialized software can help with calculations.
Tools & Materials | Purpose |
---|---|
Tape Measure | To measure dimensions of the framing lumber |
Square | To check for squareness and mark perpendicular lines |
Hammer | To drive nails into wood |
Nails | To join pieces of wood together |
Saw | To cut wood pieces to the required length |
Specialized Software | To help with the calculations |
Accurate estimation of wood framing requires certain tools and materials. We’ve outlined them in a table below. Also, specialized software can help with calculations.
It’s critical to remember that even small miscalculations can lead to delays. Knowing how to use the tools correctly is a must for success.
My team learned this the hard way when we had to re-estimate a job. We hadn’t taken into account changes in building codes. From then on, we made sure to stay updated on code regulations for estimates.
Estimated Materials for Timber Construction
To estimate materials for timber construction, there are certain items to consider. These vary based on the project’s scope and specifications. Generally, lumber, connectors, framing hardware, sheathing panels, insulation material and roofing components are required.
A table below details the materials needed for estimation:
Materials | Description |
---|---|
Lumber | Treated lumber |
Connectors | Structual screws |
Framing Hardware | Nails 1 3/4″ rated at .131 inch |
Sheathing Panels | Structural Insulation Panels (SIPs) |
Insulation Material | Fiberglass blanket insulation |
Roofing Components | Shingle |
Adhesives and sealants should also be taken into account. Using accurate building plans is important for a complete and accurate material list.
Remember, project requirements may need further considerations.
Timber construction has been used for centuries. Wood’s strength and beauty make it an excellent choice for post-and-beam frames. Counting wood planks is like counting sheep – only you’re building a house, not falling asleep!
It’s critical to remember that even small miscalculations can lead to delays. Knowing how to use the tools correctly is a must for success.
My team learned this the hard way when we had to re-estimate a job. We hadn’t taken into account changes in building codes. From then on, we made sure to stay updated on code regulations for estimates.
We help contractors find new customers with high-converting websites and locally targeted niche-specific lead-generation programs. You’ll never need to worry about running out of work again! We focus on quality over quantity with our leads for contractors.
To calculate the wood framing requirements for your building, this section, ‘Calculating Wood Framing Requirements’ with sub-sections ‘Measuring the Building Parameters, Wall Framing Estimation, Roof Framing Estimation’ can help. Each of these sub-sections offers a unique solution for calculating the framing requirements of your building project.
Accurately gauging the structural dimensions is key when planning wood framing needs for construction. We can accurately assess these metrics to decide the best wood measurements and quantities.
Critical Metric | True Value |
---|---|
Wall Height | 12 feet |
Wall Length | 45 feet |
Stud Spacing | 16 inches |
Plate Width | 2 inches |
Plate Thickness | 1 inch |
It’s important to recognize that not all building parameters rely just on measuring linear dimensions. Local building codes, lumber grades, and weather conditions also affect wood framing computations.
Throughout time, people have used wood as a main source for constructing buildings because of its durability and renewable form. Complex ways have been developed to calculate suitable amounts of wood necessary for structural stability and cost-effectiveness. Building walls may sound hard, but at least they won’t judge you like your therapist does.
To estimate the wood frame for walls, calculate the total length and height. Add all the measurements together to get the amount of wood needed. Take into account any openings like windows and doors. Subtract their measurements from the total to have a more accurate estimate. Pro tip: It is best to overestimate when calculating wood framing requirements. Calculating roof framing requirements is like playing Jenga, but more expensive if it collapses!
Working out the quantity of framing supplies for a roof is super important in construction. By doing calculations and taking measurements, you can make an accurate estimation.
Materials and how much you need:
To get the right amount of materials, there are factors to consider like pitch, span and load capacity.
Professionals have been using formulas and methods to estimate framing needs for years. With tech and tools, estimations have become more precise. Look out, your wallet! We’re about to reveal the real cost of building with wood framing.
To understand material costs when estimating wood framing, you need to be familiar with types of lumber and their costs, as well as determining material quantities and costs. In the following sub-sections, we’ll cover each of these topics, giving you the tools you need to complete your project with a better understanding of the costs involved.
The cost of lumber varies greatly based on what type of wood you use. Each kind has unique characteristics, which makes them suitable for different uses such as furniture, flooring, or construction.
We have created a table to explain the various types of lumber and their associated price per board foot. To measure, a board foot is a piece of wood that’s 12 inches long, 12 inches wide, and 1 inch thick.
Lumber Type | Description | Price per Board Foot |
---|---|---|
Douglas Fir | Versatile, strong. Used in framing and construction | $4 – $8 |
Redwood | Resists decay and insects. Great for decking and outdoor furniture | $6 – $10 |
Maple | Durable hardwood. Used for flooring and cabinetry | $5 – $15 |
Cedar | Aromatic softwood. Used for cladding and siding projects | $2 – $5 |
This is just a small sample. There are many other types of lumber with different prices.
Pro Tip: When budgeting for a project involving lumber, consider the type you will use and calculate the number of board feet precisely.
Know your material quantities and prices, or else your budget will feel like it’s been hit with a bat at a kid’s birthday party!
Text: Analyzing Necessary Materials and Costing
Knowing what materials are needed and what they cost is a major part of any construction project. You must consider size, scope, function, quality, and design. With those elements, you can make an exact list of what’s required, and how much it’ll cost.
To help with this, create a table for all components needed for the task. It should include quantity and cost. For example:
Component | Quantity | Cost |
---|---|---|
Bricks | 10,000 | $5,000 |
Cement | 200 bags | $2,000 |
Steel | 500 kg | $3,500 |
By listing the components, it’s easier to figure out a budget for materials.
Remember, certain unique features of the project could change the estimates. If there are special regulations or standards, materials could differ and cost more.
Pro Tip: To keep material costs low, monitor progress and adjust based on what’s actually used. Be prepared for surprise expenses too.
Maximize your framing construction business’s potential with our competitive financing options
To account for additional costs while estimating wood framing, Labor Costs for Wood Framing and Additional Costs to Consider are the two sub-sections that will provide you with solutions. Knowing the labor costs involved will help you account for them in the estimate, while considering additional costs will ensure that no hidden costs pop up later.
Labor expenses have a big impact on the cost of wood framing. To figure out labor costs, we have to consider the number of workers needed, their hourly wage rate, and the project’s size, complexity, and timeline.
Here’s a table with essential info about average wage rates and additional costs:
Number of Workers | Average Hourly Wage Rate | Additional Costs (Per Hour) |
---|---|---|
1-2 | $25-$35 | $15-$20 |
3-4 | $35-$45 | $20-$30 |
5 or more (depending on requirements) (vary by location) | $45-$60 | $30-$40* *May include benefits such as insurance and off-site training. |
Remember, these are just averages and may vary due to state laws and regulations. Planning is key when it comes to estimating labor costs for wood framing. Investing in labor costs today can save you money in the future. Oh, and don’t forget the headache and the stiff drink!
When estimating costs, there’s more to consider than what’s obvious. Unforeseen or hidden expenses can really affect a project’s success. These can include:
It’s important to take extra costs into account during planning and budgeting. This will help avoid costly overruns and issues with project completion. Seeking advice from experienced professionals can be useful in this regard. Calculating costs is like shooting in the dark, but with a calculator instead of a bullet.
To avoid common estimation mistakes while estimating wood framing with our comprehensive guide, this section will discuss some common errors that must be avoided. Not accounting for waste, underestimating labor costs, and overestimating material costs are some of the sub-sections that we’ll explore in detail. By understanding these mistakes, you can estimate wood framing projects more accurately, ensuring success and profitability.
Discover the transformative power of hiring professional contractors for your project. Unlock a wealth of expertise and experience to ensure success. Get started today and see the difference!
A mistake commonly made when estimating costs is overlooking “waste” materials. This leads to overspending or underestimation of the project’s cost.
It is crucial to assess the waste for an accurate estimate. Failing to do so can cause extra expenses and strain budgets. Not accounting for waste can also require more labour and resources than needed.
No two projects are ever the same. A mistake might be significantly understated despite similarities. For example, 33% of materials in a high-rise office tower may end up as unnecessary waste, increasing costs if unaccounted for.
Underbudgeting and mismanaging waste has bankrupted big companies, such as General Motors and Chrysler. Hence, proper waste management is key for success and sustainability.
Underestimating labor costs is a recipe for disaster.
Underestimating manpower expenses is a common mistake. It can lead to resource allocation issues, overworked teams and even loss of revenue. To prevent this, one must factor in the available staff – their expertise, skill level, and workload.
This approach ensures that all requirements are clearly defined from the start. It also helps to avoid mid-project budget strains. Reasons for underestimating labor costs include overlooking qualification prerequisites or using too low an hourly rate.
By taking these variables into account, businesses can ensure realistic estimations that guarantee success. Don’t miss out on vital criteria when costing out staff. Get accurate forecasts by assessing needs based on team size, budgets and abilities.
By using a thorough approach during estimation, businesses reduce risk factors while increasing efficiency and profitability. This makes them more competitive in their industries.
Miscalculating materials costs can be a huge hit to any project budget. An inaccurate evaluation of those materials leads to extra expenses that can take away from the project’s profitability.
When bidding for a project, it’s important to collect full and accurate information on what materials are needed. If not, the costs will be hard to estimate.
Your team must be aware of the current pricing trends; they can change quickly. And, if the supplier changes or additional materials are needed, update the estimates right away.
Overestimating costs can cause delays and disappointments – two expensive outcomes for business owners. A Firmatek analysis says material errors can cause cost overruns of 60% above the estimated costs. It’s important to understand the scope and do research before starting a project.
Time to use your estimation skills – or just hire someone who can do it properly.
Wood framing is the construction method of creating a structure using lumber or engineered wood products to form a frame or skeleton that supports the building’s weight and loads.
To estimate the amount of wood needed, you will need to calculate the linear footage of the walls and roof. Then, you can multiply the linear footage by the number of studs or joists needed per foot, which will depend on local building codes.
Common tools used for wood framing include a circular saw, handsaw, hammer, framing square, level, chisel, nail gun, and measuring tape.
The spacing of the framing members, such as studs or joists, will depend on the local building codes. Typically, they are spaced at 16-inch intervals, but in larger structures, they may be spaced at 24 inches. Always check local codes to ensure compliance.
The most commonly used woods for framing are Douglas fir, southern yellow pine, and spruce pine fir. These species are strong and durable enough to support the weight of a building and resist moisture and pests. Always check with your local lumber supplier to find the best option for your area.
Use a level and plumb line to ensure your framing is straight and even. You can also use braces and temporary supports to hold the framing in place while building. It’s essential to check your work as you go to avoid costly mistakes.
Here I am going to share some steps to get your framing construction cost estimate report.
You can send us your plan on info@estimatorflorida.com
Before starting your project, we send you a quote for your service. That quote will have detailed information about your project. Here you will get information about the size, difficulty, complexity and bid date when determining pricing.
We do framing construction cost estimating and prepare a detailed report for your project. At last, you finalize the report and finish the project.
561-530-2845
info@estimatorflorida.com
Address
5245 Wiles Rd Apt 3-102 St. Pete Beach, FL 33073 United States
561-530-2845
info@estimatorflorida.com
Address
5245 Wiles Rd Apt 3-102 St. Pete Beach, FL 33073 United States
All copyright © Reserved | Designed By V Marketing Media | Disclaimer