A Wining Cost Estimate
That Helps You To Win More Construction Projects
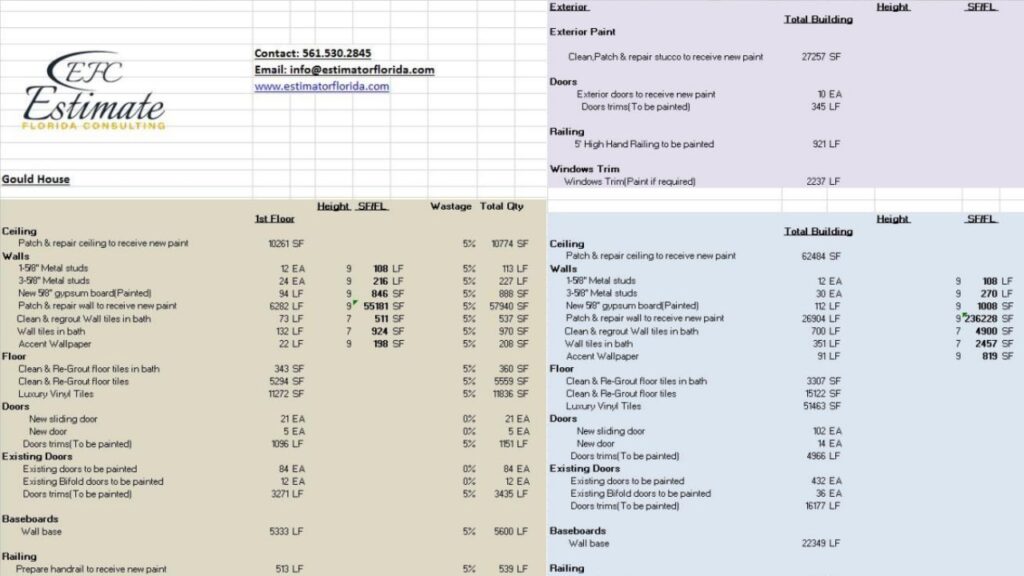
Estimating the cost of designing book storage and shelving spaces is tricky. It depends on the material used, size, and added features. Here’s a look at some of the major factors:
Cost Considerations | True Data |
---|---|
Materials | $100-$400 per linear foot |
Labor | $50-$200 per hour |
Design Fees | 10-20% of total cost |
Installation Fees | $100-$300 per unit |
Keep these costs in mind when planning a custom book storage space. Research various designers and contractors to get the best value. Pre-manufactured pieces can help reduce prices.
Book storage spaces go way back. Ancient Egyptians had basic shelves for scrolls. Later, it evolved into complex systems of wall-mounted shelving used by scholars.
Building custom bookcases? Guess IKEA won’t do for your superiority complex.
To determine the scope of your custom bookcase and shelving unit project, measuring the space and identifying the purpose and function are essential. These two sub-sections will help you achieve a better understanding of what you want and need from your bookcase or shelving unit.
Measuring the area is very important, to give you real data for making smarter decisions. Here’s a table with the factors to think about when measuring up space:
Factor | Measurement |
---|---|
Height | feet |
Width | feet |
Length | feet |
Square footage | sq feet |
It’s important to note any curves or nooks that could affect your reading. Take pictures and notes to remember all details.
Consider multiple ways to measure. Cross-sectional measurements and mathematical modeling can help confirm accuracy.
Hiring a professional surveyor is the best solution to get accurate data. They will know how to measure and survey while following building codes and regulations.
Bookcases and shelving units are key for organizing living spaces. To determine design, placement, and size, considering their purpose and function can be useful. Assessing the use of these pieces helps create areas for books, decor, or storage.
Considering user needs is essential when defining purpose and function. For instance, a home office may require more space to store books and papers, unlike a kid’s room, which needs shelves at lower heights. Don’t forget the aesthetics! Bookcase designs range from minimalist to ornate.
Understanding how bookshelves fit into space is significant for deciding scope. Keeping them away from direct sunlight helps preserve books; particular types of shelves work best, depending on what they hold. Built-in shelves save floor space, unlike freestanding units.
Pro Tip: Function should be prioritized over aesthetics when designing custom-built cabinetry. Still, keep form coherent with surrounding furnishings and fittings. Choosing the right materials is just as important as choosing the right outfit for a first date.
To make sure you choose the right materials for building custom bookcases and shelving units, this section “Selecting Materials” with the sub-sections “Types of Wood” and “Hardware and Fasteners” can help you. Each of these sub-sections offers unique solutions for selecting the best materials that are durable, cost-effective, and match your design needs.
Maximize your construction business’s potential with our competitive financing options
Wood types are essential for selecting materials. Here are some popular timber choices:
Name | Color | Density (kg/m3) | Workability |
---|---|---|---|
Cedar | Light Brown to Reddish-Brown | 340-400 | Easy with hand & power tools. Favored for its fine texture & grain. |
Oak | Natural tan to yellow-brown; often has a golden glow | 645–930 | Moderately hard, durable and coarse-grained. Open grain needs careful sanding or finishing. |
Pine | Ranges from pale yellow to light red-brown heartwood; sapwood is whitish-yellow-to-pale brown in color. | Density varies from 390 kg/m3-650 kg/m3 based on specific gravity, hardness tests & moisture content rating |
When selecting timber, consider your project’s needs and desired look. Pine is cheap but less durable than oak or cedar, which are more expensive but sturdier.
Hardware and fasteners are also important – you can’t rely solely on glue to put things together.
When picking materials for a project, it’s key to think about the bits to hold everything in place. An essential part is choosing the right ‘Fixings and Joiners’. Some common types are:
In addition, decide on the right size, material (stainless steel or zinc), and type (flat head or round head screws). When selecting fixings & joiners, be sure they match the materials you’re using.
Pro Tip: Always use corrosion-resistant or stainless-steel fasteners in outdoor or damp areas.
Time to do some math, ’cause figuring out material costs is as thrilling as watching paint dry.
To calculate material costs for building custom bookcases and shelving units, you need an estimation of the amount of wood required and pricing of the wood and hardware. That’s where the sub-sections, estimating the amount of wood needed and pricing wood and hardware come in as a solution to accurately calculate the cost of your project.
Knowing the Necessary Amount of Timber
To make accurate cost estimations, you need to calculate the required timber for a project. This can be done by various methods, like calculators and software programs for construction.
Check this table for an example material calculation for wood projects:
Item | Quantity | Size (in meters) |
---|---|---|
Ceiling | 5 | 3 x 6 |
Flooring | 4 | 4 x 8 |
Walls | 10 | 2 x 4 |
When estimating wood, you have to think about both rough and finished lumber, plus waste factor when cutting to size. This will make sure you have enough materials while reducing potential waste.
It is crucial to take precise measurements before calculating materials. A tiny discrepancy can lead to extra costs or inadequate construction.
Woodworking Network states that wood prices have grown recently due to more home renovations. So, make sure your wood and hardware don’t give you splinters in your budget.
Calculating material costs? Wood & hardware got you stumped? Here’s how to do it!
Create a table with item name, quantity needed, unit price, & total cost. Calculate the total cost with this info. Example:
Item Name | Quantity Needed | Unit Price ($) | Total Cost ($) |
---|---|---|---|
2×4 pine lumber | 20 pieces | 2.50 | 50.00 |
Deck screws | 1 box (350 screws) | 28.99 per box | 28.99 |
Wood glue | 1 quart bottle | 7.99 per bottle | 7.99 |
Sandpaper (fine grit) | 5 sheets | 1.50 each sheet | 7.50 |
Total Cost: | – | – | >95.48 |
Remember: prices change depending on the wood & hardware. Shop around for the best deals. Calculate the cost without breaking the bank!
To estimate the labor costs involved in building custom bookcases and shelving units with the sub-sections of Determining the Number of Hours Required, and Calculating Hourly Rates are the solutions. Estimating the labor costs accurately is crucial to ensure that you do not undercharge or overcharge your clients. The sub-sections will help you determine the fair and reasonable price for the services you provide.
Calculating The Required Number of Hours is key for optimizing labor costs. Factors like project scope, worker availability, and skill level must be taken into account. Using historical data and team input can help refine the estimate. Prioritizing accurate hour calculations is crucial for businesses and their resources.
It’s essential to analyze various aspects of a job to determine the estimated number of hours. Consulting experienced workers who have done similar jobs can help identify potential roadblocks affecting time requirements.
Ignoring hourly calculations or making inaccurate estimates can cause projects to exceed the expected timeframe. This increases labor costs and customer dissatisfaction. Inaccurate calculations can also cause overhead expenses to exceed the revenue generated.
Accurate hour calculations help avoid unnecessary over-expenditure. Therefore, tracking and estimating proper time allotments are essential for businesses to achieve proper profit margins and satisfy customers. Why do we calculate hourly rates? So we can figure out exactly how much money we’re losing while we scroll through social media at work!
Determining hourly rates for labor requires analyzing multiple factors. These include job role, experience level, desired profit margin, and projected expenses. The following table lists these factors and their corresponding variables for calculating hourly rates correctly.
Factors Involved | Variables |
---|---|
Job role | Required Skill set, years of experience |
Experience level | Entry-level, Mid-level, or Senior-level |
Desired profit margin | Percentage markup required, profit goal per project/hour |
Projected expenses | Labor, Equipment, Materials, Overheads, and Insurance |
It’s essential to note that the variables of each factor influence the overall hourly rate calculation. Thus, thoughtful selection of values for each factor is necessary.
Industry standards and comprehensive research point to keeping hourly rates in line with market expectations. Additionally, clear communication throughout the bidding process minimizes the risk of monetary discrepancies during contract completion.
The exact hourly rates will depend on individual business needs. However, by taking into account all relevant factors and following a consistent methodology across estimating procedures, companies can ensure profitability while still maintaining competitive pricing. Remember, adding up additional costs is an arduous yet necessary task for the successful running of your business.
Remember: prices change depending on the wood & hardware. Shop around for the best deals. Calculate the cost without breaking the bank!
To calculate the complete cost of building custom bookcases and shelving units, you need to consider the additional expenses besides material and labor costs. In order to provide an accurate estimate, you should take into account the tools and equipment required, as well as any costs associated with delivery and installation.
To help you plan for expenses related to essential tools, here’s a breakdown of the cost:
Item | Cost |
---|---|
Hammer | $10 |
Drill | $50 |
Screwdriver Set | $20 |
Power Sander | $80 |
Don’t forget safety gear and cleaning supplies. Those costs can add up quickly. You can save money by renting infrequently-used tools or buying in bulk. Also, ask around for surplus materials or equipment from coworkers or peers.
By planning ahead and budgeting carefully, you can avoid a financial shock after delivery and installation.
It’s essential to understand the transport and installation of your product clearly. Here’s what you need to know:
Be aware: Despite our best efforts, there may be unexpected factors that could cause a delay. In case of queries or concerns, our support team is ready to assist.
Pro Tip: To ensure a smooth delivery and installation, provide accurate details on location access points and any pre-existing challenges. And keep in mind – the final cost estimation won’t be cheap!
To calculate the final cost of building custom bookcases and shelving units with accurate estimation, summing up material and labor costs, and factoring in additional costs are the solutions you need to consider. These sub-sections will give you insights into the necessary considerations when estimating the final cost of building custom bookcases and shelving units.
Computing the total cost by combining material and workforce expenses is essential. Calculating all expenses precisely prevents any financial shockers during the last stages of the project.
A table offers an overview of different material and labor costs needed for the project. It includes the name, quantity, unit cost, and total cost of each item. The last column calculates the expense by multiplying the unit cost with the amount spent on that material or service.
It is important to remember that some expenses may not be included in this analysis. However, they must be estimated prior to submitting any bids.
Our source has decided that aside from primary expenses, such as materials and labor, travel costs, storage fees, permits, and insurance should also be taken into account to provide a proper estimate of the project’s costs.
Fun Fact: According to a survey conducted by Zillow Research Institute, Americans spend roughly $15k-20k on home improvement each year.
Adding extra costs is like peeling an onion – the more you do it, the more tearful you become!
Take into Consideration Extra Expenses:
It is important to remember extra costs that can come up during a project. These can include items such as materials, labor, and transport. Thinking of them beforehand stops sudden financial issues and delays.
So, we made a table to help with outlining potential extra expenses. It includes sections like ‘Description of Expense’, ‘Cost Estimate’, and ‘Actual Cost’. With this, you can find any differences between the estimated cost and the actual cost.
Also, there are more elements to keep in mind when considering extra expenses. These include seasonality, market demand, and material price changes. Doing research and consulting experts can lead to more accurate financial projections.
According to Forbes, 90% of construction projects go over budget due to unplanned costs. Paying attention to extra costs can have a major effect on your project’s budget plan.
And, the only thing worse than underestimating final costs is overestimating your skill on a DIY project!
Analyzing the building of custom bookcases and shelving units? Consider factors like materials, labor, and time. Evaluation is key, before starting any project.
Recommend selecting materials that suit needs and budget. Explore options to find sturdy, affordable wood. Consulting a professional carpenter or interior designer can help too.
Planning and proper measurement are key for success. Consider the purpose of the bookcase or shelving unit before creating designs. It’ll help avoid unexpected expenses. Professional consultation is advised.
When estimating total cost, consider all necessary elements for an efficient and satisfactory outcome.
Some factors to consider include the type of materials used, the size and complexity of the design, and the labor costs.
The cost can vary widely depending on the factors listed above, but generally you can expect to pay anywhere from $500 to $5000 or more.
While building your own custom bookcases and shelving units can be a cost-effective solution, it is important to consider your own skill level and time constraints before taking on such a project.
Yes, additional costs could include tools and equipment needed for the job, as well as any necessary permits and inspections.
The length of time can vary depending on the size and complexity of the design, but typically it can take anywhere from a few days to several weeks to complete the project.
Here I am going to share some steps to get your construction cost estimate report.
You can send us your plan on info@estimatorflorida.com
Before starting your project, we send you a quote for your service. That quote will have detailed information about your project. Here you will get information about the size, difficulty, complexity and bid date when determining pricing.
We do construction cost estimating and prepare a detailed report for your project. At last, you finalize the report and finish the project.
561-530-2845
info@estimatorflorida.com
Address
5245 Wiles Rd Apt 3-102 St. Pete Beach, FL 33073 United States
561-530-2845
info@estimatorflorida.com
Address
5245 Wiles Rd Apt 3-102 St. Pete Beach, FL 33073 United States
All copyright © Reserved | Designed By V Marketing Media | Disclaimer
IMPORTANT: Make sure the email and cell phone number you enter are correct. We will email and text you a link to get started.
By clicking “I Agree” above you give Estimate Florida Consultin express written consent to deliver or cause to be delivered calls and messages to you by email, telephone, pre-recorded message, autodialer, and text. Message and data rates may apply. You are able to opt-out at any time. You can text STOP to cancel future text messages.