A Wining Cost Estimate
That Helps You To Win More Painting Construction Projects
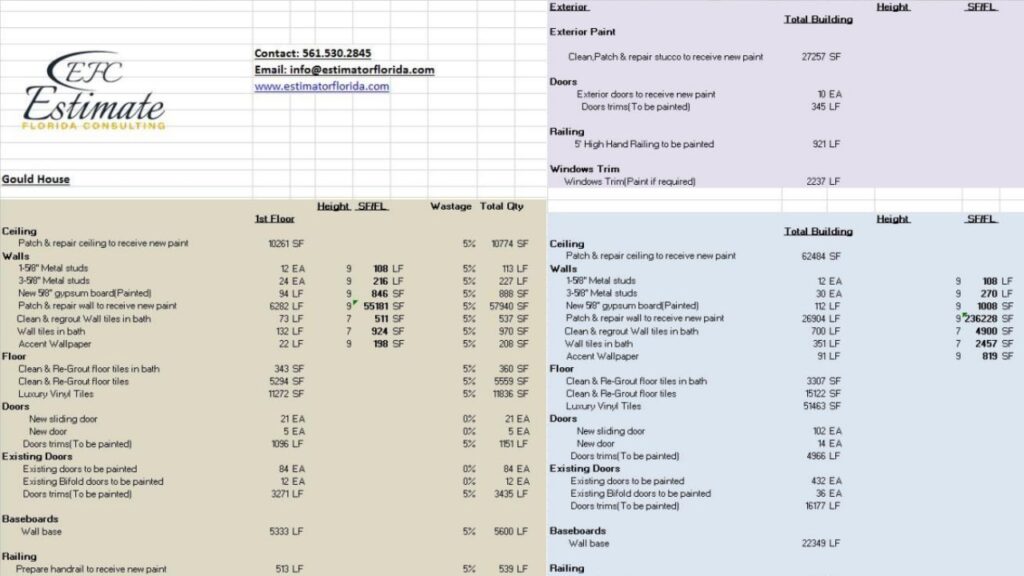
Speciality finishes are a special way to bring character and depth into any area. They involve faux painting, textures, and other craftsman techniques that replace traditional painting and decorating. This requires precision and top-grade materials.
These finishes can be seen in expensive homes and commercial venues, to make stunning visuals. Most of these are customised, so you need an artisan with special skills to create the design you want.
Specialty finishes may be pricey, but they give you more value for money. This is because they last longer than regular paint! Benjamin Moore says that faux finishes add unique features, dimensionality, and sophistication using mixed colours, textures, patterns, and surfaces which look amazing.
These special finishes can also be used on interior/exterior walls, wood panelling, and cabinetry, giving surfaces a special feel that you can choose. Just remember – specialty finishes will cost more than you thought!
To estimate the cost of specialty finishes for your next project, you need to consider various factors. In order to get a better idea, delve into the section of “Factors Affecting Cost Estimation” with “Size of the Surface Area, Type of Specialty Finish, Complexity of the Design, Quality of Materials Used, and Labor Costs” as solution.
The surface area size is critical to cost estimation, no matter what. It affects how long the job will take, and how much materials are needed.
Size of Room (sq ft) | Time Required | Amount of Paint Needed |
---|---|---|
Small (100-199) | Paint 1 coat in 3 days | 9 gallons |
Medium (200-500) | Paint over 6 days | 20-25 gallons |
Large (over 600) | Need special equip., take 15+ days | use more paint |
Factors including expertise level, paint quality, and labor costs can increase costs. To save, evaluate related variables first. Also, seek help from people who have done similar jobs. Why not add some special pizzazz and make that cost estimation soar?
Unique and special finishes have a big influence on the cost of any project. This includes materials, design styles, and application techniques each one with different features.
Take a look at how the type of specialty finish affects cost estimation:
Each finish needs different techniques. Metallics require more material, faux painting needs more workmanship, and Venetian plaster needs both higher skill level and paint application.
It’s important to understand these factors during project planning. Lack of technical skills can add costs through reworks. Design complexity is like putting together a puzzle blindfolded, but with razor blades instead of pieces.
The design’s intricacies can affect cost estimation significantly. Complex designs require more resources for development, thus costing more. Variables like number of components, size and material choices may influence this complexity. Also, small alterations or added features may increase complexity and expenses.
It is essential to understand how complexity affects project costs as it affects so many other things. These include labor, machinery, specialized knowledge and raw materials. Furthermore, design complexity often warrants modifications to manufacturing processes. This leads to higher costs due to time and financial losses.
Sometimes seemingly simple designs result in unforeseen challenges. To avoid such issues, designers need to evaluate the complexity of each component before committing and reduce risks of delays and costs due to complex designs.
Maximize your painting construction business’s potential with our competitive financing options
The quality of materials used has a major impact on cost estimation. Different qualities of materials lead to different prices. Lower quality materials increase repair and maintenance costs.
To understand this better, a table can be made. It should include: Material Type, Quality Level, Price per Unit, and Total Cost. For example, steel plates for building construction. High-grade steel plates can cost up to $1000 per unit. 10K units would cost $10 Million.
Using high-grade materials also has benefits. It boosts structural integrity, increases stability, and improves sustainability.
This has been an issue for a long time. Ancient craftsmen found ways to use materials that were resistant to decay. This enabled them to build structures that lasted in tough conditions.
Labor costs can make or break a budget. But it’s not as bad as hiring a clown for a kid’s birthday party – we all know how that could be a financial disaster.
Labor expenses are key for cost estimation. The price of staff for a project affects the end cost. This includes wages, salaries, benefits and payroll taxes for full-time workers.
To stop labor costs from going out of control, use accurate forecasting and estimating software. This can help decide how many people are needed, what skills they must have, and a timeline for completion.
Outsourcing some of the project can lower labor costs by bringing in contract professionals with the right expertise without hiring long-term workers. It can also help manage peak-period workloads.
Using freelance resources is another way to cut expenses while still having good output. Freelancers generally work on a per-project basis, making it simple to scale up or down.
These steps not only reduce labor costs but also make sure the team runs smoothly and delivers great result at an affordable cost. Estimating the cost of faux painting is like trying to predict the weather in a snow globe.
To estimate the cost of faux painting, you need to know more than just price per square foot. Learn about various techniques used in faux painting, along with the material and labor costs involved. In this section, we’ll explore the sub-sections of material costs for faux painting, labor costs for faux painting, and techniques used in faux painting, all of which will help you accurately estimate the cost of a specialty finish.
You should use high-quality materials and consult experts when choosing colors that fit the area.
Faux art has been around since ancient times; Egyptians would use pigments to create fake finishes on walls, which still exist today in preserved museums or temples around Egypt.
Impressive how much you can spend when pretending paint is something else!
Doing faux painting? Costs matter! The price of materials depend on quality and quantity. Consider the prices in the table below.
Materials | Price Range ($) |
---|---|
Base Coat | 25-65 |
Glaze Medium | 10-30 |
Metallic Paints | 8-20 |
Paint Brushes | 6-15 |
Rollers | 5-10 |
Plus, painter’s tape, gloves and drop cloths for protection. No need to pay for labor if you do it yourself. Prices may vary by location, but the above costs are usually correct. HomeAdvisor’s True Cost Guide says the average cost for faux painting is $2,272. Unless you want to risk a DIY Pinterest fail, be ready to pay up!
Creating faux paintings can be costly. Labor costs make up a big part of the budget. Prices vary based on location, skill level, experience, and complexity.
A breakdown of the costs is shown in the table below:
City | Skill Level | Experience | Cost Per Hour | |
---|---|---|---|---|
1 | New York | Intermediate | 1-2 years | $50-$65 |
2 | Los Angeles | Expert | 5+ years | $75-$95 |
3 | Chicago | Beginner | Less than a year | $35-$45 |
Remember to factor in the time it takes to complete the project. Complex or artisanal projects may cost up to $6 per square foot.
Labor Costs can be a key factor in successful faux painting projects. So it’s important to assess them accurately.
To estimate the cost of textured finishes, such as faux painting and textures, you’ll need to understand the types of finishes and the costs associated with them. For this, we have divided the section into three sub-sections: types of textured finishes, material costs related to textured finishes, and labor costs for textured finishes. These sub-sections will help you calculate the accurate cost estimation for your next textured finish project.
Different variations of textured finishes are used to create a tactile surface on walls. Each finish offers a unique feeling and look. Here’s a breakdown of the most popular types:
Type | Description |
---|---|
Venetian Plaster | Semi-gloss finish that gives depth and clarity. |
Stucco | Rough texture with lots of character. |
Knockdown Texture | Basic texture achieved by spraying a mixture of water and drywall joint compound. |
Spackling can also offer walls an eye-catching look. But, industry experts say textured finishes take longer and cost more than smooth finishes. So, prepare to spend extra dough to give your wall a ‘gym-like’ look.
To calculate the cost of textured finishes, materials play a significant role. This usually involves multiple layers of coating and adhesive, combined with natural or synthetic paints and other decorative items.
For better understanding of the cost structure, we created a table. This includes columns like Product Name, Brand Name, Cost per unit (USD), Quantity used/sq ft (litres/ sq ft) and Total Material Cost (USD/ sq ft).
When estimating textured finish costs, it’s essential to include other factors. These are labour, transportation and complexity levels. These vary based on surface area & installation location. Plus, material expenses must be factored in.
One way to trim estimates while keeping material quality is to work with local manufacturers & suppliers for bulk purchase discounts.
A study from “Building Design + Construction” highlights that buying materials locally can reduce material costs by 10-20%. So, labor costs for textured finishes? More like ‘texture-naught’ am I right?
The expenses for textured finishes are key. To keep costs low, you have to consider Labor Costs. Here’s a table with details of factors impacting labor costs:
Number of Days | Hourly Rate (USD) | Labor Cost (per sq.ft) |
---|---|---|
1-2 | 30-50 | 45 |
3-4 | 50-70 | 60 |
5-6 | 70-100 | 80 |
Keep in mind, these are standard prices. They may change depending on location, complexity and urgency. Make sure to get an experienced contractor, who is transparent about cost, before starting.
An example: One client asked us to finish their home with a textured finish. We came up with solutions that stayed within their budget, without sacrificing quality. In the end, we reduced the overall cost by 20% with excellent results.
Remember, don’t forget the therapist’s cost when budgeting for textured finishes!
To account for all the additional costs and considerations that come with the execution of specialty finishes like faux painting and textures according to A Comprehensive Guide to Estimating the Cost of Specialty Finishes, surface preparation, removal of existing finishes, equipment and tool costs, and travel costs are essential sub-sections to be considered as a solution.
Efficient prepping of the surface is key. Preparation will reduce future maintenance and bring ideal results. Start by cleaning all dirt, grease, and scraps. Then examine to spot any existing issues, such as cracks or holes. Once done, sanding could be required to promote adhesion of paint/coating.
Plus, if there are bumps or uneven parts on the surface, they need to be fixed before going further for a smooth base. Pay attention to moisture fluctuations which can cause peeling of paint soon after application. This must be done to protect your investment for years to come.
Don’t forget to prep that surface – it’s essential for a lasting finish. Don’t miss out on the chance to build a solid foundation by overlooking this step. Don’t worry about removing old finish – it’ll add character to your renovation, or even mold!
Eliminating a prior coating is key, with costs and factors in mind. It can be tricky, needing close attention to the details for the desired outcome. Here’s a 4-step guide for removal:
Remember: Different finishes need specific treatment. Incorrect methods can damage the surface below. Timelines may vary due to weather, age of finish, etc.
Pro Tip: If unsure of DIY removal, get help from a pro. DIY really means ‘Dip into Your Wallet’ for tools and equipment.
For equipment and tool costs, there are many aspects to consider. Expenses vary based on industry and work conditions. See the table below for some associated costs.
Type of Equipment/Tool | Cost (in dollars) |
---|---|
Computers | 700 – 3000+ |
Power Tools | 50 – 5000+ |
Office Furniture | 100 – 4000+ |
Safety Gear | 10 – 500+ |
Repair and maintenance costs should also be considered when calculating total expenses.
It may be wise to rent equipment, instead of buying it. Especially for items used seldomly.
I remember a construction company, which couldn’t afford the equipment for a project. They had to rent, which caused financial strain. It was a lesson in planning and having financial arrangements in place before taking on big projects.
Traveling is fun, but it can empty your wallet quick!
Travel Expenses:
When it comes to journey costs, there are lots of factors that can affect the price. These include:
Plus, there are other expenses to think about like; travel insurance, baggage charges (if applicable), visa applications and vaccinations (regional requirements).
Booking early is a great way to save money and time. Other ways to limit costs include opting for homestays instead of hotels, and investing in travel credit cards for rewards points and exclusive deals. With careful planning, you can get the most out of your budget.
“To estimate the cost of specialty finishes like faux painting and textures, you need to master the estimation process. With the estimation tips shared in this section, you will be able to accurately estimate the material and labor costs. The sub-sections in this segment – Gathering Information, Calculating Material Costs, Calculating Labor Costs, Adding Additional Costs, and Adjusting for Regional Pricing – provide solutions to the most common estimation challenges.”
When estimating, make sure to collect all the project’s details – time, resources, scope – by interacting with stakeholders, gathering requirements, and reviewing documents. Ask for clarification on unclear requirements too.
To get accurate info, it’s important to build a good rapport with stakeholders and ask for clarifications. Interview subject matter experts and research similar projects to spot gaps or challenges. Use data analytics and simulations to inform your estimations.
Use all resources when collecting estimation info, and keep records of findings. Cross-check results often and have peers review your estimates. 50% of software engineering projects face cost overruns from inaccurate estimations (Heitlager et al., 2007). Do sufficient research to avoid this pitfall! Calculating material costs is like playing a game of Jenga – one wrong move and your budget falls.
When it comes to estimating the cost of a project, calculating material expenses is vital. To start, one should do a material cost calculation. Here’s the drill:
by reaching out to multiple suppliers and comparing prices.
I personally experienced this when renovating a home. We researched different flooring options, contacted suppliers for quotes, and compared quality and price. We chose a durable yet affordable option that fit our budget.
Estimating labor costs is like trying to forecast the weather – you can make an educated guess, but you never know what you’ll get.
When you’re estimating project costs, it’s vital to think about ‘Calculating Labor Costs’. A well-structured table can help. For example:
Employee Name | Rate |
---|---|
John | $20 |
Emily | $25 |
Calculate the hours worked by each employee and multiply by their rate. This gives an accurate labor cost estimate.
Unique details, such as overtime hours or different rates, must be taken into account when calculating labor costs. This helps make cost analysis more accurate.
In the past, businesses used manual methods to calculate labor costs and track employee hours. Thanks to technology, software programs can now automate this process and save time/money.
Adding extra costs is like playing Jenga – the tower of expenses grows layer by layer until it collapses!
When it comes to estimating costs, it’s essential to consider all expenses. Here are some tips for factoring in unforeseen costs:
Remember, accurately incorporating additional costs can save you time and money. Plus, keeping a record of added expenses can help with future estimations. By analyzing these records, you’ll get insights about profits and losses due to extra costs.
For example, an IT company was hired for custom software development, but they didn’t factor in specialized hardware. This caused their project budget to be exceeded. Had they planned for additional expenditures while estimating, the experience could have been more productive for both parties. Regional pricing should also be taken into account – nothing says fairness like accounting for different costs around the world.
It is significant to adjust for varied regional pricing in the estimation process. Different pricing models are flourishing in different regions, so this step cannot be overlooked.
Factors to consider include Labor costs, Material costs, Tax rates, and construction regulations. To get a better understanding, a table showing typical data would help.
The table below explains Adjusting Factors for Regional Pricing:
Location | Labor Costs | Materials Costs | Tax Rates | Regulations |
---|---|---|---|---|
City A | $35 | $125 | 6% | Strict |
City B | $30 | $130 | 4% | Moderate |
City C | $25 | $120 | 3% | Lenient |
It is essential to make sure the estimation considers all adjusting factors and region-specific details that may affect project costs. This way, you can refine your budget and avoid costly errors later.
Fluctuations in market prices and new regulations must be taken into account. An adjustment must be made and consistently maintained for accurate estimation.
For instance, one construction company did not adjust for any regional pricing variation, leading to an underestimation of their budget by over 10%. This mistake caused significant delays and extra expenses. To avoid this, ensure proper adjustments for regional pricing.
Estimation may not be an exact science, but with these tips, you can present a convincing estimate.
This guide gives a thorough and helpful way to calculate costs for special coatings like faux painting and textures. Here are some tips:
Remember to think about extra details, for example humidity levels and eco-friendly options. Adding a contingency is also a smart move. It can help reduce unpredicted costs and keep quality results.
Faux painting is a decorative painting technique that imitates the look and feel of other materials, such as marble, wood, or stone.
Textured painting is a technique that adds depth and dimension to a surface by creating various patterns and textures with different tools and materials.
The cost of specialty finishes depends on several factors, including the complexity of the design, the type of materials used, the size of the surface to be painted, and the level of preparation and detail work required.
The time it takes to complete a specialty finishes project varies depending on the size and complexity of the design, the type of materials used, and the level of detail work required. It can range from a few days to several weeks.
While DIY enthusiasts may be able to tackle some specialty finishes projects, it is often recommended to hire a professional with experience in these techniques. They have the expertise and tools to ensure a high-quality, long-lasting finish.
To choose the right specialist for specialty finishes, look for someone with experience in your desired technique, positive reviews and recommendations from previous clients, and transparent pricing and communication throughout the project.
Here I am going to share some steps to get your concrete polishing and staining construction cost estimate report.
You can send us your plan on info@estimatorflorida.com
Before starting your project, we send you a quote for your service. That quote will have detailed information about your project. Here you will get information about the size, difficulty, complexity and bid date when determining pricing.
We do painting construction cost estimating and prepare a detailed report for your project. At last you finalize the report and finish the project.
561-530-2845
info@estimatorflorida.com
Address
5245 Wiles Rd Apt 3-102 St. Pete Beach, FL 33073 United States
561-530-2845
info@estimatorflorida.com
Address
5245 Wiles Rd Apt 3-102 St. Pete Beach, FL 33073 United States
All copyright © Reserved | Designed By V Marketing Media | Disclaimer
IMPORTANT: Make sure the email and cell phone number you enter are correct. We will email and text you a link to get started.
By clicking “I Agree” above you give Estimate Florida Consultin express written consent to deliver or cause to be delivered calls and messages to you by email, telephone, pre-recorded message, autodialer, and text. Message and data rates may apply. You are able to opt-out at any time. You can text STOP to cancel future text messages.