A Wining Cost Estimate
That Helps You To Win More Masonry Construction Projects
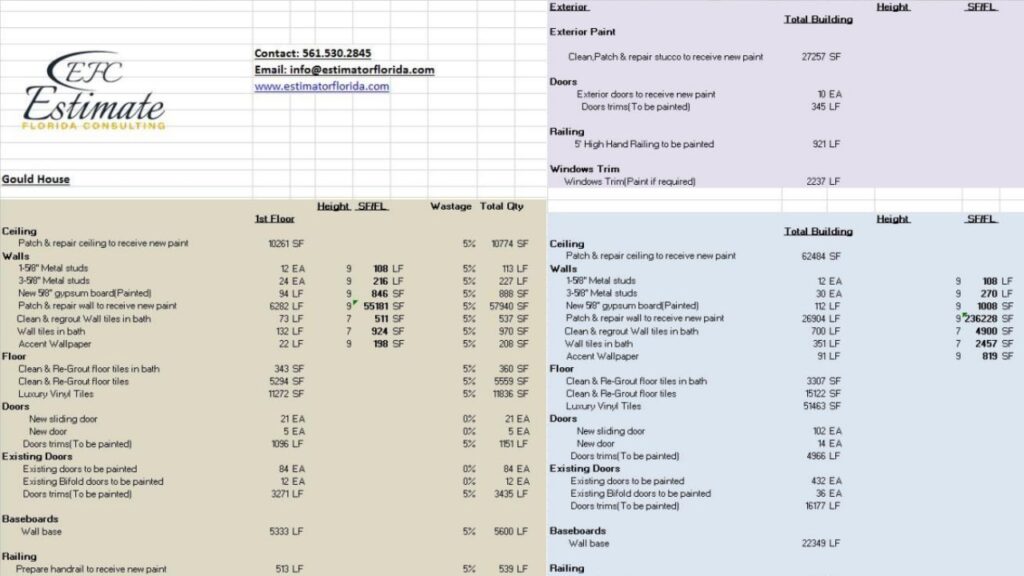
An in-depth analysis of estimating masonry projects using digital tools and techniques.
Key Takeaways | Industry leading practices |
---|---|
Tools and Technologies | Tips and Tricks |
This table summarizes the key takeaways, industry-leading practices, tools, and tips for understanding how to estimate Masonry projects using the latest digital tools and techniques available. Learn how to get the most accurate estimates quickly with confidence as we explore masonry estimators in detail.
For a comprehensive understanding of the subject matter, it’s essential to look beyond price estimation into resource optimization. From choosing the right equipment to understanding your team’s workflow breakdown, every small detail can be optimized with smart planning.
Pro Tip: A successful estimate requires walking through every possible aspect of the project in detail. To achieve this, gather as much information about the project’s requirements as possible before beginning any estimation task.
Estimating masonry costs without a proper estimator is like building a wall without bricks – it’s bound to crumble.
Masonry estimators are essential tools in the construction industry. Accurate estimates help contractors to bid competitively and increase their chances of winning contracts. In addition, precise calculations and projections ensure that materials are properly sourced, sufficient labor is available, and costs are well-controlled. This leads to the timely completion of projects within budgetary constraints.
By using masonry estimators, contractors can streamline their work processes. These digital tools allow easy calculation of all project-related costs, like labor cost and material requirements. This minimizes the risk of errors and omissions typically made when making manual estimates. With such a structured approach, professionals achieve a higher degree of efficiency by cutting down on the time spent on such calculations.
An important aspect that cannot be neglected is how masonry estimators enable accurate budgeting for projects. Contractors get insights into vital aspects like total expenses on labor or material procurement needed to execute tasks adequately. They also provide an approximation of the total cost borne by clients.
One contractor’s experience comes to mind when discussing how crucial these tools are: when he was presenting his estimate for a job to a client without using an estimator, he was too high with his estimate. The client then asked him why it needs to be so much. It created fear and concern about value for money before building works began. However, after employing a masonry estimator tool into his projects, he could always assure his clients about adequate estimation optimized for optimal results while minimizing costs – thus creating more reliable business bonds with happy customers at considerably lower dwell time showing competitiveness in getting even more jobs done easily in shorter time frames costing less initially yet generating more profits later as demand increased over time through better services rendered than other competitors who improvised their estimates leading them to losses eventually due to inadequate generation business not properly balanced from inception caused by improper evaluation due to inadequate planning triggered from opening scenes where no proper work processes were established based on the ideal foundation provided via appropriate estimations.
Counting bricks has never been so exciting – get ready to learn about the essential components of a masonry estimator!
To understand the components of masonry estimator with estimating software tools, take-off sheets, and project management tools as solutions to streamline the estimation process for your project. These sub-sections will help you learn about different tools that can help you in your masonry estimation process and help you complete your masonry projects more efficiently.
Software for Material Estimation
Estimating software tools assist in calculating the amount of construction material required for a project. These tools provide an accurate estimation of materials, costs, and budget planning.
The following table highlights some critical components of masonry estimating software:
Component | Function |
---|---|
Material Catalogue | Provides a detailed list of available materials |
Quantity Takeoff | Calculates the volume, cost, and quantity of materials |
Project Scheduling | Helps plan out the timeline and resources needed for tasks |
Cost Tracking | Monitors actual job expenses against estimated budgets |
In addition to intuitive functionality, these software tools help builders to eliminate inaccuracies in their estimations. They enable teams and builders to function better while adhering to tight deadlines and budgetary constraints.
It is essential to have an accurate system to prevent under or overspending on the project. Story has it that without a solid material estimation tool, many projects faced difficulties staying within budget constraints.
Get ready to take off with these sheets, but don’t worry, no airplanes are involved in this masonry estimate.
For professionals in the masonry field, take-off sheets are an essential part of estimating project costs. These sheets are used to measure and calculate the necessary materials required for a particular job. Using specific data from project blueprints, these estimates help ensure accurate budgeting and efficient planning.
Below is an example of how take-off sheets can be structured, using actual data:
Item Type | Quantity Needed |
---|---|
8″x8″ CMU | 500 |
4″x16″ Brick | 2500 |
It’s important to note that each take-off sheet will vary depending on the unique requirements of a project. However, they all serve the same purpose of providing detailed material estimates.
Pro Tip: It’s useful to use digital tools for creating take-off sheets, as they can streamline the process and reduce errors.
If project management was easy, everyone would do it…oh wait, they do.
Project Management Tools are vital in ensuring the success of your masonry project. Some tools that could be used for effective project management are:
While Project Management Tools are vital in ensuring the success of your masonry project, it is also important to choose the right tool depending on project size, complexity and duration.
Project management has been in existence since ancient times; there is evidence from large projects such as the construction of The Great Pyramids in Egypt where planning tools were used to keep track of workers and resources. Today’s Project Management tools have evolved to incorporate more sophisticated technology capable of handling complex data sets.
Get ready to stack up your knowledge on masonry estimation, because the only thing worse than a crooked wall is a faulty estimate.
To prepare for masonry estimation with the help of “The Complete Guide to Masonry Estimator”, you need to analyze project plans, develop a material list, and estimate manpower and time. Analyzing the project plans closely will help you understand the necessary materials and the amount needed. Developing a material list will help keep track of the supplies and ensure smooth progress. Estimating the manpower and time is crucial in delivering the project on time and within budget.
For effective Masonry Estimation, it’s crucial to assess project plans. Assessing the scope and analyzing specifications can make or break a construction project.
Analyzing Project Plans:
Column 1 | Column 2 |
---|---|
Identify and understand scope | Review architectural drawings |
Determine material requirements | Evaluate floor plans |
Estimate labor costs | Account for project timeline |
By assessing all these factors, masonry contractors can get a clear picture of the necessary resources (time, money, materials) for smooth execution.
It is possible that the client may provide hidden details or may have special requests/eventualities which should be taken into consideration while studying plans.
Did you know that according to a study conducted by Dodge Data and Analytics in 2019, nearly 57% of North American Contractors were using BIM (Building Information Modelling) extensively?
Who needs a shopping list when you can just wing it during a masonry project? Just kidding, always develop a material list to avoid a literal crumbling mess.
One important aspect of estimating for a masonry project is determining the required materials. This involves carefully developing a list of all necessary items needed to complete the job.
It’s also crucial to keep in mind any special requirements or considerations unique to your particular job site or project when developing your material list. This can include factors such as accessibility challenges or environmental concerns like water runoff. Interestingly, developing a detailed material list is not only important for current planning processes but has been integral throughout history in architectural marvels such as The Great Wall of China where an army of soldiers developed meticulous inventory records covering every aspect from food provisions, bedding supplies- ropes & lashings- transportation support etc., which aided smooth running & maintenance over centuries despite being located across fluctuating terrains making it one of world’s oldest & most reliable construction monuments. Estimating manpower and time is like trying to predict the weather – you’re never quite sure how many workers and how much time you’ll need until you’re knee-deep in the project.
Estimating the number of workers required and timeframe for a masonry project is crucial before commencing any construction work. Accurate estimation is important to keep the project within budget, ensure on-time completion and improve efficiency.
To estimate manpower and time for masonry, a table can be created that includes columns such as task description, estimated hours per task, workers needed, total hours and number of days required. For instance, tasks can include site preparation, foundation laying, brickwork installation, and finishing work. The estimated hours per task may vary depending on the type of work and complexity of the project.
Task Description | Estimated Hours per Task | Workers Needed | Total Hours | Number of Days Required |
---|---|---|---|---|
Site Preparation | 10 hours | 3 workers | 30 hours | 4 days |
Foundation Laying | 20 hours | 5 workers | 100 hours | 10 days |
Brickwork Installation | 40 hours | 6 workers | 240 hours | 24 days |
Finishing Work | 20 hours | 4 workers | 80 hours | 8 days |
It is important to consider different factors that can affect manpower and time estimation. The availability of resources such as materials, equipment, and machinery can impact the productivity rate. Weather conditions can also have an impact on how quickly work can be done.
A client once requested an estimate for a large commercial masonry project. After conducting a thorough analysis of the project requirements including material sourcing restrictions, our team was able to provide an accurate estimate for manpower and time which allowed us to complete the project ahead of schedule while staying within budget. Effective estimation helps ensure successful completion of projects.
Get ready to do some heavy lifting – estimating masonry materials is not for the weak!
Maximize your masonry construction business’s potential with our competitive financing options
To estimate the masonry materials required, you need to be precise. This requires careful planning and meticulous calculations. In order to help make this process simpler, we introduce the brick estimation, block estimation, and mortar estimation sub-sections.
For efficient construction work, it is essential to detect the number of bricks required for a particular project. Accurately calculating brick estimation is crucial as it minimizes wastage and helps in budgeting.
The following table provides an assessment of brick requirements based on wall dimensions. The table includes columns for height, length, width, brick size in inches, joint thickness in inches, and the number of bricks required:
Height | Length | Width | Brick Size (in) | Joint Thickness (in.) | Number of Bricks |
---|---|---|---|---|---|
10 ft | 20 ft | 8 in. | 2x4x8 | .5 | 8280 |
It is advisable to add extra bricks in case they get damaged during usage or some other unforeseen events. Additionally, one must account for doors and windows that are installed within the wall.
In ancient times, brick estimation was done manually by expert masons who had excellent spatial intelligence. Now due to the advancement in technology, we can calculate materials electronically using modern software like AutoCAD. Who needs a crystal ball to estimate masonry materials? Just grab a calculator and stack those blocks like a boss.
Quantifying the Material for Masonry Construction
Masonry construction comprises of building structures using brick, concrete blocks, cement and other similar materials. Estimating the required amount of materials is crucial to avoid wastage or overspending.
Below is a detailed table for Block Estimation that highlights the necessary information.
Block size | Quantity per wall (8 feet) | Quantity per 100 sq.ft |
---|---|---|
4 inch | 64 | 120 |
6 inch | 47 | 88 |
8 inch | 35 | 64 |
It is essential to consider other factors that may increase material requirements such as pilasters, corner returns, or bond beams. Additionally, it is crucial to confirm the durability of mortar used depending on site conditions.
The use of concrete blocks dates back to ancient times when mud bricks were prevalent in many regions. The concept of masonry construction originated in the Indus Valley civilization over four thousand years ago and evolved independently worldwide. In modern times masonry construction has seen technological advancements and a significant contribution in this evergrowing field can be seen through precision block estimation techniques.
Want to know the key to perfect mortar estimation? Just remember: it’s all about mixing accuracy with bricklaying finesse.
Accurately computing the amount of mortar for masonry is essential to any construction project. Proper Mortar Estimation guarantees that there will be no wastage or shortages in material quantities, resulting in cost savings. Below is a table that lists various factors to consider when estimating the amount of mortar required.
Factors | Quantity |
---|---|
Number of Bricks Required | 6000 |
Brick Dimensions | 8″ x 4″ x 2″ |
Mortar Thickness (inch) per Brickwork Layer | 0.5 – 1 inch |
Mortar Mix Ratio (Cement:Sand ratio) | 1:4, or as required |
Unique details to consider when computing mortar quantities are water absorption rates for bricks and block walls, variations in rebar spacing, and soil type. These variables affect the durability of the structure. It is always preferable to use more durable materials than estimate only for settling costs.
Mortar estimation has been integral to masonry since ancient times when humans started using crude materials like mud and straw mix to bind bricks or stones together. However, innovations in science have drastically improved modern methodologies resulting in increased levels of precision and durability with which we can build monumental structures today.
Laboring over estimating masonry labor can feel like building a wall without mortar.
To accurately estimate masonry labor with masonry contractor wages and project timeline estimation as solutions, this section will provide you with the necessary information. You will learn how to determine the hourly wages of masonry contractors and estimate the duration of masonry projects.
When it comes to the compensation provided for masonry services, it is necessary to take into account several factors. Factors like experience, location and market conditions all contribute to determining the wages of a masonry contractor. Taking these factors into consideration can help in estimating the fair compensation for their labor.
Considering masonry contractor wages, experience plays an impactful role in determining their earning potential. Masons with years of experience earn more than the newly employed ones with little or no experience at all. The location also contributes as wages are determined by the city’s cost of living. Moreover, market competition affects it too.
Additionally, benefits like health insurance and paid time off should be considered when determining their overall compensation package.
Determining masonry contractor labor costs accurately is vital for successful projects within budget limits while providing fair wages for workers. Without accurate estimates, labor costs may skyrocket and may result in losing profitability or even ruin the project.
If you’re planning to hire a masonry contractor for your project, it is important not only for budget purposes but also to ensure worker protection by providing fair pay; making sure you estimate their compensation package accurately. By doing so, you will not only get quality work done but also avoid any issues arising from insufficient compensation.
Nothing gets a project completed quicker than estimating the timeline with the precision of a 3-year-old trying to clean their room.
A detailed table can be created to estimate the timeline of a masonry labor project, consisting of columns such as Task/Activity, Duration in Days, Start Date, and End Date. Including this information can help contractors set realistic deadlines and manage expectations.
It is important to note that unexpected issues may arise during any project that could cause delays. As such, it is imperative to allow some wiggle room in scheduling to avoid disappointing clients or investors.
To ensure success in any construction project, it is vital to consider how long each task will take before starting the work. Accurate Project Timeline Estimation is an essential part of this process. Don’t miss out on potential opportunities by neglecting proper timeline planning.
If you’re anything like me, estimating the cost of a masonry project is about as easy as predicting the weather in space.
To estimate the cost of your masonry project with ease, turn to the section ‘Estimating the cost of Masonry Projects’ with ‘Calculating Total Materials Cost, Calculating Total Labor Cost, and Finalizing the Project Budget” as the solution. Here, you’ll learn the process of calculating the total cost of materials and labor involved in the project. Lastly, you’ll get expert guidance on finalizing the project budget.
To ascertain the cost of materials for masonry projects, one would need to compute the total cost of all required materials.
The following table outlines various factors that professionals take into account when calculating the total materials cost:
A detailed table can be created to estimate the timeline of a masonry labor project, consisting of columns such as Task/Activity, Duration in Days, Start Date, and End Date. Including this information can help contractors set realistic deadlines and manage expectations.
It is important to note that unexpected issues may arise during any project that could cause delays. As such, it is imperative to allow some wiggle room in scheduling to avoid disappointing clients or investors.
To ensure success in any construction project, it is vital to consider how long each task will take before starting the work. Accurate Project Timeline Estimation is an essential part of this process. Don’t miss out on potential opportunities by neglecting proper timeline planning.
If you’re anything like me, estimating the cost of a masonry project is about as easy as predicting the weather in space.
Materials | Quantity | Unit Cost ($) | Total Cost ($) |
---|---|---|---|
Bricks | 1200 | 0.50 | 600 |
Cement | 30 | 12.00 | 360 |
Sand | 2 | 50.00 | 100 |
Water | – | – | Free |
As can be seen from the table, this estimation involves identifying the necessary materials and their quantity while taking into consideration their corresponding unit cost.
It is essential to keep in mind that additional expenses such as transportation costs and labor charges may also influence overall expenses.
Pro Tip: Always calculate a little extra than what is required in case of unforeseen circumstances during masonry projects.
Want to know the cost of labor for your masonry project? Just remember to factor in the price of a strong back and a lot of patience.
To compute the overall expense of Masonry Projects, calculating the sum of Labor costs is an essential step. Accurately expensing for labor assures budget control and project profitability.
A visual representation to estimate the labor cost for a customary masonry project is shown below:
Task | Number of Workers | Work Hours Required |
---|---|---|
??? | ?? | ?? |
??? | ?? | ?? |
After listing all the necessary tasks that need to be performed during a masonry project, specify the number of workers required for each task and the hours needed to complete it. This will allow us to ascertain the total labor cost effectively.
For instance, disregarding specific expenditures such as rates and specialty tools will give you a general concept of how much a residential masonry job should cost. Enterprising these specifics unveil obvious benefits concerning profitability.
It is evident that accurate estimation of labor costs for any construction project would result in constructing better budgets and accurately bidding projects that are being tendered.
Before you finalize that budget, make sure to leave some extra cash for the inevitable masonry apocalypse.
To Incur the Final Expense for Masonry Projects
One of the primary tasks in any construction project is to determine the final expense. This is no different when it comes to masonry projects. Calculating the cost involved before initiating the project and finalizing the budget helps in curbing unexpected expenses and delays.
The Final Estimation Table
Column 1: Task Details | Column 2: Labor Cost (per hour) | Column 3: Material Cost | Column 4: Equipment and Machinery Cost | Column 5: Total |
---|
True fact, as stated by The Balance Small Business, “Masonry work requires consistent craftsmanship and attention to detail to ensure a quality build.”
Other Vital Aspects of Budget Planning
Once all the explicit costs associated with labor, equipment, and materials are noted down, consider other implicit ones too like transportation charges, external utility connections, inspection fees etc. These can fluctuate based on location and project magnitude.
Careful estimation of a masonry project’s budget is essential for smooth workflow and can help avoid unnecessary expenses. By dedicating sufficient time to developing an accurate estimate table, projects can be completed successfully within projected costs.
Managing masonry projects is like playing Jenga – one wrong move and the whole thing comes crashing down.
To manage masonry projects successfully, you need to schedule tasks, communicate with stakeholders, and monitor and control progress. These sub-sections will help you understand how to break down your project into manageable parts, keep everyone informed and involved, and track progress against your goals.
Efficient planning and organizing of tasks is integral in the successful completion of Masonry Projects. Assigning them according to priority, resources available and timelines set are key factors to take into account when scheduling tasks.
A 6-step guide for task scheduling that can streamline masonry projects includes:
Effective communication with contractors and clients is crucial in keeping everyone up-to-date with progress and changes made to the original schedule.
To avoid delays especially due to unforeseen circumstances such as extreme weather conditions, it’s important to factor in some buffer time while creating schedules.
History shows that many Masonry projects falter due to poor scheduling practices leading to faulty coordination amongst project participants resulting in cost overruns, missed deadlines and increased risks in terms of safety and quality issues for both workers and future users alike.
Remember, communicating with stakeholders is like playing Jenga: one wrong move and the whole project comes crashing down.
When handling masonry projects, it is vital to establish an efficient means of communicating with those who have a vested interest, otherwise known as stakeholders. Ensuring your project progresses harmoniously requires clear and concise communication with your team, clients, suppliers, inspectors and even members of the public. As a result, it’s essential to put together a detailed plan that outlines each individual’s role within the project and how you intend to communicate progress updates.
Efficient communication can help mitigate risks before they arise through stakeholder monitoring and continual engagement. Stakeholders can provide insights into different aspects of the project that could go unnoticed without their input; this enables risks to be identified early on, avoiding costly delays or rework later down the line. Using mobile apps or online platforms such as WhatsApp groups or Trello boards can significantly streamline communications between all stakeholders involved in the project.
Relationship building is also crucial in maintaining good communication during any construction project, where stakeholder engagement is critical. Project managers should regularly schedule meetings with stakeholders, exchange emails or make phone conference calls at periodic intervals to foster a deeper understanding of one another’s concerns. Taking action based on feedback received from these engagements shows stakeholders that their opinions matter which promotes trust and transparency throughout the project life-cycle.
Many site managers make the mistake of overlooking effective stakeholder communication channels by prioritising technical issues over stakeholder interaction. Case studies have shown time and again that poor stakeholder management can lead to unhappy clients, work stoppages, reputation damage for companies amongst other downsides leading to financial losses for all parties involved in construction projects.
Understanding who your stakeholders are and aligning needs that meet their expectations is one way of guaranteeing success when it comes to communicating about critical masonry projects such as reinforced concrete works for residential high-rises or brickworks for government infrastructure.
Building relationships with stakeholders through open, clear lines of communication can often be what sets one contractor apart from another when pursuing similar projects.
Watching masonry being built is like watching paint dry, but with more bricks involved.
To ensure the smooth execution of a masonry project, it is crucial to maintain constant surveillance and governance of all activities involved. This process can be referred to as Supervisory and Regulatory Practices.
It is essential to keep an open mind during this process since prospective obstacles may require one to deviate from initial plans. Ensure that each stage leading to completion reflects progress as per set milestones.
By constantly inspecting project advancement and implementing a supervisory strategy in place, risk associated with inefficiency or inadequate results is mitigated. Stay proactive in keeping everything aligned while encouraging worker efficiency. Failure is imminent when details aren’t monitored in real-time.
Don’t be left behind – allow effective supervision and regulation practices lead your next masonry project towards victory! If estimating masonry projects was easy, everyone would be a bricklayer. Unfortunately, it’s more like playing Jenga with your budget.
To tackle common challenges in masonry estimation for your project with “The Complete Guide to Masonry Estimator,” you must identify hidden costs, account for waste, and adjust your estimate when changes occur. These sub-sections will discuss how to overcome these obstacles and provide solutions to ensure an accurate masonry estimation.
When estimating masonry work, it can be challenging to identify costs that are not immediately visible. These hidden expenses include factors such as material waste, site preparation, and project management. Failure to account for these expenses can lead to budget overruns and delays.
One way to address hidden costs is to conduct a thorough site evaluation before beginning work. This evaluation can identify potential challenges such as difficult access or soil conditions that may require extra preparation. Additionally, using digital tools such as 3D modeling software can help anticipate material needs and reduce waste.
It’s crucial to communicate with all stakeholders involved in the project, including subcontractors and suppliers, about their role in managing cost. Clear communication can prevent misunderstandings and ensure that everyone is on the same page when it comes to budgeting.
Identifying Hidden Costs has been a common challenge in masonry estimation since the inception of modern construction techniques. A misstep in calculating actual costs or technology may cause a project catastrophe – damaging both trust and profit margins. Therefore, it’s important to grow aware of missteps when they occur to avoid repeating them in future works.
Calculating waste in masonry estimation is like trying to count the number of no-shows at a family reunion – you know it’s going to happen, but you can never quite predict just how much.
When estimating masonry projects, it is crucial to account for material loss due to waste. This can occur due to various reasons such as cutting bricks or blocks, breakage during installation, and leftover materials that cannot be used in the project.
To accurately calculate the required amount of materials while also accounting for waste, it is essential to consider the type and size of materials being used. Additionally, reviewing past projects and determining the amount of waste incurred can help in predicting future losses.
Incorporating a contingency factor in the estimate also helps account for potential waste that may occur during the construction process. It is essential to include this factor as an allowance to cover any unexpected issues that may arise.
Taking accurate measurements of the site and using precision tools can further reduce material waste while also ensuring correct estimates. Reusing scraps from previous projects can also help save money and minimize overall wastage.
By considering material loss due to waste and taking preventive measures during estimation, contractors can better manage project costs while ensuring timely completion.
Ah, project changes – because who doesn’t love a good plot twist in their masonry estimation journey?
As construction projects progress, unforeseen changes arise which can lead to adjustments in masonry estimates. These modifications may include alterations in building plans, materials, or timelines. Adjusting for such project changes is vital to ensure accurate cost estimation and successful completion of the project.
To adjust for project changes in masonry estimation, it is essential to keep track of all modifications made through a change order process. This involves documenting the nature of the change, its impact on the quantity and quality of work needed, and the additional resources required. Communication with all stakeholders involved in the project is also important to ensure transparency and accountability.
One challenge when adjusting for project changes is estimating the appropriate markup percentage for overhead costs. The markup percentage should account for additional expenses incurred due to a change but not overprice or undercharge the client. Overhead costs can include administrative expenses, equipment rental fees, and labor burden costs.
In some cases, project changes may necessitate revising a masonry unit’s unit rate. For example, structural design changes could affect bracing requirements or affect reinforcing steel quantities. It is important to evaluate these factors when adjusting unit rates as failure to do so could result in cost inaccuracies or potential losses.
History has shown that failure to adjust for project changes has led to substantial legal disputes between contractors, inspectors and clients due to miscommunication or unaccounted costs. Proper documentation and communication throughout the project can help mitigate these risks while ensuring an accurate masonry estimate.
Get your estimates right, or you’ll end up with a wall full of regrets – and not the kind you can just plaster over.
To improve your masonry estimation skills, you need to follow some best practices. In order to do so, you should start with obtaining continuing education and work with experienced masonry contractors. Additionally, utilizing estimating software effectively can increase your efficiency. These sub-sections will provide you with the solutions for achieving success in the masonry estimation field.
As estimators, it is essential to have continuous learning opportunities.
Continuous Professional Development for Estimators allows them to stay up-to-date with industry changes, technologies and best practices and enhance their skills. Regular workshops, conferences and online courses are great ways for estimators to learn from experts in the field. Additionally, networking with other professionals can provide valuable insights into what works well in estimating practices.
In this fast-paced industry, staying current on emerging trends is critical. Continuing Education for Estimators ensures that they have the expansive knowledge base required to estimate masonry projects accurately. This includes being aware of new products and techniques which may impact pricing or quality expectations.
Learning from past projects is just as crucial as keeping current for Estimators. Collecting data on construction timelines, costs and performance metrics provides valuable insights into potential challenges others have faced in estimating similar projects.
According to an industry report by the Mason Contractors Association of America (MCAA), better Estimating results in greater profitability and improved project management overall.
In summary, continuous education is instrumental in keeping up-to-date with new industry standards, technologies and practices while also building invaluable relationships with peers which facilitate knowledge-sharing. Working with experienced masonry contractors is like having a trusted brick in the wall of your building project.
When collaborating with seasoned masonry professionals, it is essential to communicate a clear project scope, specific requirements and timeline. Working with experienced masons ensures quality workmanship, detailed quotations and accurate material estimates. They can leverage their extensive knowledge of local codes, regulations and industry standards to provide efficient solutions for your masonry needs.
Furthermore, contractors can advise on cost-effective and sustainable construction methods that deliver long-term value. Besides providing competitive pricing and managing the procurement process, experienced masonry contractors will guarantee timely completion of your project while minimizing disruptions to adjacent areas.
To avoid unwarranted delays or extra expenses in the course of construction projects, it is crucial to engage skilled and reputable contractors early on. By fostering good relationships with stone- or brick-masons who share your vision, you can execute successful projects that meet quality expectations.
For instance, a client we worked with knew just what they needed – retaining walls on both sides of their driveway to prevent erosion but were uncertain about the materials to use. Upon assessment, we advised them on durable limestone block finishes that matched the house’s existing stonework. The client was pleased with our attention to detail and expertise.
When it comes to estimating software, remember: Garbage in, garbage out…but at least it does the math for you.
Masonry estimating software can significantly improve accuracy and efficiency in estimation processes. However, to use it effectively, proper training is necessary for comprehensive utilization and implementation. The use of shortcut keys, multi-tasking, and customization options can further enhance productivity.
Moreover, ensuring the masonry estimation software is up-to-date with current market pricing is crucial to providing reliable estimates. Collaborating with suppliers and subcontractors when setting up the software can also streamline communication and provide real-time updates on material availability.
Additionally, embracing various features such as drag-and-drop functionalities or digital takeoffs can further streamline the masonry estimation process while minimizing human error.
To stay competitive in the industry, utilizing masonry estimating tools must be a priority. By dedicating time to training and staying up-to-date with technological advancements, businesses can improve efficiency in their operations and increase profitability.
Implementing these strategies within your company today could lead to improved results tomorrow. Don’t wait until you’re left behind; take action now.
A masonry estimator is a professional who evaluates and estimates the cost of masonry work on construction projects.
A masonry estimator should have knowledge of materials and techniques used in masonry work, as well as experience in project management, cost analysis, and estimating software.
A masonry estimator can work on a variety of construction projects, including residential and commercial buildings, bridges, retaining walls, and other masonry-related infrastructure.
If you are planning a masonry project and want accurate cost estimates, it is highly recommended to enlist the services of a professional masonry estimator. They can help ensure your project is completed within budget and on time.
The cost of hiring a masonry estimator varies depending on the project’s size and scope. However, working with a skilled professional can lead to cost savings in the long run by identifying potential issues before they become major problems.
Accurate estimation is crucial in millwork projects because it ensures that the project stays within budget and is completed on time. A reliable estimate also helps the client make informed decisions about the project and gives contractors a clear understanding of the scope of work.
Here I am going to share some steps to get your masonry construction cost estimate report.
You can send us your plan on info@estimatorflorida.com
Before starting your project, we send you a quote for your service. That quote will have detailed information about your project. Here you will get information about the size, difficulty, complexity and bid date when determining pricing.
We do masonry construction cost estimating and prepare a detailed report for your project. At last you finalize the report and finish the project.
561-530-2845
info@estimatorflorida.com
Address
5245 Wiles Rd Apt 3-102 St. Pete Beach, FL 33073 United States
561-530-2845
info@estimatorflorida.com
Address
5245 Wiles Rd Apt 3-102 St. Pete Beach, FL 33073 United States
All copyright © Reserved | Designed By V Marketing Media | Disclaimer
IMPORTANT: Make sure the email and cell phone number you enter are correct. We will email and text you a link to get started.
By clicking “I Agree” above you give Estimate Florida Consultin express written consent to deliver or cause to be delivered calls and messages to you by email, telephone, pre-recorded message, autodialer, and text. Message and data rates may apply. You are able to opt-out at any time. You can text STOP to cancel future text messages.