- Homepage
- Porcelain Slab Shower Walls in Tampa
Porcelain Slab Shower Walls in Tampa
Leading provider of porcelain tile installation services
Porcelain slabs have emerged as a premium choice for shower wall installations in Tampa, Florida, combining aesthetic elegance with durability and low maintenance. For construction professionals, understanding the cost dynamics of porcelain slab shower walls is critical to delivering high-quality projects within budget. At Estimate Florida Consulting, we provide precise cost estimates, material takeoffs, 3D visualizations, scope reviews, and professional porcelain tile installation services to ensure projects are completed efficiently and within budget. Whether you’re working on a residential property or a commercial project, our expertise helps ensure accurate projections, reducing costly surprises and ensuring the best outcomes.
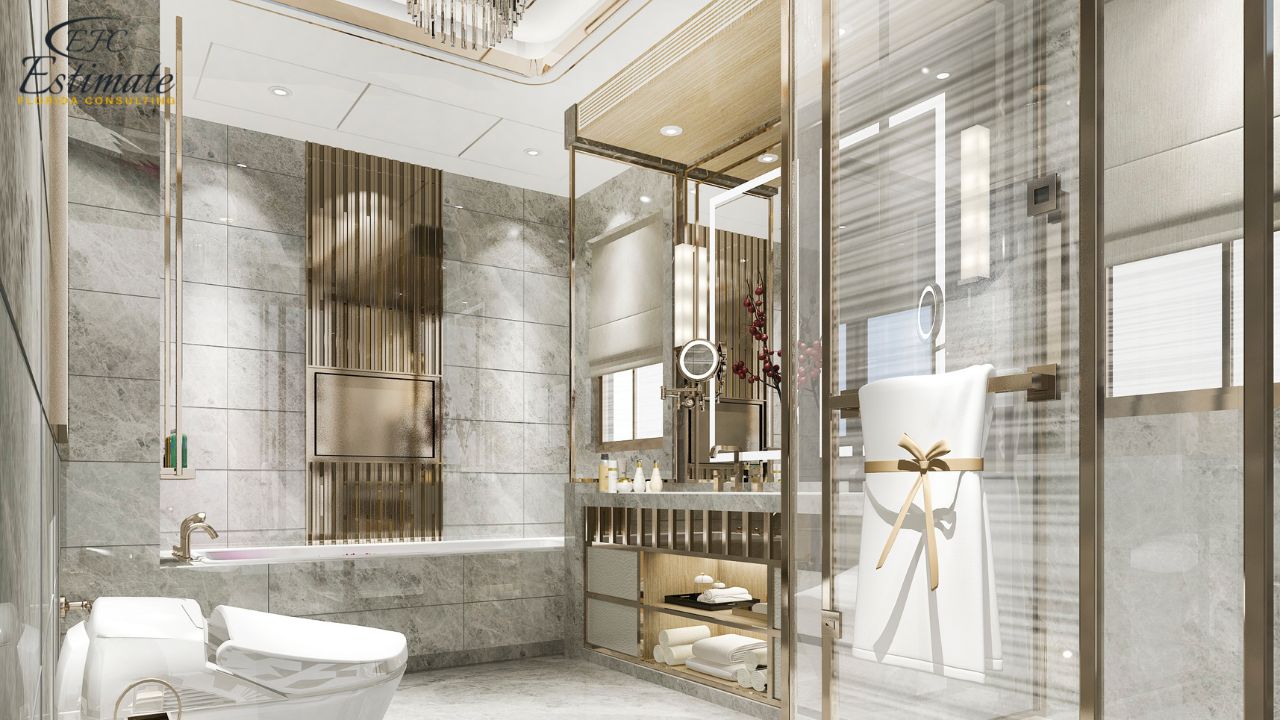
Why Porcelain Slabs for Shower Walls in New Construction in Tampa?
Porcelain slabs are manufactured from refined clay fired at high temperatures, creating a dense, non-porous material ideally suited for shower walls in Tampa’s humid, coastal climate. Their exceptional water resistance prevents moisture penetration, reducing the risk of mold and mildew, a critical factor in Florida’s high-moisture environments. In new construction, driven by Tampa’s population growth and real estate development, porcelain slabs meet the demand for durable, low-maintenance, and visually appealing shower wall solutions. Available in large-format sizes and finishes mimicking natural stone, they provide a seamless, luxurious aesthetic with minimal grout lines. Additionally, their resistance to staining and fading ensures longevity despite exposure to intense sunlight and humidity, making them a top choice for high-end residential projects.
Cost by Type Porcelain Slabs in Tampa
The type of porcelain slab significantly impacts material costs, with variations based on manufacturing and design complexity.
Type | Cost Range | Description |
Standard Porcelain Slabs | $8–$15 per sq. ft. | Machine-made, uniform patterns; cost-effective for mid-range projects. |
High-End Porcelain Slabs | $15–$30 per sq. ft. | Intricate designs, natural stone-like finishes; ideal for luxury residences. |
Ultra-Thin Porcelain Slabs | $20–$40 per sq. ft. | Lightweight, 3–6 mm thick; suited for renovations with weight constraints. |
90% More Chances to Win Porcelain tile Bids with
Our Estimate!
Costs by Material Porcelain Slabs in Tampa
Material costs encompass porcelain slabs and supporting components required for installation.
Material | Cost Range | Description |
Porcelain Slabs | $8–$30 per sq. ft. | Primary material, varies by quality and design. |
Backer Board (60” x 32” shower) | $50–$80 per shower | Cement board for stability; alternatives like green board are less durable. |
Adhesives and Grout | $1–$3 per sq. ft. | Thin-set mortar and epoxy grout for water resistance. |
Waterproofing Membranes | $2–$5 per sq. ft. | Essential for code-compliant, water-tight installations. |
Five Critical Considerations for Porcelain Slab Shower Walls
To ensure project success, focus on these five critical considerations:
- Building Code Compliance: Adhere to Florida Building Code (FBC) requirements, including waterproofing membranes and ventilation (50 CFM minimum exhaust fans). Non-compliance risks failed inspections and $500–$2,000 in rework costs.
- Structural Integrity: Heavy slabs (15–20 lbs per square foot) require robust wall framing. A structural engineer’s assessment ($100–$200 per hour) may be needed, especially for older homes, to avoid structural issues.
- Installation Precision: Large-format slabs demand precise cutting and leveling to prevent uneven surfaces or seams. Certified tile installers ensure quality but increase labor costs ($5–$15 per square foot).
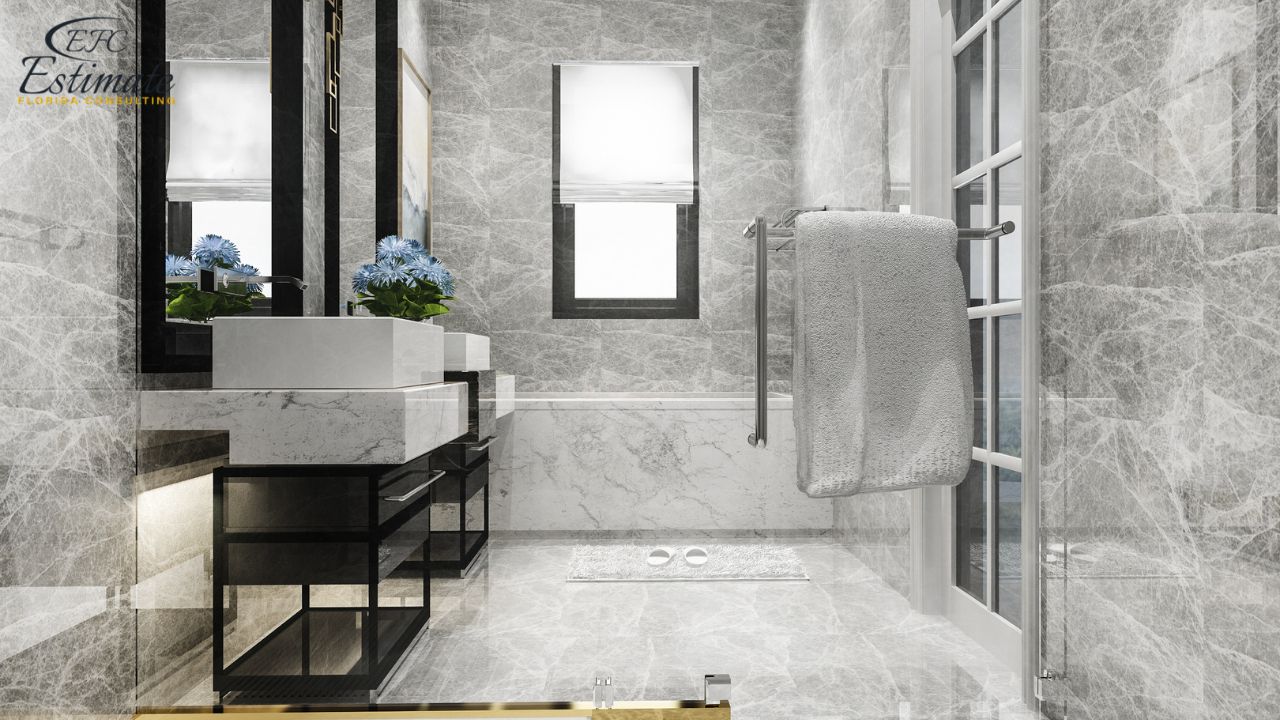
- Climate-Adapted Materials: Tampa’s humid, coastal climate accelerates mold growth. Use high-quality epoxy grout and waterproofing systems ($1–$5 per square foot) to prevent repairs ($1,000–$3,000).
- Supplier Reliability: Source from reputable local suppliers to ensure quality, availability, and compliance with standards (e.g., ANSI A137.1). Local sourcing reduces delivery fees ($100–$300) and ensures timely supply.
Cost by Size Porcelain Slabs in Tampa
Shower size directly influences material and labor costs, with larger showers requiring more resources.
Shower Size | Material Cost | Labor Cost | Total Cost |
Small (32” x 32”) | $200–$600 | $300–$800 | $500–$1,400 |
Standard (60” x 32”) | $400–$1,200 | $500–$1,500 | $900–$2,700 |
Large Walk-In (72” x 48”) | $800–$2,400 | $1,000–$3,000 | $1,800–$5,400 |
Repair Costs Porcelain Slabs in Tampa
Porcelain slabs are durable, but repairs may be needed for damage or installation issues.
Repair Type | Cost Range | Description |
Crack or Chip Repair | $100–$300 per incident | Epoxy fillers for minor damage. |
Retiling Small Sections | $200–$600 per section | Replacing damaged slab sections, including labor and materials. |
Water Damage Behind Slabs | $3.75–$10 per sq. ft. + $350–$1,100 | Repairs for leaks, including mold remediation. |
We Provide 3D Rendering Services!
For Porcelain Tiles and Other Projects
Turnaround time is 1-2 days.
Win More Projects With Us
Replacement Costs Porcelain Slabs in Tampa
Replacement costs arise from aesthetic upgrades or severe damage requiring partial or full reinstallation.
Replacement Type | Cost Range | Description |
Full Replacement (60” x 32” shower) | $2,000–$5,000 | Includes demolition ($300–$500), materials, and labor. |
Partial Replacement | $500–$1,500 | Replacing a single slab or section. |
Conversion (Tub to Walk-In Shower) | $1,800–$4,430 | Excludes additional plumbing modifications. |
Maintenance Costs Porcelain Slabs in Tampa
Porcelain slabs require minimal upkeep, but periodic maintenance ensures longevity.
Maintenance Type | Cost Range | Description |
Sealing (Textured Finishes) | $100–$200 per application | Required every 2–3 years for some high-end slabs. |
Cleaning (Annual Supplies) | $20–$50 per year | Non-abrasive cleaning products for routine care. |
Regrouting | $200–$500 per shower | Performed every 5–7 years to prevent water seepage. |
Pros and Cons of Porcelain Slabs
Porcelain slabs are highly regarded in the construction industry, but like any material, they have advantages and limitations. Below is a detailed overview to guide decision-making.
Pros:
- Durability: Porcelain slabs are highly resistant to scratches, chips, and cracks, making them ideal for high-traffic bathrooms. Their non-porous nature prevents water absorption, reducing the risk of mold and mildew.
- Low Maintenance: Unlike natural stone, porcelain requires minimal upkeep. Routine cleaning with non-abrasive products keeps slabs looking pristine, and most don’t need regular sealing.
- Aesthetic Versatility: Available in a wide range of finishes (e.g., marble-look, wood-grain, matte) and large-format sizes, porcelain slabs can mimic luxury materials while offering a seamless, modern appearance with fewer grout lines.
- Water Resistance: The non-porous surface ensures excellent performance in wet environments, making porcelain ideal for shower walls and compliant with bathroom waterproofing standards.
- Eco-Friendly Options: Many porcelain slabs are made with recycled materials and sustainable manufacturing processes, appealing to environmentally conscious clients.
- Cost-Effective Compared to Natural Stone: Porcelain offers a high-end look at a lower cost than materials like marble or granite, with similar durability.
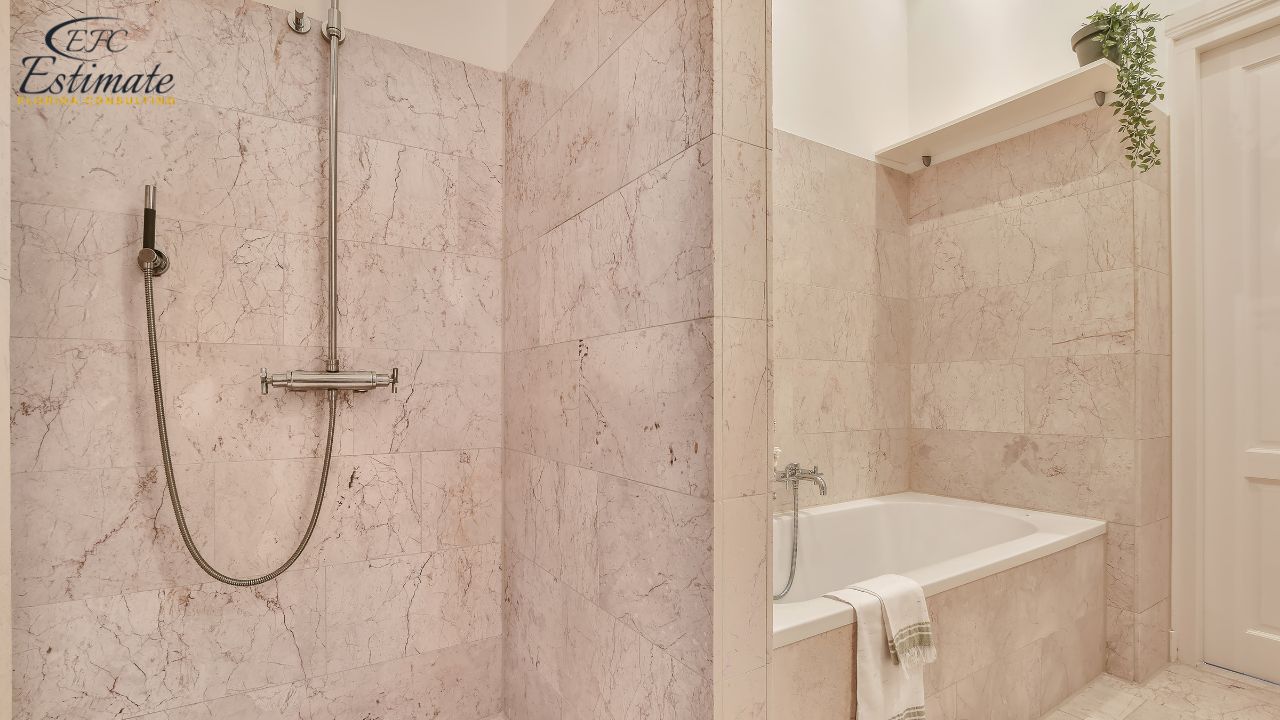
Cons:
- Higher Initial Cost: Porcelain slabs, especially high-end or ultra-thin varieties, can be more expensive than ceramic tiles or acrylic panels, with costs ranging from $8 to $40 per square foot.
- Installation Complexity: Large-format slabs require skilled labor for precise cutting and handling, increasing labor costs ($5–$15 per square foot) and potentially extending project timelines.
- Weight Considerations: Standard porcelain slabs are heavy, sometimes necessitating structural reinforcement, which adds $100–$200 per hour for engineering assessments.
- Limited Repair Options: While minor chips can be repaired ($100–$300), significant damage often requires replacing entire slabs ($500–$1,500), which can be costly.
- Cold Surface: Porcelain can feel cold underfoot or to the touch, which may be a drawback for clients seeking a warmer bathroom ambiance unless paired with underfloor heating.
- Slipperiness: Some polished porcelain finishes can become slippery when wet, requiring textured or matte finishes or anti-slip treatments, which may increase costs.
Labor Costs for Porcelain Slabs
Labor constitutes a significant portion of project costs, driven by Tampa’s competitive market.
Labor Type | Cost Range | Description |
Tile Installers | $5–$15 per sq. ft. | Varies by complexity; higher for intricate patterns. |
Plumbers | $45–$200 per hour | For plumbing reconfiguration, e.g., moving shower controls. |
Demolition Crews | $300–$500 per shower | Demolition and debris removal for existing showers. |
Structural Engineers | $100–$200 per hour | Assess wall reinforcement for heavy slabs. |
Get 5 New Projects in the Next 7 Days With Our System
Additional Costs
Ancillary costs can impact budgets, often arising from regulatory or unforeseen issues.
Additional Cost Type | Cost Range | Description |
Permits | $150–$600 | Required for shower remodels, varies by project scope. |
Water Damage Repairs | $1,000–$3,000 | Mold or rotted wood discovered during demolition. |
Ventilation Upgrades | $100–$500 | Bathroom fan installation to prevent moisture buildup. |
Disposal Fees | $100–$200 | Hauling away old materials; larger projects may require truck rentals. |
Other Costs
Additional expenses may include:
- Delivery Fees: $100–$300 for heavy porcelain slabs, especially from out-of-state suppliers.
- Interior Design Services: $50–$200 per hour or $600–$1,400 per project for layout and material selection.
- Custom Features: $200–$500 each for niches, benches, or thresholds.
- Luxury Fixtures: $200–$900 for rainfall showerheads or thermostatic mixers.
Customization Options
Porcelain slabs offer extensive customization to enhance functionality and aesthetics:
- Patterns and Finishes: Marble-look, wood-grain, or matte finishes; custom patterns increase costs by 10–20%.
- Slab Sizes: Large-format slabs (up to 60” x 120”) minimize grout lines, reducing installation time but increasing material costs.
- Integrated Features: Built-in niches, shelves, or benches cost $200–$500 each.
- Frameless Glass Doors: Pair with slabs for a modern look, costing $600–$1,900.
Cost-Saving Tips
To optimize budgets while maintaining quality, consider:
- Choose Standard Slabs: Save up to 50% by using standard porcelain over high-end or ultra-thin slabs.
- Minimize Demolition: Install over existing backer boards to avoid $300–$500 in demolition costs.
- Schedule Off-Season: Plan projects in winter for 10–15% labor discounts.
- Source Locally: Avoid $100–$300 in delivery fees by purchasing from local suppliers.
- DIY Minor Tasks: Handle demolition or debris removal to save $100–$500, leaving tiling and plumbing to professionals.
- Mix Materials: Combine porcelain with budget-friendly ceramic tiles for accents, reducing material costs by 20–30%.
Conclusion
Porcelain slab shower walls are a top choice for new construction in Tampa, offering durability, water resistance, and aesthetic appeal suited to the region’s humid climate and real estate demands. Costs range from $500 for small showers to $5,400 for large walk-ins, driven by material quality, labor, and unforeseen expenses. The pros—durability, low maintenance, and eco-friendliness—outweigh cons like higher costs and installation complexity when planned effectively. Critical considerations like code compliance and climate-adapted materials ensure performance. By leveraging cost tables, pros and cons, and cost-saving strategies, professionals can deliver quality projects within budget. Ensure compliance with local codes, secure permits, and engage qualified contractors for durable installations.
Frequently Asked Question
Porcelain slabs are denser and less porous than ceramic tiles, offering superior water resistance and durability in Tampa’s humid climate. Their large-format sizes reduce grout lines, minimizing maintenance and enhancing aesthetics, making them ideal for high-end shower installations.
Use waterproofing membranes and ensure proper ventilation (50 CFM minimum exhaust fans) as per FBC requirementsreshower installations. Engage certified contractors and secure permits ($150–$600) to avoid failed inspections and rework costs ($500–$2,000).
Maintenance is minimal, with annual cleaning supplies costing $20–$50. Regrouting every 5–7 years costs $200–$500, and sealing textured finishes every 2–3 years costs $100–$200. These low costs enhance porcelain’s value for clients.
Opt for standard porcelain slabs ($8–$15 per square foot), source materials locally to save $100–$300 on delivery, and schedule projects in winter for 10–15% labor discounts. DIY minor tasks like demolition can save $100–$500, but leave tiling to professionals.
Choose reputable local suppliers to ensure quality, availability, and compliance with standards like ANSI A137.1. Local sourcing reduces delivery fees ($100–$300) and ensures timely supply, critical for meeting project deadlines.
Many porcelain slabs are made with recycled materials and sustainable processes, appealing to eco-conscious clients. These options typically cost 5–10% more than standard slabs but may qualify for green building incentives ($200–$1,000), offsetting expenses.