- Homepage
- Blogs
Quantity Estimation for Warehouse Construction
Leading provider of warehouse estimating.
Planning a warehouse construction project requires accurate quantity estimation to ensure smooth execution and cost efficiency. Quantity estimation involves calculating the materials, labor, and resources needed to complete the project while avoiding wastage and cost overruns. With years of expertise in the field, Estimate Florida Consulting is here to provide a comprehensive guide on quantity estimation tailored specifically for warehouses.
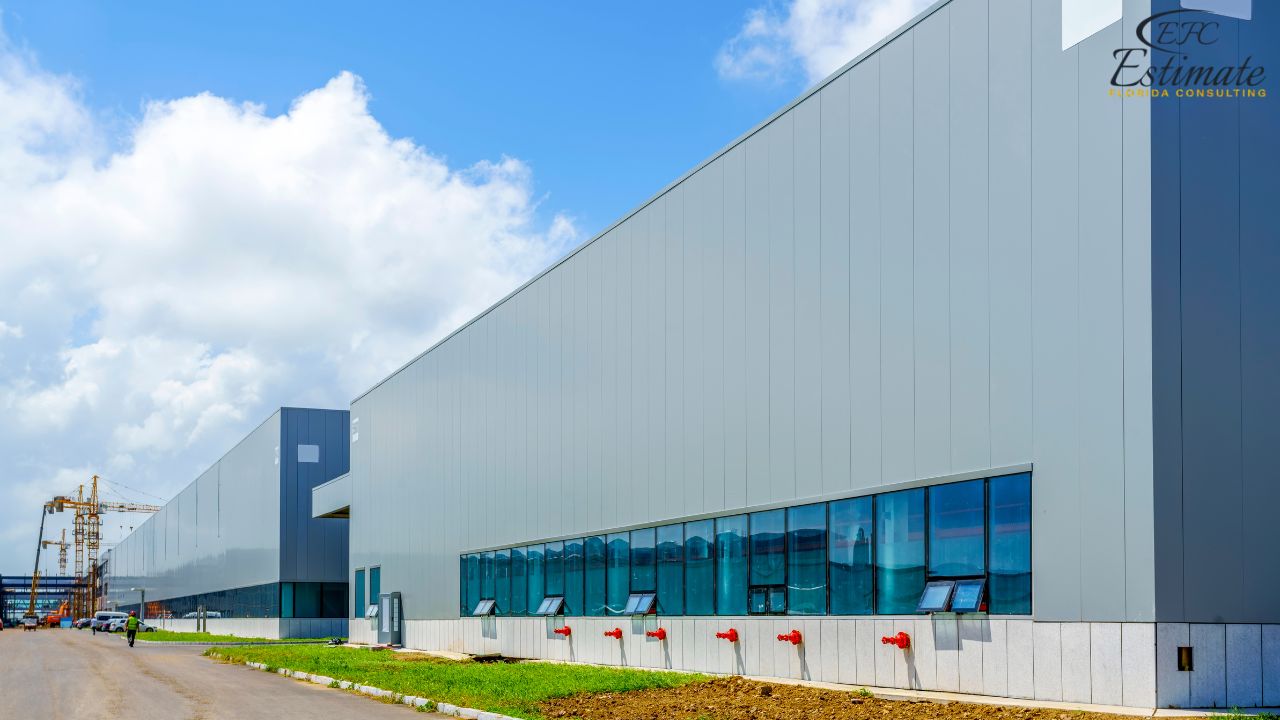
What is Quantity Estimation?
Quantity estimation is the process of calculating the amount of materials, labor, and equipment needed for a construction project. For warehouses, this includes:
- Materials like concrete, steel, and insulation.
- Labor for tasks such as foundation work, structural assembly, and roofing.
- Equipment like cranes, mixers, and forklifts.
By accurately estimating quantities, you can control costs, minimize delays, and ensure proper resource allocation throughout the project.
Why is Quantity Estimation Important for Warehouses?
Warehouses are large structures with unique requirements, and proper quantity estimation is essential for:
- Cost Management: Preventing budget overruns by accounting for all necessary materials and labor.
- Project Efficiency: Streamlining workflows by ensuring timely availability of resources.
- Waste Reduction: Avoiding excess material orders, which leads to savings and sustainability.
- Compliance: Meeting building codes and industry standards with precise calculations.
Key Components of Warehouse Quantity Estimation
1. Foundation Materials
The foundation is critical for supporting the heavy loads stored in a warehouse. Estimation should include:
- Concrete: Calculate based on the foundation’s depth, area, and type (e.g., slab-on-grade).
- Reinforcement Steel: Account for rebar quantities for added strength.
- Formwork: Include materials for temporary molds during concrete pouring.
2. Structural Steel
Structural steel forms the framework of the warehouse. Quantities are determined based on:
- Columns and Beams: Measure lengths and cross-sections.
- Trusses: Include calculations for roof support structures.
- Fasteners: Bolts, nuts, and welding materials.
Get Acquainted with Estimation
Top 5 Cost-Effective Tips to Manage Construction Budgets!!
Glass Building Construction Cost Estimator | Call: 561.530.2845
3. Roofing and Insulation
Warehouses require durable and weather-resistant roofing systems. Estimation involves:
- Roof Panels: Measure total roof area and account for overlaps.
- Insulation: Include materials like fiberglass or foam to regulate temperature.
- Gutters and Downspouts: For proper drainage.
4. Flooring Systems
Warehouse floors must withstand heavy loads and traffic. Consider:
- Concrete Flooring: Volume of concrete needed for slabs.
- Coatings and Finishes: Epoxy or other surface treatments for durability.
- Reinforcements: Include steel mesh or fibers for added strength.
5. Electrical and Mechanical Systems
Warehouses often require specialized systems for lighting, HVAC, and more. Estimate:
- Electrical Wiring: Lengths and types of cables.
- Lighting Fixtures: Quantity and type (e.g., LED or fluorescent).
- HVAC Systems: Size and components based on warehouse dimensions.
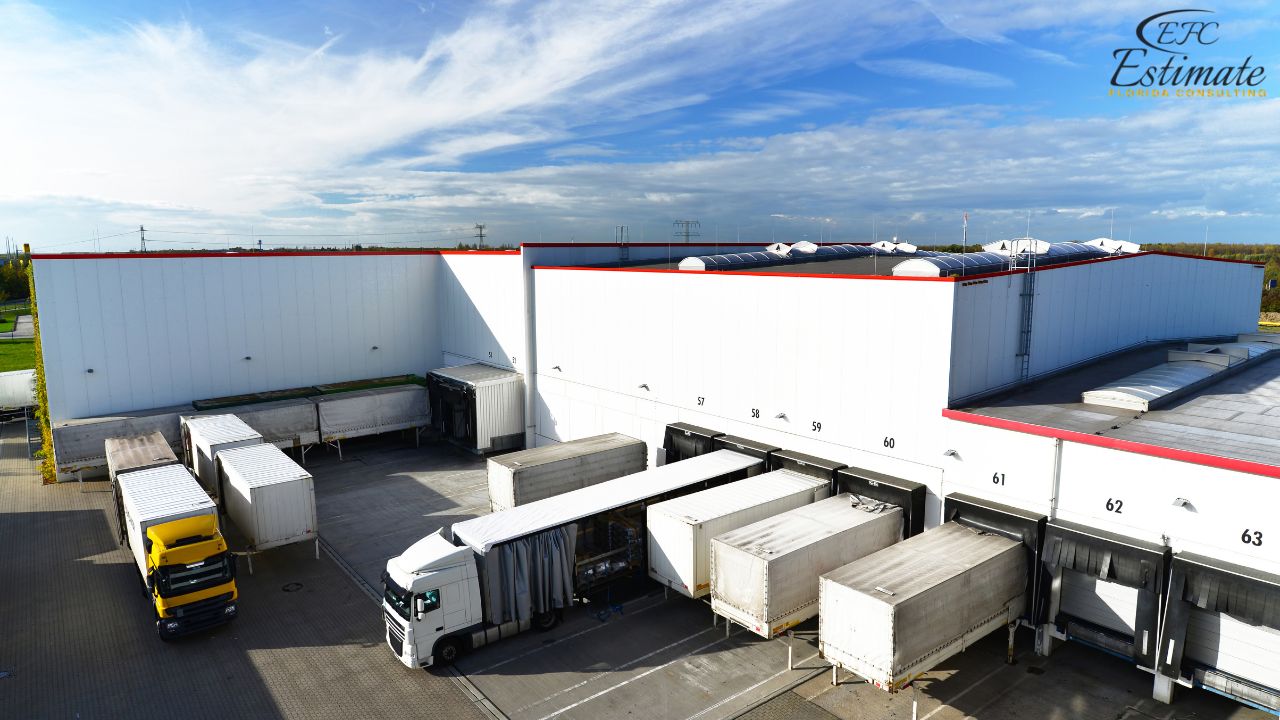
6. Storage Systems and Racking
A warehouse’s primary purpose is storage, so include:
- Shelving Units: Number and size based on storage needs.
- Pallet Racks: Calculate based on the type and weight of goods.
- Forklift Paths: Ensure space is allocated for efficient movement.
7. Fire Safety Systems
Fire safety is critical for warehouses. Estimate the quantity for:
- Sprinkler Systems: Number of heads and pipe lengths.
- Fire Extinguishers: Placement and total count.
- Fire Alarms and Sensors: Quantity based on building size and regulations.
Steps to Perform Quantity Estimation for a Warehouse
- Review the Project Plans: Study architectural and structural drawings to identify all components.
- List Materials and Resources: Create a detailed list of everything needed for the project.
- Measure Quantities: Use measurements from the drawings to calculate material volumes, lengths, and weights.
- Apply Unit Rates: Multiply quantities by current market rates to determine costs.
- Account for Wastage: Add 5-10% for material loss during construction.
- Summarize Totals: Include subtotals for each category (materials, labor, equipment) and calculate the overall budget.
Build your dream project with ease—contact Estimate Florida Consulting today!
Tools and Software for Warehouse Quantity Estimation
Several tools and software solutions can simplify the estimation process:
- Microsoft Excel: Ideal for creating custom spreadsheets with formulas and templates.
- AutoCAD: For accurate measurement extraction from digital drawings.
- Estimation Software: Specialized tools like PlanSwift and Bluebeam streamline calculations and provide professional reports.
Common Challenges in Warehouse Estimation
- Inaccurate Measurements: Errors in interpreting plans can lead to underestimation or overestimation.
- Price Fluctuations: Sudden changes in material costs can affect budgets.
- Complex Designs: Custom features or unconventional layouts complicate calculations.
- Coordination Issues: Miscommunication between teams can lead to errors in material orders.
How to Minimize Errors in Quantity Estimation?
- Double-Check Calculations: Always review your estimates for accuracy.
- Use Standardized Templates: Ensure consistency across projects by using templates.
- Stay Updated on Market Rates: Regularly update your cost database to reflect current prices.
- Involve Experts: Collaborate with experienced estimators for complex projects.
The Role of Technology in Modern Warehouse Estimation?
Technology has revolutionized quantity estimation with tools and software that provide:
- Real-Time Updates: Reflecting current market rates and material availability.
- Automated Calculations: Reducing human error and saving time.
- 3D Visualization: Helping identify potential issues early by visualizing designs.
- Integration: Linking with project management systems for seamless planning.
Benefits of Professional Estimation Services
Hiring a professional estimation service like Estimate Florida Consulting provides:
- Accurate Results: Ensuring reliable calculations based on years of experience.
- Time Savings: Freeing up your time to focus on other project aspects.
- Cost Optimization: Identifying areas to reduce expenses without compromising quality.
- Expert Guidance: Offering insights and recommendations tailored to your specific project needs.
Why Choose Estimate Florida Consulting?
At Estimate Florida Consulting, we specialize in precise and efficient quantity estimation for warehouses. Our services include:
- Comprehensive material take-offs.
- Detailed cost breakdowns for labor and equipment.
- Customized Excel templates for your specific requirements.
- Support throughout the planning and construction phases.
With our expertise, you can ensure that your warehouse project stays on track and within budget.
Download Template For Construction Project Breakdown
- Materials list updated to the zip code
- Fast delivery
- Data base of general contractors and sub-contractors
- Local estimators
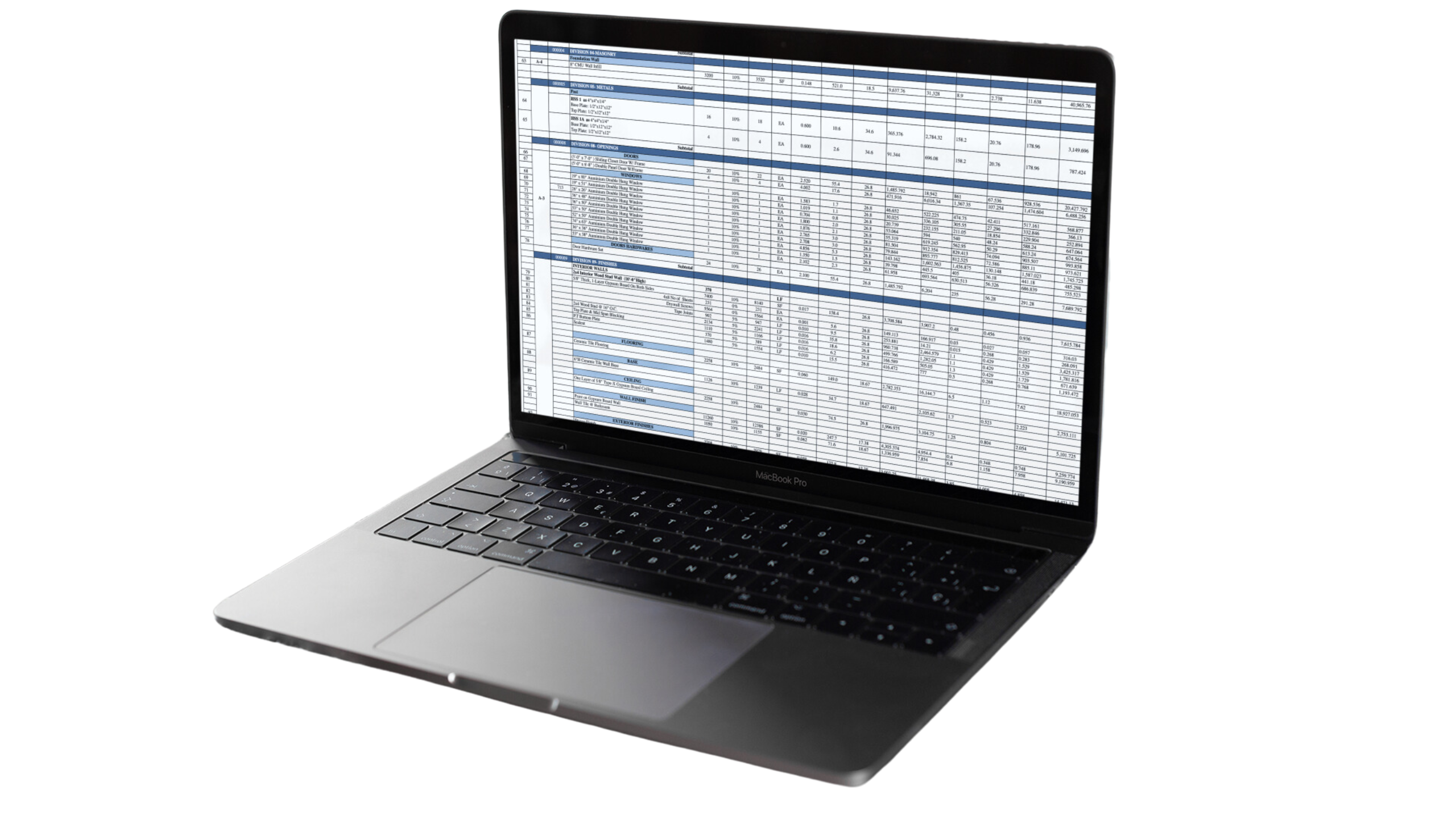
Final Thoughts
Accurate quantity estimation is essential for the successful construction of a warehouse. By following a structured approach and leveraging the right tools, you can streamline your estimation process and avoid costly mistakes. For professional support and guidance, contact Estimate Florida Consulting today and let us help you bring your warehouse project to life with confidence!
Frequently Asked Question
Materials are estimated based on the warehouse’s dimensions and the types of materials specified for the project. For example, calculate concrete based on the slab size, walls, and foundation. Steel is estimated based on the structural framework requirements.
Factors such as the complexity of the design, the choice of materials, local labor rates, weather conditions, and the warehouse’s location can all impact the quantity estimate. External factors like regulatory requirements and unforeseen site conditions can also influence costs.
Labor costs are estimated by determining the number of workers required for each phase of the construction, such as site preparation, foundation laying, steel framework erection, and interior work. You can multiply the estimated hours by the hourly wage rate for each type of labor required. Additionally, factors like local labor rates in Florida should be factored in.
A warehouse quantity estimation includes materials (concrete, steel, insulation, etc.), labor costs, equipment rentals, external factors such as land preparation, and a contingency fund. It also takes into account the specific warehouse design and size, the local market conditions, and regulatory compliance costs.
You can reduce material costs by:
- Sourcing materials locally to reduce transportation fees.
- Using alternative or more affordable materials (e.g., opting for standard steel vs. premium finishes).
- Planning ahead to avoid last-minute purchases, which can be more expensive.
A contingency fund is a percentage of the total estimated cost (typically 5-10%) set aside to cover unforeseen expenses during the construction process, such as delays, material price fluctuations, or unanticipated changes in the scope of the project.
Some common mistakes include:
- Underestimating material quantities: Failing to account for all necessary materials can lead to shortages or unexpected purchases.
- Not including a contingency fund: Without a contingency, the project is more vulnerable to cost overruns due to unforeseen issues.
- Ignoring local conditions: Overlooking factors like local labor rates or weather conditions can lead to inaccurate estimates.
- Relying solely on outdated data: Using outdated cost data for materials or labor can result in an inaccurate estimate.
Equipment rental costs are estimated by identifying the machinery needed for the construction phases (e.g., cranes, excavators, forklifts) and obtaining rental rates from local suppliers. The number of days or weeks each piece of equipment will be needed must also be factored into the total cost.
Comprehensive Trade-Specific Estimates
At Estimate Florida Consulting, we offer detailed cost estimates across all major trades, ensuring no part of your project is overlooked. From the foundation to the finishing touches, our trade-specific estimates provide you with a complete and accurate breakdown of costs for any type of construction project.
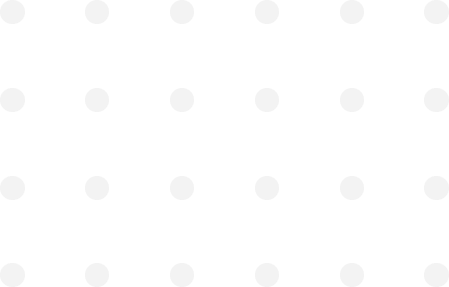
Testimonials
What Our Clients Say
We take pride in delivering accurate, timely, and reliable estimates that help contractors and builders win more projects. Our clients consistently praise our attention to detail, fast turnaround times, and the positive impact our estimates have on their businesses.
Estimate Florida Consulting has helped us win more bids with their fast and accurate estimates. We trust them for every project!
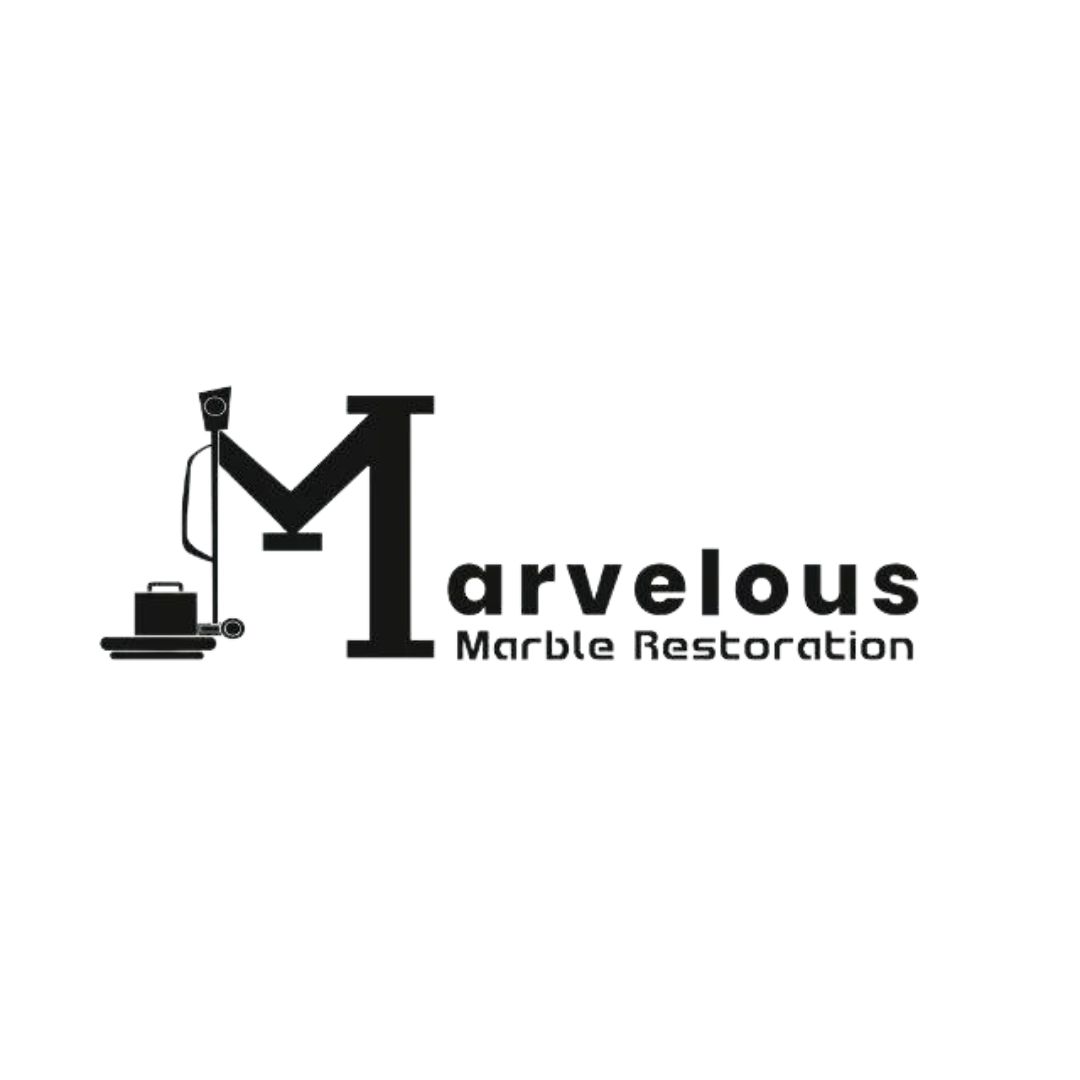
Steps to Follow
Our Simple Process to Get Your Estimate
01
Upload Plans
Submit your project plans, blueprints, or relevant documents through our online form or via email.
02
Receive Quotation
We’ll review your project details and send you a quote based on your scope and requirements.
03
Confirmation
Confirm the details and finalize any adjustments to ensure the estimate meets your project needs.
04
Get Estimate
Receive your detailed, trade-specific estimate within 1-2 business days, ready for your project execution.
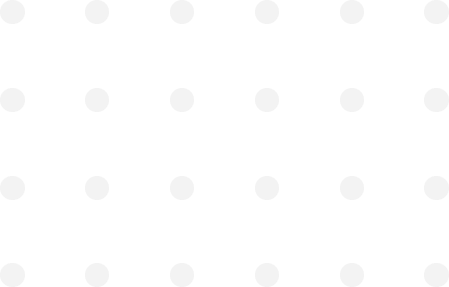