Cost per square foot is a common metric for gauging construction expenses. In Florida, the cost per square foot for hangars typically ranges from $90 to $220, depending on design complexity, materials, and added features like advanced HVAC systems or custom doors.
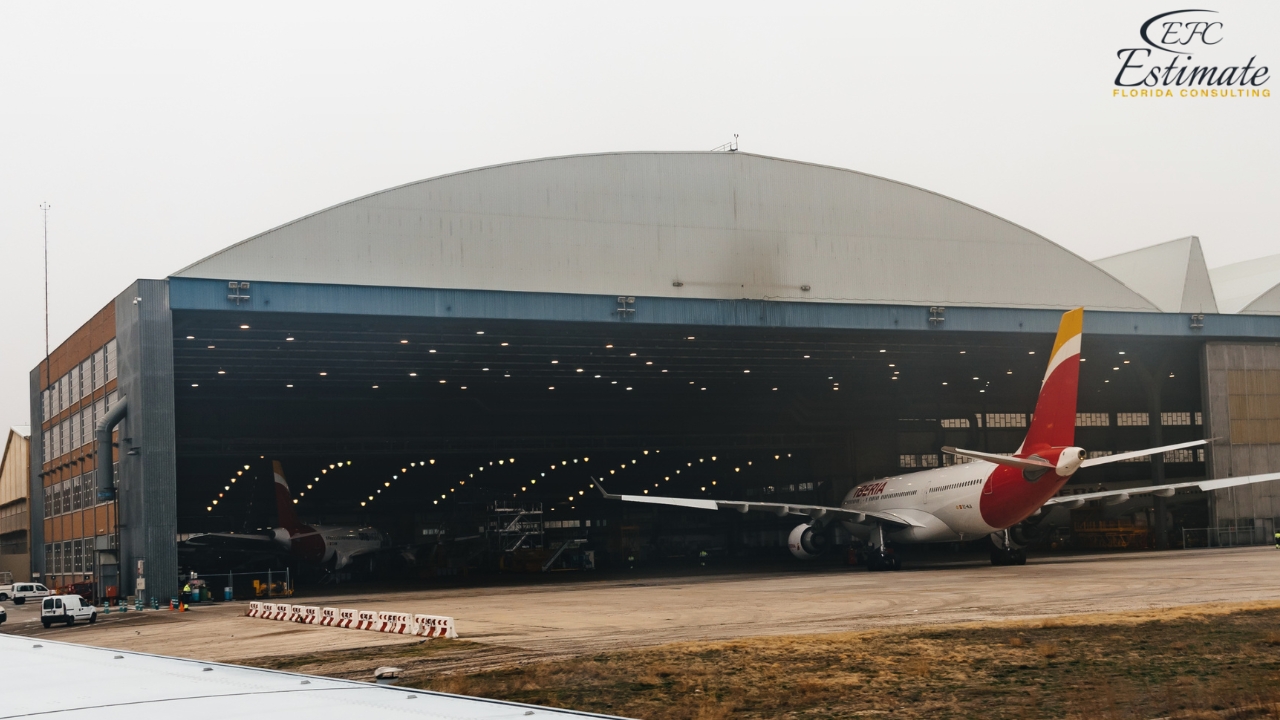
For example:
- Basic Metal Hangar (Minimal Finishes): $90 – $120 per sq. ft.
- Mid-Range Hangar (Insulation, Standard Doors): $120 – $160 per sq. ft.
- High-End Hangar (Climate Control, Premium Doors, Office Space): $160 – $220 per sq. ft.
Below are sample cost tables to help visualize hangar construction expenses:
Hangar Construction Cost by Size (Basic Finish)
Hangar Size (sq. ft.) | Estimated Cost Range |
2,000 – 3,000 | $180,000 – $660,000 |
5,000 – 10,000 | $450,000 – $2,200,000 |
20,000+ | $1,800,000+ |
Major Component Costs
Component | Cost Range |
Roofing (per sq. ft.) | $10 – $20 |
Foundation (per sq. ft.) | $6 – $12 |
Doors (total) | $20,000 – $150,000+ |
Types of Hangars and Their Costs
Private Aircraft Hangars
Private aircraft hangars are designed for individual aircraft owners who prioritize functionality and affordability. These hangars often feature simple layouts focused on protecting planes from weather and external damage. The cost of a private hangar typically ranges from $120,000 to $350,000, depending on factors such as the size of the hangar, the type of door system (sliding or hydraulic), and the quality of the foundation. Additional amenities, like heating, cooling, or storage spaces for tools and spare parts, can further impact the cost. Private hangars are ideal for small-scale owners seeking a secure and customized storage solution.
Commercial Aviation Hangars
Commercial aviation hangars are built to accommodate the needs of larger operators, including airlines, charter services, and flight schools. These hangars are significantly more complex and expansive, often including space for maintenance activities, offices, and customer lounges. Costs can range from $500,000 to several million dollars, depending on the size and the level of customization required. For instance, a hangar with specialized maintenance equipment, high-tech fire suppression systems, or energy-efficient lighting will cost more. Compliance with commercial aviation regulations, which often dictate stringent safety and operational standards, also adds to the cost. These hangars are designed for high durability and functionality to support busy aviation operations.
T-Hangars and Nested T-Hangars
T-hangars are designed to store multiple small aircraft in a compact, staggered layout, making them a cost-effective option for small-scale operations. They are particularly popular among small aviation businesses or private pilots who need efficient storage. The costs for T-hangars generally fall between $80,000 and $250,000 per unit, depending on factors like the size of the hangar, the level of interior finishing, and whether utilities like shared electricity or plumbing systems are included. Nested T-hangars, a variation of the standard T-hangar, maximize space utilization by interlocking units, further optimizing storage in limited areas.
Multi-Aircraft Storage Hangars
Multi-aircraft storage hangars are designed for larger operations that require space to house several aircraft under one roof. These hangars are ideal for flight schools, charter services, or aviation companies that manage a fleet. Construction costs can range from $300,000 to over $1 million, heavily influenced by the hangar’s size, structural requirements, and the complexity of features like automated door systems or reinforced flooring to support heavier aircraft. Interior finishes such as office spaces, climate control, and advanced lighting systems can also add to the cost. These hangars are built to accommodate high traffic and provide efficient, centralized storage for multiple aircraft.
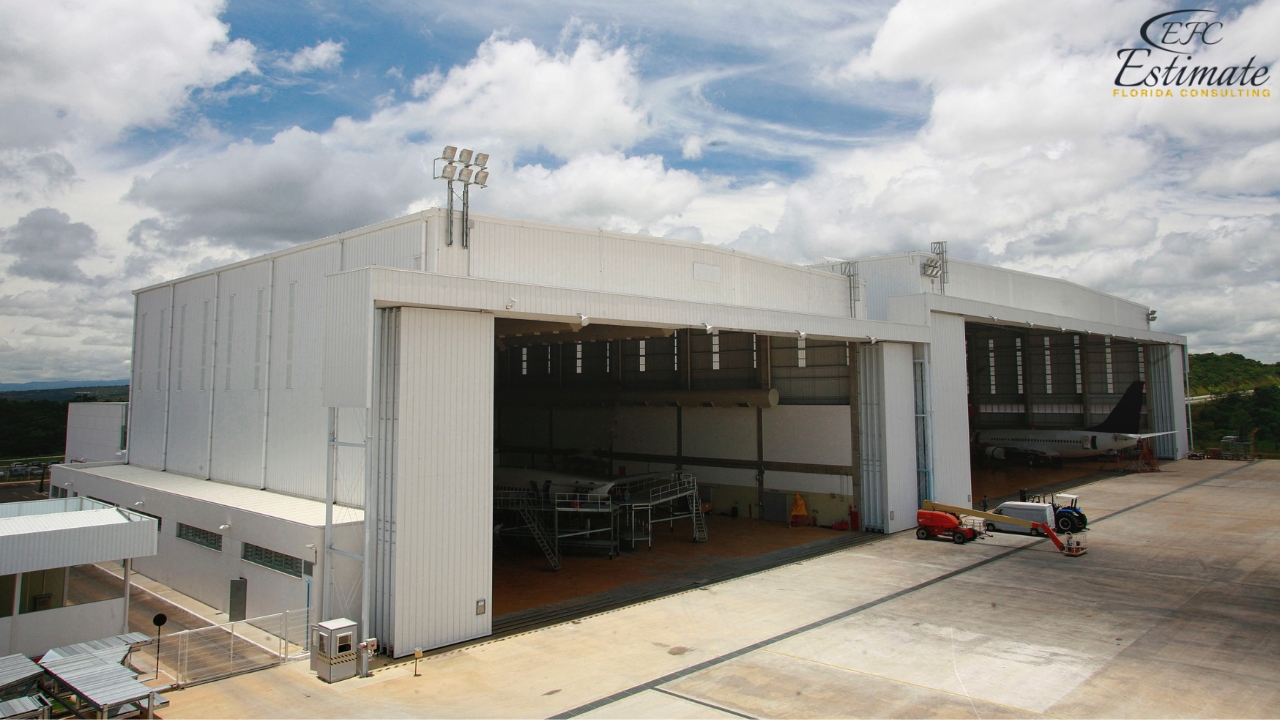
Hangar Construction Costs by Size and Complexity
Small Single-Aircraft Hangars
Small single-aircraft hangars are designed to provide shelter for one or two smaller planes, such as private jets or single-engine aircraft. These hangars typically range in size from 1,500 to 3,000 square feet, making them an excellent option for individual aircraft owners or small businesses. Construction costs for these hangars usually range from $150,000 to $400,000, depending on factors like the choice of materials, location, and additional features. Basic hangars include simple metal structures with sliding doors, while higher-end options may feature insulation, lighting, and even small office spaces. The cost can also vary based on the local climate and building regulations, as areas with harsher weather conditions may require reinforced structures or climate control systems.
Mid-Size Hangars (2-4 Aircraft)
Mid-size hangars are commonly used to house multiple general aviation aircraft, such as small corporate fleets or regional service planes. These hangars range in size from 3,000 to 10,000 square feet, providing enough room for two to four planes along with additional space for storage or minor maintenance. The cost of constructing a mid-size hangar typically falls between $300,000 and $1 million, influenced by factors like structural complexity, door systems, and interior finishes. Features such as automatic door openers, fire suppression systems, and basic climate control may be included, driving up the cost. These hangars often serve flight schools, charter companies, or small aviation businesses that need functional yet affordable facilities.
Large Hangars (5+ Aircraft, Commercial Uses)
Large hangars cater to the needs of corporate fleets, charter operations, or even small-scale commercial aviation services. With sizes ranging from 10,000 to 50,000 square feet or more, these hangars are designed to accommodate multiple aircraft, including larger jets or helicopters. Construction costs for large hangars often exceed $1 million, depending on the level of customization and operational requirements. Advanced features such as heavy-duty motorized doors, robust climate control systems, and integrated office or maintenance areas significantly impact the budget. These hangars may also include reinforced flooring to support the weight of larger aircraft and systems for fuel storage or delivery. Their scale and functionality make them ideal for high-traffic aviation hubs or corporate headquarters.
Specialized Hangars (Maintenance, FBO Facilities)
Specialized hangars are tailored to meet specific operational needs, such as those of Fixed Base Operators (FBOs) or aircraft maintenance facilities. These structures are more than just shelters for planes—they often include integrated workshops, parts storage areas, administrative offices, and even customer-facing spaces like lounges or retail sections. Construction costs for specialized hangars can exceed $2 million, largely due to the complexity of the design and the need for specialized equipment. For example, a maintenance hangar might require reinforced cranes, hydraulic lifts, and advanced lighting systems, while an FBO facility may include high-end finishes to appeal to luxury travelers. Regulatory compliance, such as meeting strict safety and environmental standards, also contributes to the higher cost. These hangars are critical for supporting large-scale aviation operations and enhancing the overall customer experience.
Win More Projects With Us
Hangar Construction Costs by Structural Components
Hangar Roofing Cost
The roofing system is a critical part of any hangar, providing protection against the elements while ensuring durability and efficiency. Hangar roofs can be constructed using materials like standard metal panels for basic coverage or insulated composite systems for enhanced energy efficiency. Costs typically range between $10 and $20 per square foot, depending on the material chosen, the level of insulation required, and additional features such as reflective coatings or corrosion resistance. In Florida, hurricane-resistant roofing systems are often necessary, which can drive costs higher due to reinforced designs and specialized fasteners that withstand strong winds.
Hangar Foundations and Concrete Slabs
The foundation is the backbone of any hangar, ensuring stability and safety. Concrete slabs are commonly used and cost around $6 to $12 per square foot, with variations based on thickness, the type of reinforcement (such as rebar or post-tensioning), and the level of soil preparation needed. In areas with poor soil conditions, additional measures such as pilings or ground stabilization might be required, significantly increasing costs. In Florida, where the water table is high in many regions, foundation work may involve extra drainage solutions or waterproofing measures, adding to the complexity and expense.
Hangar Framing and Structural Steel
The steel frame is the core structural element of a hangar, supporting the roof and walls while ensuring the building can handle heavy loads and environmental pressures. Costs for framing range from $25 to $60 per square foot, influenced by the quality of the steel, the complexity of truss designs, and the size of the hangar. Florida’s stringent wind-load requirements often necessitate heavier steel sections and additional bracing, increasing both material and labor costs. The framing process also involves precise engineering and installation to meet safety and building code standards, making it one of the more expensive aspects of hangar construction.
Hangar Doors and Entry Systems
Hangar doors are a significant expense and vary widely based on design, size, and features. Basic sliding doors provide a cost-effective option, while automated hydraulic or bifold doors offer superior convenience and durability. The cost of door systems can range from $20,000 to over $150,000, with larger doors and those featuring advanced automation or hurricane-rated designs at the higher end of the spectrum. In Florida, where wind ratings are a priority, custom-built doors with reinforced frames and weather seals are often required, adding to the overall expense. Additionally, integrating door systems with modern control technologies can further increase costs.
Hangar Insulation and Interior Finishes
Insulation plays a crucial role in improving the energy efficiency and comfort of a hangar. Basic insulation materials, such as spray foam or fiberglass, typically cost between $2 and $6 per square foot, depending on thickness and thermal resistance. Beyond insulation, interior finishes can greatly enhance the functionality and aesthetics of a hangar. These may include drywall partitions for office or storage areas, epoxy floor coatings for durability, and custom cabinetry or storage systems. Interior finishes can add anywhere from $10,000 to $100,000 or more to the total project cost, depending on the complexity and materials chosen. For Florida hangars, climate control solutions like HVAC systems may also be necessary, further increasing the budget.
Hangar Utilities and Systems Costs
Electrical and Lighting Systems
A well-designed electrical and lighting system is critical for a functional and efficient hangar. Basic electrical installation costs can range from $5 to $10 per square foot, covering wiring, outlets, and standard lighting. However, the type of lighting and power systems significantly impacts overall expenses. Basic fluorescent or halogen lighting may be more cost-effective, but many modern hangars opt for energy-efficient LED systems that offer better illumination and long-term savings on energy bills. For larger hangars or those requiring uninterrupted operations, backup generators, redundant power supplies, and intricate electrical setups may be necessary, further increasing costs. These systems not only enhance safety but also improve operational efficiency, making them a worthwhile investment.
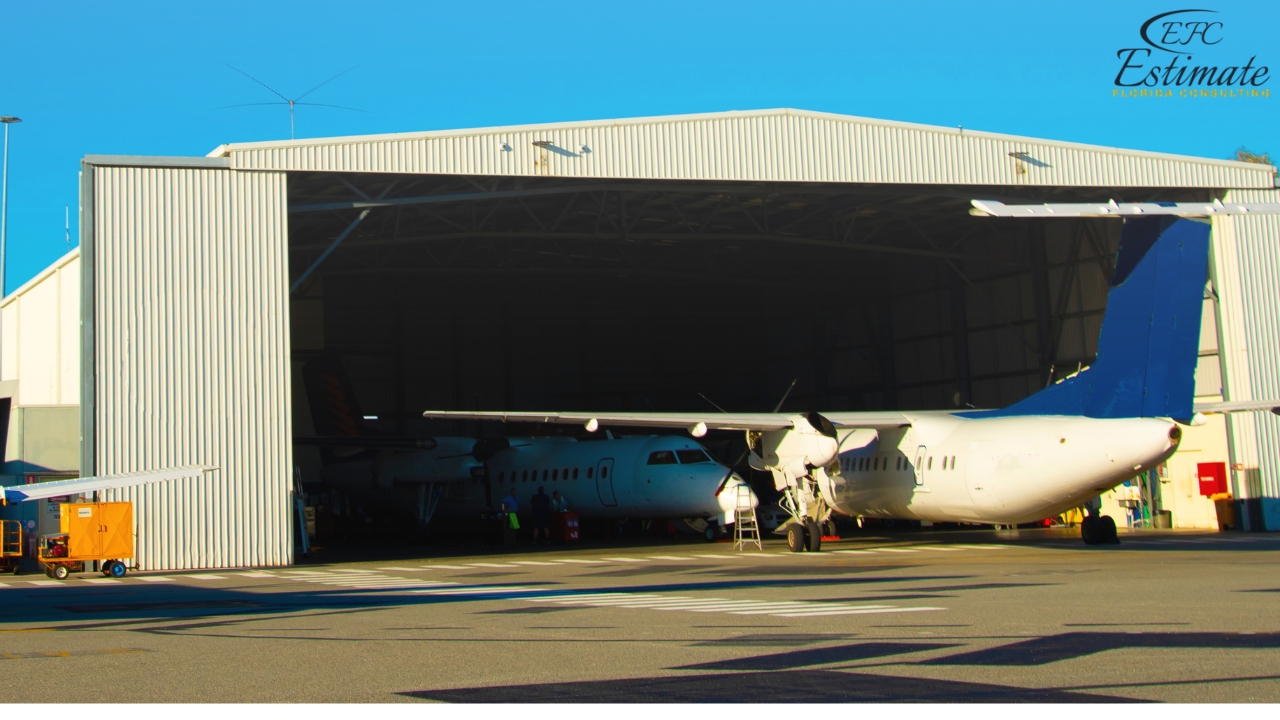
HVAC and Ventilation Systems
Maintaining a stable and controlled environment inside a hangar is essential, particularly for preserving high-value aircraft and equipment. HVAC and ventilation system costs can vary significantly, ranging from $10,000 to over $100,000, depending on the size of the hangar and the level of climate control needed. Smaller hangars might only require basic ventilation to circulate air, while larger or specialized hangars often need complex HVAC systems with precise temperature and humidity controls. For example, hangars storing aircraft with sensitive electronics or delicate materials may need advanced dehumidifiers and air filtration systems. Energy-efficient designs, including smart thermostats and zoning systems, can help lower operational costs in the long run.
Plumbing and Drainage Systems
Plumbing is another crucial utility, especially in hangars that include restrooms, kitchenettes, or aircraft maintenance facilities. The cost of installing plumbing systems typically ranges from $5,000 to $25,000, depending on the complexity and scope of the project. Hangars dedicated to maintenance or cleaning operations may also require specialized drainage systems, such as oil/water separators and wash bays, to manage wastewater effectively. These additions ensure compliance with environmental regulations and help prevent contamination of local water sources. Proper planning and installation of drainage systems are particularly important in Florida, where heavy rainfall and runoff are common concerns.
Fire Suppression and Safety Systems
Safety systems are an integral part of any hangar, with fire suppression being one of the most critical features. The cost of these systems can range from $15,000 to $100,000, influenced by the size of the hangar and specific regulatory requirements. Standard fire safety measures include smoke detectors, alarms, and sprinklers, but many hangars require more advanced systems such as foam-based fire suppression to combat fuel or chemical fires effectively. Compliance with FAA regulations, NFPA codes, and local fire safety standards is essential, and meeting these requirements may necessitate specialized designs and materials. While these systems add to the upfront costs, they ensure the safety of personnel, aircraft, and other assets.
Get Acquainted with Estimation
Maximize Profits: Budgeting Hacks for Big Construction Projects
Estimating Construction Costs in Bad Weather: What You Need to Know?
Cost Factors Influencing Hangar Construction in Florida
Location and Zoning Requirements
Florida’s diverse geography and local regulations significantly affect hangar construction costs. Coastal areas may involve higher land acquisition costs and more stringent zoning regulations due to environmental sensitivities and hurricane risks. Conversely, inland regions might have more affordable land but could require additional permit fees and site preparation to meet local standards. Airport authority guidelines also vary, with some requiring additional approvals or fees for construction projects. Understanding the nuances of location-specific requirements is critical to budgeting accurately and avoiding unforeseen expenses.
Labor and Material Availability
The availability of skilled labor and construction materials plays a significant role in determining overall costs. In Florida, labor rates can fluctuate based on local market conditions, with specialized subcontractors—such as those skilled in electrical, HVAC, or fire safety installations—often commanding higher wages. Additionally, Florida’s exposure to hurricanes has led to stricter building codes, which may require upgraded materials like impact-resistant glass, reinforced steel, or durable roofing systems. Material shortages or price surges, common during peak construction seasons or after hurricanes, can further increase costs and extend timelines.
Local Building Codes and Regulations
Compliance with the Florida Building Code (FBC) is a non-negotiable aspect of hangar construction. These codes are designed to ensure buildings can withstand high winds, storms, and other environmental challenges common in Florida. Meeting these requirements often involves using reinforced concrete, hurricane straps, and high-strength steel, all of which add to construction expenses. Additionally, inspections and certifications required by local authorities may introduce additional costs and project delays. Investing in quality materials and experienced contractors helps ensure compliance and reduces the risk of costly post-construction modifications.
Weather and Environmental Considerations
Florida’s climate, with its intense heat, humidity, and frequent hurricanes, poses unique challenges for construction projects. These conditions can impact both the materials used and the scheduling of construction activities. For instance, weather-resistant materials, such as corrosion-resistant steel and moisture-resistant finishes, are often required to withstand Florida’s harsh climate. Construction schedules must also account for hurricane seasons, which can delay progress and increase costs due to protective measures. Proper planning, including choosing weather-appropriate materials and scheduling activities strategically, helps mitigate these challenges and ensures a smoother construction process.
Download Template For Hangar Project Breakdown
- Materials list updated to the zip code
- Fast delivery
- Data base of general contractors and sub-contractors
- Local estimators
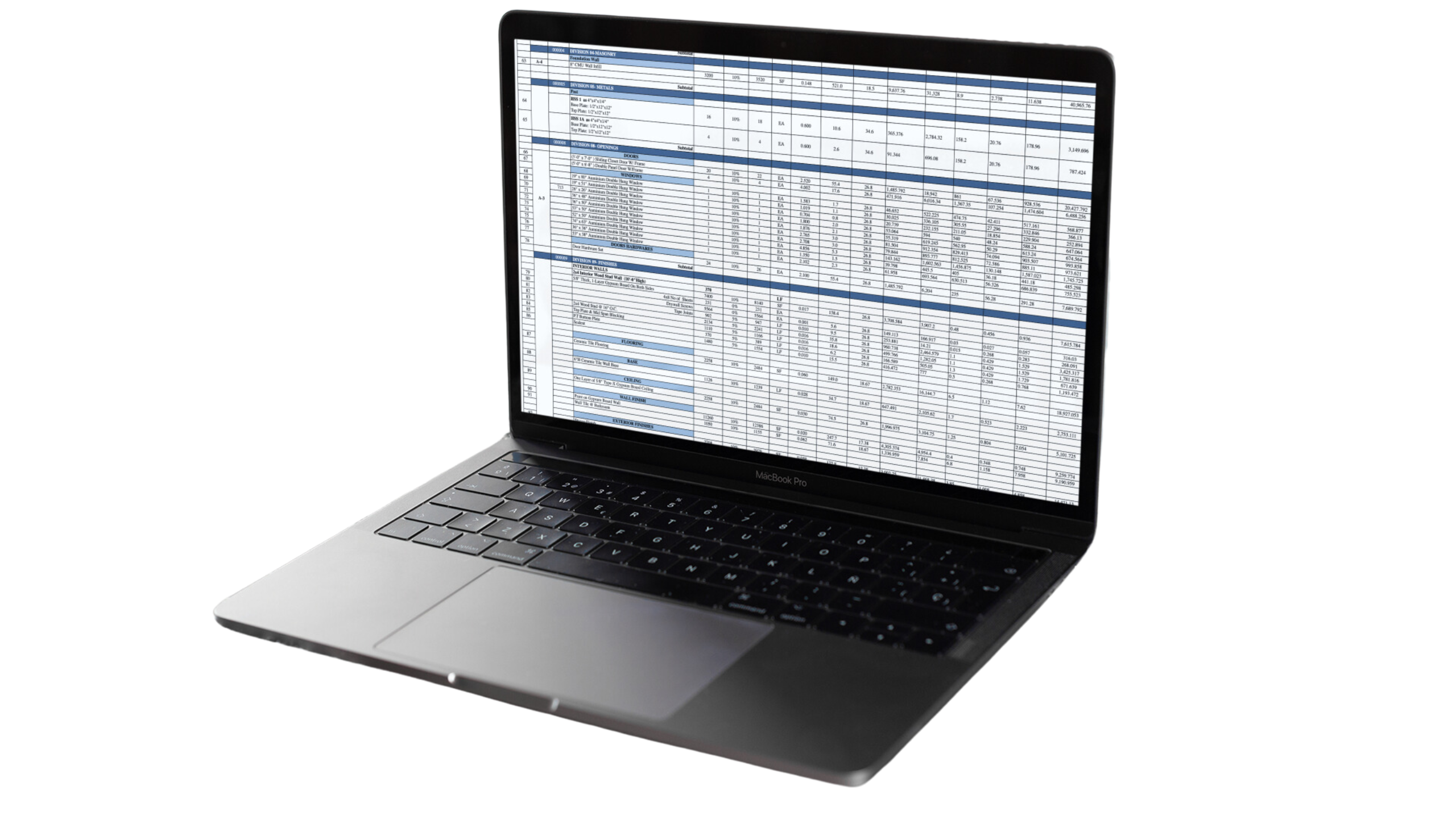
Conclusion
The cost of building a hangar varies significantly based on its size, intended use, and the level of customization required. In Florida, expenses range from $90 to $220 per square foot, reflecting the impact of local regulations, weather considerations, and material choices. Private hangars offer affordable options for individual aircraft owners, while commercial and specialized hangars demand higher investments due to added features like climate control, advanced safety systems, and compliance with stringent building codes. By understanding these factors and planning effectively, clients can balance functionality, durability, and cost to achieve their ideal aviation storage solution.
Question Answer
Frequently Asked Question
The cost to build a hangar in Florida typically ranges from $90 to $220 per square foot, depending on factors like design complexity, materials, and added features. Basic metal hangars cost around $90-$120 per square foot, while mid-range hangars with insulation and standard doors cost $120-$160 per square foot. High-end hangars with climate control, premium doors, and office spaces can range between $160 and $220 per square foot.
Here are some examples of estimated costs based on hangar size and finish:
Hangar Size (sq. ft.) | Estimated Cost Range |
2,000 - 3,000 | $180,000 - $660,000 |
5,000 - 10,000 | $450,000 - $2,200,000 |
20,000+ | $1,800,000+ |
The following are typical cost ranges for key components of hangar construction:
Component | Cost Range |
Roofing (per sq. ft.) | $10 - $20 |
Foundation (per sq. ft.) | $6 - $12 |
Doors (total) | $20,000 - $150,000+ |
Private aircraft hangars typically cost between $120,000 and $350,000, depending on size and features. Basic hangars include sliding doors and standard finishes, while more advanced options may include climate control, storage areas, and hydraulic door systems, which add to the overall cost.
Commercial aviation hangars are larger and more complex, costing $500,000 to several million dollars. These hangars often include maintenance areas, offices, and customer lounges. Specialized systems like advanced fire suppression or energy-efficient lighting can increase costs.
T-hangars, designed to store multiple small aircraft efficiently, cost between $80,000 and $250,000 per unit. Nested T-hangars, which maximize storage space, are slightly more expensive due to their optimized layouts and shared utilities.
Multi-aircraft storage hangars range from $300,000 to over $1 million, depending on size, structural complexity, and additional features like automated doors and reinforced flooring. These hangars are ideal for operations managing multiple aircraft.
Specialized hangars, such as maintenance facilities or Fixed Base Operator (FBO) hangars, can cost $2 million or more. These structures often include workshops, parts storage, customer lounges, and regulatory-compliant systems, making them more expensive.
Comprehensive Trade-Specific Estimates
At Estimate Florida Consulting, we offer detailed cost estimates across all major trades, ensuring no part of your project is overlooked. From the foundation to the finishing touches, our trade-specific estimates provide you with a complete and accurate breakdown of costs for any type of construction project.
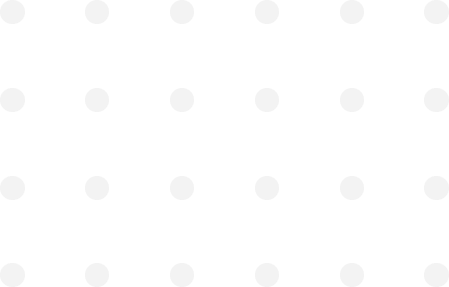
Testimonials
What Our Clients Say
We take pride in delivering accurate, timely, and reliable estimates that help contractors and builders win more projects. Our clients consistently praise our attention to detail, fast turnaround times, and the positive impact our estimates have on their businesses.
Estimate Florida Consulting has helped us win more bids with their fast and accurate estimates. We trust them for every project!
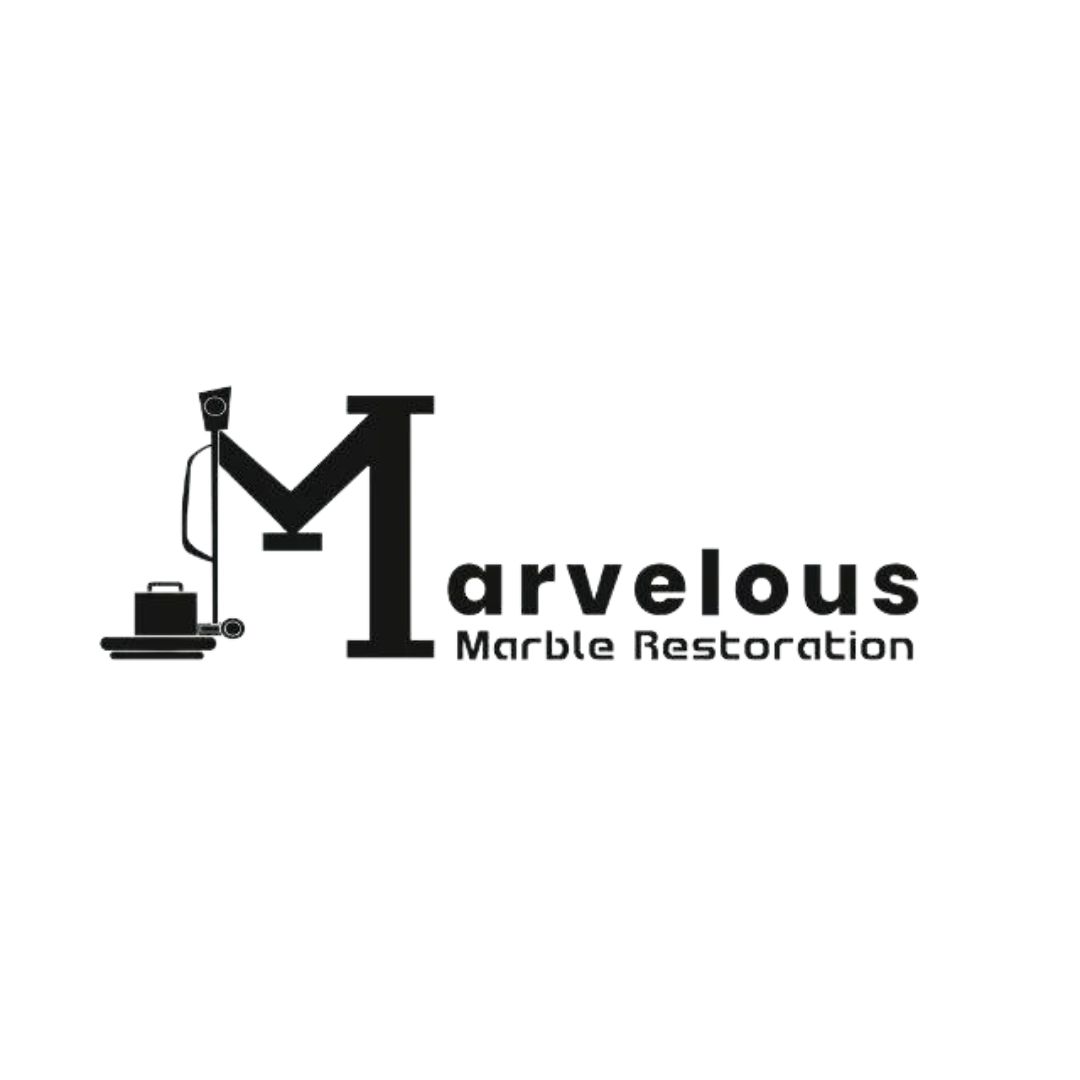
Steps to Follow
Our Simple Process to Get Your Estimate
01
Upload Plans
Submit your project plans, blueprints, or relevant documents through our online form or via email.
02
Receive Quotation
We’ll review your project details and send you a quote based on your scope and requirements.
03
Confirmation
Confirm the details and finalize any adjustments to ensure the estimate meets your project needs.
04
Get Estimate
Receive your detailed, trade-specific estimate within 1-2 business days, ready for your project execution.
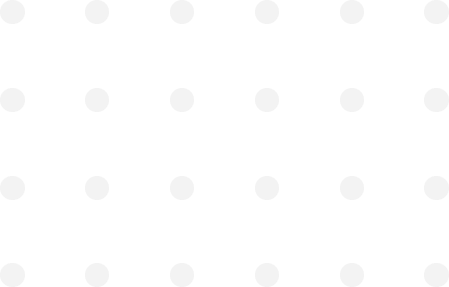