Construction professionals rely heavily on accurate takeoffs to estimate costs, order materials, and plan projects efficiently. Understanding how to perform takeoffs from blueprints is a crucial skill for general contractors, subcontractors, developers, and material suppliers. This article provides a comprehensive guide to mastering blueprint takeoffs with practical tips, tools, and techniques.
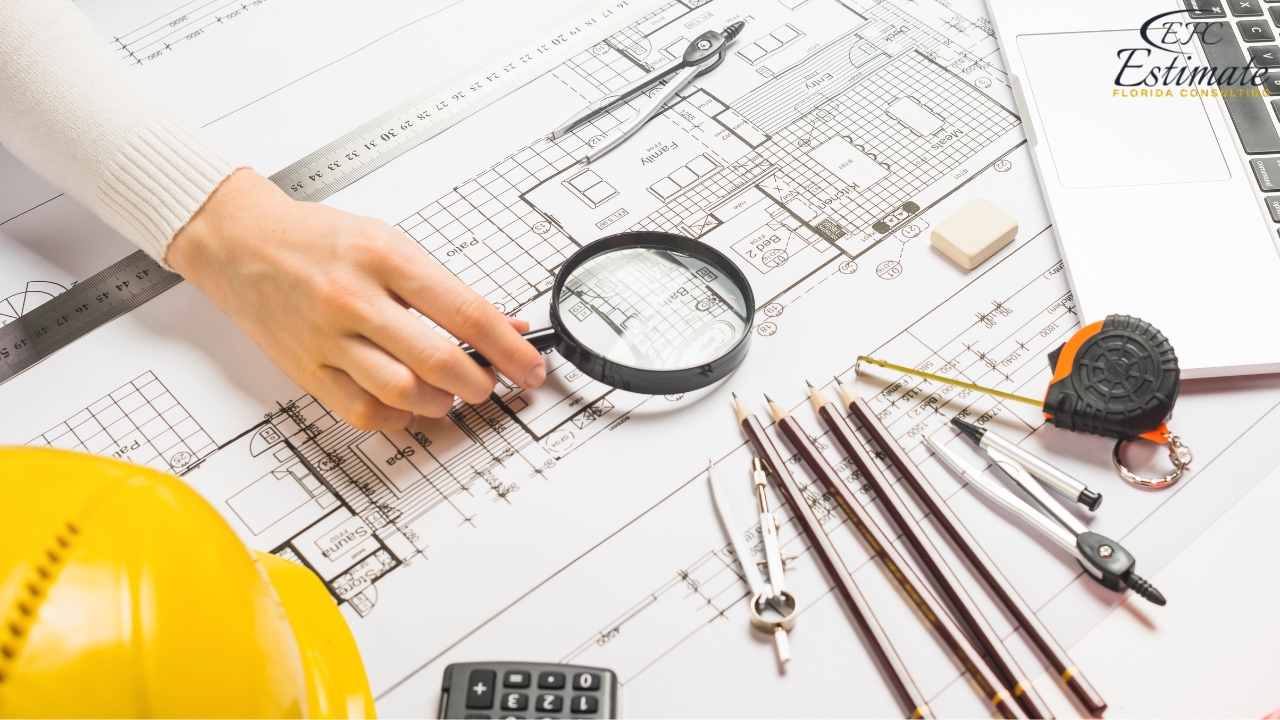
Takeoffs and Their Importance
A takeoff, also known as a quantity takeoff or material takeoff, is the process of quantifying the components of a construction project. It involves analyzing blueprints or construction drawings to determine the amount of materials, labor, and equipment required. Accurate takeoffs are essential for:
- Cost Estimation: Providing an accurate budget for the project.
- Procurement Planning: Ensuring the right materials and quantities are ordered.
- Project Scheduling: Identifying the resources needed at each stage of construction.
- Bid Preparation: Helping contractors develop competitive bids based on precise data.
Types of Construction Takeoffs
Construction takeoffs are essential for accurate project planning and resource allocation. They involve quantifying various project components to ensure efficient execution. Here’s an in-depth look at the main types of construction takeoffs:
Material Takeoffs
Material takeoffs focus on identifying and quantifying all physical materials required for a project. This includes items like concrete, lumber, drywall, steel, roofing materials, and finishes. The process ensures that the correct amounts of materials are ordered, avoiding shortages that could delay the project or excesses that lead to waste and increased costs. For example, in a residential project, the material takeoff might calculate the number of drywall sheets for interior walls or the volume of concrete needed for foundations. Advanced tools and software are often used to improve accuracy, especially in large or complex projects.
Get Acquainted with Estimation
Mastering Bids: 12 Pro-Level Bidding Tips for Construction Managers
Maximize Profits: Budgeting Hacks for Big Construction Projects
Labor Takeoffs
Labor takeoffs estimate the workforce requirements to complete the project, including the number of hours, skill levels, and types of trades involved. This might encompass electricians, plumbers, carpenters, masons, and other specialists. Labor takeoffs are critical for scheduling, ensuring that the right workers are available at each project phase. For example, a commercial project requiring extensive electrical work will include detailed estimates of the hours needed for skilled electricians, as well as general labor for support tasks. Accurate labor takeoffs prevent understaffing, which can cause delays, or overstaffing, which increases costs unnecessarily.
Equipment Takeoffs
Equipment takeoffs identify the machinery, tools, and equipment necessary for completing the project. This ranges from heavy machinery like excavators, cranes, and bulldozers to specialized tools such as concrete mixers, scaffolding, and welding machines. Equipment takeoffs also account for the duration and frequency of equipment use, as well as associated costs like rental fees, transportation, and maintenance. For instance, a road construction project might require graders and pavers, while a multi-story building may involve cranes and scaffolding for structural assembly. Proper equipment planning ensures smooth operations and prevents delays due to equipment shortages.
How to Read Blueprints for Takeoffs?
Reading blueprints is a fundamental skill for accurate takeoffs, enabling contractors and estimators to extract vital information about materials, labor, and equipment. Here’s a step-by-step guide to approaching blueprints effectively:
Understand Symbols and Legends
Blueprints rely on standardized symbols to represent various construction components, such as walls, doors, windows, and fixtures. Familiarizing yourself with the legend—usually located on the blueprint—helps decode these symbols accurately. For example, electrical plans may use specific symbols for outlets, switches, and lighting fixtures, while structural drawings include symbols for beams and columns. Misinterpreting these symbols can lead to inaccurate takeoffs, so taking time to understand them is crucial.
Review the Scale
Blueprints are scaled-down representations of the actual project dimensions. Common scales include 1/4″ = 1′-0″ for floor plans or 1″ = 10′-0″ for site plans. Understanding the scale is essential for calculating precise measurements for materials and quantities. Use a scale ruler or digital tools to translate blueprint dimensions into real-world values. For example, accurately interpreting wall lengths or room sizes from the blueprint ensures correct material estimates, such as drywall or flooring.
Identify Key Sections
Focus on critical blueprint sections that directly relate to the takeoff. These include:
- Floor Plans: Provide an overhead view of the layout, showing room dimensions, wall placements, and fixture locations.
- Elevations: Depict vertical views of the structure, showing heights, window placements, and exterior finishes.
- Details: Include close-up views of specific components, such as staircases, joinery, or structural reinforcements.
Identifying and analyzing these sections ensures all relevant data is captured for the takeoff.
Note Specifications
Blueprints often include written specifications that provide detailed instructions about materials, construction methods, and finishes. These notes complement the visual elements of the drawings and are critical for accurate takeoffs. For instance, specifications might indicate the type of concrete mix required for foundations or the grade of lumber for framing. Ignoring these details can lead to inaccurate estimates or the use of inappropriate materials.
Check for Revisions and Updates
Construction projects often undergo design changes, resulting in revised blueprints. Ensure you’re working with the latest version of the plans to avoid discrepancies in the takeoff process. Cross-check revision notes and updates for any modifications that could affect material quantities or labor estimates.
Step-by-Step Process for Performing Takeoffs
An accurate takeoff is essential for precise estimation and efficient construction planning. Below is a detailed step-by-step guide for performing takeoffs effectively:
Reviewing the Blueprint
The first step is to thoroughly review the blueprint to understand the project’s scope and requirements. Study all architectural and engineering drawings to identify the materials, structural elements, and utilities specified. This includes layouts for foundations, walls, plumbing, and electrical systems. Pay close attention to details like dimensions, specifications, and notes to ensure nothing is overlooked. A clear understanding of the design ensures the accuracy of subsequent calculations.
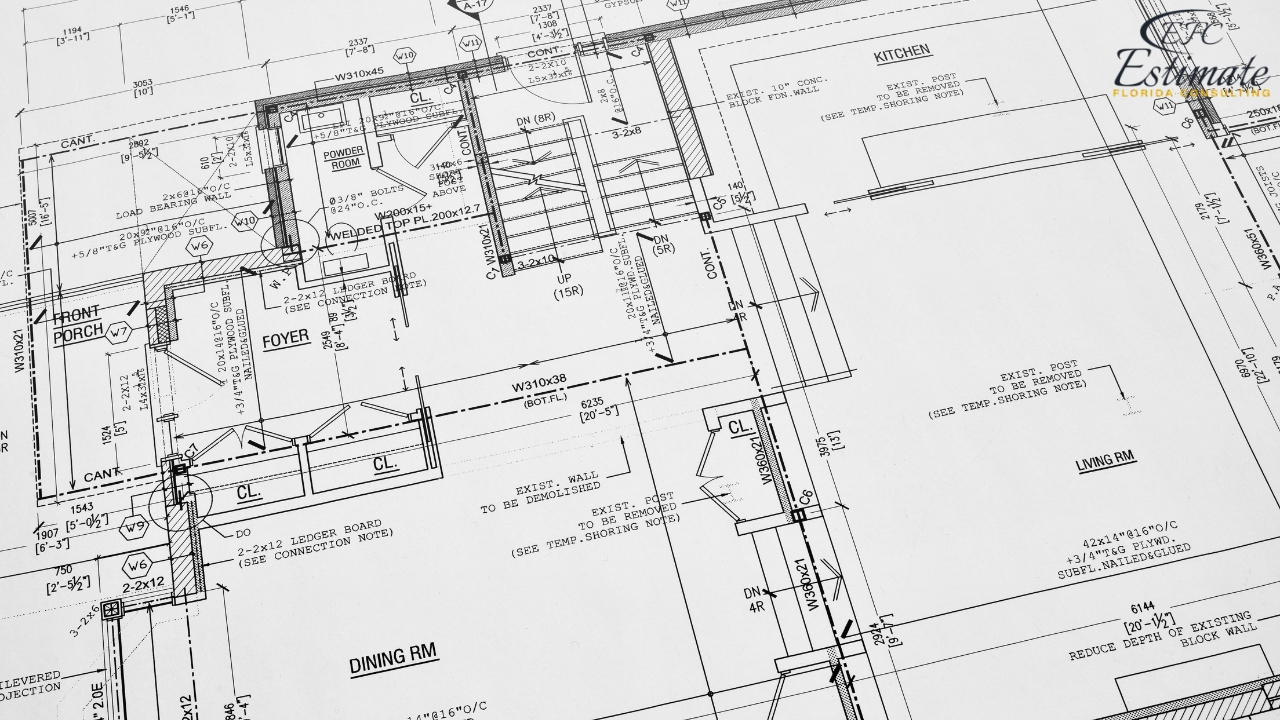
Identifying Key Components
Next, break down the blueprint into manageable sections, such as foundation, framing, roofing, and interiors. Identify each component that requires quantification. For example:
- Foundations: Concrete, rebar, and formwork.
- Framing: Lumber, steel beams, or prefabricated panels.
- Roofing: Shingles, underlayment, flashing.
- Interiors: Drywall, flooring, paint.
By isolating key components, you can ensure every aspect of the project is accounted for in your takeoff.
Measuring Quantities
Accurate measurements are the core of any takeoff process. Use digital takeoff tools or a traditional scale ruler to measure the quantities of materials required. Common measurements include:
- Square Footage: Measure total area for items like flooring, drywall, and roofing.
- Cubic Yards: Calculate concrete volumes for foundations, footings, and slabs.
- Linear Footage: Determine the length of materials such as pipes, wiring, or framing lumber.
For example:
- Measure the floor area in square feet for tile or carpet installation.
- Calculate the volume of concrete by multiplying the length, width, and depth of a foundation slab.
- Use the perimeter of walls to estimate the linear footage of baseboards or crown molding.
Win More Projects With Us
Documenting Data
After taking measurements, organize all data into a structured format. Use spreadsheets or takeoff software to categorize information by material type, quantity, and cost. Ensure all measurements are clear, precise, and easily accessible for reference. Proper documentation should include:
- Material Quantities: Categorized by type (e.g., drywall, concrete, lumber).
- Costs: Estimated price per unit and total cost for each material.
- Annotations: Notes or assumptions, such as waste factors or special requirements.
For example, a foundation takeoff might document:
- 100 cubic yards of concrete @ $150 per cubic yard = $15,000
- 500 linear feet of rebar @ $2.50 per linear foot = $1,250
Common Challenges in Blueprint Takeoffs
Performing accurate blueprint takeoffs is a critical part of construction planning but can be fraught with challenges. These difficulties, if not addressed, can lead to costly errors and inefficiencies. Below are some of the most common obstacles faced during blueprint takeoffs:
Complex Blueprints
Modern construction projects often involve intricate blueprints with multiple layers, dimensions, and technical details. These designs can be difficult to interpret, especially for projects with advanced features like irregular shapes, complex HVAC systems, or custom architectural elements. Misinterpreting even a small detail can result in inaccurate takeoffs, leading to issues like material shortages or overspending. Advanced software tools and experienced professionals are often required to navigate the complexity of such blueprints.
Human Error
Manual calculations in blueprint takeoffs are prone to errors, such as misreading dimensions, omitting critical components, or inputting incorrect data. Even a small mistake can snowball into significant problems during procurement or construction. For example, underestimating the quantity of concrete needed for a foundation can cause delays and increase costs. Verifying takeoffs through peer reviews or automated software can help mitigate this challenge.
Inaccurate Data
Outdated, incomplete, or poorly prepared blueprints can lead to incorrect takeoffs. Changes to project designs or missing details such as elevations, material specifications, or structural requirements can result in miscalculations. Using the most current and comprehensive set of blueprints is essential, and any ambiguities should be clarified with architects or engineers before proceeding with the takeoff process.
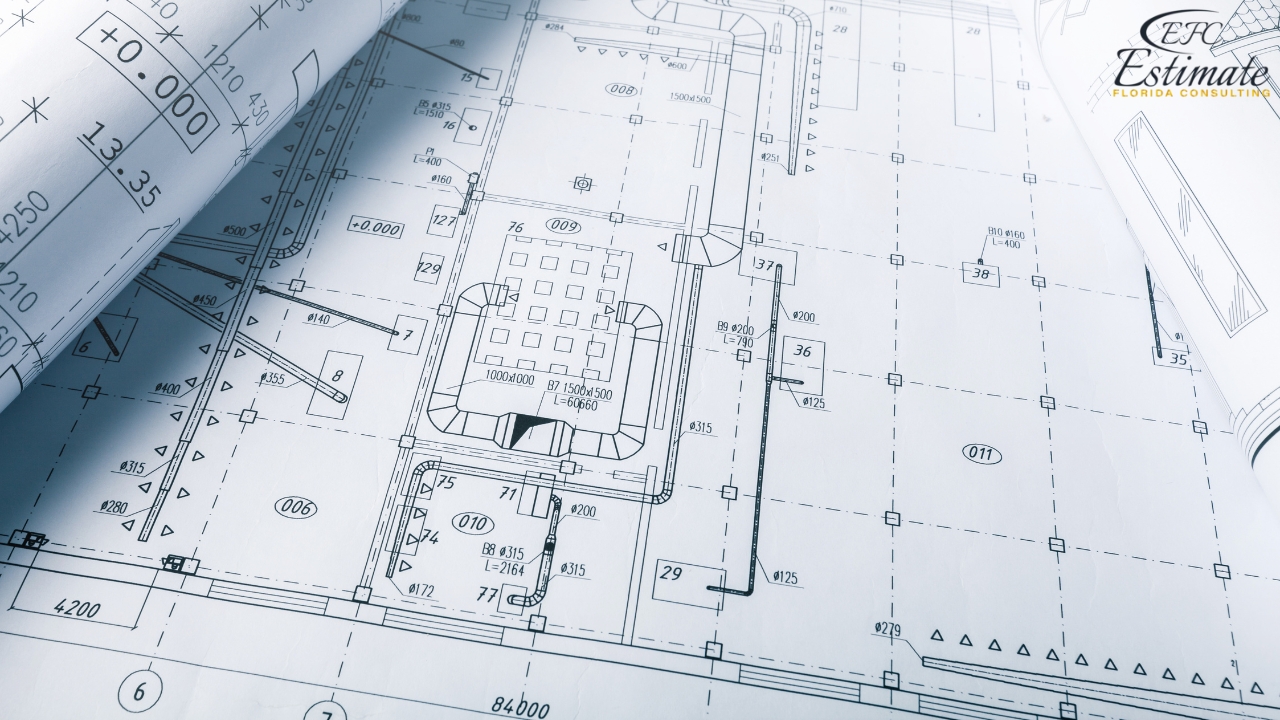
Time Constraints
Large or complex projects often require significant time to perform takeoffs accurately. Tight deadlines can pressure estimators to rush the process, increasing the likelihood of errors. For instance, a high-rise building may have hundreds of pages of blueprints, making it challenging to complete detailed takeoffs within a limited timeframe. Leveraging technology, such as digital takeoff software, can speed up the process without compromising accuracy.
Tips for Accurate Takeoffs
- Double-Check Measurements: Verify all measurements to ensure accuracy.
- Use Digital Tools: Leverage software to streamline the process and minimize errors.
- Stay Organized: Keep your data well-structured for easy reference.
- Collaborate with Experts: Work with architects or engineers to clarify any uncertainties.
- Update Regularly: Revisit takeoffs if project specifications change.
Download Template For Construction Project Breakdown
- Materials list updated to the zip code
- Fast delivery
- Data base of general contractors and sub-contractors
- Local estimators
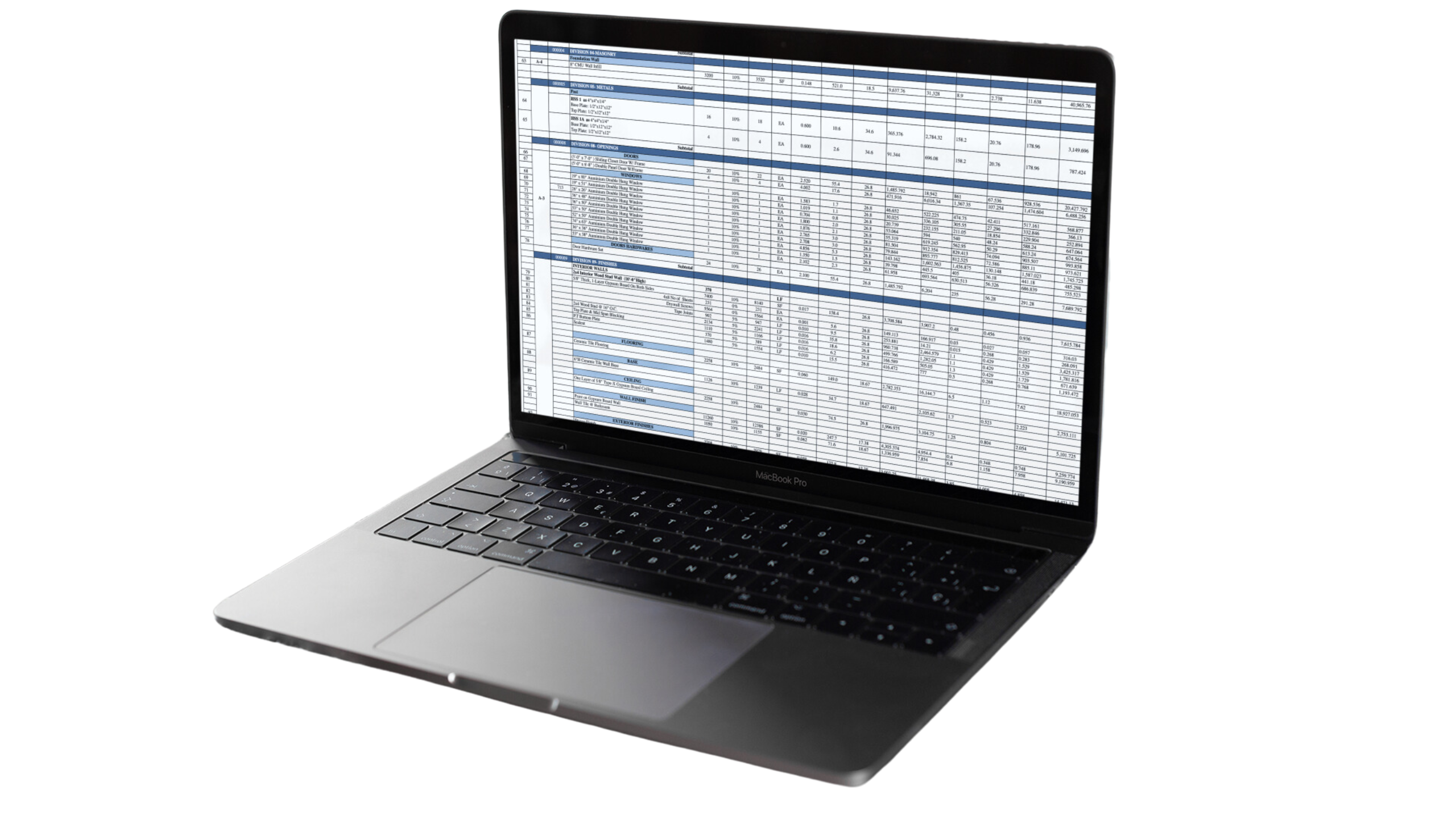
Conclusion
Mastering the art of performing takeoffs from blueprints is essential for successful project management in the construction industry. By leveraging modern tools, adhering to systematic processes, and paying attention to detail, contractors and estimators can achieve greater accuracy and efficiency in their projects. At Estimate Florida Consulting, we specialize in helping our clients navigate the complexities of blueprint takeoffs, ensuring that every project starts on a solid foundation.
Question Answer
Frequently Asked Question
A blueprint takeoff involves quantifying the materials, labor, and equipment needed for a construction project based on the information provided in blueprints.
Takeoffs provide the detailed data needed for cost estimation, procurement planning, and project scheduling, ensuring that resources are allocated efficiently.
The time required for a takeoff depends on the project's complexity and size. Small projects may take a few hours, while larger projects can take several days.
Yes, takeoffs can be done manually using tools like a scale ruler and spreadsheets, but using digital software is recommended for improved accuracy and speed.
Comprehensive Trade-Specific Estimates
At Estimate Florida Consulting, we offer detailed cost estimates across all major trades, ensuring no part of your project is overlooked. From the foundation to the finishing touches, our trade-specific estimates provide you with a complete and accurate breakdown of costs for any type of construction project.
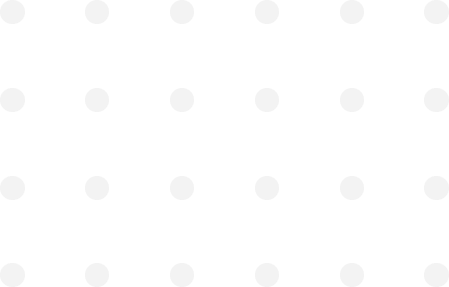
Testimonials
What Our Clients Say
We take pride in delivering accurate, timely, and reliable estimates that help contractors and builders win more projects. Our clients consistently praise our attention to detail, fast turnaround times, and the positive impact our estimates have on their businesses.
Estimate Florida Consulting has helped us win more bids with their fast and accurate estimates. We trust them for every project!
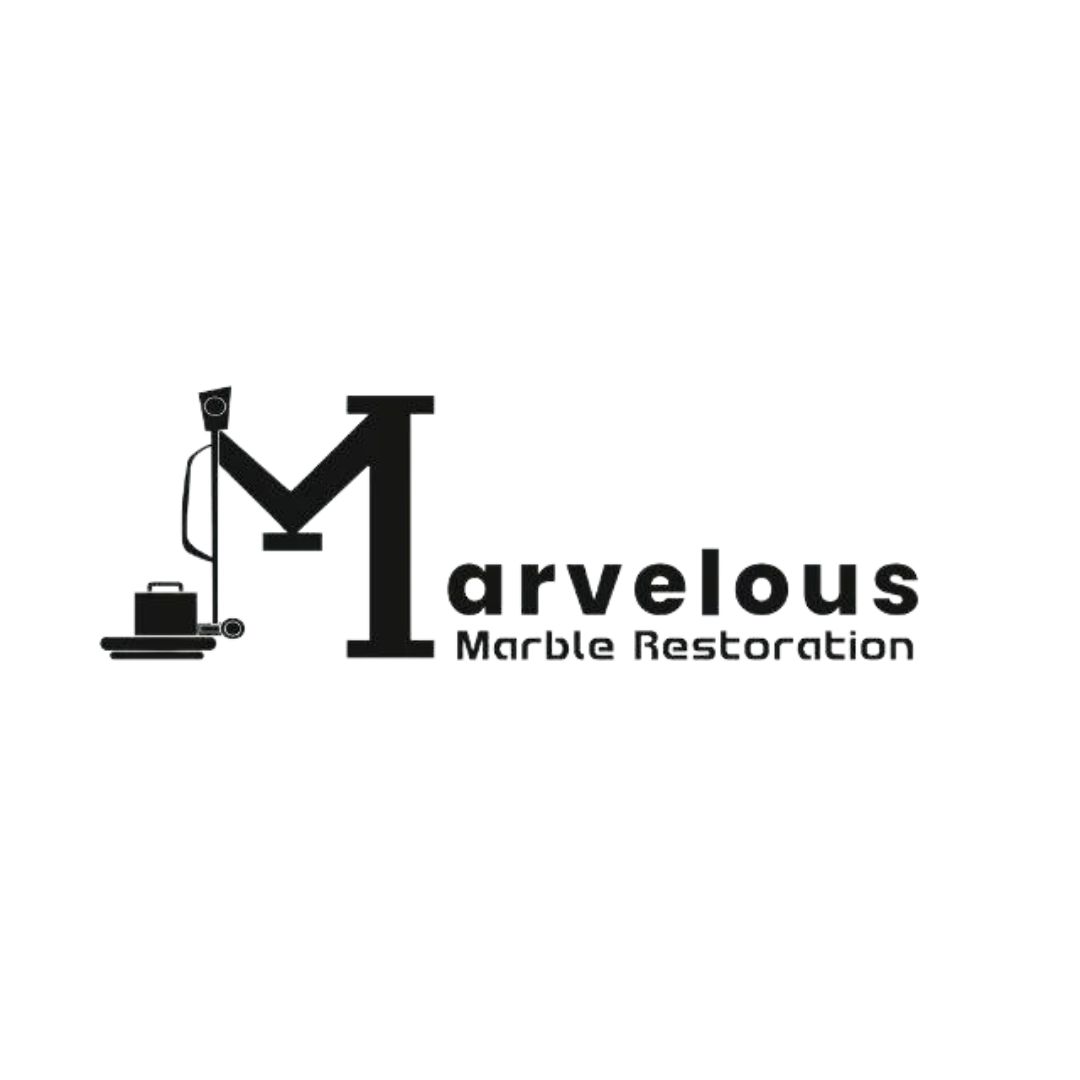
Steps to Follow
Our Simple Process to Get Your Estimate
01
Upload Plans
Submit your project plans, blueprints, or relevant documents through our online form or via email.
02
Receive Quotation
We’ll review your project details and send you a quote based on your scope and requirements.
03
Confirmation
Confirm the details and finalize any adjustments to ensure the estimate meets your project needs.
04
Get Estimate
Receive your detailed, trade-specific estimate within 1-2 business days, ready for your project execution.
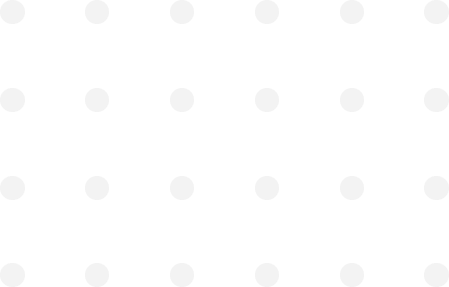