- Homepage
- Blogs
What Is Quantity Takeoff in Construction?
Leading provider of construction estimating.
Quantity takeoffs play a crucial role in the decision-making process for construction projects. They are essential for understanding the full scope and requirements of any project, regardless of its size. A well-executed quantity takeoff ensures accurate data collection and analysis, which directly impacts the success of a project. On the other hand, poor estimations can lead to costly mistakes that disrupt the entire construction process. This task demands expertise in data management, as even small errors in cost estimation can have significant consequences throughout the project lifecycle.
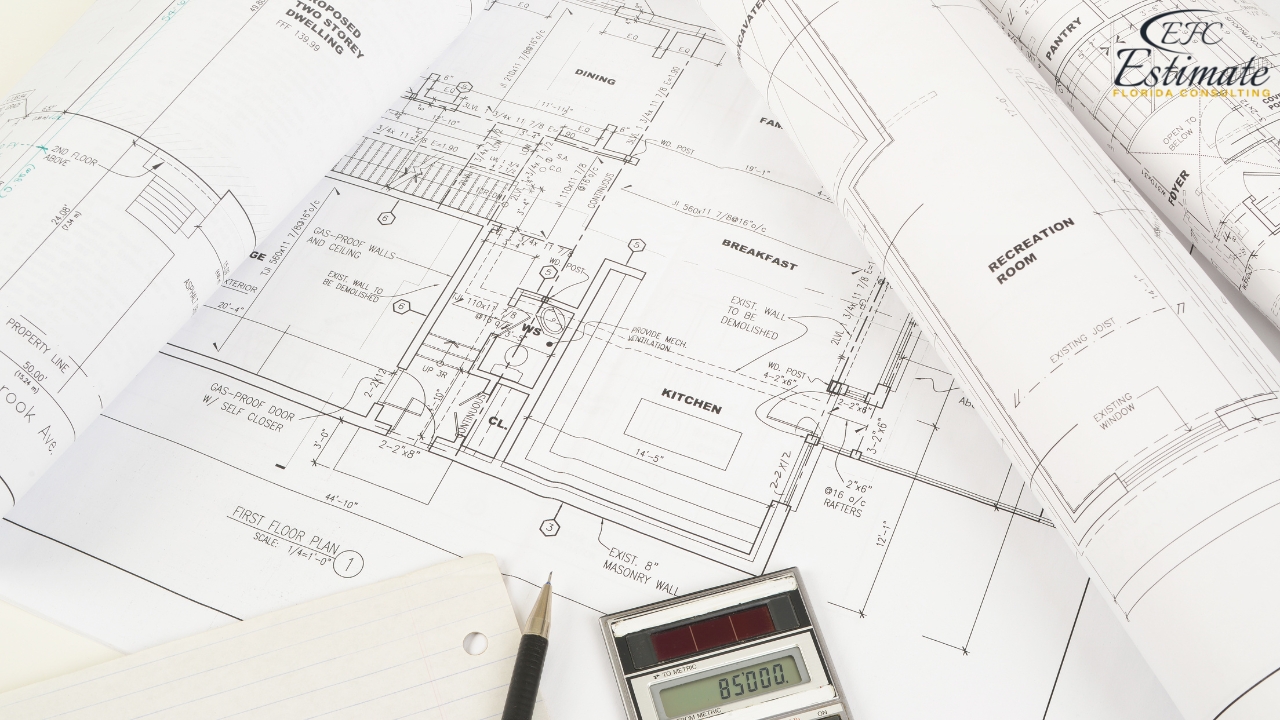
What is a Quantity Takeoff?
A quantity takeoff in construction is the process of estimating the quantities of materials required for a project based on drawings and plans. The information gathered during this process is typically recorded in a Bill of Quantities (BOQ). In practical terms, a quantity takeoff involves a construction cost estimator carefully analyzing project plans—such as architectural, structural, electrical, and water system drawings—to predict the material and labor costs for the project.
While the theoretical definition focuses on listing contract quantities, the practical application revolves around forecasting construction costs. This makes it a vital step in ensuring projects stay on budget and run efficiently.
Alternative Names for Quantity Takeoffs
Quantity takeoffs are referred to by several interchangeable terms in the construction industry, including:
- Construction takeoffs
- Material estimating
- Material takeoffs
- Material counts
- Quantity surveying
- Estimating takeoffs
- Earthwork takeoffs
The Importance of Quantity Takeoffs
Quantity takeoffs are a cornerstone of accurate cost estimation in construction projects. Their precision directly influences overall project costs, timelines, and client satisfaction. Below, we break down why quantity takeoffs are so crucial.
Cost Tracking
Accurate quantity takeoffs make it easier to track construction costs by providing a clear financial roadmap. Knowing the exact amount of money required for labor, equipment, and materials helps decision-making and prevents budget overruns. Proper takeoffs also create a financial cushion for unexpected expenses, ensuring that projects stay on track and aligned with the budget.
Improved Communication
In construction, everything revolves around cost. Clients want assurance that their money is being spent efficiently. Precise quantity takeoffs facilitate transparent communication between contractors and clients, fostering trust and ensuring clients remain informed about the project’s progress and expenditures. This clarity strengthens relationships and builds confidence in the project team.
Winning More Bids
Accurate takeoffs give contractors a competitive edge in bidding. Thorough research and well-calculated estimates demonstrate professionalism and reliability, helping contractors stand out from competitors. Consistency in delivering precise takeoffs reflects efficiency and credibility, ultimately leading to more successful bids. While preparing takeoffs might seem tedious, it can be the winning strategy for securing future projects.
Time Management
Quantity takeoffs streamline the budgetary and contractor selection process, saving valuable time for both clients and project teams. Accurate takeoffs reduce the likelihood of costly errors and rework, ensuring smoother project execution with fewer delays caused by budget overruns. Proper planning from the start allows projects to progress seamlessly, minimizing downtime and maximizing efficiency.
Types of Quantity Takeoffs
The construction industry has evolved significantly with the advent of technology, bringing transformative changes to the quantity takeoff process. Despite these advancements, the human element remains indispensable. Quantity takeoffs are categorized into two main types: manual takeoffs and digital takeoffs. Below, we delve into each type and their respective pros and cons.
Manual Takeoffs
Manual takeoffs are the traditional method of estimating material quantities. In this approach, construction estimators calculate quantities without the use of specialized cost estimation software, often relying on tools like Excel spreadsheets or word processors. The process involves:
- Reviewing the scope of work and project specifications outlined in the contract documents.
- Taking measurements directly from project drawings.
- Converting these measurements into the quantities required to complete the construction.
For manual takeoffs, estimators must have a strong understanding of construction plans and a meticulous approach to ensure nothing is missed during the process.
Pros of Manual Takeoffs
- Relies on expertise: Manual takeoffs benefit from the deep insight and experience of skilled cost estimators, ensuring a personalized touch that software might not provide.
- Validation tool: They can serve as a reliable cross-check for digital takeoffs, verifying their accuracy.
Cons of Manual Takeoffs
- Time-consuming: Manual processes are inherently slower, requiring significant time to manually input and analyze data.
- Less accurate: Compared to digital methods, manual takeoffs are more prone to human error, leading to potential inaccuracies in the final estimate.
Digital Takeoffs
Digital takeoffs leverage specialized software to streamline the estimation process, allowing for faster and more precise calculations. These tools can automatically extract measurements from uploaded project plans and integrate them into cost estimation models. Digital takeoffs are gaining popularity due to their efficiency and ability to handle complex projects.
Pros of Digital Takeoffs
- Speed and efficiency: Automated processes significantly reduce the time needed for takeoffs, enabling estimators to focus on other tasks.
- Increased accuracy: Advanced algorithms minimize errors, ensuring precise calculations that can be trusted for budgeting and planning.
- Data storage and retrieval: Digital tools allow for easy storage and access to previous projects, aiding in future estimates and comparisons.
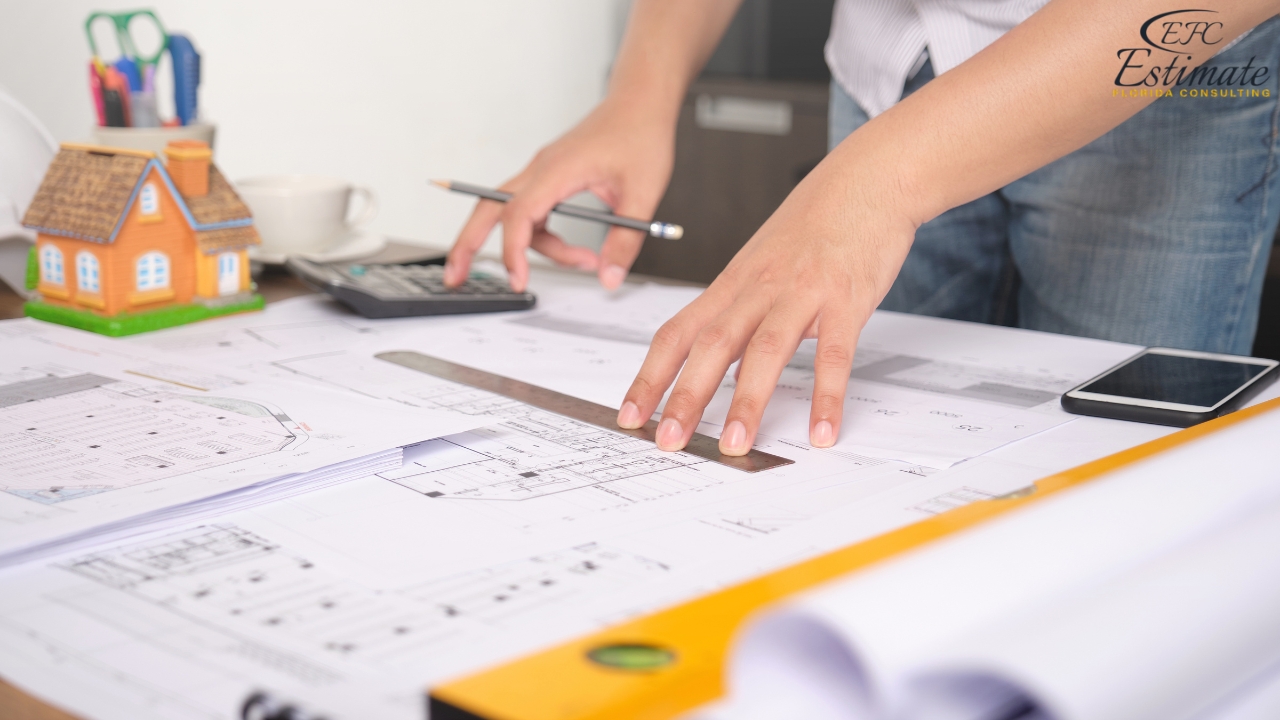
Cons of Digital Takeoffs
- Learning curve: Some estimators may require time to adapt to new software.
- Dependency on technology: Digital methods rely heavily on software and hardware, which may fail or require updates.
Digital Takeoffs
Digital takeoffs, powered by computer applications and databases, have transitioned from being a novel innovation to a standard practice in the construction industry. These takeoffs offer unmatched speed and accuracy compared to manual methods. They rely on digitizers—specialized electronic devices that measure data from project drawings and input it directly into software for analysis. These tools can process drawings of any size and format, making them versatile and efficient. However, due to the complexity of the technology, skilled technicians are needed to interpret results accurately and apply cost estimates effectively using the software.
Advantages of Digital Takeoffs
Enhanced Accuracy
Digital takeoffs are far more precise than manual methods. By extracting data directly from project drawings, they minimize human error and ensure that critical elements are not overlooked. This built-in redundancy improves the reliability of the estimates.
Time Efficiency
Digital tools significantly reduce the time required to produce a takeoff, cutting labor costs and allowing contractors to pursue additional opportunities. Their rapid turnaround time is a game-changer for tight project schedules.
Reduced Specialization Requirements
Unlike manual takeoffs, which require extensive expertise in reading blueprints and interpreting drawings, digital takeoffs rely on software functionalities. The software can process complex calculations and extract critical data, making it less reliant on the estimator’s specialized skills.
Quantity Takeoff vs. Material Takeoff
While the terms “quantity takeoff” and “material takeoff” are often used interchangeably, they refer to distinct processes.
Material Takeoff
A material takeoff focuses solely on the quantities of materials required to complete a project. It calculates the “gross quantities” of materials that must be purchased, such as bricks, cement, or steel.
Win More Projects With Us
Quantity Takeoff
A quantity takeoff is a broader process that encompasses material takeoffs but goes further. It also includes labor, equipment, and other non-material resources required for the project. For example, a quantity takeoff may calculate the time and cost for tasks like troweling or excavation, which are labor-intensive activities not tied directly to material quantities. Quantity takeoffs generally measure “net quantities,” providing a holistic view of all project needs.
Who is Involved in a Quantity Takeoff?
The quantity takeoff process involves a collaborative effort from all key personnel involved in the front-end planning of a construction project. This critical step begins during the preconstruction phase, particularly during the bidding process, to develop a realistic and accurate project contract.
Regardless of the project’s scale, the first task is to calculate the required materials and associated costs. The primary individuals responsible for this process include:
Key Participants
Architects
Architects provide detailed project drawings and specifications that form the foundation of the quantity takeoff process. Their input ensures that all design elements are accurately quantified.
Contractors
Contractors rely on takeoffs to understand the project scope, plan resource allocation, and submit competitive bids.
Cost Estimators
Cost estimators play a pivotal role in calculating the material quantities, labor, and equipment costs based on the drawings and project specifications. Their accuracy determines the financial feasibility of the project.
Engineers
Engineers ensure that the quantities align with structural and technical requirements, verifying the practicality and safety of the proposed designs.
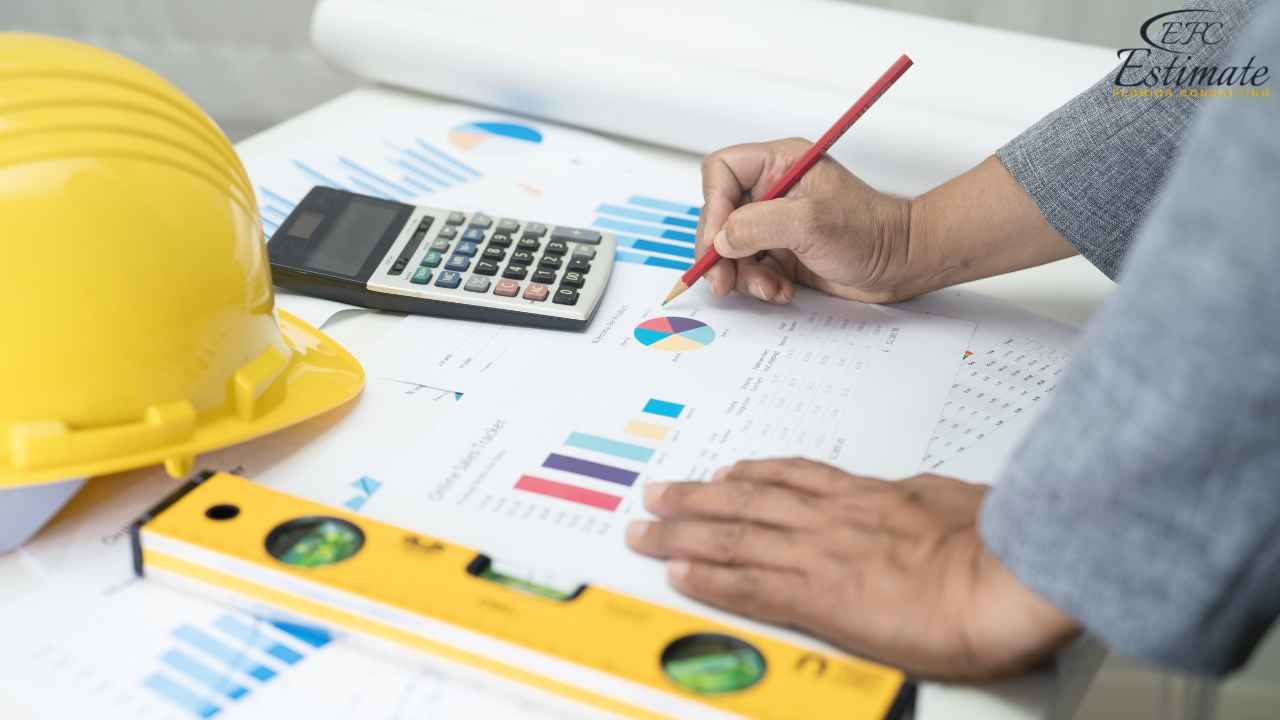
Additional Personnel
Depending on the project’s type and complexity, other specialists may also be involved in the quantity takeoff process, including:
- Urban Master Planners: For large-scale urban developments requiring comprehensive resource planning.
- Home Renovators or Residential Builders: For smaller projects like home renovations or custom home builds.
- Rail Transportation Engineers: For rail infrastructure projects with specific material and labor needs.
- Landscapers: For projects with significant outdoor design components.
- Highway Engineers: For road construction projects requiring detailed planning of asphalt, concrete, and other materials.
- Utility Contractors: For projects involving electrical, plumbing, or other utility installations.
How to Perform a Quantity Takeoff: An Example
Quantity takeoff requires skill, experience, and patience to ensure precision. An accurate takeoff not only influences the success of a project but also strengthens project proposals and helps contractors secure bids. Collaborative input from all involved staff ensures that the quantity takeoff process is thorough and reliable, minimizing errors and maximizing efficiency.
Who is Involved in a Quantity Takeoff?
Performing a quantity takeoff is a skill honed over time, blending precision, attention to detail, and experience. Whether done manually or digitally, the process involves two main components: input and output. While manual methods are still used, digital quantity takeoffs are preferred to minimize errors, as mistakes in the early stages can lead to costly issues later in the project.
Input Stage
The input stage focuses on collecting and validating the data needed for an accurate quantity takeoff. Whether using manual calculations or digital tools, this phase requires feeding correct data into the model.
- Data Collection: Use accurate project drawings, including architectural, structural, and engineering plans.
- Design Review: Cost estimators often rely on designs provided by architects or engineers. To ensure accuracy, a thorough review of the designs and concepts is necessary.
- Software Solutions: Digital tools often include features like clash detection and model validation to ensure that the provided data is free from inconsistencies.
Output Stage
In the output stage, the collected data is converted into specific material and resource requirements. This phase involves creating detailed estimates that provide the foundation for bidding, budgeting, and execution.
- Material Quantification: Accurately calculate the materials required for the project based on the input data.
- Cost Estimation: Align the material quantities with pricing systems to create a detailed and reliable estimate.
- Bid Preparation: The more detailed and accurate the data, the higher the likelihood of a successful bid submission.
The key to a successful output stage is focusing on precision, aligning materials and labor with costs, and avoiding overlooked details.
Get Acquainted with Estimation
Mastering Bids: 12 Pro-Level Bidding Tips for Construction Managers
Maximize Profits: Budgeting Hacks for Big Construction Projects
Example: Performing a Quantity Takeoff for a Masonry Wall
Below is a simplified step-by-step process for calculating the materials needed to construct a masonry wall:
Calculate the Net Surface Area of the Wall
- Measure the total surface area of the wall (in square feet or meters) from the structural drawings.
- Exclude any openings (e.g., doors and windows) and avoid double-counting corners.
Determine the Surface Area of a Single Brick
- Include the mortar joint in this calculation for accuracy.
Divide the Wall's Surface Area by the Brick's Surface Area
- This gives the total number of bricks required for the wall.
Add a Waste Factor
- Include an additional 2–10% to account for material wastage during construction.
For example, if a wall has a net surface area of 500 square feet and each brick covers 0.5 square feet (including mortar), the required number of bricks is:
Bricks Needed = 0.5/500 = 1,000 bricks
Adding a 5% waste factor:
Total Bricks = 1,000 × 1.05=1,050 bricks Total Bricks=1,000×1.05=1,050 bricks
This simple example demonstrates how basic takeoff calculations are performed, ensuring accuracy and efficiency in construction planning.
What Is Included in a Quantity Takeoff?
A quantity takeoff is a detailed and mathematical process of extracting values from project plans and converting them into measurable quantities. This forms the foundation of cost estimation by combining material quantities with labor, equipment, and overhead costs. Prefabricated materials required for the project are also accounted for. The primary challenge for quantity surveyors lies in interpreting two-dimensional plans and translating them into three-dimensional data for accurate takeoff calculations.
Here’s a breakdown of the key components typically included in a quantity takeoff:
Unit Count
This is one of the simplest tasks in a takeoff. It involves counting the number of single units required for the project, such as doors, windows, or fixtures. Estimators calculate the total quantity and multiply it by the unit price to determine the overall cost.
Linear Length
For materials like pipes, steel, and timber that are not measured by unit count, the length is used as the basis for calculation. Estimators measure the total combined length of these materials and use it to calculate their costs, often factoring in weight and pricing by unit length.
Surface Area
Surface area calculations are typically used for tasks like masonry, flooring, and painting. Estimators measure the length and width to determine the total area, enabling them to estimate material requirements and costs accurately.
Weight
Weight is a critical factor in estimating transportation costs and handling requirements. Materials such as steel and backfill are measured in tonnage to calculate shipping and installation expenses.
Cubic Volume
Cubic volume calculations are essential for three-dimensional materials and activities like earthworks, concrete pours, and excavation. These measurements account for the depth, length, and width of the materials, providing a comprehensive view of material quantities and related costs.
Download Template For Construction Project Breakdown
- Materials list updated to the zip code
- Fast delivery
- Data base of general contractors and sub-contractors
- Local estimators
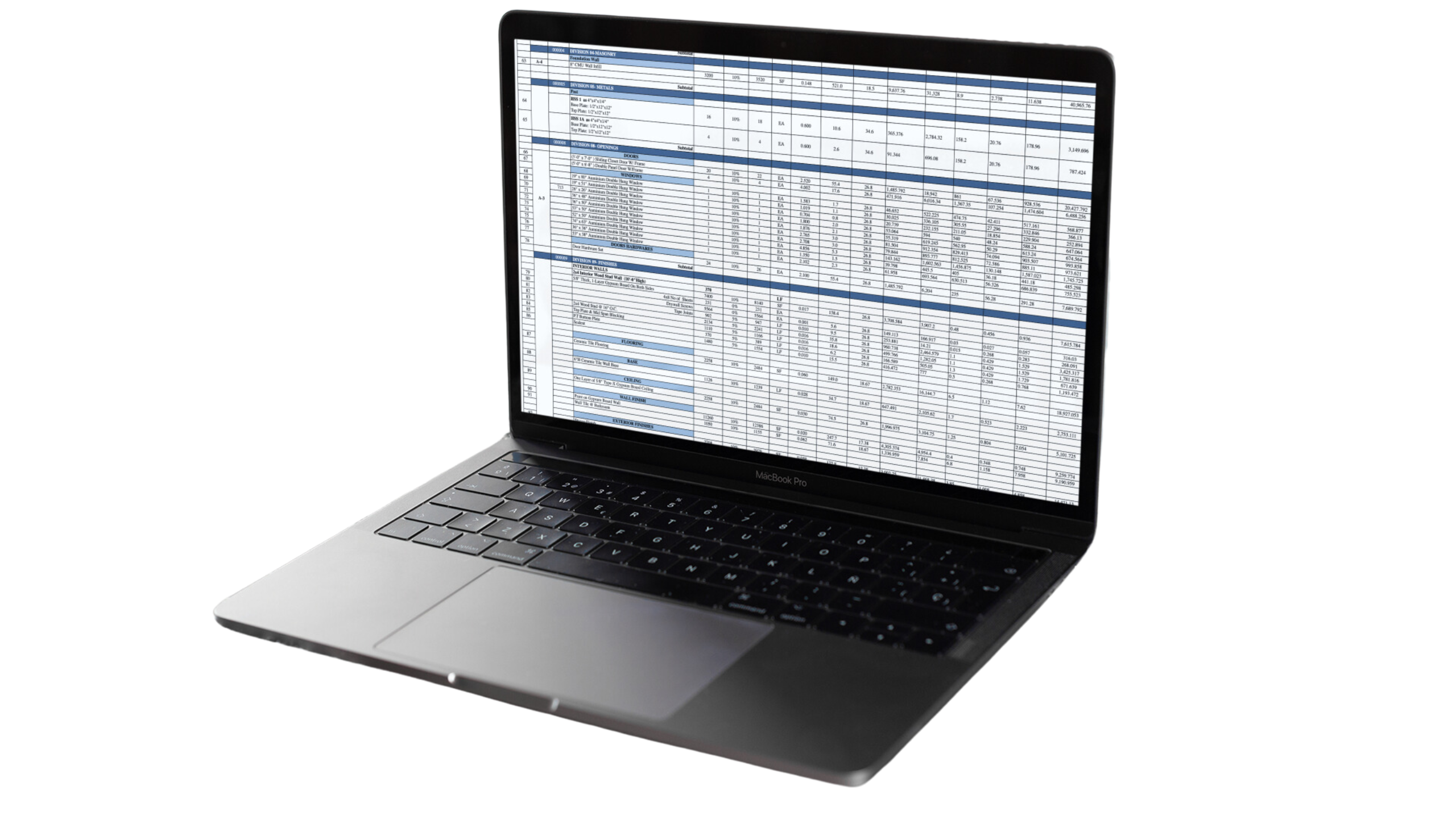
What Is Not Included in a Quantity Takeoff?
While quantity takeoffs provide detailed material and labor estimates, certain costs and factors are excluded to avoid confusion. These items are typically addressed later in the overall cost estimation process:
- Transportation Costs: Costs for moving materials to and from the site are calculated separately.
- Loading and Unloading Costs: The expense of handling materials during transportation is excluded.
- Scaffolding: Temporary structures required during construction are not included in takeoffs.
- Lapping and Waste Materials: Overlaps, wastage, and material scrap are excluded, as they are factored into contingency planning later.
- Stripping Formwork: The removal of temporary molds after concrete sets is excluded.
Conclusion
Quantity takeoffs are a fundamental part of the construction process, providing the foundation for accurate cost estimation and efficient project planning. By systematically analyzing project plans, they ensure precise material and labor calculations, helping contractors manage budgets, improve communication with clients, and win competitive bids. Whether performed manually or digitally, the quality of a quantity takeoff directly impacts the project’s success, from budgeting to execution. While digital tools have enhanced accuracy and efficiency, skilled professionals remain vital to interpret data and align estimates with project requirements. A well-executed takeoff minimizes errors, saves time, and ultimately leads to successful project outcomes.
Question Answer
Frequently Asked Question
A quantity takeoff is the process of estimating the quantities of materials, labor, and resources needed for a construction project by analyzing detailed project plans and drawings. It forms the basis of cost estimation and budget planning.
Quantity takeoffs are essential for accurate cost estimation, efficient resource planning, and budgeting. They help prevent cost overruns, streamline project execution, and improve communication between stakeholders.
A quantity takeoff typically includes:
- Material quantities (e.g., bricks, cement, steel)
- Labor requirements
- Equipment needs
- Unit counts, surface areas, linear lengths, and cubic volumes.
There are two main types:
- Manual Takeoffs: Performed by estimators using tools like blueprints, rulers, and spreadsheets.
- Digital Takeoffs: Conducted using specialized software that automates calculations for greater speed and accuracy.
- Material Takeoff: Focuses on the gross quantities of materials required.
- Quantity Takeoff: Includes material takeoff but also accounts for labor, equipment, and other project resources.
Popular software for digital takeoffs includes:
- PlanSwift
- Bluebeam Revu
- Autodesk Takeoff
- STACK Construction Takeoff Software
Comprehensive Trade-Specific Estimates
At Estimate Florida Consulting, we offer detailed cost estimates across all major trades, ensuring no part of your project is overlooked. From the foundation to the finishing touches, our trade-specific estimates provide you with a complete and accurate breakdown of costs for any type of construction project.
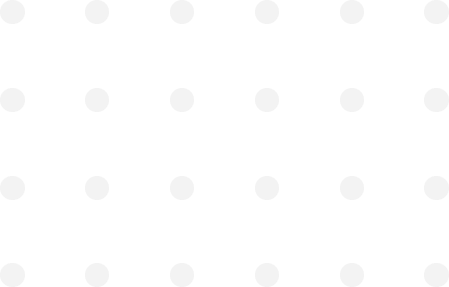
Testimonials
What Our Clients Say
We take pride in delivering accurate, timely, and reliable estimates that help contractors and builders win more projects. Our clients consistently praise our attention to detail, fast turnaround times, and the positive impact our estimates have on their businesses.
Estimate Florida Consulting has helped us win more bids with their fast and accurate estimates. We trust them for every project!
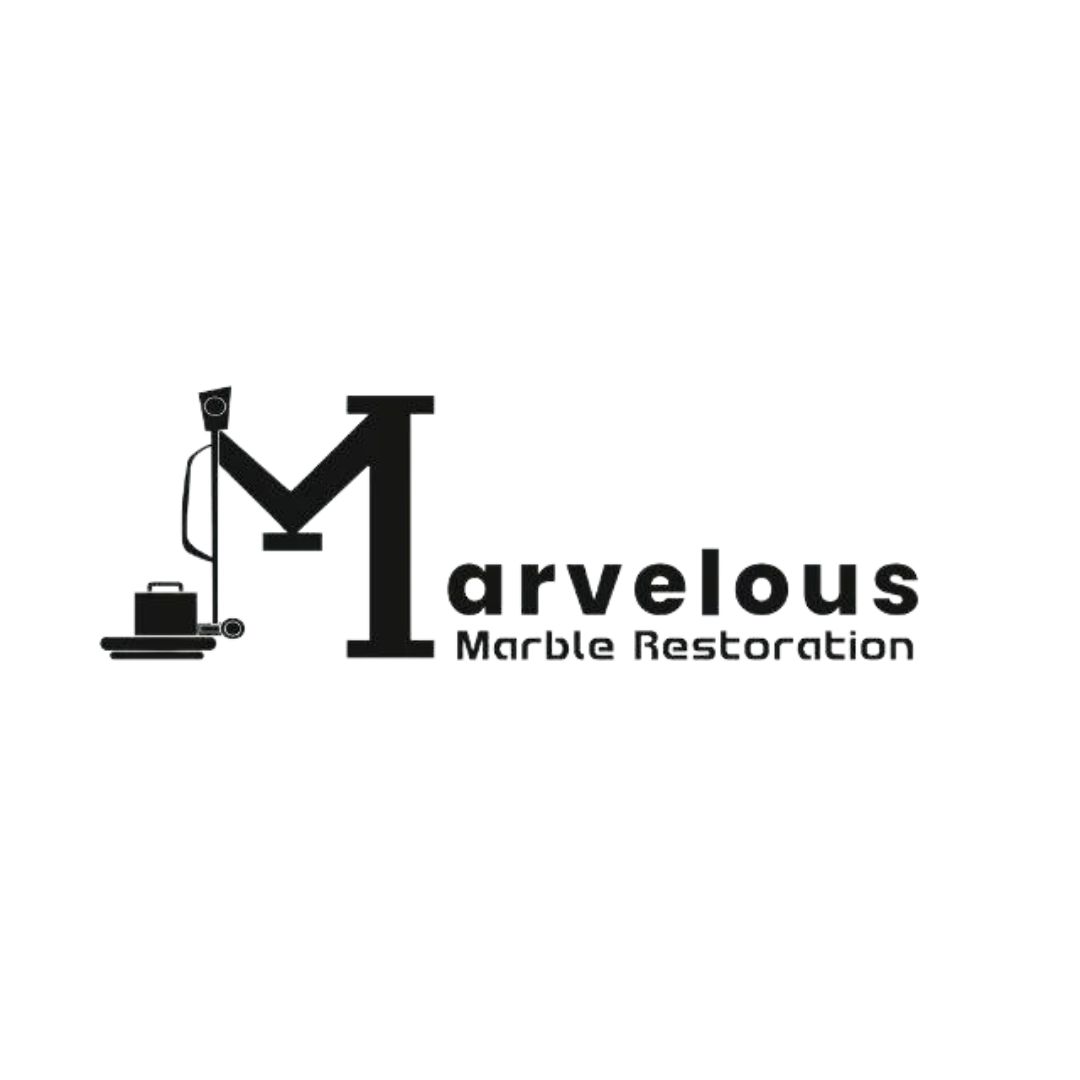
Steps to Follow
Our Simple Process to Get Your Estimate
01
Upload Plans
Submit your project plans, blueprints, or relevant documents through our online form or via email.
02
Receive Quotation
We’ll review your project details and send you a quote based on your scope and requirements.
03
Confirmation
Confirm the details and finalize any adjustments to ensure the estimate meets your project needs.
04
Get Estimate
Receive your detailed, trade-specific estimate within 1-2 business days, ready for your project execution.
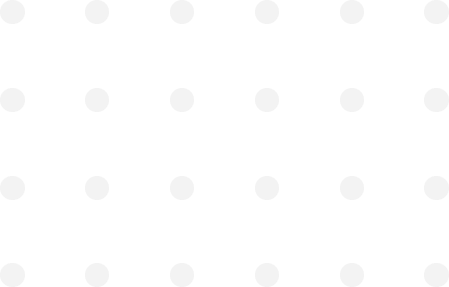