- Homepage
- Blogs
Built-Up Roofs (BUR) Cost Estimator
Leading provider of built-up roofs (BUR) estimating.
Built-Up Roofs (BUR), also known as tar and gravel roofs, are one of the most durable and cost-effective roofing systems for flat or low-sloped buildings. Whether it’s for residential or commercial structures, a BUR system involves alternating layers of bitumen (asphalt or coal tar) and reinforcing fabrics, creating a multi-ply, watertight membrane. This roofing type is favored due to its proven track record of performance, resistance to the elements, and long-lasting reliability.
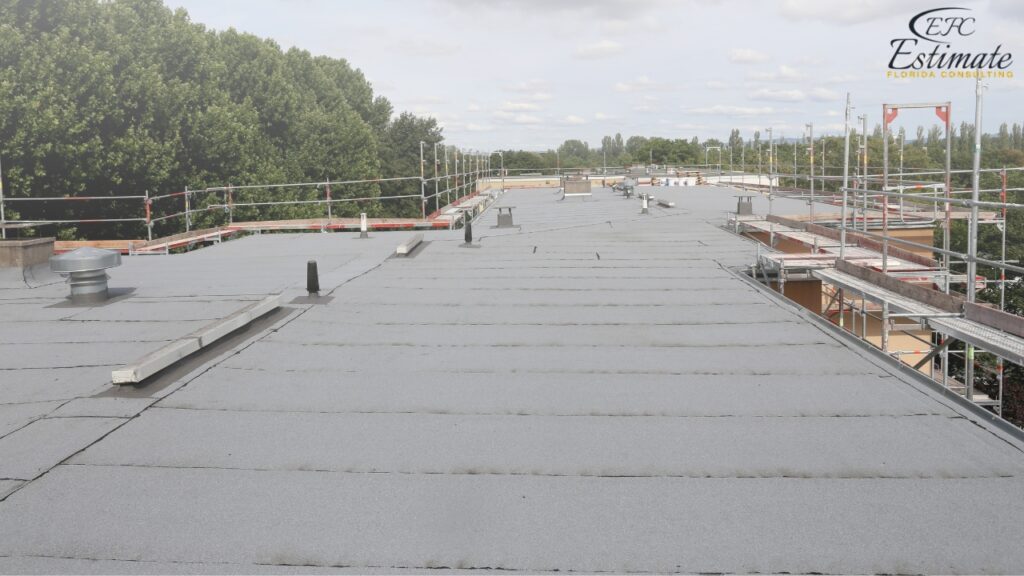
Built-Up Roof Cost per Square Foot
The cost of a Built-Up Roof can vary significantly depending on the materials used, the thickness of the layers, and the installation complexity. On average, you can expect the cost per square foot to range from $6.50 to $13 for residential buildings. In commercial settings, the cost can increase due to larger roof areas, ranging from $10.50 to $19.50 per square foot.
Installation Type | Average Cost per Square Foot |
Residential BUR | $6.50 – $13 |
Commercial BUR | $10.50 – $19.50 |
High-End Materials | $13.50 – $23 |
As seen in the table, different variables such as material quality and labor intensity significantly influence the final price. This estimate covers essential costs, including labor, materials, and equipment, but additional costs may arise if specialized features like reflective coatings or custom designs are chosen.
Built-Up Roof Cost by Size
The size of the roof is one of the most important factors in determining the total cost of a BUR system. Larger roofs require more material and labor, thus increasing the overall expense. Below is a cost breakdown by roof size:
Roof Size | Average Total Cost |
1,000 sq. ft. | $6,500 – $13,000 |
2,000 sq. ft. | $13,000 – $26,000 |
3,000 sq. ft. | $19,500 – $39,000 |
5,000 sq. ft. | $32,500 – $65,000 |
10,000 sq. ft. | $65,000 – $130,000 |
The cost rises as the roof area increases. Large commercial projects may reach six-figure price tags, depending on the materials and labor requirements.
Residential Built-Up Roof Costs
In residential buildings, the cost of installing a Built-Up Roof largely depends on the size of the roof, material choices, and labor rates. For a typical single-family home with a roof area of 2,000 square feet, the total cost of a BUR system may range from $13,000 to $26,000. Additional factors like roof pitch, insulation needs, and the complexity of the installation may increase the overall price.
Roof Size | Average Total Cost |
1,000 sq. ft. | $6,500 – $13,000 |
2,000 sq. ft. | $13,000 – $26,000 |
3,000 sq. ft. | $19,500 – $39,000 |
5,000 sq. ft. | $32,500 – $65,000 |
This cost breakdown shows the significant impact roof size has on the overall price. Larger roofs require more materials and labor, thereby driving up the cost.
Commercial Built-Up Roof Costs
Commercial buildings, such as warehouses, office buildings, or industrial facilities, typically have much larger roofs compared to residential properties. The cost of a commercial BUR installation can vary from $21,000 to $97,500 for roof sizes between 2,000 and 5,000 square feet. Complex installations or additional features, such as reflective coatings or enhanced insulation, may push the cost even higher.
Roof Size | Average Total Cost |
2,000 sq. ft. | $21,000 – $39,000 |
3,000 sq. ft. | $31,500 – $58,500 |
5,000 sq. ft. | $52,500 – $97,500 |
In commercial settings, BUR roofs offer a cost-effective solution for flat or low-sloped roofs, especially when long-term maintenance and energy efficiency are taken into account.
Win More Projects With Us
Types of Built-Up Roofs
Asphalt Built-Up Roofs
Asphalt-based BUR roofs are highly popular due to their affordability and waterproofing properties. Typically, asphalt BUR costs range from $6 to $14 per square foot. The multiple layers of asphalt provide effective weather resistance, making them a great choice for regions with varying climate conditions. The additional surfacing layer of gravel or a reflective coating can enhance its durability and protect against UV radiation, prolonging the roof’s lifespan.
Coal Tar Built-Up Roofs
Coal tar BUR systems are known for their exceptional chemical resistance and superior waterproofing abilities. They are primarily used in industrial or commercial buildings that are subject to harsh environmental conditions. The costs for coal tar BUR systems range from $10.50 to $19 per square foot, making them more expensive than asphalt-based systems, but the long-term savings from reduced repairs and maintenance often outweigh the initial investment.
Gravel-Surfaced BUR
Gravel-surfaced BUR is an attractive option for property owners who prioritize protection against physical damage, UV rays, and weather extremes. This type of BUR system adds a layer of gravel to shield the asphalt from direct sunlight, preventing cracks and degradation. The cost for gravel-surfaced BUR roofs ranges between $9 to $15 per square foot, with variations depending on the thickness of the gravel and the number of bitumen layers.
Modified Bitumen BUR
Modified Bitumen BUR is a hybrid roofing system that merges the benefits of traditional BUR with advanced bitumen technology. This roofing system offers enhanced flexibility, UV resistance, and superior weather protection. Costs for Modified Bitumen BUR range from $12.50 to $21 per square foot, making it a premium option for those seeking advanced protection and long-term reliability.
BUR Material Costs Breakdown
Asphalt
Asphalt is a core material in many BUR systems, known for its durability, affordability, and ease of application. The cost of asphalt typically ranges from $3.25 to $6.50 per square foot, depending on the quality of the asphalt and the thickness of the layers required for the project. Lower-end asphalt may offer sufficient protection for residential projects, while high-quality asphalt is often used in commercial or industrial applications where longevity and resilience are paramount. Asphalt’s ability to handle temperature fluctuations and its flexibility in various climate conditions make it a versatile and popular choice for BUR systems. However, the number of layers required, local market rates, and transportation costs can further impact the overall expense.
Coal Tar
Coal tar, though more expensive than asphalt, provides superior waterproofing and chemical resistance, making it a preferred material for projects requiring enhanced protection, such as industrial settings. The cost of coal tar ranges from $4.75 to $9 per square foot, depending on the project’s specific requirements and the quality of the coal tar. Despite its higher price, coal tar offers extended longevity, often outlasting asphalt in environments where chemical exposure or standing water is common. Additionally, coal tar performs well under prolonged exposure to ultraviolet rays, reducing the potential for cracks or surface degradation. The long-term durability of coal tar can result in lower maintenance costs, offsetting the higher initial investment.
Fiberglass Felt
Fiberglass felt acts as a crucial reinforcing layer in BUR systems, providing both strength and flexibility to the roof membrane. This material helps bind the layers of asphalt or coal tar, ensuring that the roof remains structurally sound while offering resistance to punctures and tears. The cost of fiberglass felt ranges from $1.50 to $3 per square foot, depending on factors like thickness, manufacturer, and regional availability. While thinner felt is generally sufficient for residential installations, thicker and more durable options are typically chosen for commercial applications where added strength is necessary. Fiberglass felt’s lightweight nature also helps reduce overall roof weight, making it a practical option for buildings with load-bearing limitations.

Gravel and Ballast
Gravel and ballast serve an important protective function in BUR systems, shielding the roof from ultraviolet rays and weathering while helping to anchor the roofing materials. The cost of gravel and ballast typically ranges between $2.50 to $5 per square foot, depending on the size of the gravel used, the depth of the ballast layer, and the region where the materials are sourced. Heavier ballast provides greater protection from high winds and can prevent the roof membrane from shifting, while lighter gravel can offer sufficient protection for areas with less severe weather. In addition to UV protection, gravel and ballast improve the roof’s fire resistance and add an extra layer of durability against physical impacts. The quantity of gravel used also affects the insulation value of the roof, contributing to energy savings over time.
Built-Up Roof Installation Costs
Labor costs for BUR installation play a significant role in the overall project price, often accounting for a significant portion of the total expense. Since installation involves multiple layers of material and precise workmanship, it can be labor-intensive, requiring skilled laborers to ensure the roof is installed correctly. The labor cost per square foot generally ranges between $3 to $7, depending on the complexity of the roof design, local labor rates, and the experience of the installation crew. Factors such as roof slope, accessibility, and weather conditions during installation can also influence labor costs. More complex roof designs, such as those with numerous penetrations or unique architectural features, may require additional labor time, pushing costs higher.
Built-Up Roof Maintenance and Repair Costs
Maintenance and repairs are essential to prolong the life of a BUR system and avoid more costly replacements in the future. Routine maintenance costs for BUR systems range from $0.50 to $2.50 per square foot annually, depending on the roof’s condition and the type of maintenance required. This can include inspections, cleaning, and minor repairs to keep the roof in optimal shape. Repair costs can vary significantly depending on the extent of damage and the nature of the repair work. For example, small repairs like patching leaks or fixing small punctures may cost between $300 to $1,200. Larger repairs, such as addressing extensive water damage or replacing sections of the roof, can exceed $5,000. Regular inspections and proactive maintenance are essential to detect issues early and prevent more expensive repairs down the line.
Energy Efficiency and Longevity of BUR
Modern BUR systems are designed with energy efficiency in mind, making them a cost-effective choice for property owners. By using reflective coatings or light-colored surfacing materials, property owners can reduce heat absorption, leading to lower cooling costs during hot seasons. These reflective surfaces help prevent excessive heat buildup, particularly in areas with high sun exposure, thereby reducing the strain on HVAC systems. This energy-saving feature, combined with proper insulation, can contribute to significant long-term savings on energy bills. Moreover, investing in energy-efficient BUR systems may also qualify for local tax incentives or rebates, further improving cost savings over time. When paired with regular maintenance, BUR systems can often exceed a lifespan of 20 to 30 years, making them a durable and energy-efficient roofing solution.
Get Acquainted
Which Construction Software is Best?
How the start an estimate in Buildxact?
Built-Up Roof Lifespan and Durability
Built-Up Roofs are renowned for their long lifespan, which can extend beyond 25 years with proper care and maintenance. The durability of BUR systems makes them an ideal choice for areas prone to extreme weather conditions such as heavy rain, snow, high winds, and intense sunlight. The multi-layer structure, consisting of alternating layers of bitumen and reinforcing fabrics, creates a robust barrier that effectively protects the underlying structure from water damage, UV rays, and physical impacts. This makes BUR systems highly resistant to punctures, tears, and weather-related wear. In regions with harsh weather, BUR systems provide enhanced protection, minimizing the risk of leaks and structural damage. Property owners can expect their BUR systems to withstand the elements for decades, providing peace of mind and reducing the frequency of major repairs or replacements.
What is a Built-Up Roof (BUR)?
A Built-Up Roof (BUR) is a roofing system created by layering multiple sheets of reinforcing fabric, typically fiberglass or organic material, and bonding them together with alternating layers of hot bitumen. The layers are then topped with a surfacing material like gravel or asphalt, which acts as a protective shield. BUR is highly efficient for waterproofing flat and low-slope roofs due to its multi-layer structure, which provides enhanced durability and longevity. These roofs have been used for over a century, with modifications that now include reflective coatings to improve energy efficiency.
Download Template For Condominium construction Project Breakdown
- Materials list updated to the zip code
- Fast delivery
- Data base of general contractors and sub-contractors
- Local estimators
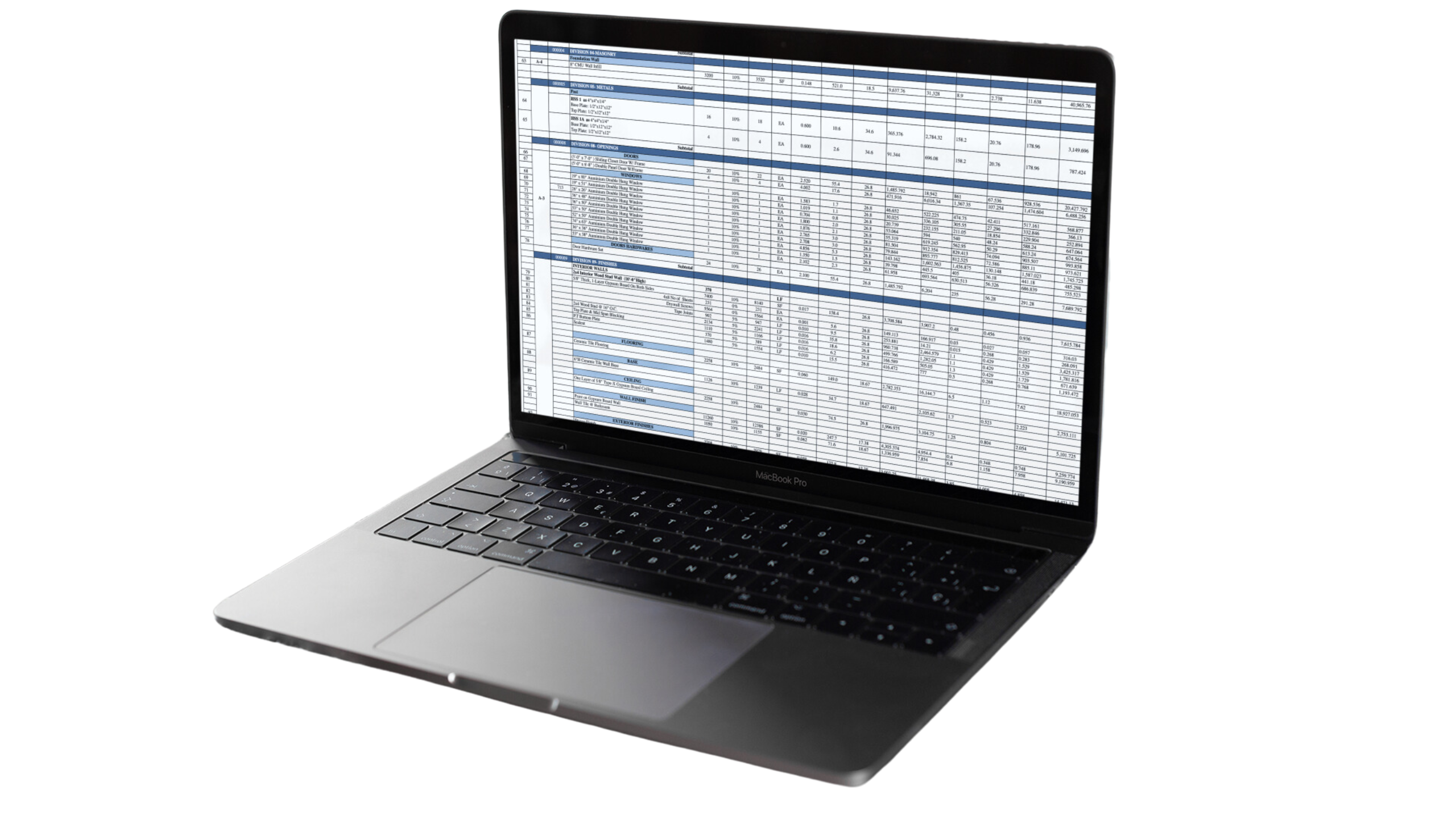
Conclusion
Built-Up Roofs are a time-tested solution for both residential and commercial properties, offering a balance of durability, cost-efficiency, and longevity. While the upfront costs may seem high, the long-term benefits of reduced maintenance, energy efficiency, and extended lifespan make BUR a wise investment for property owners. By understanding the cost breakdown of materials, installation, and maintenance, you can make an informed decision when selecting the best roofing solution for your building.
Question Answer
Frequently Asked Question
The cost of a modified bitumen roof typically ranges from $12.50 to $21 per square foot. Factors such as material quality, installation complexity, and the specific roofing project can affect the overall price.
To estimate the cost of a new roof, consider the roof size (in square feet), the type of roofing material used (e.g., asphalt shingles, BUR, or modified bitumen), labor costs, and any additional features such as insulation or coatings. Average roofing costs can range from $6.50 to $23 per square foot, depending on these factors.
Replacing 500 sq ft of roofing can cost between $3,250 and $10,500, depending on the roofing material, labor rates, and specific project requirements.
Hot mop roofing is considered a cost-effective option for flat or low-sloped roofs, with prices ranging between $2.50 and $5 per square foot. While it is not as expensive as some other roofing systems, the overall cost depends on the project scope and roof size.
A hot mop roof can last between 15 to 20 years with proper maintenance. Regular inspections and repairs can help extend its lifespan.
The choice between hot mop and membrane roofing depends on specific project needs. Hot mop is more cost-effective but may require more frequent maintenance. Membrane roofing, such as TPO or PVC, offers superior durability and UV resistance, often lasting longer with less maintenance.
Comprehensive Trade-Specific Estimates
At Estimate Florida Consulting, we offer detailed cost estimates across all major trades, ensuring no part of your project is overlooked. From the foundation to the finishing touches, our trade-specific estimates provide you with a complete and accurate breakdown of costs for any type of construction project.
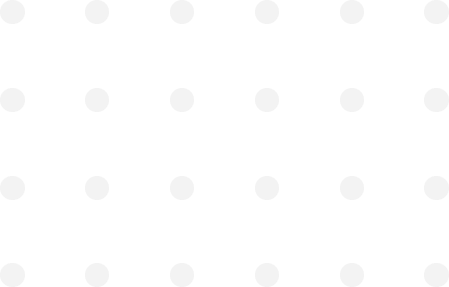
Testimonials
What Our Clients Say
We take pride in delivering accurate, timely, and reliable estimates that help contractors and builders win more projects. Our clients consistently praise our attention to detail, fast turnaround times, and the positive impact our estimates have on their businesses.
Estimate Florida Consulting has helped us win more bids with their fast and accurate estimates. We trust them for every project!
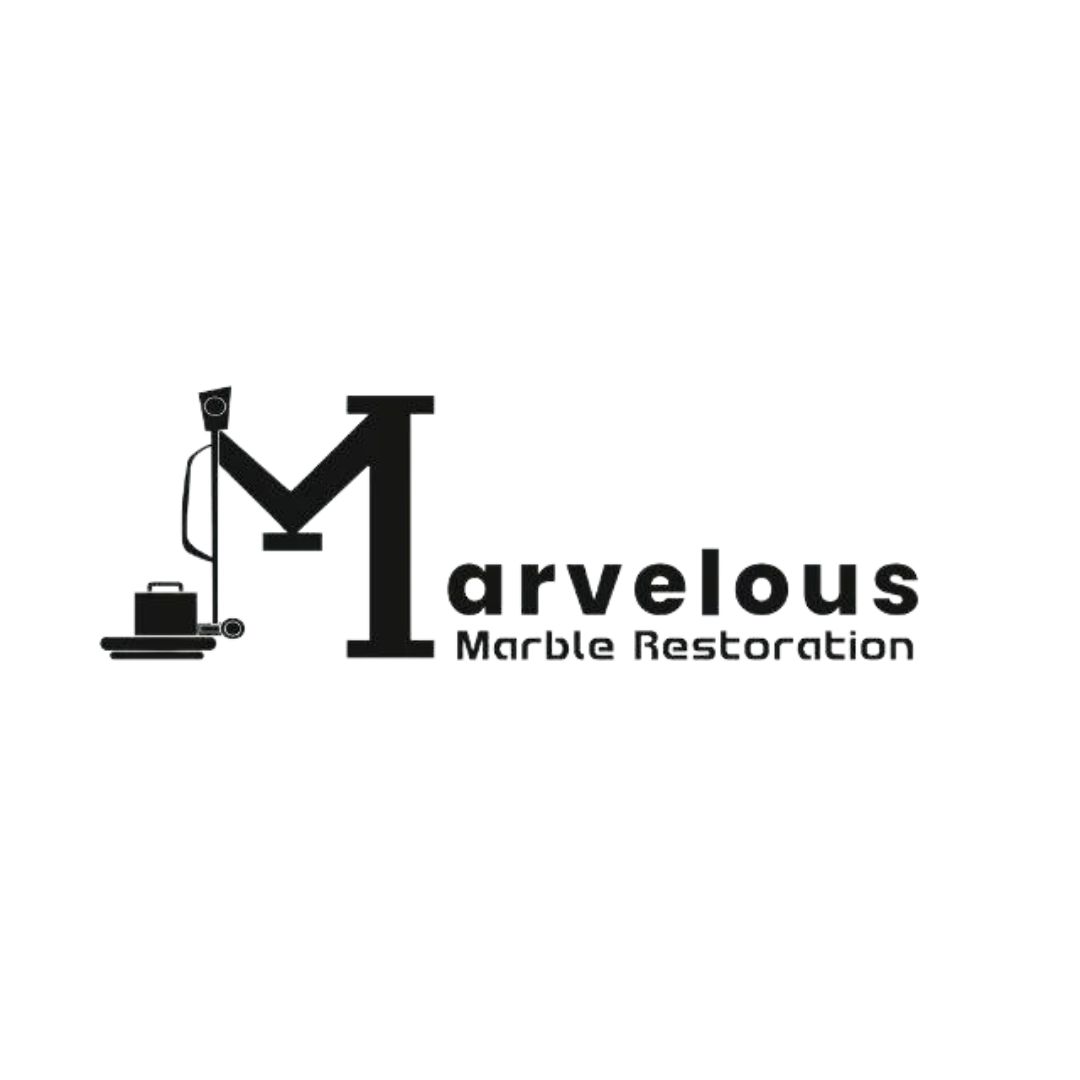
Steps to Follow
Our Simple Process to Get Your Estimate
01
Upload Plans
Submit your project plans, blueprints, or relevant documents through our online form or via email.
02
Receive Quotation
We’ll review your project details and send you a quote based on your scope and requirements.
03
Confirmation
Confirm the details and finalize any adjustments to ensure the estimate meets your project needs.
04
Get Estimate
Receive your detailed, trade-specific estimate within 1-2 business days, ready for your project execution.
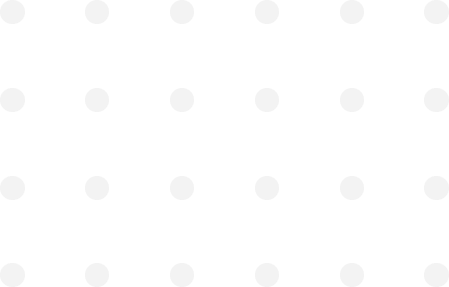