90% More Chances to Win Projects With Our Estimate!
- Multi-Family Building
- Hotel Building
- Hospital Building
- Warehouse Building
- School & University Building
- High-Rise Building
- Shopping Complex
- Data Center Building
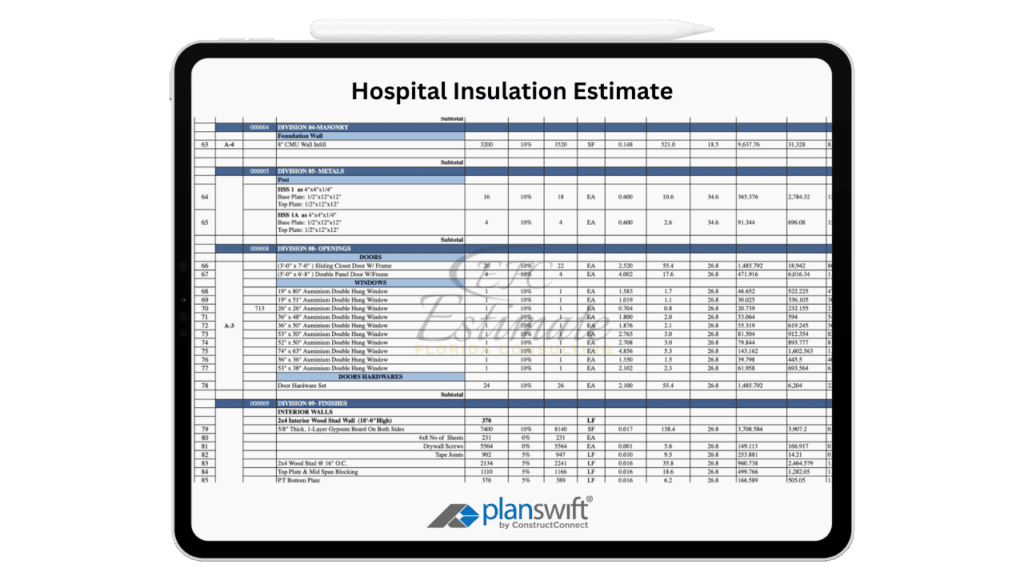
Insulation is an essential component of any building, playing a vital role in energy efficiency, comfort, and long-term operational costs. For homeowners, contractors, and developers, understanding insulation material options and their associated costs is crucial for making informed decisions that align with both budget and performance expectations. This guide will provide a comprehensive overview of insulation materials, their costs, and factors influencing these costs, particularly within the diverse climate of Florida.
The installation costs for insulation can vary widely based on the type of insulation chosen, the area to be insulated, and the complexity of the installation. Below is a breakdown of estimated installation costs based on different insulation materials:
Insulation Type | Installation Cost per Square Foot |
Fiberglass Insulation | $1.47 – $2.93 |
Foam Board Insulation | $2.93 – $4.40 |
Spray Foam Insulation | $2.93 – $8.80 |
Cellulose Insulation | $1.98 – $4.40 |
Mineral Wool Insulation | $2.93 – $5.85 |
Selecting the right insulation material is critical for achieving optimal performance and cost-effectiveness. There are several types of insulation materials available, each with unique properties, advantages, and costs. Understanding these options is essential for homeowners and contractors looking to ensure efficient insulation installations while maximizing their return on investment.
Fiberglass insulation remains one of the most popular choices in both residential and commercial applications due to its affordability and effectiveness. This material comes in various forms, including batts, rolls, and loose-fill, making it versatile for different applications. Fiberglass insulation provides excellent thermal resistance, with an R-value typically ranging from R-2.9 to R-4.3 per inch, depending on the density and type used. Additionally, it is relatively easy to install, which can save on labor costs, making it a go-to option for many construction projects. The average cost for fiberglass insulation typically ranges from $1.47 to $4.40 per square foot, depending on the specific type and installation method.
Fiberglass Insulation Type | Average Cost per Square Foot |
Batt Insulation | $1.47 – $2.93 |
Loose-Fill Insulation | $2.93 – $4.40 |
Fiberglass insulation also has a relatively long lifespan, often lasting several decades, and can help reduce noise transfer between rooms, making it suitable for both residential and multi-family dwellings. Additionally, many fiberglass products are made with recycled materials, enhancing their environmental appeal. It is also resistant to moisture and does not support mold growth, adding to its durability. Proper installation is crucial, as gaps and compression can significantly reduce the effectiveness of fiberglass insulation.
Foam board insulation offers exceptional thermal resistance and is commonly utilized in various applications, including basement walls, exterior walls, and roofs. Its rigid structure allows it to maintain insulation performance even under high moisture conditions, making it an ideal choice for Florida’s humid environment. The typical cost for foam board insulation is between $2.14 and $7.32 per square foot.
Foam Board Insulation Type | Average Cost per Square Foot |
Rigid Foam Board | $2.14 – $4.40 |
Extruded Polystyrene | $4.40 – $7.32 |
The effectiveness of foam board insulation in preventing thermal bridging is significant, helping to create a continuous thermal barrier that enhances energy efficiency. Its lightweight nature and ease of installation further contribute to its popularity in construction projects. Foam board insulation also provides excellent soundproofing capabilities, which can enhance the quality of life in residential settings. Its versatility makes it a suitable option for both new constructions and retrofits, as it can be applied to walls, roofs, and even foundation systems.
Spray foam insulation is increasingly favored for its superior sealing capabilities and adaptability. This material expands upon application, filling gaps and crevices, which significantly improves air sealing. This characteristic is particularly important in climates with high humidity, where moisture can become a concern. The cost for spray foam insulation typically falls between $4.40 and $8.80 per square foot, depending on the application method and material used.
Spray Foam Type | Average Cost per Square Foot |
Open-Cell Spray Foam | $4.40 – $5.85 |
Closed-Cell Spray Foam | $5.85 – $8.80 |
While spray foam insulation may have a higher initial cost, its effectiveness in reducing energy loss can result in significant long-term savings on energy bills. Moreover, it can also provide additional benefits such as soundproofing and moisture resistance. Homeowners and builders alike appreciate the ability of spray foam to enhance the overall energy efficiency of a building, often leading to a more comfortable living environment. The flexibility of application makes it suitable for a variety of structures, including hard-to-reach areas and retrofitting projects.
Made primarily from recycled paper products, cellulose insulation is an environmentally friendly option that also provides good thermal performance. It is treated with fire retardants, making it a safe choice for various applications. The cost for cellulose insulation generally ranges from $2.93 to $4.40 per square foot for loose-fill applications, often blown into attics and wall cavities.
Cellulose Insulation Type | Average Cost per Square Foot |
Loose-Fill Cellulose | $2.93 – $4.40 |
Blown-In Cellulose | $3.38 – $5.08 |
Cellulose insulation offers excellent air barrier properties and can help minimize air leakage, further enhancing a building’s energy efficiency. Its recycled nature also appeals to environmentally conscious homeowners and builders. Additionally, cellulose is known for its ability to absorb sound, making it a suitable choice for enhancing acoustic performance in multi-family housing and commercial applications. Proper installation is critical, as settled cellulose can lose its effectiveness, so hiring a professional installer is recommended.
Mineral wool insulation is recognized for its fire resistance, soundproofing properties, and resistance to moisture. It can be used in various applications, including walls, ceilings, and floors. The cost of mineral wool insulation typically falls between $2.93 and $5.85 per square foot.
Mineral Wool Insulation Type | Average Cost per Square Foot |
Batt or Roll Mineral Wool | $2.93 – $4.40 |
Loose-Fill Mineral Wool | $4.40 – $5.85 |
When selecting insulation, it’s essential to consider not only the initial costs but also the long-term savings associated with energy efficiency. Here’s a comparative analysis of insulation materials based on cost, R-value, and application.
Insulation Type | Average Cost per Square Foot | Average R-Value | Best Applications |
Fiberglass | $0.98 – $2.93 | R-3.0 to R-4.0 | Walls, ceilings |
Foam Board | $1.56 – $3.90 | R-4.0 to R-6.0 | Exterior walls, foundations |
Spray Foam | $1.76 – $5.85 | R-5.0 to R-7.0 | Attics, crawl spaces |
Cellulose | $1.36 – $2.93 | R-3.5 to R-4.0 | Walls, attics |
Mineral Wool | $1.56 – $3.32 | R-3.0 to R-4.0 | Walls, roofs |
Radiant Barrier | $0.98 – $1.95 | R-2.0 to R-3.0 | Attics, roofs |
Many homeowners opt for DIY installation to save on labor costs. While this approach can reduce expenses, it requires knowledge of insulation techniques and safety measures.
Installation Method | Average Cost per Square Foot |
DIY Installation | $0.98 – $1.95 |
Hiring professionals to install insulation guarantees a high-quality result and adherence to local building codes. Professional installation typically costs more but can save money on energy bills in the long run.
Installation Method | Average Cost per Square Foot |
Professional Installation | $1.95 – $4.88 |
Several key factors can influence the overall cost of insulation materials and installation. Understanding these factors is essential for making informed choices and managing budgets effectively.
Different types of insulation materials come with varying costs due to their manufacturing processes, thermal properties, and effectiveness. While high-performance options like spray foam may have a higher upfront cost, they can yield long-term energy savings that outweigh initial investments. Contractors and homeowners should carefully consider the balance between cost and performance when selecting insulation materials.
The complexity of the installation process can significantly impact labor costs. For example, installing spray foam requires specialized equipment and trained professionals, increasing the overall expense compared to more straightforward insulation types, such as fiberglass batts. Additionally, the size and shape of the area being insulated can influence installation costs, as irregular spaces may require more time and effort to insulate effectively.
The geographic location of a project can also affect insulation costs. Areas with a higher cost of living often experience elevated labor rates, impacting the overall cost of installation. Additionally, if the project site is difficult to access, it may lead to higher transportation and equipment costs, further adding to expenses.
Local building codes and regulations can dictate specific insulation requirements, which may affect material choices and installation methods. Adhering to these codes is essential to avoid potential fines or costly mistakes during the construction process. Ensuring compliance can also influence the types of insulation selected, as certain materials may be more suitable for specific applications than others.
Investing in high-quality insulation materials may result in substantial long-term savings on energy bills. Energy-efficient insulation minimizes heat transfer, reducing the need for heating and cooling, which in turn lowers energy consumption. Homeowners may also qualify for rebates or incentives for implementing energy-efficient improvements. Understanding these potential savings can help justify the upfront costs associated with premium insulation materials.
Beyond immediate cost savings, energy-efficient insulation contributes to a more sustainable future. By reducing energy consumption, homeowners can decrease their carbon footprint, promoting environmental stewardship. Moreover, energy-efficient homes tend to have higher resale values, appealing to eco-conscious buyers. The benefits of investing in effective insulation extend well beyond immediate financial considerations, influencing long-term comfort and sustainability.
Choosing the right insulation material is critical for ensuring energy efficiency, comfort, and cost-effectiveness in any building project. By understanding the various insulation options available, their associated costs, and the factors influencing these costs, homeowners, contractors, and developers can make informed decisions that align with their budget and performance needs. Investing in high-quality insulation not only enhances comfort and energy efficiency but also contributes to the overall sustainability of the building, ultimately leading to long-term financial benefits.
To estimate the cost of insulation, you need to consider several factors: the type of insulation material (such as fiberglass, spray foam, cellulose, etc.), the total square footage to be insulated, and the installation costs. Begin by determining the area (in square feet) that requires insulation. Next, research the average cost per square foot for your chosen insulation type. For instance, fiberglass insulation ranges from $1.47 to $4.40 per square foot, while spray foam can range from $4.40 to $8.80. Finally, multiply the cost per square foot by the total square footage, and add installation costs, which vary from $1.95 to $4.88 per square foot for professional services.
Insulation material costs can vary widely depending on the type. Here's a brief overview of average costs per square foot for various insulation materials:
The cost to insulate 1,000 square feet depends on the insulation material selected. For example, using fiberglass insulation, the cost would range from approximately $1,470 to $4,400. If you choose spray foam insulation, the cost could be between $4,400 and $8,800. Remember to add installation costs, which could range from $1,950 to $4,880 for professional installation.
To insulate a 2,500 square foot attic, the cost can vary significantly based on insulation type. Using the average costs, if you choose cellulose insulation (around $2.93 - $4.40 per square foot), it would range from approximately $7,325 to $11,000. For spray foam insulation, it could range from $11,000 to $22,000, considering installation costs. Always factor in both material and labor costs when estimating.
Insulating a 3,000 square foot house could range widely depending on the type of insulation chosen. For instance, if you opt for fiberglass insulation, costs could range from $4,410 to $13,200, while using spray foam insulation could run between $13,200 and $26,400. These estimates include both material and professional installation costs. Always calculate based on the specific areas needing insulation.
The choice between blown (typically cellulose or fiberglass) and rolled insulation (usually fiberglass batts) depends on several factors, including the space's shape and accessibility. Blown insulation is often preferred for attics because it can fill gaps and irregular spaces more effectively, providing better coverage and a more consistent thermal barrier. It also has excellent soundproofing properties. Rolled insulation can be more cost-effective for standard-sized areas and is easier for DIY projects, but it may leave gaps if not installed properly. Ultimately, for most attics, blown insulation is typically considered superior due to its efficiency and coverage capabilities.
At Estimate Florida Consulting, we offer detailed cost estimates across all major trades, ensuring no part of your project is overlooked. From the foundation to the finishing touches, our trade-specific estimates provide you with a complete and accurate breakdown of costs for any type of construction project.
We take pride in delivering accurate, timely, and reliable estimates that help contractors and builders win more projects. Our clients consistently praise our attention to detail, fast turnaround times, and the positive impact our estimates have on their businesses.
Estimate Florida Consulting has helped us win more bids with their fast and accurate estimates. We trust them for every project!
Submit your project plans, blueprints, or relevant documents through our online form or via email.
We’ll review your project details and send you a quote based on your scope and requirements.
Confirm the details and finalize any adjustments to ensure the estimate meets your project needs.
Receive your detailed, trade-specific estimate within 1-2 business days, ready for your project execution.
561-530-2845
info@estimatorflorida.com
Address
5245 Wiles Rd Apt 3-102 St. Pete Beach, FL 33073 United States
561-530-2845
info@estimatorflorida.com
Address
5245 Wiles Rd Apt 3-102 St. Pete Beach, FL 33073 United States
All copyright © Reserved | Designed By V Marketing Media | Disclaimer