90% More Chances to Win Projects With Our Estimate!
- Multi-Family Building
- Hotel Building
- Hospital Building
- Warehouse Building
- School & University Building
- High-Rise Building
- Shopping Complex
- Data Center Building
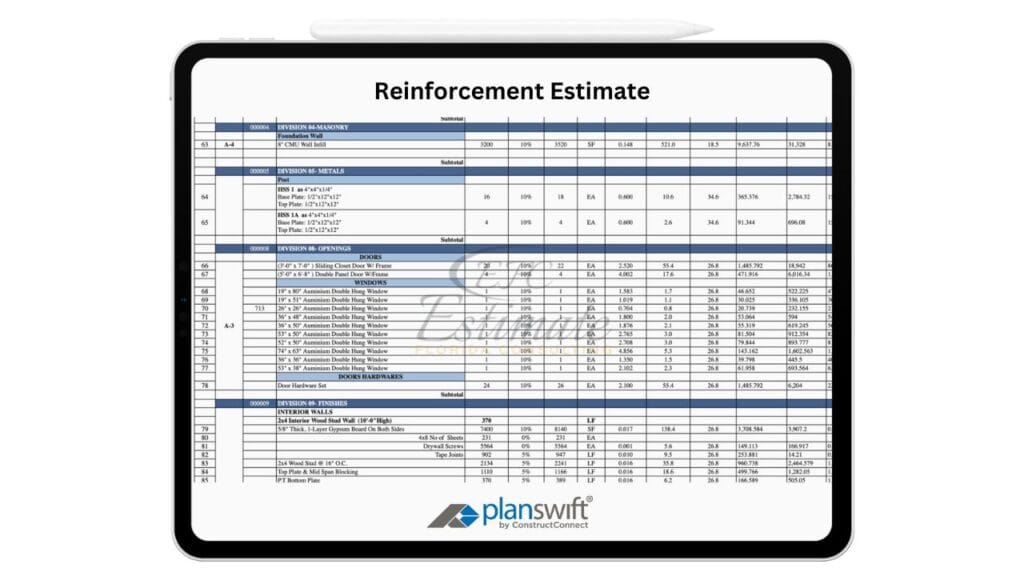
Reinforcement is vital in construction projects, ensuring that structures can withstand various stresses and loads. The costs associated with reinforcement can vary widely based on the type of materials used, labor rates, and the overall complexity of the project. On average, reinforcement costs can range from $0.65 to $3.90 per pound for steel reinforcement, depending on market conditions and specifications. Accurate reinforcement cost estimation is crucial for effective budgeting and successful project management.
Reinforcement is vital in construction projects, ensuring that structures can withstand various stresses and loads. The costs associated with reinforcement can vary widely based on the type of materials used, labor rates, and the overall complexity of the project. On average, reinforcement costs can range from $0.65 to $3.90 per pound for steel reinforcement, depending on market conditions and specifications. Accurate reinforcement cost estimation is crucial for effective budgeting and successful project management.
Steel reinforcement, commonly referred to as rebar, is widely used in concrete structures to improve tensile strength and ductility. The cost of steel reinforcement varies based on the grade, diameter, and market fluctuations. Steel prices have been volatile in recent years, significantly impacting overall construction budgets.
Rebar Diameter (inches) | Estimated Cost per Ton |
#3 (3/8″) | $780 – $1,170 |
#4 (1/2″) | $910 – $1,300 |
#5 (5/8″) | $1,040 – $1,560 |
#6 (3/4″) | $1,170 – $1,690 |
Fiber reinforcement involves adding fibers (steel, glass, or synthetic) to concrete to enhance its properties, improving its resistance to cracking and increasing overall durability. The costs can vary depending on the type and quality of fiber used.
Fiber Type | Estimated Cost per Pound |
Steel Fibers | $0.65 – $1.04 |
Glass Fibers | $0.78 – $1.30 |
Synthetic Fibers | $0.52 – $0.91 |
Steel fibers are widely used to enhance the tensile strength and durability of concrete. They help in minimizing cracking and improving load-bearing capabilities. The price may vary based on the type of steel, fiber length, and the manufacturer. This makes them a popular choice for high-stress applications such as industrial flooring and shotcrete.
Glass fibers are commonly utilized for their excellent tensile strength and corrosion resistance. They are ideal for applications requiring lightweight reinforcement, such as precast concrete and architectural elements. The cost can fluctuate based on fiber composition and the intended application, making them suitable for a variety of construction projects.
Synthetic fibers, including polypropylene and nylon, are increasingly popular for their cost-effectiveness and versatility. They help control plastic shrinkage cracking in concrete and improve impact resistance. This category of fibers is often chosen for residential concrete slabs and pavements, with pricing influenced by the fiber’s type and performance characteristics.
Geosynthetics are used to enhance soil and pavement stability, often in larger infrastructure projects. The costs depend on the type and application, with various materials available for different reinforcement needs.
Geosynthetic Type | Estimated Cost per Square Yard |
Geotextiles | $1.30 – $2.60 |
Geogrids | $3.25 – $5.20 |
Geocells | $1.95 – $3.90 |
Geotextiles are permeable fabrics used in geotechnical engineering to enhance soil stability and drainage. They can be made from woven or non-woven materials, serving functions such as filtration, separation, and reinforcement. The cost of geotextiles may vary based on the material type, weight, and intended application, making them suitable for projects like road construction, retaining walls, and erosion control.
Geogrids are high-strength polymer grids that provide structural reinforcement for soil and gravel layers. They are particularly effective in stabilizing subgrades and improving load distribution, which is essential for roadways, embankments, and retaining structures. The pricing of geogrids can depend on the grid configuration, material composition, and the specific engineering requirements of the project.
Geocells are three-dimensional structures made from polymer materials that create a cellular confinement system for soil and aggregates. They are used for applications like slope stabilization, channel protection, and load support on soft soils. The cost of geocells can vary based on the cell size, wall thickness, and manufacturer, providing versatility in design and application.
The primary factor influencing reinforcement costs is the type of materials used. Prices for steel and other reinforcement materials can fluctuate based on market demand, availability, and geopolitical factors. For instance, increased demand for construction materials due to economic growth can lead to higher prices. Additionally, different types of reinforcement materials—like fiber or geosynthetics—come with their own cost implications, often influenced by performance specifications and material quality.
Labor costs for installing reinforcement can vary based on regional wages, labor availability, and project complexity. In Florida, the average hourly wage for skilled labor in construction can range from $26 to $52, depending on experience and specialization. More complex installations requiring specialized skills can lead to higher labor costs. It’s important to factor in the total labor hours required for the installation of reinforcement, as this can significantly affect the overall project budget.
The size and complexity of the project significantly impact overall reinforcement costs. Larger projects often benefit from economies of scale, reducing per-unit costs. However, intricate designs or unique engineering requirements can lead to higher costs. For example, reinforcing a high-rise building will typically incur greater expenses than a single-story residential home due to the additional materials, labor, and engineering expertise required for safe and effective reinforcement.
In residential projects, reinforcement is typically utilized in foundations, driveways, and slabs. The average cost for reinforcement in a residential project can range from $1,950 to $6,500, depending on the project size, complexity, and material choices.
Project Element | Estimated Cost for Reinforcement |
Foundation | $1,560 – $2,600 |
Slab on Grade | $1,040 – $1,950 |
Driveway | $780 – $1,300 |
The foundation is a critical component of any construction project, providing stability and support for the entire structure. Reinforcement typically involves the use of steel rebar or mesh to enhance the strength and durability of the foundation. The cost can vary based on factors such as foundation type (e.g., slab, crawl space, or basement), soil conditions, and local building codes.
A slab on grade is a common foundation type for residential and commercial buildings, where the concrete slab is poured directly on the ground. Reinforcement is crucial for preventing cracking and ensuring the slab can support the weight of the structure above. The cost can vary depending on the thickness of the slab, the amount of reinforcement needed, and the overall design specifications.
Reinforcing a driveway is essential for ensuring it can withstand the weight of vehicles and resist cracking over time. The reinforcement typically includes steel mesh or rebar to improve structural integrity. Costs can fluctuate based on the driveway size, materials used (concrete, asphalt, etc.), and local labor rates.
Commercial buildings often require more extensive reinforcement to support larger structures and increased loads. Costs can range from $6,500 to $26,000, depending on the project scope and material selection.
Project Element | Estimated Cost for Reinforcement |
Structural Frames | $3,900 – $13,000 |
Parking Garages | $6,500 – $19,500 |
Retaining Walls | $2,600 – $10,400 |
Structural frames form the backbone of a building, supporting the weight of floors, roofs, and walls. Reinforcement typically involves the use of steel beams, columns, and bracing systems to enhance load-bearing capacity and resist lateral forces such as wind and seismic activity. The cost can vary significantly based on factors like building height, complexity of the design, material specifications, and local labor rates.
Reinforcement in parking garages is essential to accommodate the weight of vehicles and provide safety for users. This often involves the use of reinforced concrete slabs and beams designed to handle heavy loads and dynamic forces. The pricing can fluctuate based on the size of the garage, the number of levels, materials used, and specific design requirements tailored to local regulations and site conditions.
Retaining walls are crucial for preventing soil erosion and managing grade changes on construction sites. Reinforcement, which may include steel rebar or mesh, is necessary to provide stability and prevent structural failure due to lateral earth pressures. The estimated cost can vary based on wall height, material type (concrete, stone, etc.), and the complexity of the design and construction process.
Infrastructure projects such as bridges, highways, and tunnels require substantial reinforcement due to their size and load-bearing requirements. Costs can range significantly, often exceeding $130,000 for major projects.
Project Element | Estimated Cost for Reinforcement |
Bridges | $65,000 – $260,000 |
Tunnels | $130,000 – $650,000 |
Roadways | $39,000 – $130,000 |
Reinforcement in bridges is crucial for supporting loads and withstanding various environmental factors, such as wind, traffic, and seismic activity. This typically involves the use of high-strength steel rebar, prestressed concrete elements, and expansion joints. The cost varies significantly depending on factors such as bridge design (e.g., beam, arch, or cable-stayed), materials used, span length, and local regulations.
Reinforcement in tunnels is essential to ensure safety and structural stability against earth pressure, water infiltration, and seismic forces. Reinforcement methods may include rock bolts, steel mesh, and shotcrete, along with precast concrete segments. Costs can vary widely based on tunnel length, diameter, geological conditions, and construction methods employed, making it one of the more complex elements to budget for.
Reinforcement in roadways is vital for enhancing load-bearing capacity and preventing cracking and deformation under traffic loads. This generally involves the use of reinforced concrete or asphalt overlays, depending on the design and expected traffic volumes. The estimated cost for roadway reinforcement can fluctuate based on the road’s length, width, traffic patterns, and local material and labor costs.
Reinforcement costs can vary significantly based on location. Urban areas tend to have higher labor costs and material prices due to increased demand and living expenses. For instance, in Florida, labor costs in cities like Miami and Orlando may be higher than in rural areas, necessitating careful budgeting.
In Northern Florida, reinforcement costs may average around $0.65 to $3.25 per pound, while in Southern Florida, costs can range from $0.91 to $3.90 per pound, reflecting differences in labor rates, material availability, and regional demand.
Urban centers often experience higher costs due to competition and demand for skilled labor. Conversely, rural areas may provide more competitive pricing, making them a more cost-effective option for certain projects.
Accurate cost estimation for reinforcement is critical for effective project budgeting and management. Understanding these costs helps contractors and developers allocate resources efficiently, minimize waste, and avoid unexpected expenses during the construction process. This knowledge ensures that projects remain on schedule and within budget, contributing to the overall success of construction endeavors. Without precise cost estimation, projects risk running over budget, causing delays, and potentially compromising quality.
Understanding the costs associated with reinforcement is crucial for any construction project. Accurate cost estimation allows for better budget management, resource allocation, and project planning. By considering material types, labor rates, and project complexity, contractors and homeowners can make informed decisions that enhance the efficiency and success of their projects. With careful planning and monitoring of costs, it is possible to execute construction projects that not only meet structural integrity standards but also remain financially viable.
A reinforcement fee refers to the additional costs incurred when incorporating reinforcement materials, such as rebar or mesh, into a concrete structure. This fee covers the price of materials, labor for installation, and any necessary engineering assessments to ensure the structure's integrity. It is essential for projects where added strength and durability are required, such as in slabs, walls, or foundations.
The price of rebar reinforcement can vary based on factors like size, grade, and market conditions. Generally, rebar costs range from $0.25 to $1.00 per pound. When estimating the total cost for a project, consider additional expenses for labor and installation.
The cost of a ton of #4 rebar (which has a diameter of 1/2 inch) typically ranges from $700 to $900, depending on market fluctuations and location. Prices may vary due to factors such as local demand, availability, and specific supplier pricing. When planning a project, it’s advisable to request quotes from multiple suppliers to get the best price.
To calculate rebar cost, follow these steps:
Yes, using rebar in a 4-inch concrete slab is highly recommended, especially for structural applications or areas subject to heavy loads. Rebar provides additional tensile strength, reducing the risk of cracking and improving the overall durability of the slab. In residential applications, #3 or #4 rebar is commonly used to reinforce 4-inch slabs.
The cost to fabricate rebar can vary based on factors like complexity, labor rates, and location. On average, rebar fabrication costs range from $1 to $3 per linear foot. This fee includes cutting, bending, and preparing the rebar for installation. For larger projects, it’s essential to obtain quotes from multiple fabricators to ensure competitive pricing.
At Estimate Florida Consulting, we offer detailed cost estimates across all major trades, ensuring no part of your project is overlooked. From the foundation to the finishing touches, our trade-specific estimates provide you with a complete and accurate breakdown of costs for any type of construction project.
We take pride in delivering accurate, timely, and reliable estimates that help contractors and builders win more projects. Our clients consistently praise our attention to detail, fast turnaround times, and the positive impact our estimates have on their businesses.
Estimate Florida Consulting has helped us win more bids with their fast and accurate estimates. We trust them for every project!
Submit your project plans, blueprints, or relevant documents through our online form or via email.
We’ll review your project details and send you a quote based on your scope and requirements.
Confirm the details and finalize any adjustments to ensure the estimate meets your project needs.
Receive your detailed, trade-specific estimate within 1-2 business days, ready for your project execution.
561-530-2845
info@estimatorflorida.com
Address
5245 Wiles Rd Apt 3-102 St. Pete Beach, FL 33073 United States
561-530-2845
info@estimatorflorida.com
Address
5245 Wiles Rd Apt 3-102 St. Pete Beach, FL 33073 United States
All copyright © Reserved | Designed By V Marketing Media | Disclaimer