90% More Chances to Win Projects With Our Estimate!
- Multi-Family Building
- Hotel Building
- Hospital Building
- Warehouse Building
- School & University Building
- High-Rise Building
- Shopping Complex
- Data Center Building
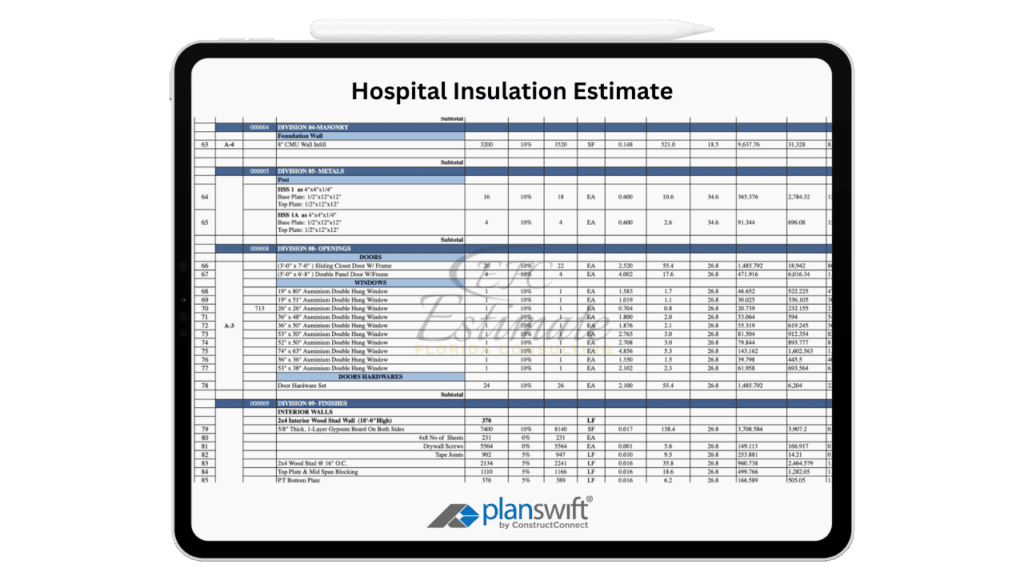
Insulation plays a vital role in hospital construction and renovation projects. Beyond just temperature regulation, it contributes to soundproofing, fire safety, and overall energy efficiency, all of which are essential in a healthcare environment. Hospitals, being large and complex structures, require different insulation types across various sections of the building. This comprehensive insulation cost estimator is designed to help general contractors, subcontractors, developers, facility managers, and material suppliers accurately estimate insulation costs for hospital projects.
To summarize the total estimated insulation costs for a 100,000 sq. ft. hospital project, we provide a comprehensive cost table below. This table includes material costs, labor, and additional costs, giving stakeholders a clear understanding of the financial commitment involved.
Cost Breakdown | Material Cost | Labor Cost | Additional Cost | Total Cost |
Fiberglass Batts | $168,000 | $252,000 | $120,000 | $540,000 |
$504,000 | $504,000 | $120,000 | $1,128,000 | |
Mineral Wool | $420,000 | $504,000 | $120,000 | $1,044,000 |
Rigid Foam Board | $336,000 | $504,000 | $120,000 | $960,000 |
This table provides a comprehensive view of the costs associated with each insulation type, allowing decision-makers to weigh the benefits against the investment required.
Several factors influence the cost of insulation in a hospital. Each of these factors can significantly affect the overall budget, so it’s essential to consider them in detail during the planning phase.
The size of the hospital has a direct impact on the cost of insulation. Larger hospitals, with more square footage to insulate, naturally require more materials and labor. Additionally, complex hospital designs with multiple wings, specialized rooms, and irregular architectural features can further increase costs. For example, insulating a 100,000 sq. ft. hospital will cost significantly more than a smaller, 50,000 sq. ft. facility due to the higher quantity of insulation materials and increased labor hours required.
Hospital Size (Sq. Ft.) | Estimated Insulation Cost |
50,000 sq. ft. | $100,800 – $201,600 |
100,000 sq. ft. | $201,600 – $403,200 |
200,000 sq. ft. | $403,200 – $806,400 |
The type of insulation material and its required thickness play significant roles in determining the overall project cost. Hospitals often require a combination of insulation types—thermal insulation for energy efficiency, acoustic insulation for noise reduction, and fire-resistant insulation for safety. Additionally, the thicker the insulation, the higher the cost, as thicker materials offer better thermal and acoustic performance but also demand more labor during installation.
Insulation Type | Cost Per Square Foot |
Fiberglass Batts | $1.18 – $3.02 |
Spray Foam | $3.36 – $6.72 |
Mineral Wool | $2.52 – $5.88 |
Rigid Foam Board | $1.68 – $4.20 |
Labor costs vary depending on the complexity of the installation, the type of insulation being used, and the standards required for healthcare environments. Hospitals require highly skilled labor to ensure insulation meets specific regulations, especially for areas that require sterile environments. For example, installing insulation in operating theaters or specialized labs requires precise methods that may increase labor costs compared to standard commercial buildings.
Labor Type | Cost Per Hour |
General Labor | $50.40 – $100.80 |
Skilled Labor (Specialists) | $100.80 – $201.60 |
To provide a clearer picture of the costs involved in hospital insulation, we present a detailed breakdown of material costs based on a 100,000 square foot hospital. Understanding these costs can help stakeholders make informed decisions regarding insulation materials.
Labor costs vary depending on the complexity of the installation, the type of insulation being used, and the standards required for healthcare environments. Hospitals require highly skilled labor to ensure insulation meets specific regulations, especially for areas that require sterile environments. For example, installing insulation in operating theaters or specialized labs requires precise methods that may increase labor costs compared to standard commercial buildings.
Labor Type | Cost Per Hour |
General Labor | $50.40 – $100.80 |
Skilled Labor (Specialists) | $100.80 – $201.60 |
Labor costs can vary significantly based on the complexity of the installation and the level of expertise required for each insulation type. Here’s a detailed breakdown of labor costs associated with installing insulation in a hospital of 100,000 square feet.
Labor Type | Cost Per Square Foot | Total Labor Cost (100,000 Sq. Ft.) |
General Labor | $2.52 | $252,000 |
Skilled Labor | $5.04 | $504,000 |
General labor encompasses basic installation tasks, while skilled labor includes specialized tradespeople who may be required for the more complex installation of spray foam or intricate soundproofing systems. Understanding the labor costs associated with each insulation type can help project managers allocate budgets appropriately and avoid unexpected expenses during the construction process.
Fiberglass batts are among the most widely used insulation materials in hospital construction due to their effectiveness in thermal control and affordability. This material consists of woven strands of glass fibers that trap air, creating a barrier against heat transfer. Fiberglass batts are available in pre-cut sizes, which simplifies installation and minimizes labor costs. Additionally, their non-combustible properties contribute to fire safety, making them an excellent choice for healthcare environments where safety is a primary concern. However, proper installation is crucial, as gaps or compression can significantly reduce their effectiveness. When installed correctly, fiberglass batts can provide an R-value of around 3.2 to 4.3 per inch, ensuring efficient thermal resistance.
Spray foam insulation has gained popularity in recent years due to its superior thermal performance and air-sealing capabilities. This material is applied as a liquid that expands and hardens, filling gaps and crevices, which helps to prevent air leaks and moisture infiltration. In a hospital setting, this can be particularly beneficial for maintaining temperature control in critical areas such as operating rooms and recovery wards. Additionally, spray foam can contribute to better indoor air quality by reducing the potential for mold growth, a common concern in humid environments like Florida. While spray foam tends to be more expensive than traditional insulation methods, its long-term benefits in energy savings and durability can offset the initial costs. Its high R-value, typically between 5.5 and 6.5 per inch, can significantly enhance a hospital’s energy efficiency.
Mineral wool, or rock wool, is another popular choice for hospital insulation due to its excellent fire resistance and soundproofing capabilities. Made from natural minerals, this material not only provides thermal insulation but also enhances the acoustic environment, which is crucial in a hospital setting where noise control can impact patient recovery. The material’s inherent fire-resistant properties can prevent the spread of flames, adding an extra layer of safety for vulnerable patients. Mineral wool can also absorb moisture without losing its insulating properties, making it suitable for Florida’s humid climate. Its R-value ranges from 3.0 to 4.5 per inch, ensuring effective thermal resistance.
Rigid foam board insulation offers a unique advantage due to its high insulating value relative to thickness, making it ideal for various applications in hospital construction. This type of insulation is particularly beneficial for exterior walls and roof applications, providing a continuous thermal barrier that minimizes thermal bridging. Rigid foam boards are lightweight, easy to handle, and resistant to moisture, which is especially important in regions prone to high humidity. Additionally, they can significantly reduce heating and cooling costs, contributing to the overall energy efficiency of the hospital. The R-value for rigid foam insulation typically ranges from 5.0 to 6.5 per inch, making it a highly effective choice for insulating large structures like hospitals.
As previously mentioned, additional costs for soundproofing and fire resistance are not just optional enhancements but rather essential investments in creating a functional and safe hospital environment. Properly soundproofing patient areas can lead to improved patient satisfaction and outcomes, making it a worthwhile investment. Furthermore, adhering to fire safety regulations protects both patients and staff, ensuring compliance with health codes and minimizing liability.
Quality soundproofing materials can significantly reduce noise disturbances between patient rooms and common areas. This reduction in noise levels is particularly important in sensitive areas like maternity wards and surgical recovery rooms. The estimated additional cost for soundproofing may vary widely depending on the design of the building and the specific needs of each area. In some cases, hospitals may choose to prioritize soundproofing in certain departments over others, affecting the overall budget and resource allocation.
Fire-resistant insulation is critical not just for compliance but also for the safety of patients, especially those who may be immobile or unable to evacuate quickly. The additional costs associated with fire resistance are often offset by the peace of mind it provides to patients and their families. Hospitals must work closely with fire safety engineers to determine the best materials and strategies to ensure compliance with local codes while maximizing safety.
Once installed, maintaining insulation is essential for sustaining its performance and ensuring that it continues to contribute effectively to energy efficiency and noise reduction. Regular inspections should be conducted, particularly after severe weather events, to identify any damage or wear that may compromise the insulation’s effectiveness.
Routine maintenance may involve checking for moisture infiltration, inspecting for pests, and ensuring that the insulation remains intact and in good condition. The estimated maintenance costs can vary widely but typically range from $5,000 to $15,000 annually, depending on the size of the facility and the type of insulation installed.
Additionally, it’s wise for hospital administrators to monitor energy consumption and HVAC performance regularly. Any fluctuations in energy usage may indicate insulation issues that need addressing. By proactively managing insulation maintenance, hospitals can extend the lifespan of their insulation systems and reduce long-term costs.
Installing insulation on your own can save you between $575 and $750 in labor costs. While many insulation projects are suitable for DIY enthusiasts, it’s wise to consult a professional for blown-in insulation in attics or roofs. These jobs often require specialized equipment and expertise to ensure adequate coverage.
Before getting started, you’ll need to measure the square footage of the area and purchase the appropriate insulation to achieve your desired R-value, along with the necessary installation tools. For most DIY projects, fiberglass rolls and batting or rigid foam boards are good options.
However, replacing insulation yourself is typically recommended only if you’re planning to open up your walls and replace the drywall simultaneously. If that’s not the case, it’s better to hire a local insulation company that can use insulation types better suited for retrofitting, such as spray foam or blown-in insulation.
Here’s a breakdown of common material costs for DIY insulation:
Additionally, if you don’t already own them, you may need to purchase the following tools:
Selecting the right insulation for a hospital project requires a comprehensive understanding of various factors, including material choices, labor costs, additional requirements like soundproofing and fire resistance, and ongoing maintenance expenses. Each insulation type presents unique benefits and considerations that must align with the hospital’s specific needs and budget constraints. By carefully evaluating these factors and employing effective cost estimation strategies, stakeholders can ensure a well-insulated facility that meets the operational demands of a healthcare environment.
A Hospital Insulation Cost Estimator is a tool designed to help stakeholders calculate the estimated costs associated with insulating a hospital building. It considers various factors, including material costs, labor expenses, and additional costs related to soundproofing and fire resistance.
Insulation is crucial in hospitals for several reasons:
Several factors influence the cost of insulation, including:
The following types of insulation are commonly used in hospital construction:
The cost breakdown for insulation in a hospital generally includes:
The estimated insulation costs for a 100,000 sq. ft. hospital can vary widely based on the type of insulation used. Here’s a summary of the costs for different insulation types:
Insulation Type | Material Cost | Labor Cost | Additional Cost | Total Cost |
Fiberglass Batts | $168,000 | $252,000 | $120,000 | $540,000 |
Spray Foam | $504,000 | $504,000 | $120,000 | $1,128,000 |
Mineral Wool | $420,000 | $504,000 | $120,000 | $1,044,000 |
Rigid Foam Board | $336,000 | $504,000 | $120,000 | $960,000 |
Labor costs for installing insulation can vary based on the complexity of the installation:
Yes, regular maintenance is essential to ensure the insulation remains effective. Estimated maintenance costs typically range from $5,000 to $15,000 annually, depending on the facility's size and insulation type.
At Estimate Florida Consulting, we offer detailed cost estimates across all major trades, ensuring no part of your project is overlooked. From the foundation to the finishing touches, our trade-specific estimates provide you with a complete and accurate breakdown of costs for any type of construction project.
We take pride in delivering accurate, timely, and reliable estimates that help contractors and builders win more projects. Our clients consistently praise our attention to detail, fast turnaround times, and the positive impact our estimates have on their businesses.
Estimate Florida Consulting has helped us win more bids with their fast and accurate estimates. We trust them for every project!
Submit your project plans, blueprints, or relevant documents through our online form or via email.
We’ll review your project details and send you a quote based on your scope and requirements.
Confirm the details and finalize any adjustments to ensure the estimate meets your project needs.
Receive your detailed, trade-specific estimate within 1-2 business days, ready for your project execution.
561-530-2845
info@estimatorflorida.com
Address
5245 Wiles Rd Apt 3-102 St. Pete Beach, FL 33073 United States
561-530-2845
info@estimatorflorida.com
Address
5245 Wiles Rd Apt 3-102 St. Pete Beach, FL 33073 United States
All copyright © Reserved | Designed By V Marketing Media | Disclaimer