90% More Chances to Win Projects With Our Estimate!
- Multi-Family Building
- Hotel Building
- Hospital Building
- Warehouse Building
- School & University Building
- High-Rise Building
- Shopping Complex
- Data Center Building
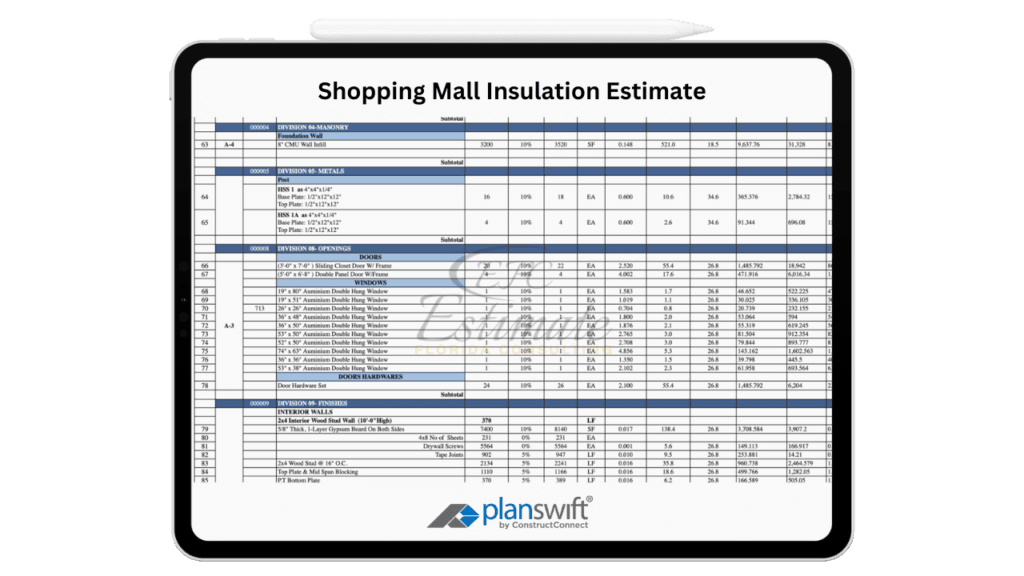
Insulating a shopping mall is a critical aspect of its construction and renovation, significantly impacting energy efficiency, comfort, and overall operating costs. Proper insulation helps maintain a stable indoor temperature, reduces energy consumption, and enhances the building’s overall sustainability. This guide provides a comprehensive cost estimator for insulation in shopping malls, focusing on various factors that influence pricing and offering detailed cost breakdowns to help general contractors, subcontractors, material suppliers, developers, and property owners make informed decisions. Understanding the nuances of insulation costs can lead to more effective budgeting and ultimately contribute to a better shopping environment.
Here’s a comprehensive summary of estimated insulation costs for a 100,000 sq. ft. shopping mall, including materials, labor, and additional costs:
Cost Breakdown | Fiberglass Batts | Spray Foam | Rigid Foam Board | Cellulose |
Materials Cost | $120,000 | $300,000 | $180,000 | $86,000 |
Labor Cost | $288,000 | $360,000 | $180,000 | $102,000 |
Air Sealing | $50,000 | $50,000 | $50,000 | $50,000 |
Moisture Barriers | $25,000 | $25,000 | $25,000 | $25,000 |
Ventilation Systems | $50,000 | $50,000 | $50,000 | $50,000 |
Several key factors influence the overall cost of insulation in shopping malls:
The total square footage of the shopping mall and its architectural design play a significant role in determining insulation costs. Larger malls with complex designs require more materials and labor, leading to higher costs. Architectural features such as atriums, large windows, and skylights can necessitate specialized insulation strategies, which may further increase expenses. The presence of unique design elements often means that insulation must be custom-fitted, adding to labor costs and installation time.
Mall Size (Sq. Ft.) | Estimated Insulation Cost |
50,000 sq. ft. | $60,000 – $120,000 |
100,000 sq. ft. | $120,000 – $240,000 |
250,000 sq. ft. | $300,000 – $600,000 |
The choice of insulation material also significantly affects costs. Different materials come with varying prices, R-values (thermal resistance), and installation complexities. For example, spray foam may offer superior insulation properties but at a higher price point compared to fiberglass batts. Selecting the right material involves weighing the upfront costs against potential long-term savings in energy bills.
Insulation Material | Cost Per Square Foot |
Fiberglass Batts | $0.60 – $1.80 |
$1.80 – $4.20 | |
Rigid Foam Board | $0.90 – $2.40 |
Cellulose | $0.72 – $1.44 |
Labor costs can vary based on the region and the complexity of the installation. In Florida, where the demand for skilled labor is high, prices may be higher than the national average. Furthermore, the experience level of the insulation contractor can impact labor costs. More experienced contractors often charge higher rates for their expertise, but their knowledge can lead to a more efficient installation and fewer issues down the line.
Labor Type | Cost Per Hour |
General Labor | $30 – $60 |
Specialist | $60 – $120 |
The choice of insulation type significantly influences the overall cost. Here are the most common insulation materials used in shopping malls, along with their characteristics and cost implications:
Fiberglass batts are one of the most common insulation materials. They are made from fine glass fibers and provide good thermal resistance at a relatively low cost. This type of insulation is easy to install, making it a popular choice for large projects like shopping malls. However, proper installation is crucial to avoid gaps and ensure optimal performance. The batts come in pre-cut sizes, which can be more convenient for certain applications but may lead to wastage if not sized correctly.
Component | Cost Range |
Fiberglass Batts | $0.60 – $1.80 per square foot |
Installation Labor | $0.90 – $2.40 per square foot |
Spray foam insulation is a premium option that provides excellent air sealing and high R-values. It expands on application, filling gaps and creating a strong barrier against air leakage. This type of insulation can enhance the structural integrity of the building, but it requires professional installation, which can drive up costs. Despite the higher initial investment, the long-term savings on energy bills often justify the expense.
Component | Cost Range |
Spray Foam Insulation | $1.80 – $4.20 per square foot |
Installation Labor | $1.20 – $3.00 per square foot |
Rigid foam board insulation is used for walls, roofs, and foundations. It is durable and provides high insulation values in a thinner profile, making it particularly effective for areas with limited space. This option also acts as a moisture barrier, protecting building materials from water damage. Installation can be straightforward, but custom cutting may be required for specific architectural features, adding to labor costs.
Component | Cost Range |
Rigid Foam Board | $0.90 – $2.40 per square foot |
Installation Labor | $0.90 – $1.80 per square foot |
Cellulose insulation is made from recycled paper and is an eco-friendly option. It is often blown into walls and ceilings, providing excellent coverage. While cellulose has a lower R-value than some other materials, its environmentally friendly nature and cost-effectiveness make it a popular choice for many projects. Moreover, cellulose can be treated with fire retardants, enhancing its safety profile.
Component | Cost Range |
Cellulose Insulation | $0.72 – $1.44 per square foot |
Installation Labor | $0.60 – $1.20 per square foot |
When estimating insulation costs, it’s important to break down the costs by various components, including materials, labor, and additional costs such as air sealing and moisture barriers.
The choice of insulation material affects the total material costs. Here’s a breakdown of common insulation materials and their costs for a 100,000 sq. ft. shopping mall, reflecting a 20% increase.
Material | Cost Per Square Foot | Total Cost for 100,000 Sq. Ft. |
Fiberglass Batts | $1.20 | $120,000 |
Spray Foam | $3.00 | $300,000 |
Rigid Foam Board | $1.80 | $180,000 |
Cellulose | $0.86 | $86,000 |
Labor costs can vary based on the complexity of the project. Here’s a breakdown based on the type of insulation and the total labor cost for a 100,000 sq. ft. shopping mall, reflecting the 20% increase in costs:
Insulation Type | Labor Cost Per Sq. Ft. | Total Labor Cost for 100,000 Sq. Ft. |
Fiberglass Batts | $2.88 | $288,000 |
Spray Foam | $3.60 | $360,000 |
Rigid Foam Board | $1.80 | $180,000 |
Cellulose | $1.02 | $102,000 |
Additional costs may include air sealing, moisture barriers, and ventilation considerations. Here’s a general breakdown of these costs for the project:
Additional Cost | Estimated Cost |
Air Sealing | $0.50 per sq. ft. ($50,000 total) |
Moisture Barriers | $0.25 per sq. ft. ($25,000 total) |
Ventilation Systems | $0.50 per sq. ft. ($50,000 total) |
Proper maintenance is essential to ensure the longevity and effectiveness of insulation systems. Regular inspections can identify any damage or settling that might affect insulation performance. The average maintenance costs for insulation in shopping malls typically range from 1% to 3% of the initial insulation investment annually. This maintenance might include re-sealing joints, replacing damaged sections, and checking for moisture issues that could compromise insulation performance.
Maintenance Cost | Estimated Annual Cost (1-3%) |
For a $500,000 insulation | $5,000 – $15,000 |
Investing in insulation has several advantages that can significantly affect a shopping mall’s operational efficiency and tenant satisfaction.
When estimating insulation costs, regional factors must be taken into account. Florida’s climate can lead to higher cooling demands, which can influence the type of insulation chosen. The warm and humid environment may necessitate more robust insulation solutions to mitigate heat gain and moisture infiltration. Furthermore, local building codes and energy efficiency requirements can affect insulation specifications and associated costs. Therefore, working with local contractors who understand these factors is crucial for accurate budgeting and effective insulation solutions.
Choosing the right contractor for insulation installation in Florida can greatly impact the overall quality and cost of the project. Here are some key considerations when hiring insulation contractors:
Understanding the costs associated with insulation in shopping malls is essential for contractors, developers, and property owners. By considering various factors such as mall size, insulation material, and labor costs, stakeholders can make informed decisions that align with their budget and energy efficiency goals. Insulation not only enhances the comfort and experience of shoppers but also contributes to the sustainability of the building. Ultimately, investing in quality insulation pays off in reduced energy costs, improved customer satisfaction, and a healthier environment for both shoppers and tenants.
The average cost to insulate a shopping mall can range significantly based on size, insulation type, and labor costs. For a 100,000 sq. ft. shopping mall, total insulation costs can range from approximately $120,000 to $240,000 depending on the materials used and installation complexity.
Key factors include:
Common insulation materials include:
Proper insulation significantly improves energy efficiency by reducing heating and cooling costs by 20-50%. This can lead to lower operational expenses and can make the shopping mall more appealing to tenants.
In addition to material and labor costs, consider:
To reduce costs:
Annual maintenance costs typically range from 1% to 3% of the initial insulation investment. For a $500,000 insulation system, maintenance might cost $5,000 to $15,000 per year, covering tasks like re-sealing joints and inspecting for moisture issues.
Insulation offers several advantages:
At Estimate Florida Consulting, we offer detailed cost estimates across all major trades, ensuring no part of your project is overlooked. From the foundation to the finishing touches, our trade-specific estimates provide you with a complete and accurate breakdown of costs for any type of construction project.
We take pride in delivering accurate, timely, and reliable estimates that help contractors and builders win more projects. Our clients consistently praise our attention to detail, fast turnaround times, and the positive impact our estimates have on their businesses.
Estimate Florida Consulting has helped us win more bids with their fast and accurate estimates. We trust them for every project!
Submit your project plans, blueprints, or relevant documents through our online form or via email.
We’ll review your project details and send you a quote based on your scope and requirements.
Confirm the details and finalize any adjustments to ensure the estimate meets your project needs.
Receive your detailed, trade-specific estimate within 1-2 business days, ready for your project execution.
561-530-2845
info@estimatorflorida.com
Address
5245 Wiles Rd Apt 3-102 St. Pete Beach, FL 33073 United States
561-530-2845
info@estimatorflorida.com
Address
5245 Wiles Rd Apt 3-102 St. Pete Beach, FL 33073 United States
All copyright © Reserved | Designed By V Marketing Media | Disclaimer