Spray Fireproofing Takeoffs
Spray fireproofing is a crucial component in protecting structural steel and other building elements from fire damage. It involves applying a fire-resistant material, typically a cementitious or fiber-based substance, to the surface of steel beams, columns, and decks to insulate them against high temperatures. Accurate spray fireproofing takeoffs are essential for ordering the correct materials, managing costs efficiently, and ensuring a smooth installation process. Estimate Florida Consulting provides expert estimate services for your spray fireproofing project, ensuring that it is completed with precision, efficiency, and strict adherence to safety standards.
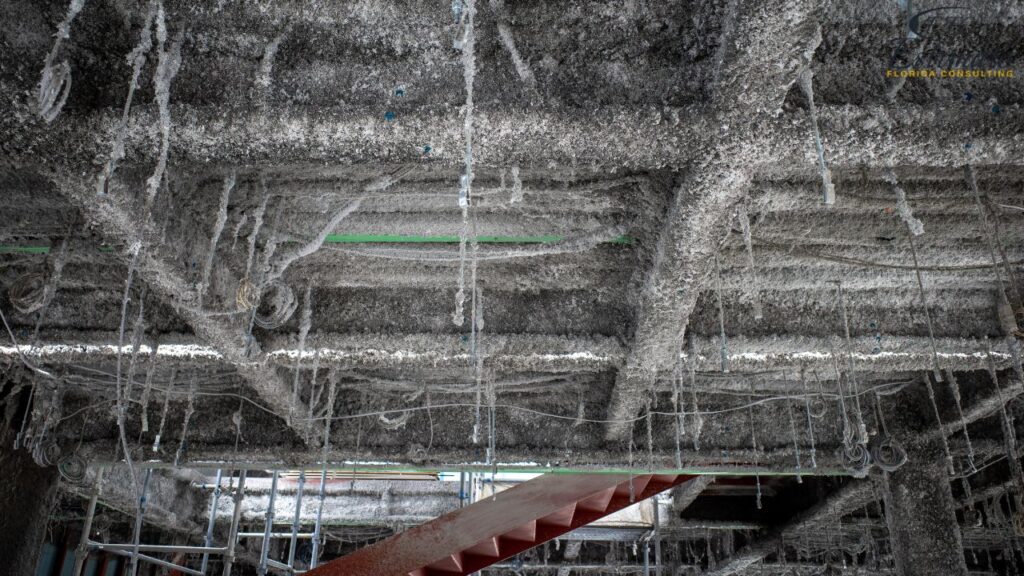
How Much Does Spray Fireproofing Cost?
The cost of spray fireproofing can vary depending on the type of material used, the thickness of the application, and the complexity of the project. On average, spray fireproofing costs range from $2.40 to $6.00 per square foot, which includes both materials and labor. Understanding these costs is crucial for effective budgeting and planning, ensuring that your project stays within financial constraints while meeting all necessary fire protection standards.
What is Spray Fireproofing?
Spray fireproofing involves applying a fire-resistant material, usually a cementitious or fibrous mixture, onto structural elements such as steel beams, columns, and decking. This protective layer helps maintain the structural integrity of the building during a fire, buying crucial time for evacuation and firefighting efforts. The fireproofing material is sprayed onto surfaces using specialized equipment, creating a uniform coating that adheres tightly to the substrate.
Common Types of Spray Fireproofing and Their Costs
Cementitious Fireproofing:
Cementitious spray fireproofing is one of the most commonly used materials for fireproofing structural steel. It offers excellent fire resistance and is relatively easy to apply. Costs for cementitious fireproofing typically range from $2.40 to $4.80 per square foot. This type of fireproofing is ideal for buildings where cost-effectiveness and reliable fire protection are key considerations.
Fibrous Fireproofing:
Fibrous spray fireproofing, often made from mineral wool or cellulose fibers, provides an alternative to cementitious materials with the added benefit of lighter weight and better acoustic properties. Costs for fibrous fireproofing generally range from $3.00 to $6.00 per square foot. Fibrous fireproofing is particularly beneficial in environments where sound absorption is important, such as in theaters, auditoriums, and offices.
Intumescent Fireproofing:
Intumescent coatings expand when exposed to high temperatures, creating an insulating layer that protects the structural steel. Although more expensive, intumescent fireproofing offers a smoother finish and can be applied in thinner layers. Costs for intumescent fireproofing typically range from $5.40 to $12.00 per square foot. Intumescent coatings are often chosen for projects where aesthetics are as important as fire protection, such as in exposed steel structures in architectural designs.
Spray Fireproofing Installation Costs
Here’s a breakdown of estimated spray fireproofing installation costs by area size:
Area Size (Square Feet) | Estimated Spray Fireproofing Installation Cost per Square Foot | Total Cost Range |
1,000 square feet | $2.40 – $6.00 | $2,400 – $6,000 |
5,000 square feet | $2.70 – $6.30 | $13,500 – $31,500 |
10,000 square feet | $3.00 – $6.60 | $30,000 – $66,000 |
20,000 square feet | $3.30 – $7.20 | $66,000 – $144,000 |
Detailed Cost Breakdown for Spray Fireproofing Installation
Here’s a detailed cost breakdown for various components involved in spray fireproofing installation:
Component | Estimated Cost per Square Foot | Total Cost Range |
Fireproofing Material | $1.20 – $3.60 | $1,200 – $72,000 (for 1,000 – 20,000 square feet) |
Installation Labor | $0.90 – $2.40 | $900 – $48,000 (for 1,000 – 20,000 square feet) |
Surface Preparation | $0.30 – $1.20 | $300 – $24,000 (for 1,000 – 20,000 square feet) |
Permits and Inspections | $240 – $1,200 (one-time fee) | $240 – $1,200 (one-time fee) |
Fireproofing Material:
The cost of fireproofing materials is a significant portion of the overall budget. The estimated cost per square foot for fireproofing materials ranges from $1.20 to $3.60. For a project covering between 1,000 and 20,000 square feet, the total cost for materials can vary from $1,200 to $72,000. This cost variation depends on the type of fireproofing material used, such as intumescent coatings, cementitious coatings, or fire-resistant boards. The choice of material affects not only the cost but also the level of fire protection provided and the ease of application, making it a critical decision in the planning process.
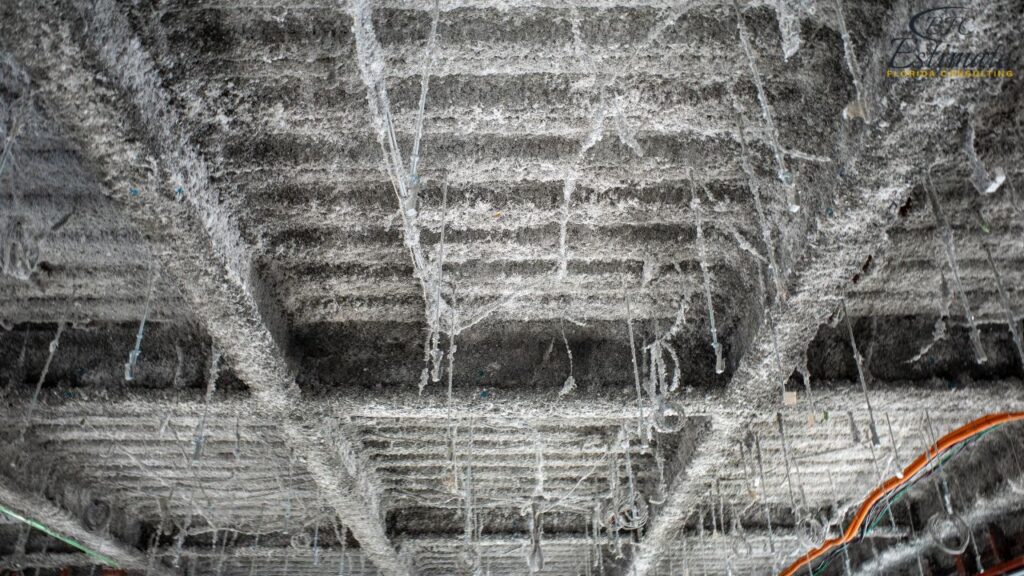
Installation Labor:
Labor costs for installing fireproofing materials are another essential factor in the overall budget. The estimated cost for installation labor ranges from $0.90 to $2.40 per square foot. For a project of 1,000 to 20,000 square feet, the total labor cost can range from $900 to $48,000. These costs are influenced by the complexity of the application process, the type of material used, and the working conditions on-site. Proper installation is crucial for ensuring that the fireproofing materials perform as intended, providing effective fire protection for the building or structure.
Surface Preparation:
Before applying fireproofing materials, the surfaces must be properly prepared, which involves cleaning, priming, and sometimes repairing the surface to ensure good adhesion of the fireproofing material. The cost of surface preparation is estimated to range from $0.30 to $1.20 per square foot. For a project spanning 1,000 to 20,000 square feet, the total cost for surface preparation can vary from $300 to $24,000. Surface preparation is a critical step that affects the durability and effectiveness of the fireproofing material, making it an essential part of the overall project cost.
Permits and Inspections:
Securing the necessary permits and passing inspections is essential for ensuring that the fireproofing project complies with local building codes and safety regulations. The cost for permits and inspections is typically a one-time fee, ranging from $240 to $1,200. This fee ensures that the project adheres to legal standards, reducing the risk of non-compliance issues that could lead to fines or the need for additional work. Although this cost is relatively small compared to the total project budget, it is a vital component that cannot be overlooked.
How to Use Our Spray Fireproofing Cost Estimator Services?
To get started with our spray fireproofing cost estimator services, simply contact Estimate Florida Consulting with your project details. Our team will work closely with you to gather all necessary information, including blueprints, material preferences, and any existing conditions that may affect the installation process. We will then provide a detailed and accurate cost estimate that covers all aspects of the spray fireproofing installation process, from material costs to labor and permits. This estimate serves as a valuable tool for planning and budgeting, ensuring that you have a clear understanding of the financial requirements for your project and can manage your resources effectively.
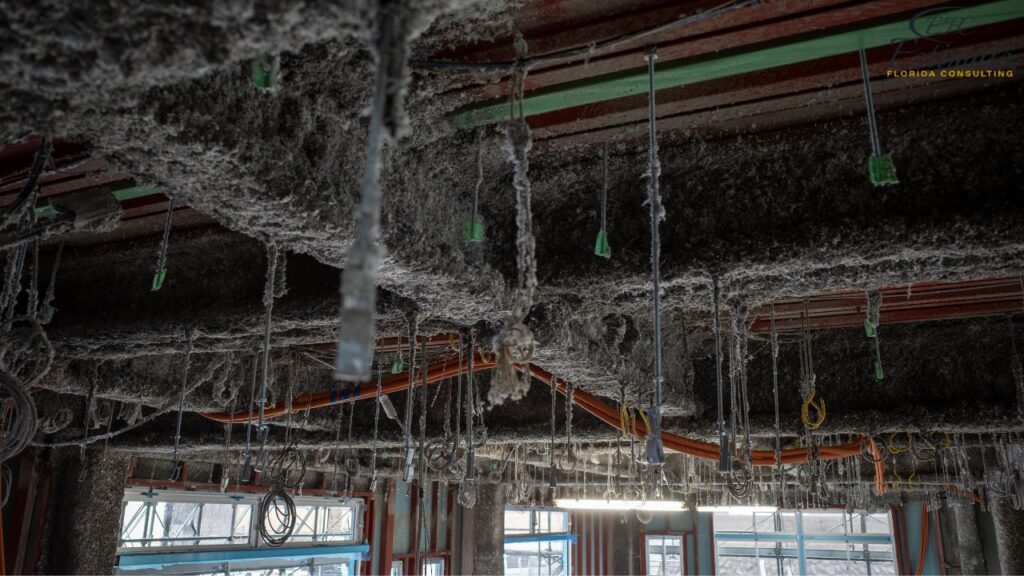
The Importance of Material Compatibility in Fireproofing
Choosing the right fireproofing material is not just about meeting the fire resistance rating; it’s also about ensuring compatibility with the substrate and environmental conditions of the project. Different materials have varying adhesion properties, moisture resistance, and durability under different conditions. For example, cementitious fireproofing may be highly effective on steel structures but could be prone to cracking in environments with significant temperature fluctuations or high moisture levels. Intumescent coatings, on the other hand, offer a more aesthetically pleasing finish but may require additional primers or sealants to perform effectively in high-humidity environments.
The Role of Building Codes and Standards in Fireproofing Takeoffs
Adhering to building codes and fire safety standards is a non-negotiable aspect of construction projects, particularly when it comes to fireproofing. These codes dictate the required fire resistance ratings for different structural components based on factors such as building occupancy, height, and type of construction. Standards like ASTM E119, UL 263, and the International Building Code (IBC) provide guidelines on the testing and performance requirements for fireproofing materials. During takeoffs, it’s essential to cross-reference project specifications with these codes to ensure compliance. Failure to meet the required standards can lead to project delays, costly rework, fines, or even legal implications. Estimators should be well-versed in the relevant codes and work closely with design teams and fireproofing specialists to ensure that all fireproofing measures are correctly specified and accounted for in the takeoff process.
Leveraging Technology for Improved Fireproofing Takeoffs
Incorporating technology into the fireproofing takeoff process can significantly improve accuracy and efficiency. Digital takeoff software allows estimators to quickly measure surface areas, calculate volumes, and adjust for complex geometries with greater precision than manual methods. These tools often include features that enable integration with Building Information Modeling (BIM) platforms, providing a more comprehensive view of the project and allowing for detailed, 3D visualization of structural elements. This level of detail helps identify potential issues early, such as hard-to-reach areas or irregular surfaces, and allows for adjustments to be made before the application begins. Additionally, some advanced software can automatically generate reports, track changes, and update material quantities in real-time as project specifications evolve. By leveraging these technologies, estimators can reduce the risk of errors, improve productivity, and provide more accurate and competitive bids.
Get Acquainted with Spray Fireproofing
Types of Spray Fireproofing: Selecting the Right Material
Choosing the right type of spray fireproofing material is crucial for balancing cost, effectiveness, and project-specific requirements. Estimate Florida Consulting provides estimate services that help you select the best material for your project based on your unique needs and goals. Here are some of the most common types of spray fireproofing materials:
Cementitious Fireproofing: Cost-Effective and Reliable
Cementitious fireproofing is widely used due to its affordability and effectiveness in protecting structural steel from fire. It is relatively easy to apply and provides excellent fire resistance, making it a cost-effective choice for a wide range of buildings, including commercial and industrial structures. Estimate Florida Consulting provides estimate services that include cementitious fireproofing as a reliable option for projects where budget constraints and fire safety are top priorities.
Fibrous Fireproofing: Lightweight and Acoustically Beneficial
Fibrous fireproofing materials, such as mineral wool or cellulose fibers, offer the advantage of being lighter in weight than cementitious options. This makes them easier to apply in certain situations, and their acoustic properties are beneficial in buildings where sound absorption is important. Estimate Florida Consulting provides estimate services that account for the dual benefits of fire protection and sound absorption offered by fibrous fireproofing, helping you achieve a safe and acoustically optimized environment.
Intumescent Fireproofing: Aesthetic and High-Performance
Intumescent fireproofing coatings expand when exposed to heat, creating a protective barrier that insulates structural steel from high temperatures. These coatings are more expensive than other types but provide a smoother, aesthetically pleasing finish and can be applied in thinner layers. Intumescent fireproofing is ideal for projects where the appearance of exposed steel is important, such as in architectural designs. Estimate Florida Consulting provides estimate services that include intumescent fireproofing as a premium option, ensuring that your project budget reflects the high-performance and aesthetic benefits of this material.
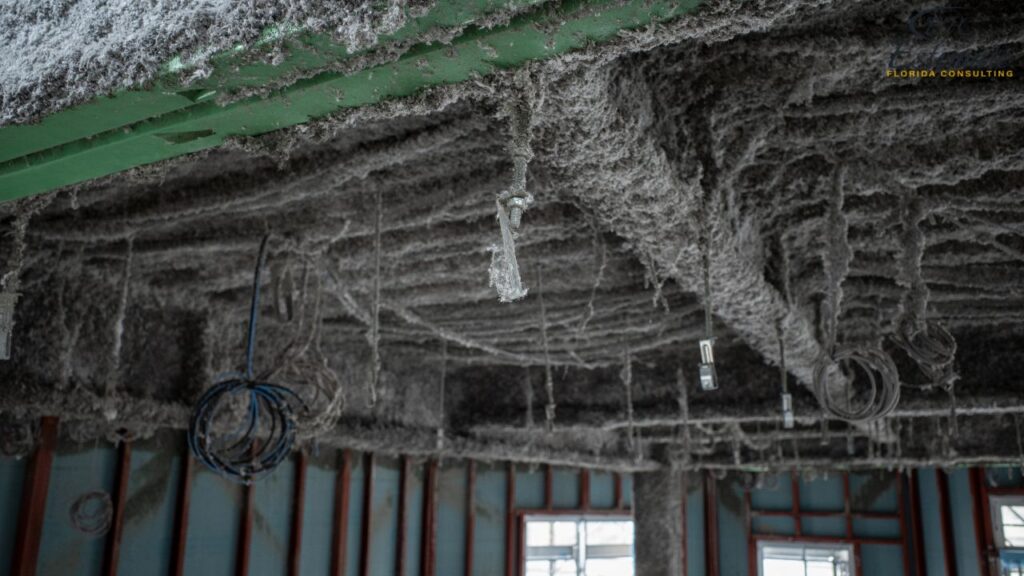
Common Challenges in Fireproofing Takeoffs
Accurate fireproofing takeoffs are essential for effective project management and cost estimation. However, several challenges can complicate the process. Below, we delve into some of the most common issues encountered during fireproofing takeoffs and provide detailed explanations of each.
Inaccurate Measurements
One of the most frequent challenges in fireproofing takeoffs is inaccurate measurements, which can arise from misreading plans or incorrectly calculating surface areas. The complexity of modern architectural designs, with their numerous beams, columns, and other structural elements, increases the likelihood of errors during measurement. Even small miscalculations can lead to significant discrepancies in material estimation, resulting in either material shortages or excess, both of which can be costly. Misinterpretation of scale, overlooking fine details in blueprints, or failing to adjust for changes in specifications can all contribute to measurement inaccuracies.
Overlooking Small Details
Another prevalent issue in fireproofing takeoffs is the overlooking of small structural components or hard-to-reach areas. These elements, although seemingly minor, can have a significant impact on the overall fireproofing requirements of a project. Small beams, intricate connections, irregularly shaped columns, and other less conspicuous parts are often missed in the initial review, leading to incomplete coverage estimates. This oversight not only affects the material quantities needed but can also compromise the fire resistance of the entire structure if not adequately addressed.
Adjusting for Irregular Surfaces
Irregular surfaces and complex geometries pose another significant challenge in fireproofing takeoffs. Structural elements with non-standard shapes, such as curved beams, tapered columns, or intricate joint configurations, require careful consideration because they often demand more material and longer application times than flat or simple surfaces. The intricacies of these shapes can lead to increased labor costs and additional waste due to the difficulty in achieving even application of the fireproofing material. Moreover, the need for precise application techniques to maintain uniform thickness and ensure adequate fire protection further complicates the estimation process. Misjudging the impact of these irregularities can lead to underestimation or overestimation of materials, both of which have financial implications.
Key Factors Influencing Spray Fireproofing Installation Costs
Several critical factors can influence the overall cost of a spray fireproofing installation project. Understanding these factors is key to effective planning and budgeting:
Material Selection and Cost Impact
The type of fireproofing material chosen will significantly impact the overall cost of the project. Higher-end materials such as intumescent coatings are more expensive but offer superior aesthetic and performance benefits, while more affordable options like cementitious fireproofing provide reliable protection at a lower cost.
Application Thickness
The required thickness of the fireproofing application, determined by building codes and fire safety standards, will also affect the cost. Thicker applications require more material and labor, increasing the overall expense. It is crucial to calculate the correct thickness to ensure compliance with fire safety regulations while managing costs effectively.
Installation Complexity
The complexity of the installation, including factors such as access to structural components, the need for surface preparation, and the type of application equipment required, can increase labor costs. Complex installations require more time and expertise, leading to higher labor costs. It’s important to factor in these complexities when estimating the costs of spray fireproofing installation, as underestimating these factors can lead to budget overruns and project delays.
The Importance of Accurate Spray Fireproofing Cost Estimation
Accurate cost estimation is critical for the success of any spray fireproofing project. It helps prevent unexpected expenses that could disrupt your budget and timeline, ensuring that your project stays on track. Misestimating the amount of material required or underestimating the complexity of the installation process can lead to significant cost overruns and delays, which can negatively impact the overall success of the project. A precise estimate allows you to manage your resources more effectively, ensuring that the right materials and labor are available when needed.
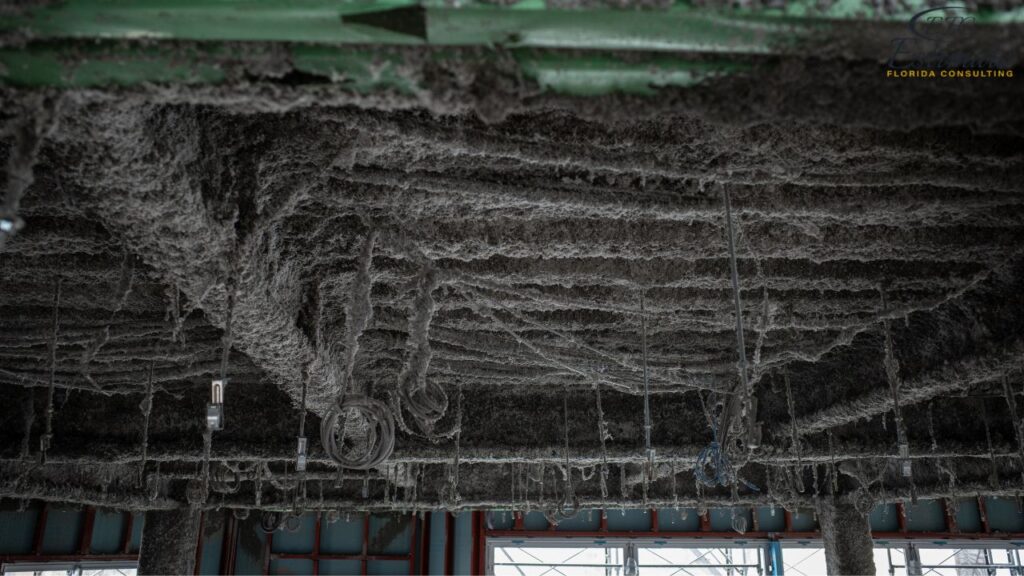
Estimate Florida Consulting provides accurate estimate services that deliver the precision needed to keep your project on budget and on schedule, ensuring that it meets the highest standards of fire safety and performance.
Spray Fireproofing Cost Calculator
To assist you in planning and budgeting your spray fireproofing project more accurately, Estimate Florida Consulting provides estimate services that include a comprehensive cost calculator. This tool allows you to input specific details about your project, such as the type of fireproofing material, the total area to be covered, and the thickness of the application. The calculator then provides an estimated cost range tailored to your project’s specific needs, offering you a clear understanding of what to expect financially. This cost calculator is an invaluable resource that helps ensure your project plans align with your budget, allowing you to allocate the necessary financial resources effectively.
The Benefits of Proper Spray Fireproofing Installation
Properly installed spray fireproofing systems offer several significant benefits that protect your building and ensure compliance with fire safety regulations:
Enhanced Fire Protection and Safety
Spray fireproofing provides critical protection for structural steel, preventing it from reaching failure temperatures during a fire. By slowing the spread of fire and maintaining the structural integrity of the building, spray fireproofing helps protect occupants and minimizes property damage. This enhanced fire protection is essential for meeting building codes and ensuring the safety of everyone who uses the building.
Compliance with Fire Safety Regulations
In many commercial and industrial settings, spray fireproofing is required to comply with fire safety regulations and standards. Properly installed fireproofing helps ensure that your building meets these requirements, reducing the risk of penalties and legal issues. Compliance with fire safety regulations not only protects occupants but also enhances the reputation of your business by demonstrating a commitment to safety and quality.
Download Template For Spray Fireproofing Project Breakdown
- Materials list updated to the zip code
- Fast delivery
- Data base of general contractors and sub-contractors
- Local estimators
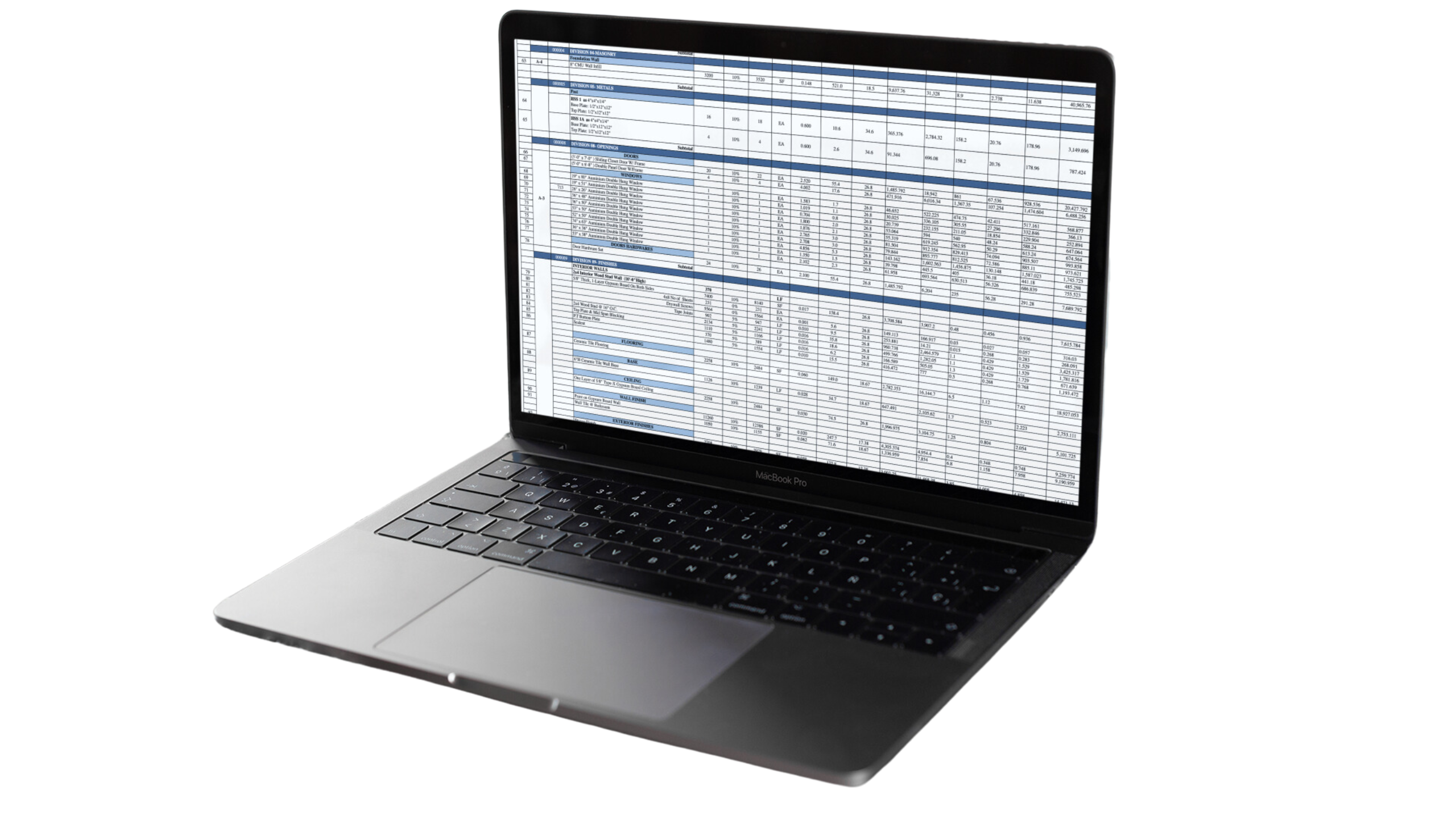
Longevity and Low Maintenance
Choosing durable fireproofing materials and ensuring proper installation can result in a fireproofing system that requires minimal maintenance and provides long-term protection. Regular inspections and maintenance can further extend the lifespan of the fireproofing, ensuring that your building remains well-protected for years to come. A well-maintained fireproofing system also contributes to the overall durability and value of the building, reducing the need for costly repairs or replacements.
Conclusion
Accurate cost estimation is the foundation of a successful spray fireproofing installation project. Estimate Florida Consulting provides comprehensive and precise estimate services that help you plan and execute your project with confidence. By understanding the cost components and potential variables, you can make informed decisions that align with your budget and project goals. Contact us today to get started with your spray fireproofing takeoff estimate, and take the first step toward a safer, more resilient building. With our expert guidance and detailed cost breakdowns, you can be assured that your project will be completed on time, within budget, and to the highest standards of safety and quality.
FAQs
Spray fireproofing involves applying a fire-resistant material, typically a cementitious or fiber-based substance, to structural steel and other building elements. This process insulates them against high temperatures, helping to protect the structure from fire damage. Estimate Florida Consulting provides expert takeoff services to ensure that your spray fireproofing project is executed efficiently and meets all safety standards.
The cost of spray fireproofing varies based on factors such as the type of material used, application thickness, and project complexity. On average, costs range from $2.40 to $6.00 per square foot, including both materials and labor. Understanding these costs is essential for effective budgeting and ensuring your project stays within financial constraints while meeting necessary fire protection standards.
- Cementitious Fireproofing: This is a widely used, cost-effective option that provides reliable fire protection. Costs typically range from $2.40 to $4.80 per square foot.
- Fibrous Fireproofing: Made from mineral wool or cellulose fibers, this material is lightweight and offers additional acoustic benefits. Costs generally range from $3.00 to $6.00 per square foot.
- Intumescent Fireproofing: This premium option expands when exposed to heat, creating an insulating layer. It offers a smoother finish and costs between $5.40 and $12.00 per square foot.
Accurate cost estimation includes the cost of materials, labor, surface preparation, and permits. Estimate Florida Consulting provides precise estimates that help you manage resources effectively, ensuring that your project stays on budget and schedule. We take into account all aspects of the project, including the specific materials and application requirements.
Installation costs vary depending on the size of the area being covered:
- 1,000 sq ft: $2,400 – $6,000
- 5,000 sq ft: $13,500 – $31,500
- 10,000 sq ft: $30,000 – $66,000
- 20,000 sq ft: $66,000 – $144,000 These ranges include materials, labor, and other essential costs, providing a clear understanding of the financial requirements for different project sizes.
Several factors can impact the overall cost:
- Material Selection: Higher-end materials like intumescent coatings are more expensive but offer superior performance.
- Application Thickness: Thicker applications require more material and labor, increasing costs.
- Installation Complexity: The difficulty of accessing structural components and the need for surface preparation can raise labor costs. Estimate Florida Consulting considers these factors in their estimates, ensuring your project is accurately scoped and budgeted.
To start, contact Estimate Florida Consulting with your project details, including blueprints and material preferences. Our team will provide a detailed and accurate cost estimate covering all aspects of the installation process, from materials to labor and permits, ensuring that you have a clear financial understanding before beginning your project.
Google Reviews
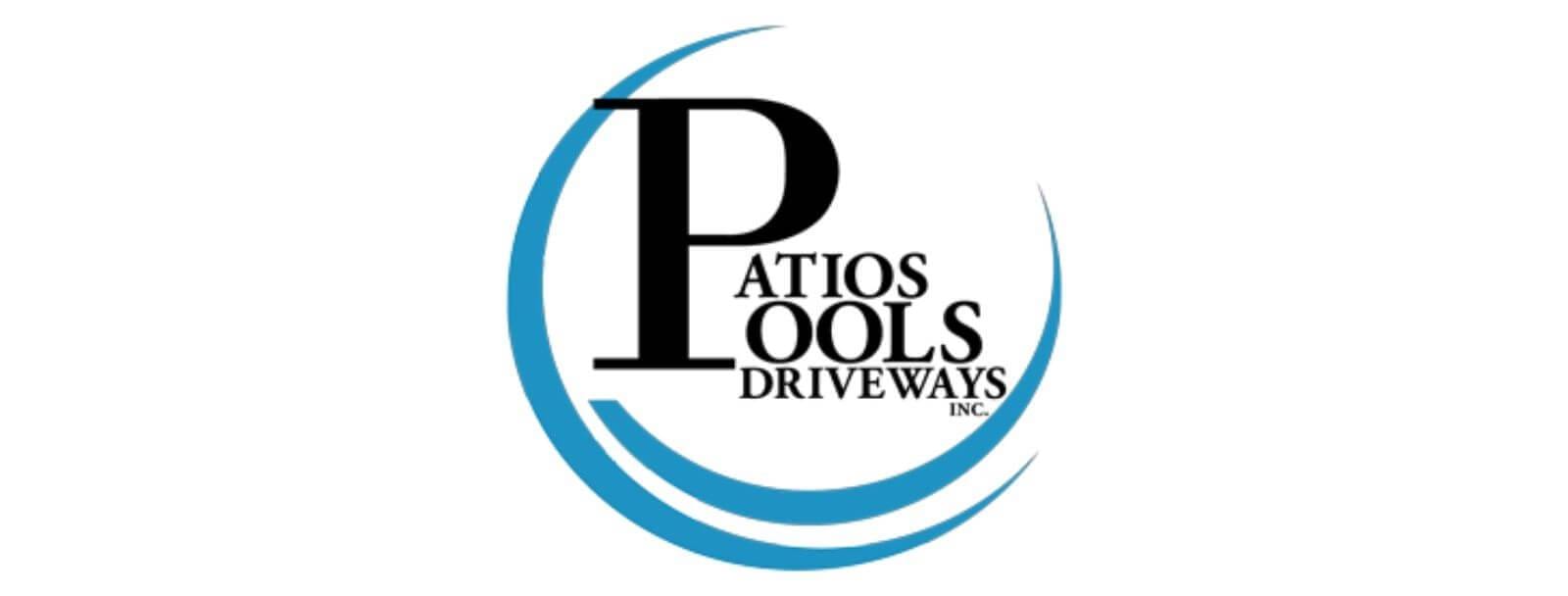
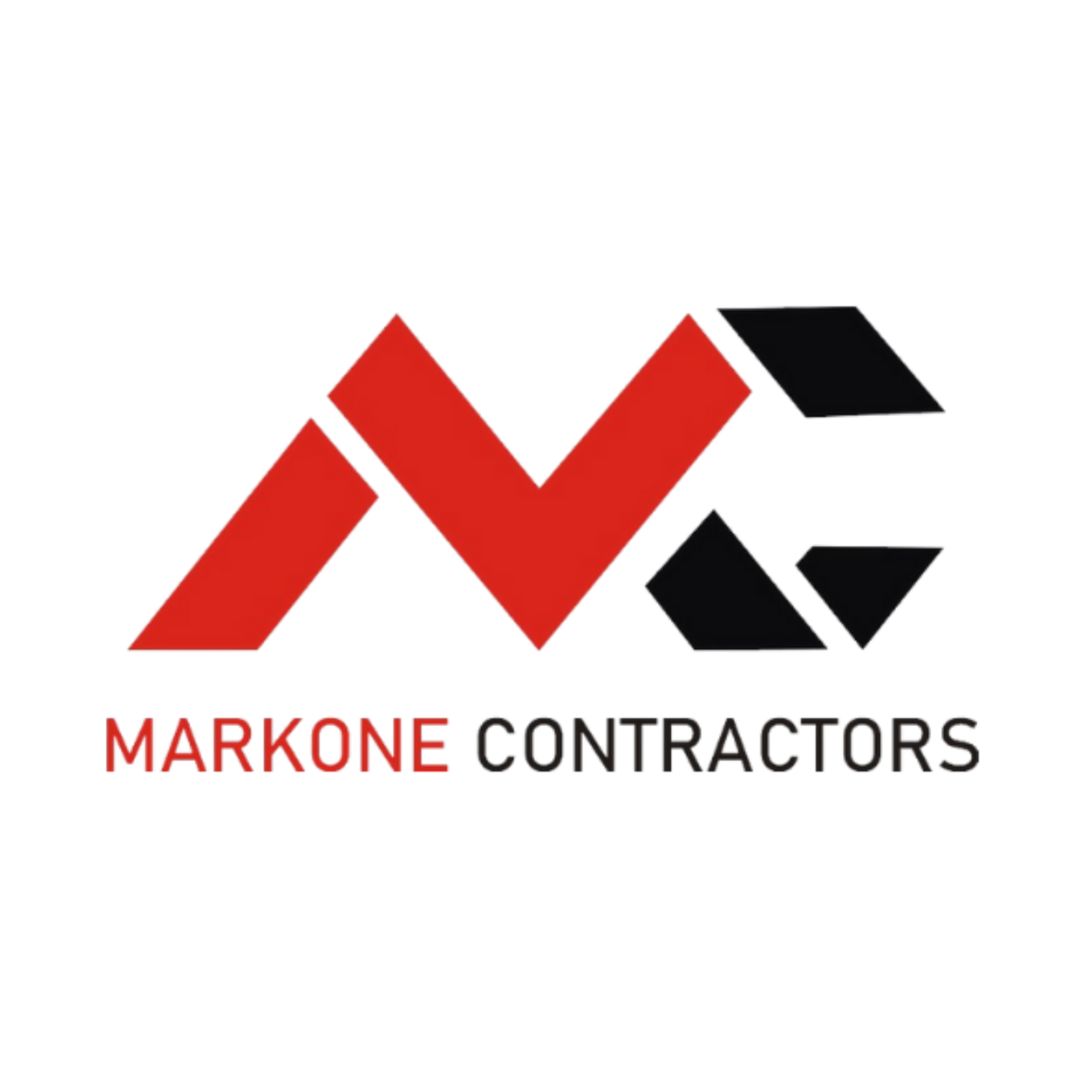

Process To Get Spray Fireproofing Cost Estimate Report
Here I am going to share some steps to get spray fireproofing cost estimate report.
-
You need to send your plan to us.
You can send us your plan on info@estimatorflorida.com
-
You receive a quote for your project.
Before starting your project, we send you a quote for your service. That quote will have detailed information about your project. Here you will get information about the size, difficulty, complexity and bid date when determining pricing.
-
Get Estimate Report
Our team will takeoff and estimate your project. When we deliver you’ll receive a PDF and an Excel file of your estimate. We can also offer construction lead generation services for the jobs you’d like to pursue further.