Fiber Insulation Takeoff Services
Fiber insulation is an essential component in modern construction, offering critical benefits such as thermal protection, soundproofing, and enhanced energy efficiency for both residential and commercial buildings. Ensuring precise and accurate fiber insulation takeoffs is crucial for contractors and builders. Accurate takeoffs allow for a more detailed estimation of materials, labor, and overall project costs, which is vital for maintaining budgets, minimizing waste, and ensuring that projects are completed on time and within the highest standards of quality. Estimate Florida Consulting provides estimate services that are customized to meet the unique needs of your project, delivering highly accurate takeoffs that help you achieve the best possible outcomes while staying well within your budget.
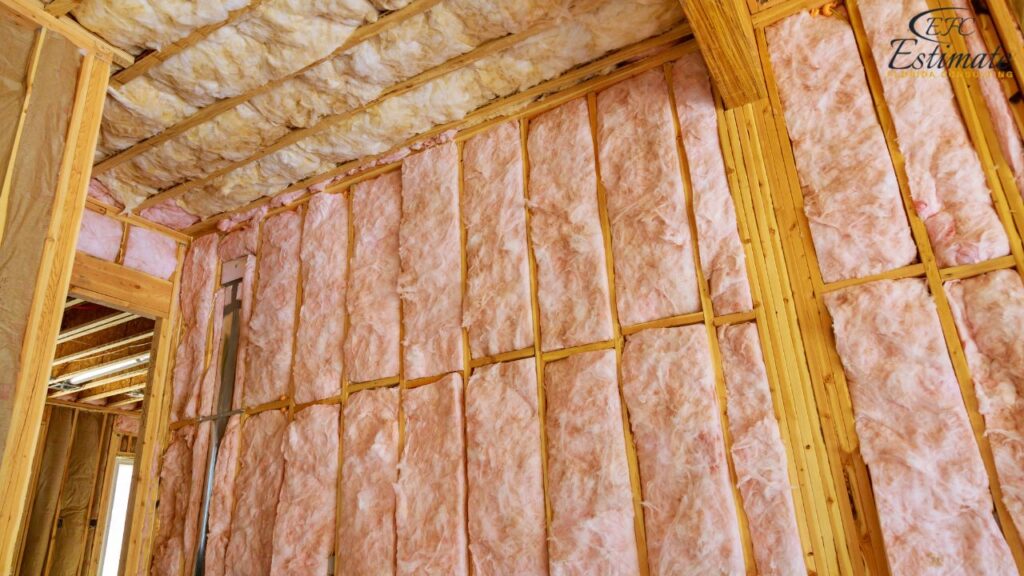
How Much Does Fiber Insulation Cost?
The cost of fiber insulation can vary widely depending on several factors, including the type of fiber material used, the required thickness, and the overall size of the area to be insulated. On average, fiber insulation costs range from $0.91 to $2.60 per square foot for materials alone, with labor costs adding an additional $0.78 to $1.95 per square foot. These costs can fluctuate based on the specific needs of the project, such as whether the insulation is being installed in walls, ceilings, or attics. It’s also important to consider the impact of local labor rates and the complexity of the installation, which can further influence costs.
Fiber Insulation Costs by Area Size
The size of the area requiring insulation is one of the most significant factors in determining the overall cost of the project. Larger areas naturally require more materials and labor, which can increase costs. Estimate Florida Consulting provides estimate services that offer detailed cost breakdowns based on the size of the area to be insulated.
Here’s a breakdown of estimated fiber insulation costs by area size:
Area Size (Square Feet) | Estimated Fiber Insulation Cost per Square Foot | Total Fiber Insulation Cost Range |
1,000 sq ft | $1.69 – $4.55 | $1,690 – $4,550 |
2,000 sq ft | $1.69 – $4.55 | $3,380 – $9,100 |
3,000 sq ft | $1.69 – $4.55 | $5,070 – $13,650 |
5,000 sq ft | $1.69 – $4.55 | $8,450 – $22,750 |
Fiber Insulation Cost Calculator for Accurate Budgeting
Planning your fiber insulation project requires careful budgeting, and to assist with this, Estimate Florida Consulting provides estimate services that include a comprehensive fiber insulation cost calculator. This tool enables you to input specific details about your project, such as the type of fiber insulation, the size of the area to be insulated, and the desired R-value (which measures the insulation’s effectiveness). The calculator then provides an estimated cost range, giving you a clear understanding of what to expect in terms of expenses. This tool is invaluable for aligning your project plans with your budget, ensuring that you have the necessary financial resources to complete the project without compromising on quality. By using our cost calculator, you can prevent potential cost overruns and ensure that your project remains both financially and structurally sound, while also maximizing energy efficiency.
Factors Influencing Fiber Insulation Costs
Several factors can significantly influence the overall cost of a fiber insulation project. Understanding these factors is essential for effective planning and budgeting:
Type of Fiber Insulation
The type of fiber insulation you select—whether it’s fiberglass, mineral wool, or cellulose—greatly impacts the project’s cost. Fiberglass is generally the most cost-effective option, making it popular for budget-conscious projects. However, mineral wool, though more expensive, offers enhanced fire resistance and superior soundproofing capabilities, making it a worthwhile investment for certain applications. Cellulose insulation, known for its eco-friendliness and excellent thermal properties, is another viable option but may come at a higher price point. Each type of insulation has its unique benefits and associated costs, so choosing the right one depends on your specific needs and budget.
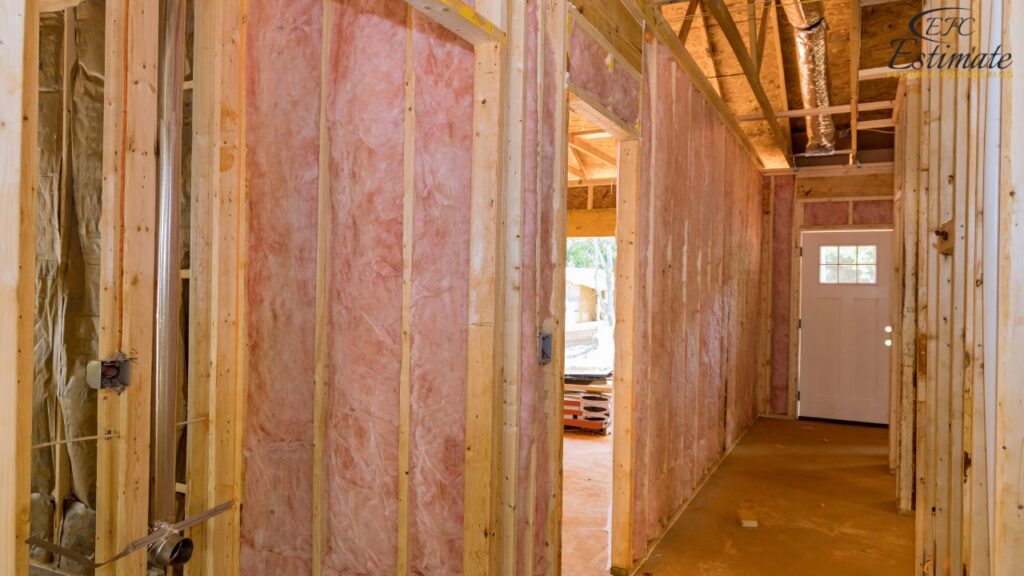
Thickness and R-Value
The thickness of the insulation and its R-value, which measures its thermal resistance, are critical factors that affect overall costs. Higher R-values provide better insulation and are often required for regions with extreme temperatures. Achieving a higher R-value typically requires thicker layers of insulation, which increases both material and labor costs. While the upfront costs may be higher, opting for insulation with a greater R-value can lead to significant energy savings over time, making it a cost-effective choice in the long term. The decision to invest in higher R-value insulation should consider both immediate budget constraints and potential future savings.
Installation Area
The specific area where insulation is being installed, such as walls, attics, or ceilings, can significantly influence the project’s cost. Some areas, like attics, can be more challenging to insulate due to difficult access, cramped spaces, or existing structures that complicate the installation process. These factors may require additional labor, specialized tools, or equipment, all of which can increase the overall cost. For instance, insulating an attic often involves navigating tight, awkward spaces, leading to higher labor costs compared to insulating more accessible areas like open walls. Understanding the complexities of the installation area is essential for accurate budgeting.
Labor and Installation Method
The method used to install the insulation, as well as the amount of labor required, are substantial factors in determining the final cost of the project. Labor-intensive methods, such as blown-in insulation for attics or densely packed wall insulation, typically involve more time and effort, leading to higher costs compared to standard batt insulation installations. The experience and skill level of the labor force also play a role; highly skilled installers may charge more, but their expertise can ensure a higher quality installation, reducing the likelihood of issues such as gaps or uneven coverage. Additionally, the chosen installation method may require specific tools or equipment, further influencing the cost. Investing in skilled labor and appropriate installation techniques can enhance the effectiveness and longevity of the insulation, providing better value over time.
Detailed Cost Breakdown for Fiber Insulation Projects
To help you understand the potential costs involved in your fiber insulation project, here’s a detailed cost breakdown based on different components of the process:
Fiber Insulation Component | Estimated Cost per Square Foot | Total Cost Range |
Material Costs | $0.91 – $2.60 | $910 – $2,600 (for 1,000 sq ft) |
Labor Costs | $0.78 – $1.95 | $780 – $1,950 (for 1,000 sq ft) |
Equipment and Setup | $0.26 – $0.65 | $260 – $650 (for 1,000 sq ft) |
Permits and Inspections | $260 – $650 | $260 – $650 (one-time fee) |
Material Costs
The material costs for fiber insulation typically range from $0.91 to $2.60 per square foot. For a standard 1,000 square foot area, this translates to a total cost range of $910 to $2,600. The wide range in material costs depends on the type of fiber insulation chosen, such as fiberglass, mineral wool, or cellulose. Each type offers different levels of thermal efficiency, fire resistance, and soundproofing capabilities, which influence the price. Higher-end materials, like mineral wool, are more expensive but provide superior insulation properties, making them a worthwhile investment for projects requiring high performance.
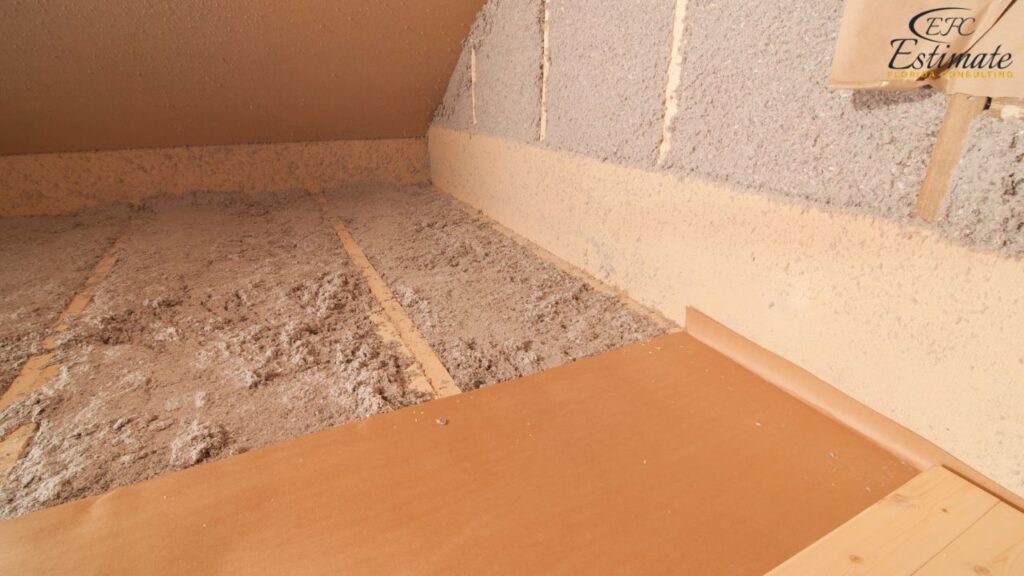
Labor Costs
Labor costs for installing fiber insulation typically fall between $0.78 and $1.95 per square foot, resulting in a total cost of $780 to $1,950 for a 1,000 square foot area. These costs can vary based on the complexity of the installation, the experience level of the workers, and the specific area being insulated. For instance, installing insulation in attics or tight spaces may require more time and specialized skills, leading to higher labor costs. Efficient and skilled labor not only ensures a high-quality installation but also helps in minimizing material waste, contributing to overall cost-effectiveness.
Equipment and Setup
The cost for equipment and setup is typically between $0.26 and $0.65 per square foot, or $260 to $650 for a 1,000 square foot project. This includes the tools and machinery required to install the insulation, such as blowers for loose-fill insulation or cutting tools for batt insulation. Depending on the installation method, different equipment may be needed, and more complex setups may require additional or specialized tools. These costs ensure that the installation is done efficiently and correctly, which is crucial for the long-term performance of the insulation.
Permits and Inspections
Permits and inspections are a necessary part of most insulation projects, with costs ranging from $260 to $650. This is typically a one-time fee that covers the cost of obtaining the necessary permits to comply with local building codes and the inspection required to ensure that the work meets all safety and quality standards. Failing to secure the proper permits and inspections can lead to fines or the need to redo work, so it’s important to factor these costs into your budget from the outset.
How to Use Our Fiber Insulation Cost Estimator Services?
To get started with our fiber insulation cost estimator services, simply contact Estimate Florida Consulting with your project details. Our team will work closely with you to gather all necessary information, including blueprints, material preferences, and any existing conditions that may affect the insulation process. We will then provide a detailed and accurate cost estimate that covers all aspects of the fiber insulation process, from material costs to labor and permits. This estimate serves as a valuable tool for planning and budgeting, ensuring you have a clear understanding of all potential costs and are prepared to manage them effectively. Estimate Florida Consulting provides estimate services that deliver the precision and reliability you need for successful project management, allowing you to focus on executing the project to the highest standards.
Advantages of Accurate Fiber Insulation Cost Estimation
There are several advantages to using our fiber insulation cost estimator services:
Precise Budgeting
By providing an accurate estimate, you can plan your budget more effectively, ensuring all necessary resources are available without overspending. This helps prevent budget overruns that could delay the project or compromise its quality. Precise budgeting also allows you to allocate funds more efficiently, ensuring that every dollar is used effectively to achieve the best possible results.
Efficient Resource Allocation
Accurate cost estimates allow for better resource planning, ensuring materials are ordered in the correct quantities and labor is scheduled efficiently. This minimizes waste and ensures the project progresses smoothly, with all necessary components available when needed. Proper resource allocation is critical to maintaining the project’s timeline and ensuring that all phases of the project are completed without unnecessary delays.
Reduced Waste
Estimating the exact amount of materials needed helps minimize waste, reducing costs and contributing to a more sustainable project. This approach not only saves money but also aligns with green building practices, which are increasingly important in today’s construction industry. By reducing waste, you not only lower costs but also contribute to a more environmentally friendly building process, which can be a significant selling point for eco-conscious clients.
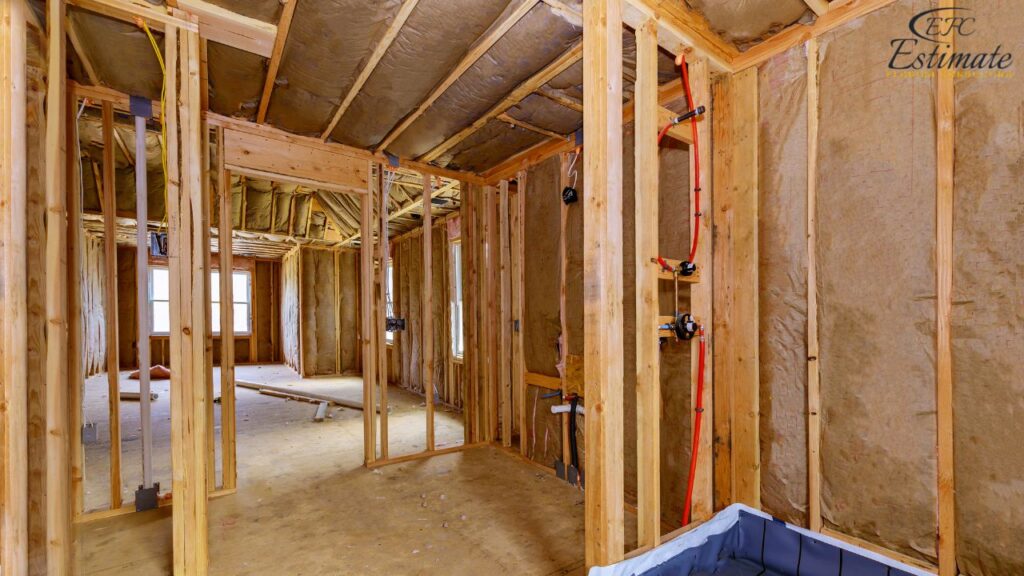
Improved Project Management
With a clear understanding of the costs involved, project managers can make informed decisions, avoiding delays and ensuring the project stays on schedule. This level of control is crucial in maintaining project momentum and ensuring deadlines are met. Effective project management ensures that all aspects of the project are coordinated smoothly, leading to a higher-quality final product and greater client satisfaction.
Additional Considerations for Fiber Insulation Projects
When planning a fiber insulation project, there are additional considerations that can impact both the cost and the success of the project:
Long-Term Energy Savings
Investing in high-quality fiber insulation can lead to significant long-term energy savings. While the initial cost may be higher, the reduction in energy bills over time can offset this expense. Our estimates take into account the potential energy savings, helping you make an informed decision about your insulation investment. High-quality insulation not only provides immediate benefits in terms of comfort and energy efficiency but also contributes to the long-term value and sustainability of the building.
Integration with Other Building Systems
Fiber insulation often needs to work in conjunction with other building systems, such as HVAC and ventilation. Ensuring that the insulation integrates seamlessly with these systems is critical for overall building performance. Our estimates include recommendations for integrating insulation with other systems to enhance energy efficiency and indoor comfort. Proper integration ensures that all building systems work together harmoniously, maximizing the overall effectiveness of the insulation and improving the building’s overall performance.
Compliance with Local Building Codes
Compliance with local building codes and environmental regulations is essential for any construction project. Our fiber insulation estimates include a review of relevant codes to ensure that your project meets all legal requirements, reducing the risk of fines or delays. This ensures that your project proceeds smoothly through the permitting process and that the final construction is compliant with all regulations. Adhering to building codes not only protects you from legal issues but also ensures that the insulation project meets the highest standards of safety and quality.
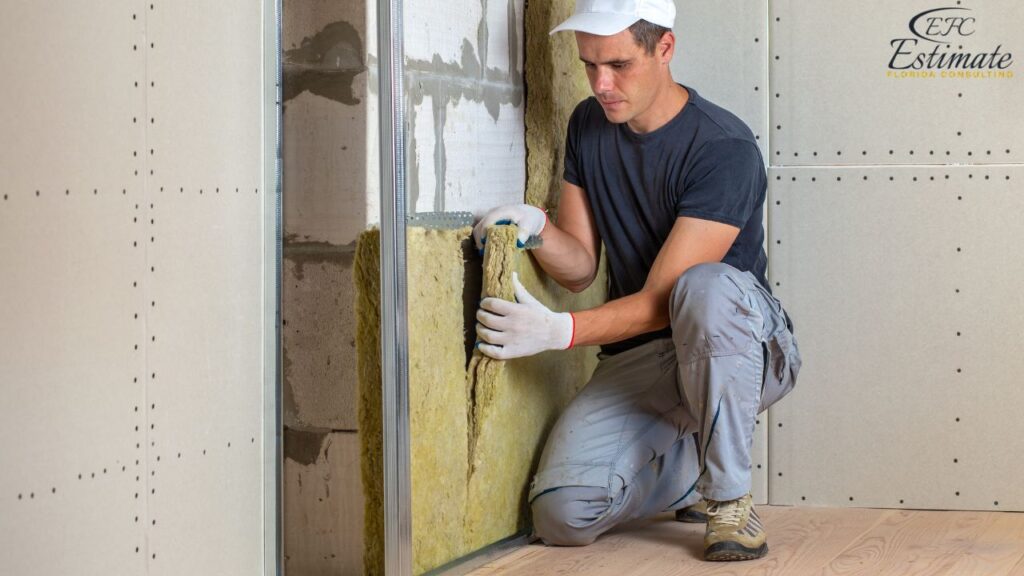
Why Choose Estimate Florida Consulting for Your Fiber Insulation Takeoffs?
Choosing Estimate Florida Consulting for your fiber insulation takeoffs ensures that you receive accurate, detailed estimates tailored to your project’s specific needs. Our team’s extensive experience in the construction industry, combined with our commitment to quality and customer satisfaction, makes us the ideal partner for your project. We take pride in our attention to detail and our ability to deliver precise estimates that help you manage costs, minimize waste, and achieve successful project outcomes. By partnering with us, you can be confident that your fiber insulation project is in capable hands, ensuring a durable and cost-effective solution. Estimate Florida Consulting provides estimate services that go beyond just numbers—we provide the expertise and support you need to bring your project to successful completion. Our dedication to accuracy and customer satisfaction ensures that your project is completed to the highest standards, delivering long-term benefits in terms of energy efficiency, comfort, and cost savings.
Download Template For Fiber Insulation Project Breakdown
- Materials list updated to the zip code
- Fast delivery
- Data base of general contractors and sub-contractors
- Local estimators
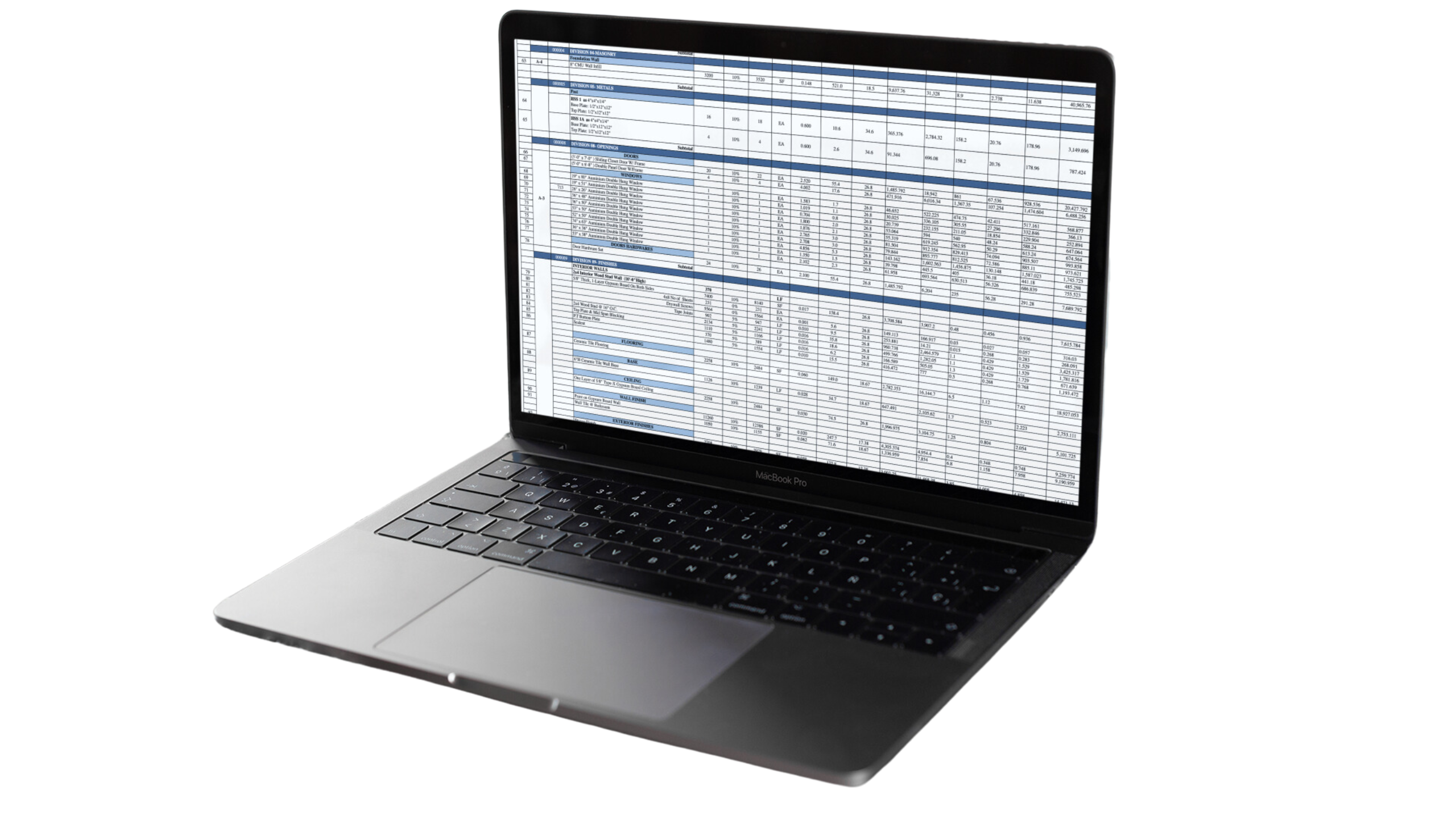
Conclusion
Accurate cost estimation is the foundation of a successful fiber insulation project. Estimate Florida Consulting provides comprehensive and precise estimate services that help you plan and execute your project with confidence. Our detailed estimates ensure that every aspect of your fiber insulation process is properly accounted for, leading to a successful and cost-effective project. Contact us today to get started with your fiber insulation takeoff estimate and take the first step toward a well-insulated and energy-efficient building. With our expert guidance, you can move forward with confidence, knowing that your project is well-planned, financially secure, and executed to the highest standards. Our commitment to excellence and precision ensures that your insulation project not only meets but exceeds your expectations, delivering lasting value and comfort for years to come.
FAQs
Fiber insulation is a crucial material used in construction to provide thermal protection, soundproofing, and energy efficiency in both residential and commercial buildings. It is made from various materials, including fiberglass, mineral wool, and cellulose, each offering distinct benefits in terms of insulation performance and cost-effectiveness.
The cost of fiber insulation can vary based on factors like the type of material used, the required thickness, and the area to be insulated. On average, fiber insulation costs range from $0.91 to $2.60 per square foot for materials, with labor costs adding an additional $0.78 to $1.95 per square foot. The total cost will depend on the specific requirements of the project, such as the area being insulated (walls, ceilings, attics) and local labor rates.
The size of the area requiring insulation significantly impacts the overall project cost. Larger areas require more materials and labor, which increases the total expense. For example:
- 1,000 sq ft: $1,690 – $4,550
- 2,000 sq ft: $3,380 – $9,100
- 5,000 sq ft: $8,450 – $22,750
Estimate Florida Consulting provides detailed cost breakdowns for different area sizes, helping you budget accurately.
Several factors can impact the overall cost of a fiber insulation project:
- Type of Fiber Insulation: The choice between fiberglass, mineral wool, and cellulose will affect costs, with fiberglass generally being the most cost-effective.
- Thickness and R-Value: Higher R-values (which measure thermal resistance) typically require thicker insulation, increasing material and labor costs.
- Installation Area: The complexity of insulating attics, walls, or ceilings can affect costs, with more challenging areas often requiring more labor and specialized equipment.
- Labor and Installation Method: Labor-intensive methods and skilled labor can increase costs but often result in higher quality installations.
Damp Proofing costs are typically broken down into several components, including:
- Surface Area Preparation: $1.00 – $2.50 per square foot.
- Asphalt-Based Coatings: $0.50 – $1.50 per square foot.
- Cementitious Coatings: $1.50 – $3.50 per square foot.
- Liquid Membranes: $2.00 – $4.50 per square foot.
- Sheet Membranes: $3.00 – $6.00 per square foot.
- Labor Costs: $2.50 – $5.00 per square foot.
- Permits and Inspections: $500 – $1,500.
These components contribute to the total cost of a Damp Proofing project and are essential for ensuring effective moisture control.
Estimate Florida Consulting offers a comprehensive fiber insulation cost calculator as part of our estimate services. This tool allows you to input specific project details, such as insulation type, area size, and desired R-value, to receive an accurate cost estimate. This helps align your project plans with your budget, ensuring that all necessary financial resources are accounted for.
A detailed cost breakdown for fiber insulation projects typically includes:
- Material Costs: $0.91 – $2.60 per square foot
- Labor Costs: $0.78 – $1.95 per square foot
- Equipment and Setup: $0.26 – $0.65 per square foot
- Permits and Inspections: $260 – $650 (one-time fee)
This breakdown helps you understand the potential costs involved and ensures that all aspects of the project are financially covered.
Accurate cost estimation is crucial for effective budgeting, efficient resource allocation, and successful project management. By obtaining precise estimates, you can prevent budget overruns, minimize material waste, and ensure that the project stays on schedule. Accurate estimates also help you make informed decisions about insulation materials and installation methods, leading to better long-term performance and energy savings.
Google Reviews
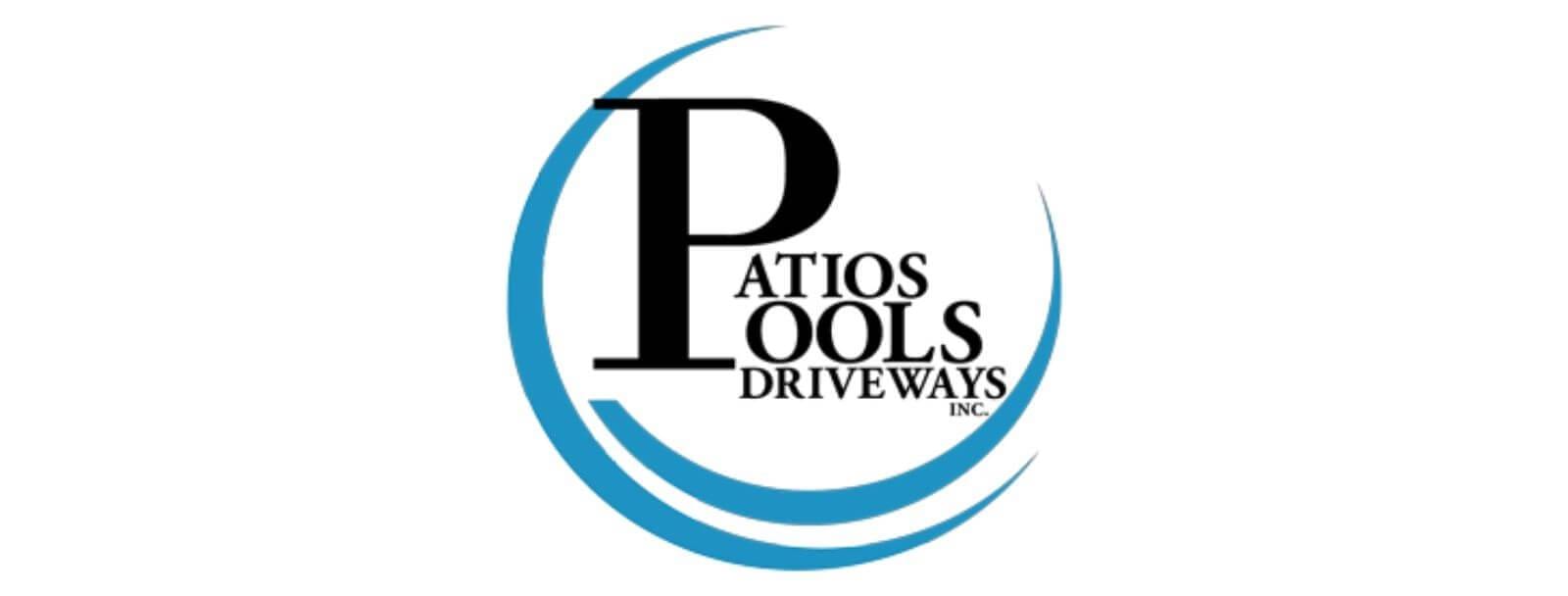
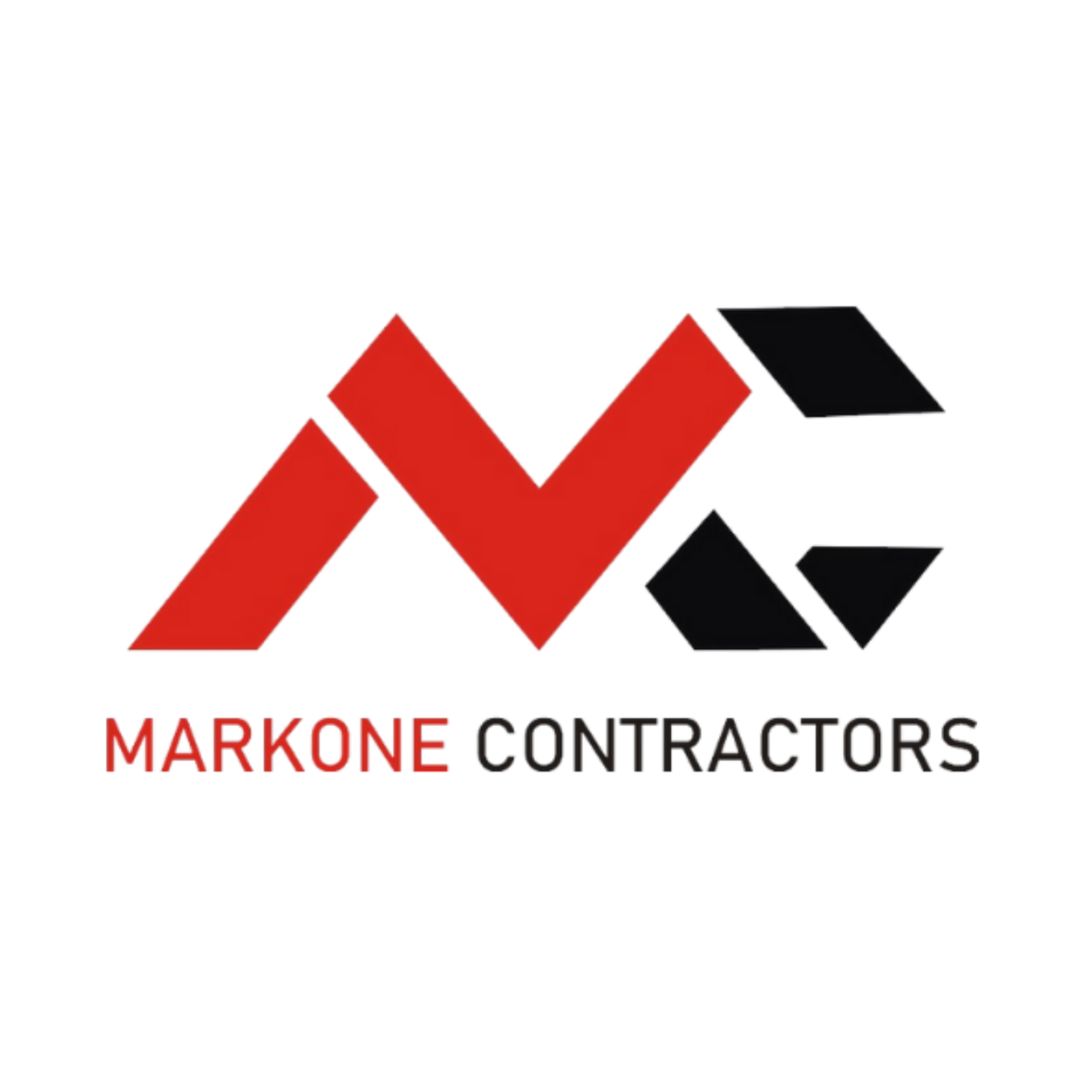

Process To Get Fiber Insulation Cost Estimate Report
Here I am going to share some steps to get fiber insulation cost estimate report.
-
You need to send your plan to us.
You can send us your plan on info@estimatorflorida.com
-
You receive a quote for your project.
Before starting your project, we send you a quote for your service. That quote will have detailed information about your project. Here you will get information about the size, difficulty, complexity and bid date when determining pricing.
-
Get Estimate Report
Our team will takeoff and estimate your project. When we deliver you’ll receive a PDF and an Excel file of your estimate. We can also offer construction lead generation services for the jobs you’d like to pursue further.