How Much Does a Tilt-Up Building Cost?
Tilt-up buildings have become a highly popular option in commercial construction, known for their efficiency, durability, and cost-effectiveness. The cost of constructing a tilt-up building typically ranges from $156 to $234 per square foot. However, the total cost can vary significantly based on a variety of factors, such as the building’s size, design complexity, and site conditions. These factors must be carefully considered to ensure that the project stays within budget while meeting all design and functional requirements. For businesses looking to build large structures like warehouses, retail centers, or office buildings, understanding these costs is crucial for effective budgeting and project planning.
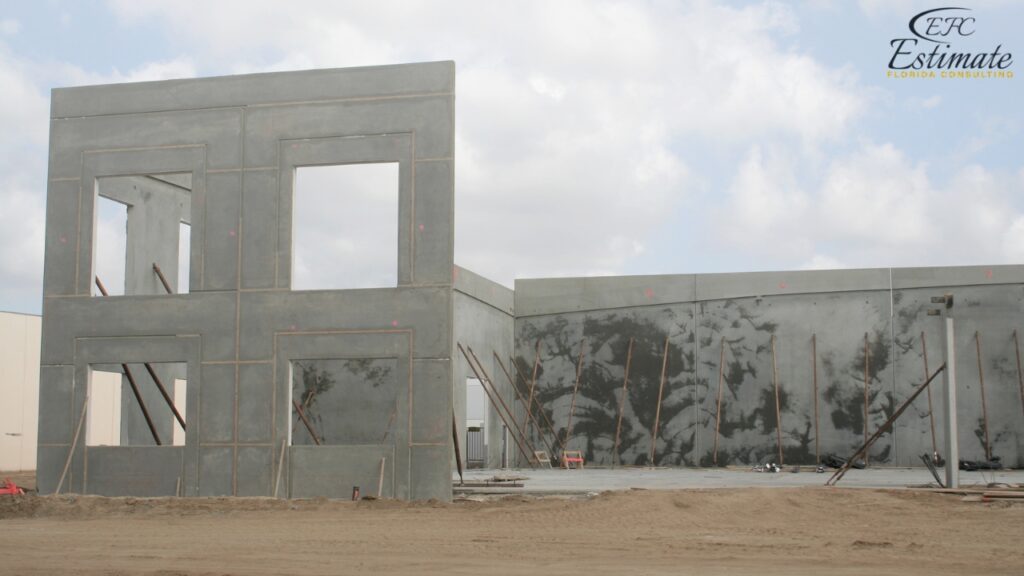
Understanding the Cost of a Tilt-Up Building
The cost of a tilt-up building is determined by several components, including materials, labor, and overheads, all of which contribute to the final price. On average, constructing a tilt-up building can cost between $1.56 million and $23.4 million, depending on the building’s size and complexity. This construction method is favored for its ability to deliver large, durable structures at a competitive cost, making it an ideal choice for various commercial applications. By understanding these cost components, developers can budget more effectively, ensuring that the project delivers the desired outcome within the allocated financial resources.
Average Cost per Square Foot for Tilt-Up Buildings
Tilt-up construction is renowned for its cost-effectiveness, with costs generally ranging between $156 and $234 per square foot. This pricing reflects the efficiencies inherent in the tilt-up construction method, which allows for the rapid construction of large structures. Here’s a breakdown of typical costs based on different building sizes:
Building Size (Square Feet) | Cost per Square Foot | Total Cost Range |
10,000 sq ft | $156 – $234 | $1,560,000 – $2,340,000 |
20,000 sq ft | $149.50 – $227.50 | $2,990,000 – $4,550,000 |
50,000 sq ft | $143 – $221 | $7,150,000 – $11,050,000 |
100,000 sq ft | $136.50 – $214.50 | $13,650,000 – $21,450,000 |
200,000 sq ft | $130 – $208 | $26,000,000 – $41,600,000 |
Get Acquainted with Tilt-Up Construction
Cost Breakdown
To budget effectively for a tilt-up construction project, it’s crucial to understand the different cost components involved. Each element plays a vital role in the overall construction process and contributes to the final cost. Here’s a detailed breakdown:
Cost Component | Cost per Square Foot |
Concrete Materials | $65 – $110.50 |
Labor Costs | $39 – $84.50 |
Equipment Rental | $13 – $39 |
Site Preparation and Foundation | $26 – $52 |
Panel Finishes and Customization | $13 – $32.50 |
Tilt-Up Building Costs to Other Construction Methods
Tilt-up construction offers a number of cost advantages when compared to other construction methods, such as steel framing, precast concrete, and masonry. Each method has its own strengths and weaknesses, but tilt-up construction is often more cost-effective for large-scale projects due to its unique combination of efficiency, durability, and flexibility.
Tilt-Up vs. Precast Concrete
Tilt-up panels are cast on-site, reducing transportation costs and allowing for greater customization. In contrast, precast concrete panels are manufactured off-site and then transported to the construction site, which can add significant costs and logistical challenges. Additionally, tilt-up construction allows for faster project timelines, as panels can be cast and erected on-site without the delays associated with transportation and scheduling. The on-site casting process also allows for last-minute adjustments, offering greater flexibility compared to precast methods.
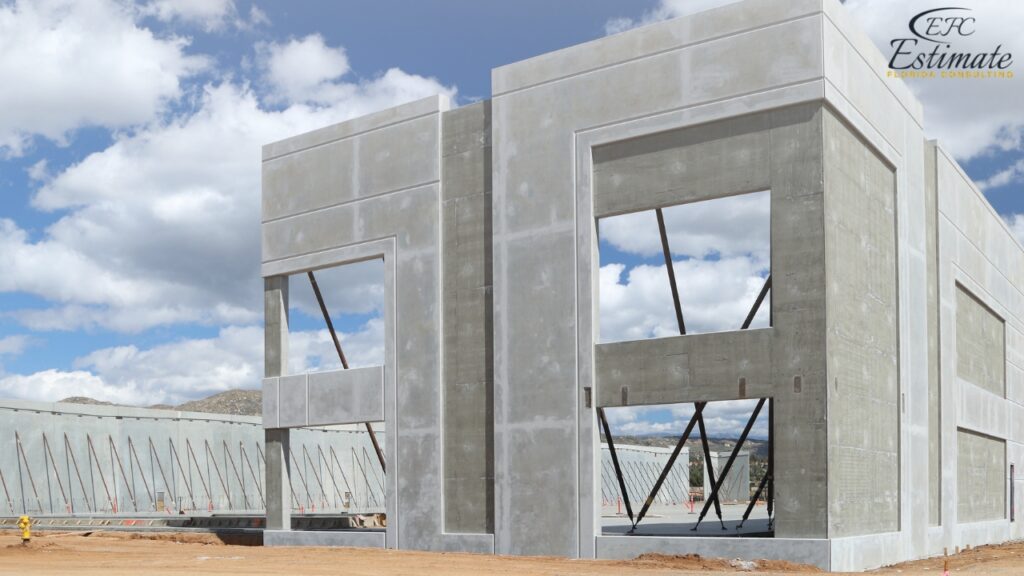
Tilt-Up vs. Steel Framing
While steel framing is lightweight and quick to erect, it may not offer the same level of durability and resistance to natural disasters as tilt-up concrete. Concrete panels provide superior thermal mass and sound insulation, making them a better choice for buildings that require high energy efficiency and noise control. Furthermore, tilt-up construction can be more cost-effective for large-scale projects, where the benefits of concrete’s durability and low maintenance requirements outweigh the initial investment.
Tilt-Up vs. Masonry
Masonry construction, although durable and aesthetically pleasing, often requires more labor and time to complete, making it more expensive for large buildings compared to tilt-up construction. Tilt-up concrete offers a faster and more efficient construction process, with fewer workers needed to achieve similar structural strength and aesthetic appeal. Additionally, the larger, uninterrupted panels used in tilt-up construction can reduce the number of joints and potential weak points in the building’s envelope, enhancing its overall performance and longevity.
How Much Does It Cost to Build a Warehouse?
Building a warehouse using tilt-up construction is one of the most cost-effective methods available, especially for large-scale industrial and storage facilities. The cost to build a warehouse typically ranges from $130 to $208 per square foot, depending on the size of the warehouse, the complexity of the design, and any custom features required. Larger warehouses benefit from economies of scale, which can reduce the cost per square foot. For instance, a 100,000 square foot warehouse may cost between $13.65 million and $21.45 million. These costs reflect the materials, labor, and equipment required to construct a durable, functional warehouse that meets the specific needs of the business.
Building Type and Size in Tilt-Up Construction
The type and size of the building greatly influence tilt-up construction costs. For example, a large warehouse might benefit from economies of scale, reducing the cost per square foot, while a smaller, more intricate office building could have higher costs due to increased design complexity and customization. Retail centers and industrial facilities often fall somewhere in between, with costs influenced by the specific requirements of the space. Understanding these variations allows developers to plan more effectively and tailor their construction approach to meet the unique needs of their project.
Long-Term Cost Benefits of Tilt-Up Buildings
Tilt-up buildings offer significant long-term cost benefits that extend well beyond the initial construction phase. These benefits include lower maintenance costs, increased energy efficiency, and enhanced durability, all of which contribute to the building’s overall value over time. The durability of concrete means that tilt-up buildings require fewer repairs and less frequent maintenance compared to structures built with other materials. Additionally, the thermal mass of concrete helps to maintain stable indoor temperatures, reducing the need for heating and cooling and leading to lower energy costs. Over the life of the building, these savings can add up, making tilt-up construction a financially sound investment.
90% More Chances to Win Projects With Our Estimate!
- Multi-Family Building
- Hotel Building
- Hospital Building
- Warehouse Building
- School & University Building
- High-Rise Building
- Shopping Complex
- Data Center Building
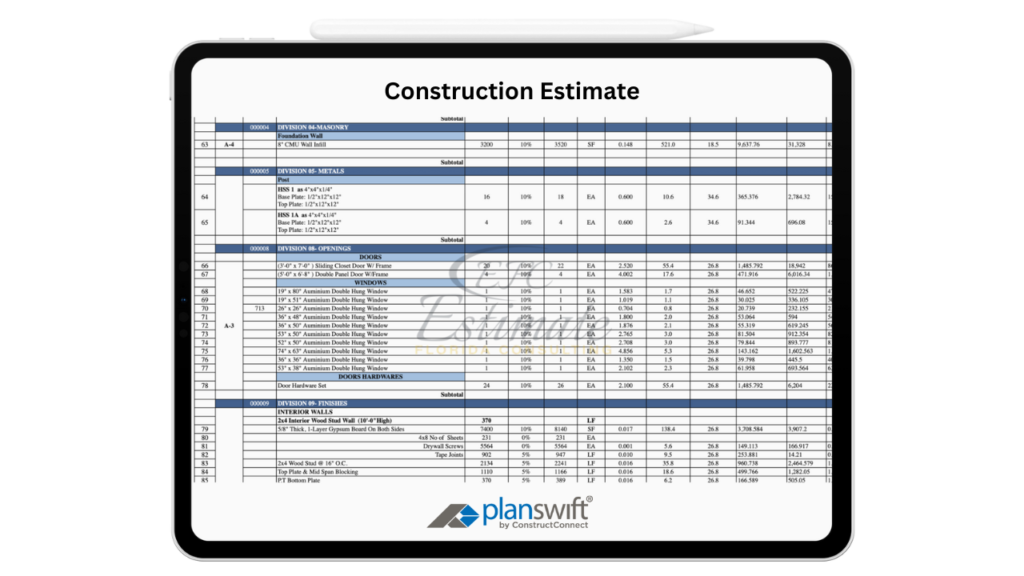
Additional Costs to Consider in Tilt-Up Building Projects
When planning a tilt-up building project, it’s essential to consider additional costs beyond the basic construction. These may include:
Permits and Inspections
Depending on the location, obtaining the necessary permits and undergoing inspections can add to the overall cost of the project. Permits are required to ensure that the construction adheres to local building codes, zoning laws, and safety regulations. Inspections by local authorities are also crucial throughout the construction process to ensure compliance with these regulations. While these costs may seem minor compared to the overall budget, failing to obtain the proper permits or pass inspections can lead to costly fines, delays, or even legal issues. Therefore, it’s essential to allocate a portion of the budget to cover these necessary expenses.
Utility Connections
Connecting the new building to existing utilities or installing new infrastructure can be an additional expense that must be factored into the overall budget. This includes connecting to water, sewer, gas, and electrical lines, which can vary significantly in cost depending on the location of the site. In some cases, the site may require extensive trenching or the installation of new utility lines, which can be both time-consuming and expensive. Additionally, the availability of utilities can influence these costs—remote locations may require more extensive work to connect to public services, increasing the overall expense. Ensuring that these connections are properly planned and executed is critical to the functionality and safety of the building.
Landscaping
Landscaping and site improvements are often required to complete the project and can add to the final cost. These enhancements go beyond just planting trees or grass; they can include grading, irrigation systems, walkways, parking lots, and outdoor lighting. Proper landscaping not only improves the aesthetic appeal of the building but also plays a role in drainage and erosion control, which are essential for maintaining the integrity of the site. Additionally, many municipalities have specific landscaping requirements that must be met to obtain final approval for the project. As a result, landscaping can represent a significant portion of the budget, particularly for commercial or large-scale developments.
Interior Finishing
While tilt-up construction primarily covers the shell of the building, interior finishing costs must also be considered, especially if the building requires high-end finishes. These can include installing flooring, lighting, HVAC systems, partition walls, and other features that make the space functional and attractive for its intended use. The choice of materials and finishes can greatly influence these costs—luxury finishes, custom cabinetry, or specialized lighting systems will add to the overall budget. Additionally, interior finishing may involve coordinating with various subcontractors, which can lead to increased labor costs and require careful scheduling to avoid delays.
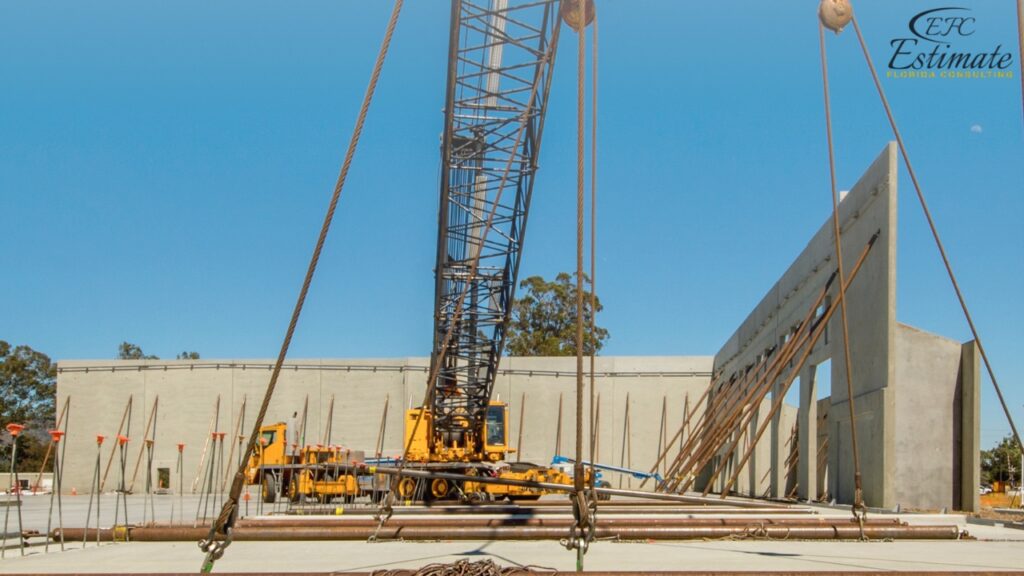
Proper planning for these costs ensures that the interior matches the quality and functionality of the building’s exterior, creating a cohesive and well-designed space.
Tips for Reducing the Cost of a Tilt-Up Building
Reducing the cost of a tilt-up building can be achieved through several strategies that focus on efficiency and smart decision-making:
Simplify the Design
Opting for a straightforward design can significantly reduce material and labor costs. Simple, functional designs are easier and faster to construct, which can lead to substantial savings. Complex architectural features, such as intricate facades, curved walls, or custom structural elements, often require additional materials, specialized labor, and more time to complete, driving up costs. By focusing on a design that emphasizes practicality and efficiency, you can streamline the construction process and reduce the need for costly custom work. Additionally, a simplified design can make it easier to meet building codes and regulations, further reducing the potential for delays and unexpected expenses.
Use Standard Materials
Utilizing standard sizes and materials can lower costs by reducing the need for custom fabrication. Standard materials are often more readily available and less expensive, helping to keep the project within budget. For example, using standard-sized panels, beams, and other components can reduce waste and minimize the need for special orders, which often come with higher price tags and longer lead times. Additionally, standard materials are typically easier to work with, requiring less specialized labor and equipment, which can further reduce costs. By choosing materials that are commonly used in the industry, you can also benefit from economies of scale, as suppliers may offer discounts for bulk purchases of widely available products.
Plan Efficiently
Careful planning and scheduling can prevent delays and reduce labor costs. Efficient project management ensures that all aspects of the construction process are coordinated effectively, minimizing downtime and maximizing productivity. Developing a comprehensive project plan that outlines each phase of the construction, including timelines, resource allocation, and contingency plans, is essential for keeping the project on track and within budget. By anticipating potential challenges and addressing them in advance, you can avoid costly delays and ensure that the construction proceeds smoothly. Additionally, maintaining clear communication among all stakeholders, including contractors, suppliers, and project managers, is crucial for ensuring that everyone is aligned and working towards the same goals.
Work with Experienced Contractors
Engaging contractors with extensive experience in tilt-up construction can help avoid costly mistakes and ensure the project stays on budget. Experienced contractors are more likely to anticipate and address potential issues before they become costly problems. They bring valuable knowledge and expertise to the table, allowing them to identify opportunities for cost savings, optimize the use of materials, and streamline the construction process. Moreover, experienced contractors are often better equipped to navigate the complexities of tilt-up construction, such as coordinating the placement of large panels, managing the sequencing of tasks, and ensuring that all work meets the required standards. By choosing contractors with a proven track record in tilt-up projects, you can reduce the risk of errors, rework, and delays, all of which can contribute to significant cost savings over the course of the project.
Tilt-Up Building Cost Estimator
Estimating the cost of your tilt-up building project is essential for accurate budgeting and financial planning. A tilt-up building cost estimator can provide a detailed analysis of expected costs based on factors like building size, materials, and site conditions. This tool helps you understand the financial scope of your project and allows for adjustments to meet your budget constraints. By using a cost estimator, you can gain insights into where to allocate resources effectively and identify areas where savings might be possible. Accurate cost estimation is crucial for the success of any construction project, as it ensures that you are fully prepared for all financial aspects of the build.
Tilt-Up Building Cost Calculator
A tilt-up building cost calculator is a valuable tool for both contractors and developers. It allows you to input specific details about your project, such as square footage, panel thickness, and customization preferences, to generate an estimated cost. This calculator helps streamline the planning process by providing real-time data that reflects current market conditions and material costs. Using a cost calculator can also aid in decision-making by comparing different construction scenarios and understanding how changes in design or materials affect the overall budget. This level of detail allows you to make informed decisions that align with your financial goals and project requirements.
Download Template For Construction Project Breakdown
- Materials list updated to the zip code
- Fast delivery
- Data base of general contractors and sub-contractors
- Local estimators
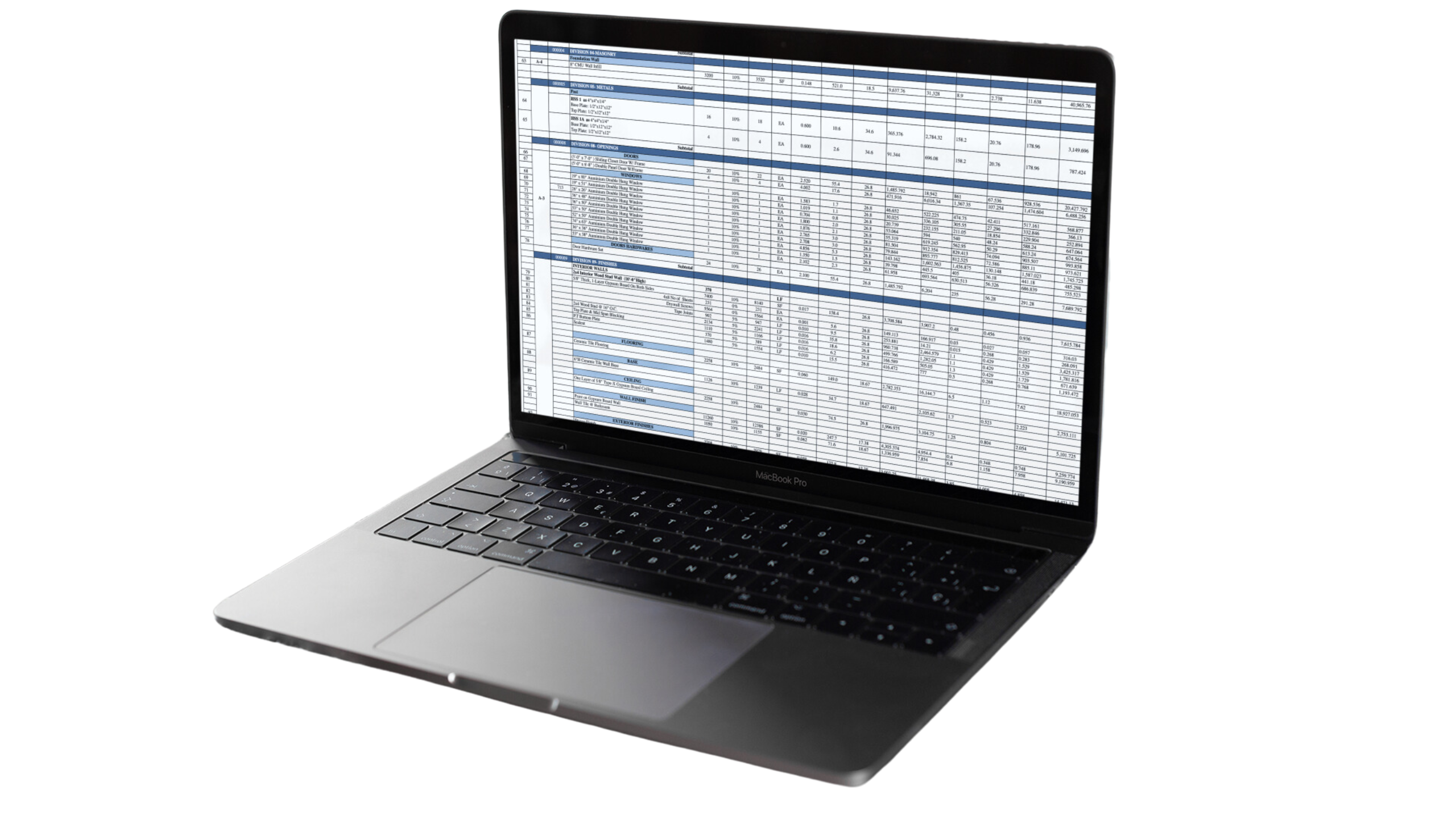
How Estimate Florida Consulting Can Help Estimate Your Tilt-Up Building Costs?
Estimate Florida Consulting provides comprehensive cost estimation services tailored to tilt-up building projects. Their expertise ensures that you receive an accurate and detailed estimate that reflects the true cost of your project, including materials, labor, and any additional expenses. By connecting you with experienced contractors, Estimate Florida Consulting helps ensure your tilt-up building project is completed on time and within budget. Their services not only assist in the planning and budgeting stages but also support you throughout the construction process, ensuring that your project is managed efficiently and effectively. Whether you are looking for a detailed cost estimate or need help with contractor selection, Estimate Florida Consulting is equipped to guide you through every step of your tilt-up building project, making sure you achieve the best possible results.
FAQs
Tilt-up buildings are a popular choice in commercial construction due to their cost-effectiveness, durability, and efficiency. The cost of constructing a tilt-up building generally ranges from $156 to $234 per square foot. However, the total cost can vary depending on factors such as the building’s size, design complexity, and site conditions. It’s essential to consider these factors carefully to stay within budget while meeting design and functional requirements.
The cost of a tilt-up building is determined by several components, including materials, labor, and overheads. On average, constructing a tilt-up building can range from $1.56 million to $23.4 million, depending on the building’s size and complexity. Understanding these cost components helps developers budget effectively, ensuring the project delivers the desired outcome within the allocated financial resources.
Tilt-up construction is known for its cost-efficiency, with prices typically ranging between $156 and $234 per square foot. Here’s a breakdown based on different building sizes:
- 10,000 sq ft: $1.56 million – $2.34 million
- 20,000 sq ft: $2.99 million – $4.55 million
- 50,000 sq ft: $7.15 million – $11.05 million
- 100,000 sq ft: $13.65 million – $21.45 million
- 200,000 sq ft: $26 million – $41.6 million
The cost breakdown for a tilt-up building includes various elements:
- Concrete Materials: $65 – $110.50 per sq ft
- Labor Costs: $39 – $84.50 per sq ft
- Equipment Rental: $13 – $39 per sq ft
- Site Preparation and Foundation: $26 – $52 per sq ft
- Panel Finishes and Customization: $13 – $32.50 per sq ft
Tilt-up construction offers several cost advantages compared to methods like steel framing, precast concrete, and masonry:
- Tilt-Up vs. Precast Concrete: Tilt-up panels are cast on-site, reducing transportation costs and allowing greater customization.
- Tilt-Up vs. Steel Framing: While steel framing is quick to erect, tilt-up concrete offers superior durability, thermal mass, and sound insulation.
- Tilt-Up vs. Masonry: Masonry requires more labor and time, making tilt-up construction more cost-effective for large buildings.
To budget effectively for a tilt-up construction project, it’s crucial to understand the different cost components involved. Each element plays a vital role in the overall construction process and contributes to the final cost. Here’s a detailed breakdown:
Cost Component | Cost per Square Foot |
Concrete Materials | $65 – $110.50 |
Labor Costs | $39 – $84.50 |
Equipment Rental | $13 – $39 |
Site Preparation and Foundation | $26 – $52 |
Panel Finishes and Customization | $13 – $32.50 |
Google Reviews
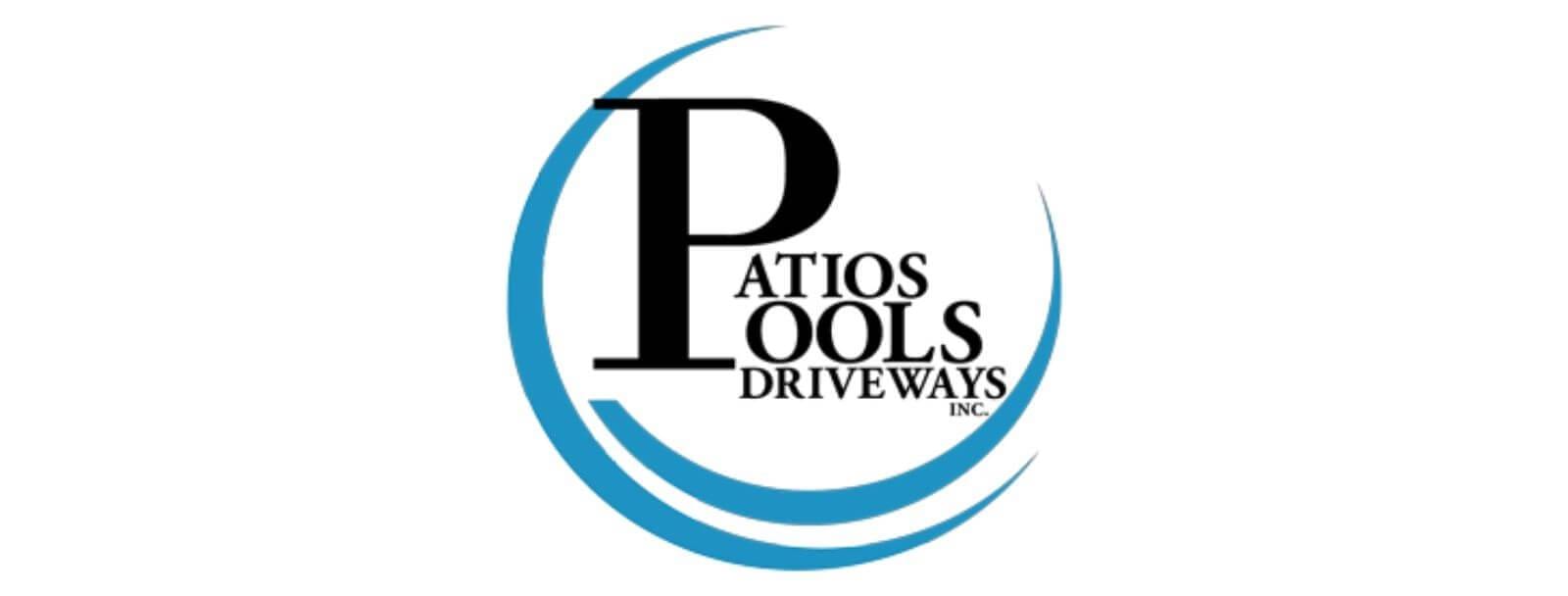
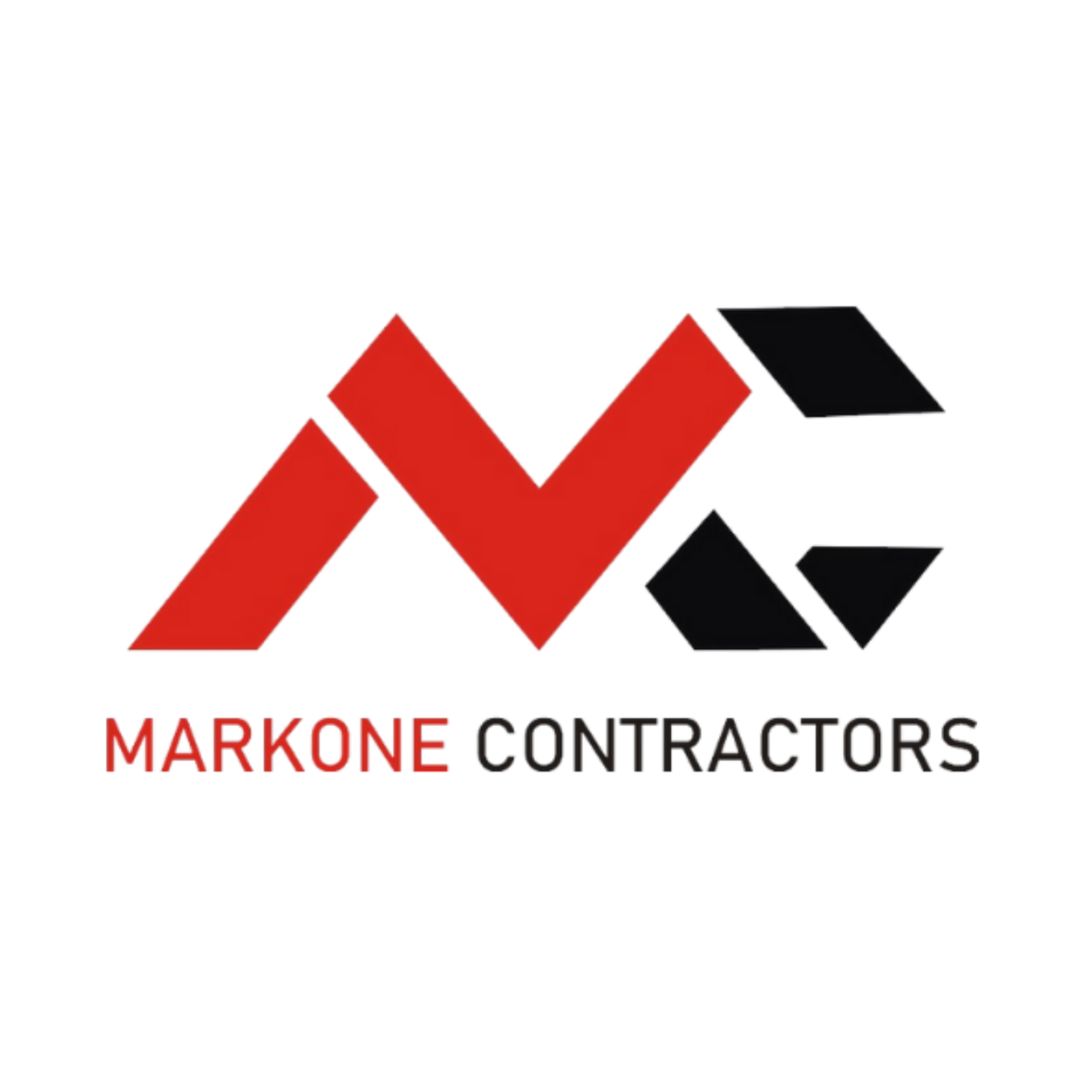

Process To Get The Tilt-Up Building Estimate Report
Here I am going to share some steps to get the tilt-up uilding estimate report.
-
You need to send your plan to us.
You can send us your plan on info@estimatorflorida.com
-
You receive a quote for your project.
Before starting your project, we send you a quote for your service. That quote will have detailed information about your project. Here you will get information about the size, difficulty, complexity and bid date when determining pricing.
-
Get Estimate Report
Our team will takeoff and estimate your project. When we deliver you’ll receive a PDF and an Excel file of your estimate. We can also offer construction lead generation services for the jobs you’d like to pursue further.