How Much Does a Commercial Elevator Cost for a 2-Story Building?
A commercial elevator for a 2-story building typically costs between $81,500 and $216,000, averaging $200 to $400 per square foot. This includes the elevator unit ($60,000 to $120,000), installation ($15,000 to $60,000), permits ($1,500 to $3,000), and necessary building modifications. Costs vary based on the type of elevator (hydraulic, traction, or machine-room-less), customization options, and the building’s structural requirements. Additional expenses may arise from structural changes ($5,000 to $15,000), electrical work ($2,000 to $5,000), and finishes ($3,000 to $7,000).
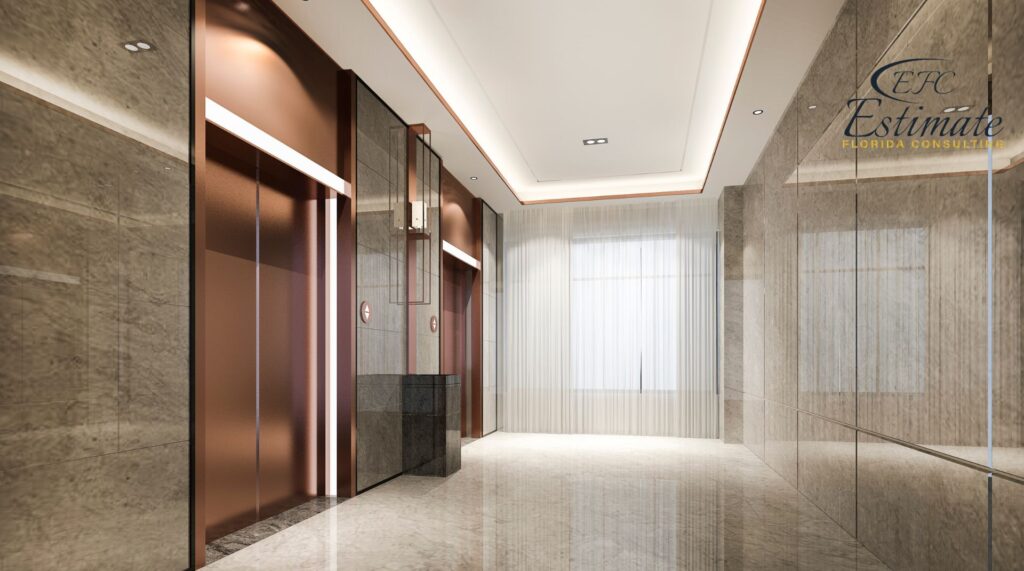
To ensure a successful installation, obtain multiple quotes, choose a reliable installer, and plan for long-term maintenance. Proper installation enhances accessibility and property value.
Cost Breakdown for Installing a Commercial Elevator
Materials
The cost of materials is a significant portion of the total cost for installing a commercial elevator. Here is an estimate of typical material costs:
Material | Estimated Cost (in dollars) |
Elevator Equipment | $20,000 – $50,000 |
Cab and Fixtures | $10,000 – $25,000 |
Doors and Entrances | $5,000 – $15,000 |
Control Systems | $5,000 – $15,000 |
These costs can vary depending on the quality of materials chosen and any additional features or upgrades included in the project. Higher-end materials and advanced construction techniques can increase the overall material costs. For instance, opting for custom-designed cabs with luxury finishes or advanced control systems can add significantly to the cost. Conversely, selecting standard materials and finishes can help keep expenses within budget while still achieving functionality and compliance with safety standards.
Labor
Labor costs for installing a commercial elevator can vary based on the complexity of the job, local labor rates, and the condition of the building. Here’s an estimate of labor costs:
Labor Task | Estimated Cost (in dollars) |
Installation | $20,000 – $50,000 |
Electrical Work | $5,000 – $15,000 |
Structural Modifications | $5,000 – $15,000 |
Testing and Inspection | $2,000 – $5,000 |
Labor costs can fluctuate based on the complexity of the project and the need for specialized work, such as electrical and structural modifications. Hiring experienced professionals is essential to ensure the work is done safely and up to code. Labor costs also include the planning and coordination efforts required to integrate the elevator into the existing building infrastructure. Skilled technicians and engineers are needed to handle the sophisticated machinery and ensure all systems are installed correctly and efficiently. Investing in experienced labor can prevent costly errors and ensure the elevator meets all regulatory requirements.
Additional Costs
Additional costs can include permits, inspection fees, site preparation, and any necessary infrastructure improvements. Here’s an estimate of the additional costs:
Additional Component | Estimated Cost (in dollars) |
Permits | $500 – $5,000 |
Site Preparation | $2,000 – $5,000 |
Utility Connections | $1,000 – $3,000 |
Inspection Fees | $1,000 – $3,000 |
Contingency Budget | $5,000 – $10,000 |
These additional costs can add up, particularly if significant site preparation or infrastructure improvements are needed. It is essential to budget for these expenses to ensure the project is completed without unexpected financial strain. Permits and inspection fees are necessary to ensure compliance with local building codes and safety standards. Site preparation costs can include modifications to existing structures, excavation for hydraulic systems, or adjustments to accommodate the elevator shaft. A contingency budget is crucial to cover any unforeseen expenses that may arise during the installation process, such as unexpected structural issues or additional labor requirements.
90% More Chances to Win Projects With Our Estimate!
- Multi-Family Building
- Hotel Building
- Hospital Building
- Warehouse Building
- School & University Building
- High-Rise Building
- Shopping Complex
- Data Center Building
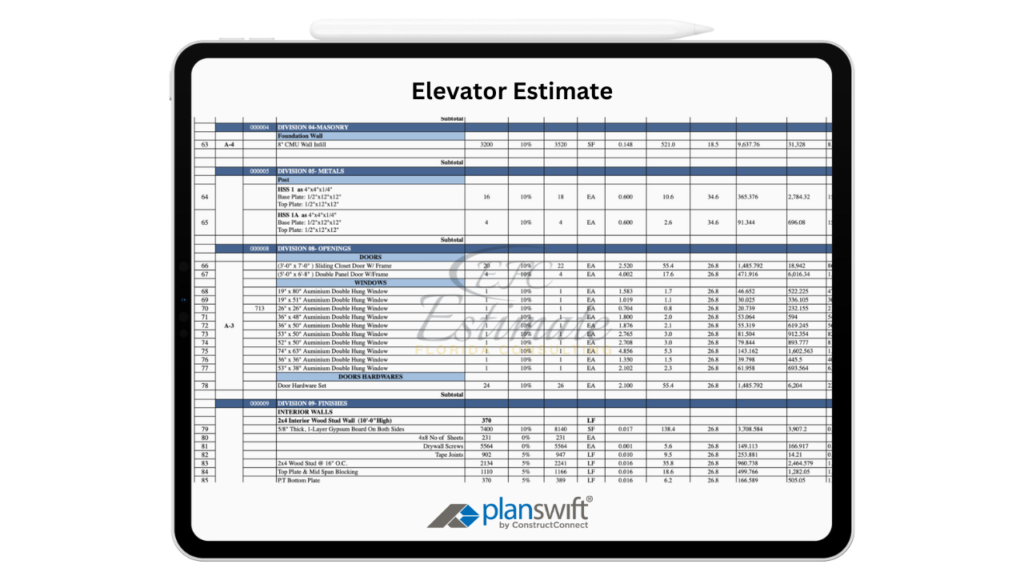
Detailed Cost Breakdown by Components
Elevator Equipment
The cost of the elevator equipment includes the machinery, cables, and other essential components. Here’s a detailed breakdown of elevator equipment costs:
Type of Equipment | Estimated Cost (in dollars) |
Hydraulic System | $20,000 – $30,000 |
Traction System | $30,000 – $50,000 |
Hydraulic systems are generally less expensive but may have higher long-term maintenance costs due to the hydraulic fluid and machinery required. Traction systems, on the other hand, are more efficient and durable, making them a preferred choice for many commercial buildings. Traction elevators typically offer smoother rides and faster travel times, which can enhance user experience. The choice between hydraulic and traction systems should consider both initial costs and long-term operational expenses.
Cab and Fixtures
The cab and fixtures include the interior finishes, lighting, and controls within the elevator cab. Here’s a detailed breakdown of cab and fixture costs:
Type of Fixtures | Estimated Cost (in dollars) |
Standard Cab | $10,000 – $15,000 |
Custom Cab | $15,000 – $25,000 |
Standard cabs are functional and cost-effective, while custom cabs offer high-end finishes and features that enhance the aesthetic appeal and user experience. Customization options can include materials like stainless steel, glass, or wood paneling, as well as lighting designs that can make the cab more appealing. Custom cabs can also be tailored to match the interior design of the building, creating a cohesive look.
Doors and Entrances
The doors and entrances include the mechanisms and finishes for the elevator doors. Here’s a detailed breakdown of door and entrance costs:
Type of Doors | Estimated Cost (in dollars) |
Standard Doors | $5,000 – $10,000 |
Custom Doors | $10,000 – $15,000 |
Standard doors are practical and economical, while custom doors provide advanced features and aesthetics, suitable for high-end commercial properties. Custom door options can include materials like glass, stainless steel, or decorative metals. Advanced door systems may also feature touchless operation, improving accessibility and hygiene, especially in high-traffic areas.
Control Systems
The control systems include the panels and software that operate the elevator. Here’s a detailed breakdown of control system costs:
Type of Control System | Estimated Cost (in dollars) |
Basic Control System | $5,000 – $10,000 |
Advanced Control System | $10,000 – $15,000 |
Basic control systems provide essential functionality, while advanced systems offer features like touch-screen interfaces, energy-efficient operations, and remote monitoring capabilities. Advanced control systems can also include features like destination dispatch, which optimizes elevator usage and reduces wait times by grouping passengers going to the same floors. Energy-efficient control systems can help reduce operational costs over the elevator’s lifespan.
Safety Features
Safety features are crucial for ensuring the protection of elevator users. Here’s a detailed breakdown of safety feature costs:
Safety Feature | Estimated Cost (in dollars) |
Emergency Communication | $2,000 – $5,000 |
Fire Safety Systems | $3,000 – $7,000 |
Backup Power Supply | $5,000 – $10,000 |
Emergency communication systems allow passengers to contact help in case of an emergency, while fire safety systems include fire-resistant materials and alarms. Backup power supplies ensure the elevator remains operational during power outages, enhancing safety and reliability.
Environmental and Energy-Efficient Features
Implementing environmental and energy-efficient features can reduce operational costs and support sustainability goals. Here’s a detailed breakdown of these feature costs:
Feature | Estimated Cost (in dollars) |
Regenerative Drives | $5,000 – $15,000 |
LED Lighting | $1,000 – $3,000 |
Energy-Efficient Motors | $3,000 – $7,000 |
Regenerative drives can convert energy generated during braking into reusable power, while LED lighting reduces electricity consumption. Energy-efficient motors operate with less power, reducing overall energy costs.
Maintenance and Service Contracts
Regular maintenance is essential to ensure the elevator operates smoothly and safely. Here’s a detailed breakdown of maintenance and service contract costs:
Maintenance Task | Estimated Cost (in dollars) per Year |
Basic Maintenance | $2,000 – $4,000 |
Comprehensive Maintenance | $4,000 – $8,000 |
Emergency Repairs | $1,000 – $3,000 |
Basic maintenance includes routine inspections and minor repairs, while comprehensive maintenance covers all aspects of elevator upkeep, including major repairs. Emergency repair costs are additional expenses that may arise from unexpected issues.
Elevator Modernization
Modernizing an existing elevator can improve performance, safety, and aesthetics. Here’s a detailed breakdown of modernization costs:
Modernization Task | Estimated Cost (in dollars) |
Upgrading Control Systems | $10,000 – $20,000 |
Replacing Cab Interiors | $5,000 – $15,000 |
Enhancing Safety Features | $5,000 – $10,000 |
Upgrading control systems can enhance efficiency and user experience, while replacing cab interiors can modernize the appearance. Enhancing safety features ensures the elevator meets the latest safety standards.
Cost-Saving Tips
Choose the Right Type of Elevator
Selecting the most suitable type of elevator for your building’s needs can help manage costs. For a 2-story building, a hydraulic elevator is often sufficient and more cost-effective than a traction elevator. Hydraulic elevators are ideal for low-rise buildings and offer a balance of cost and functionality. However, if long-term operational costs and energy efficiency are a priority, a traction elevator might be worth the higher initial investment.
Optimize Load Capacity and Speed
Choosing an elevator with a load capacity and speed appropriate for your building can avoid unnecessary expenses. Over-specifying these aspects can lead to higher costs without added benefits for a low-rise building. Assessing the typical usage and traffic patterns can help determine the most efficient and cost-effective specifications for your elevator. Additionally, consulting with an elevator specialist can provide insights into the optimal load capacity and speed for your specific building.
Plan Efficiently
Efficient planning and coordination with contractors can minimize delays and reduce overall costs. Ensure that all necessary modifications and preparations are considered before starting the installation to avoid unexpected expenses. Detailed planning includes assessing the structural integrity of the building, ensuring adequate space for the elevator shaft, and coordinating with various contractors for electrical and mechanical work. A well-coordinated project timeline can prevent delays and reduce labor costs.
Obtain Multiple Quotes
Getting multiple quotes from elevator suppliers and installation contractors can help you find the best price for your project. Compare quotes based on the scope of work, materials included, and the experience of the contractors. Engaging in competitive bidding can leverage better pricing and terms. Evaluating contractor performance and reputation can ensure quality outcomes, balancing cost considerations with project success. Taking the time to review multiple options can prevent overpaying and ensure that the project stays within budget. Additionally, obtaining detailed quotes can help in identifying potential cost-saving opportunities and negotiating better terms.
Invest in Energy-Efficient Features
Investing in energy-efficient features such as regenerative drives and LED lighting can reduce long-term operational costs. While these features might have higher initial costs, the savings on energy bills can justify the investment over time. Additionally, energy-efficient elevators contribute to sustainability efforts, which can be an attractive feature for environmentally conscious tenants and customers.
Download Template For Elevator Project Breakdown
- Materials list updated to the zip code
- Fast delivery
- Data base of general contractors and sub-contractors
- Local estimators
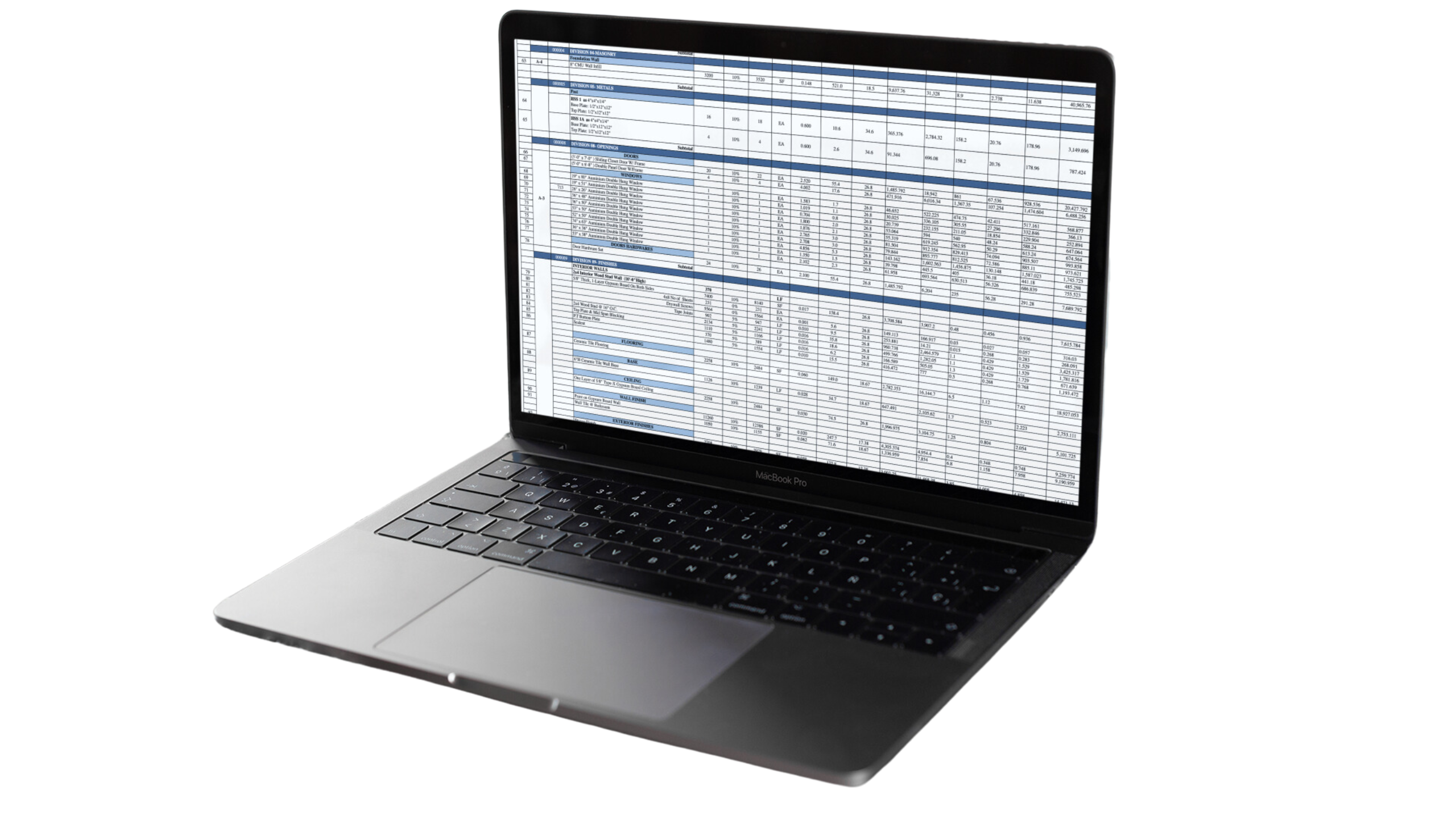
Conclusion
Installing a commercial elevator in a 2-story building is a substantial investment that requires careful planning and budgeting. By understanding the various costs involved and considering factors such as elevator type, load capacity, and customization options, you can make informed decisions and ensure the success of your elevator installation project. Investing in high-quality materials, working with experienced professionals, and planning for contingencies can ensure a successful and cost-effective elevator installation. Properly managing the installation process not only ensures compliance with safety standards but also maximizes the functionality and lifespan of your elevator. By taking the time to plan and budget carefully, you can achieve a reliable and efficient elevator system that enhances the accessibility and value of your building. Considering the long-term benefits and potential property value increase can also justify the initial investment, making it a wise choice for commercial property owners.
FAQs
The typical cost range for a commercial elevator in a 2-story building is between $81,500 and $216,000. This includes the cost of the elevator unit, installation, permits, and necessary building modifications.
The cost of the elevator unit typically ranges from $60,000 to $120,000, depending on the type of elevator and any customization options.
Installation costs for a commercial elevator can range from $15,000 to $60,000, varying based on the complexity of the installation and the local labor rates.
Yes, additional costs for permits and inspections usually range from $1,500 to $3,000. These are necessary to ensure compliance with local building codes and safety standards.
The main types of elevators available for a 2-story building include hydraulic elevators, traction elevators, and machine-room-less (MRL) elevators. Each type has different cost implications and features.
Customization options such as luxury finishes, advanced control systems, and unique cab designs can significantly increase the overall cost. Custom cabs and fixtures can add between $3,000 to $25,000 to the total cost.
Structural changes required to accommodate the elevator can cost between $5,000 and $15,000. These changes may include modifications to the building’s structure and additional support systems.
Electrical work for the elevator installation typically costs between $2,000 and $5,000. This includes wiring and connecting the elevator to the building’s electrical system.
Yes, additional costs for finishes and fixtures can range from $3,000 to $7,000. This includes interior cab finishes, lighting, and control panels.
Obtaining multiple quotes from elevator suppliers and installation contractors helps ensure you get the best price and quality for your project. Comparing quotes can highlight differences in scope, materials, and contractor experience.
Long-term maintenance is crucial for the smooth operation and safety of the elevator. Annual maintenance costs can range from $2,000 to $8,000, depending on the level of service required.
Cost-saving tips include choosing the right type of elevator for your needs, optimizing load capacity and speed, efficient planning and coordination, obtaining multiple quotes, and investing in energy-efficient features.
Google Reviews
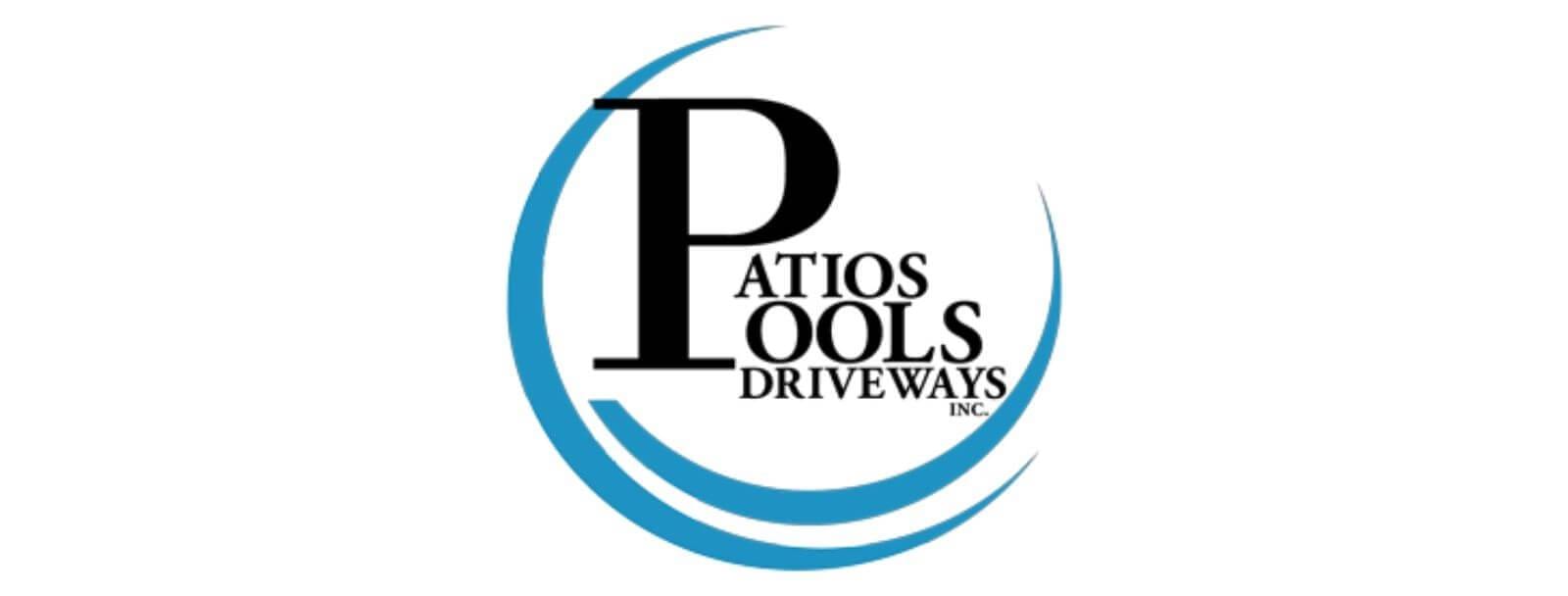
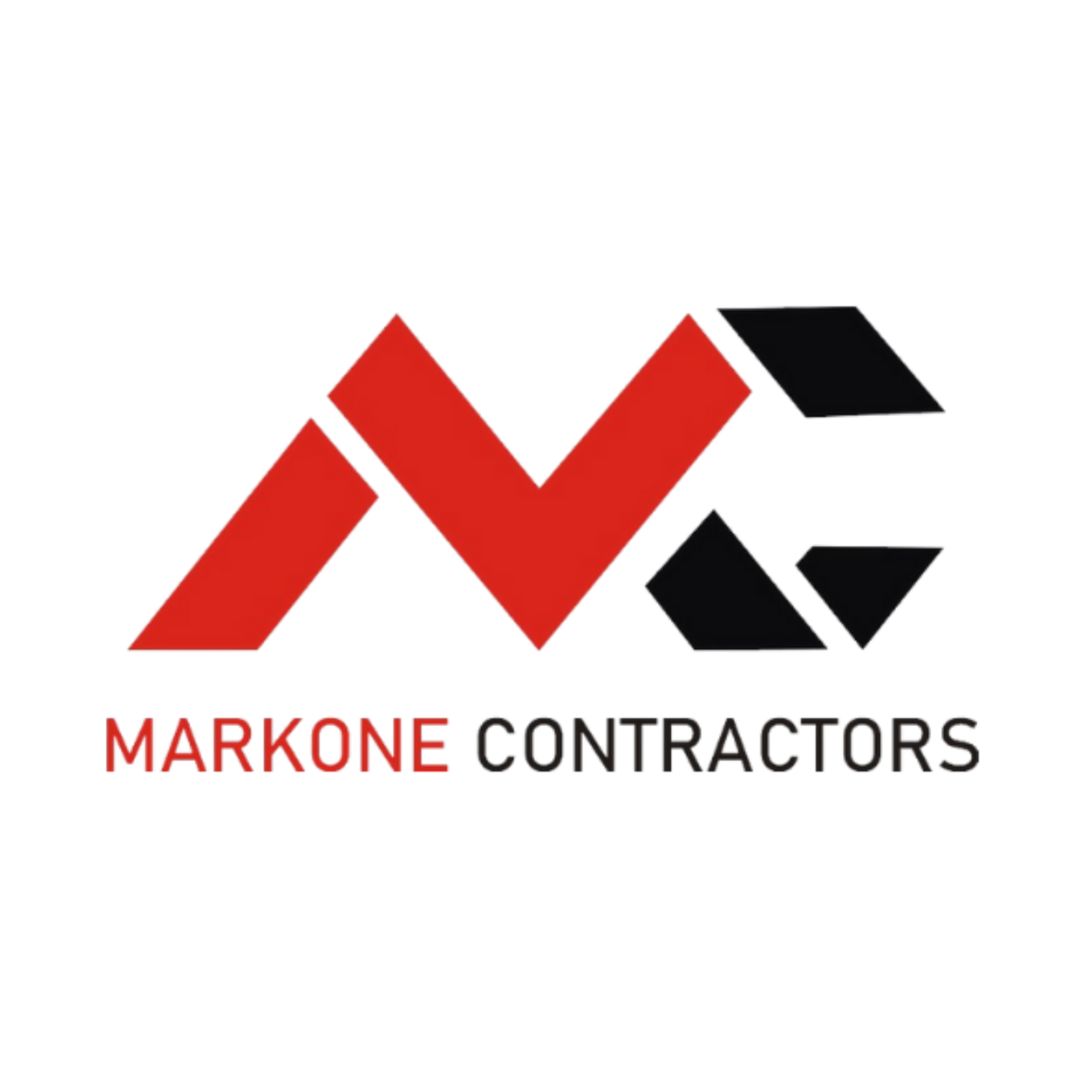

Process To Get Warehouse Fire Sprinkler System Cost Estimate Report
Here I am going to share some steps to get warehouse fire sprinkler system cost estimate report.
-
You need to send your plan to us.
You can send us your plan on info@estimatorflorida.com
-
You receive a quote for your project.
Before starting your project, we send you a quote for your service. That quote will have detailed information about your project. Here you will get information about the size, difficulty, complexity and bid date when determining pricing.
-
Get Estimate Report
Our team will takeoff and estimate your project. When we deliver you’ll receive a PDF and an Excel file of your estimate. We can also offer construction lead generation services for the jobs you’d like to pursue further.