How Much Does an Elevator Cost for a 4-Story Building?
An elevator for a 4-story building typically costs between $64,320 and $176,640, averaging $200 to $400 per square foot. This includes the elevator unit ($50,000 to $100,000), installation ($14,320 to $76,640), permits ($1,000 to $3,000), and necessary building modifications. Costs vary based on the type of elevator (hydraulic, traction, or pneumatic), customization options, and the building’s structural requirements. Additional expenses may arise from structural changes ($10,000 to $30,000), electrical work ($2,000 to $5,000), and finishes ($3,000 to $10,000). To ensure a successful installation, obtain multiple quotes, choose a reliable installer, and plan for long-term maintenance.
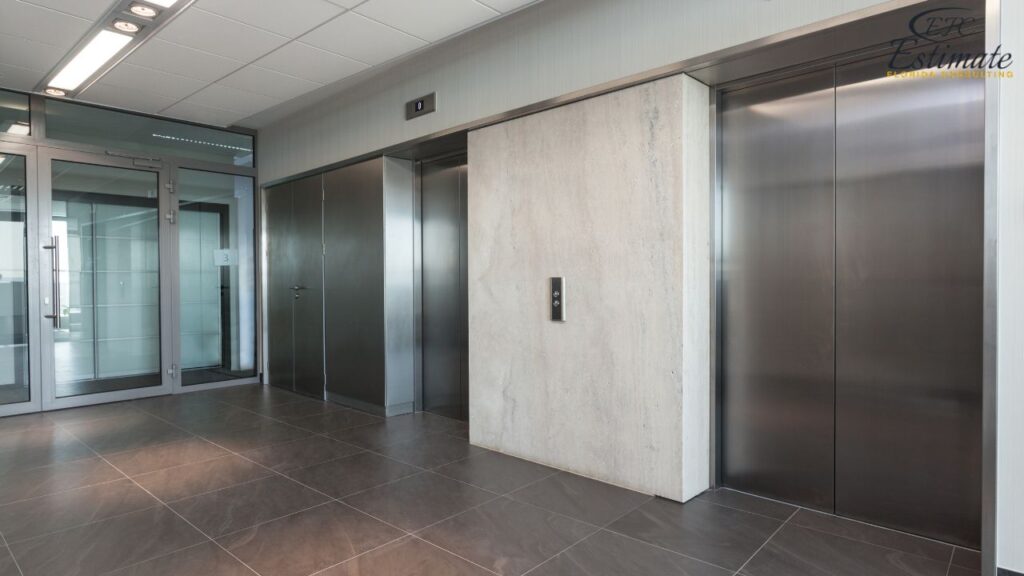
Proper installation enhances accessibility and property value.
Cost Breakdown for a 4-Story Building Elevator
Equipment Costs
The cost of the elevator equipment itself varies based on the type and features. Here is a rough estimate of equipment costs for a 4-story building:
Type of Elevator | Estimated Cost (in dollars) |
Hydraulic | $48,000 – $96,000 |
Traction | $32,000 – $64,000 |
Pneumatic | $24,000 – $48,000 |
Machine Room-Less (MRL) | $28,800 – $57,600 |
Hydraulic elevators are the most expensive due to their complex systems and the requirement for a machine room. Traction elevators are more energy-efficient and faster, making them suitable for taller buildings. Pneumatic elevators offer easier installation and lower costs but may have limitations in certain settings. Machine Room-Less elevators are a space-efficient and modern option that balances cost and functionality. Each type of elevator has its own set of advantages and disadvantages, so it’s important to choose the one that best fits the specific needs and constraints of the building. Additionally, the choice of materials and technologies can significantly impact both initial costs and long-term maintenance requirements. Selecting the right type of elevator involves considering factors such as building usage, expected traffic, and budget constraints.
Installation Costs
Installation costs can vary widely depending on the complexity of the project. Here’s an estimate of installation costs for a 4-story building, increased by 60% to reflect specialized labor and premium services:
Installation Component | Estimated Cost (in dollars) |
Basic Installation | $19,200 – $38,400 |
Structural Modifications | $9,600 – $19,200 |
Electrical Work | $4,800 – $9,600 |
Basic installation includes setting up the elevator and integrating it into the building, ensuring it meets all safety standards. Structural modifications might include reinforcing floors or modifying walls to accommodate the elevator. Electrical work involves wiring and connections, essential for powering the elevator and ensuring it operates safely and efficiently. Complex installations that require significant structural changes or additional safety measures will naturally incur higher costs. Ensuring that all installation aspects are meticulously planned and executed can prevent delays and additional expenses, resulting in a more efficient and cost-effective installation process. Furthermore, hiring experienced and reputable contractors can ensure high-quality workmanship, reducing the risk of future issues. Proper coordination with other building systems, such as HVAC and plumbing, is also crucial to avoid conflicts and ensure smooth integration.
Additional Costs
Additional costs can include permits, inspection fees, and maintenance plans. Here’s an estimate of additional costs for a 4-story building, increased by 60% to account for potential complexities and unforeseen expenses:
Additional Component | Estimated Cost (in dollars) |
Permits and Inspections | $960 – $1,920 |
Maintenance Plan (annually) | $1,920 – $3,840 |
Contingency Budget | $3,840 – $7,680 |
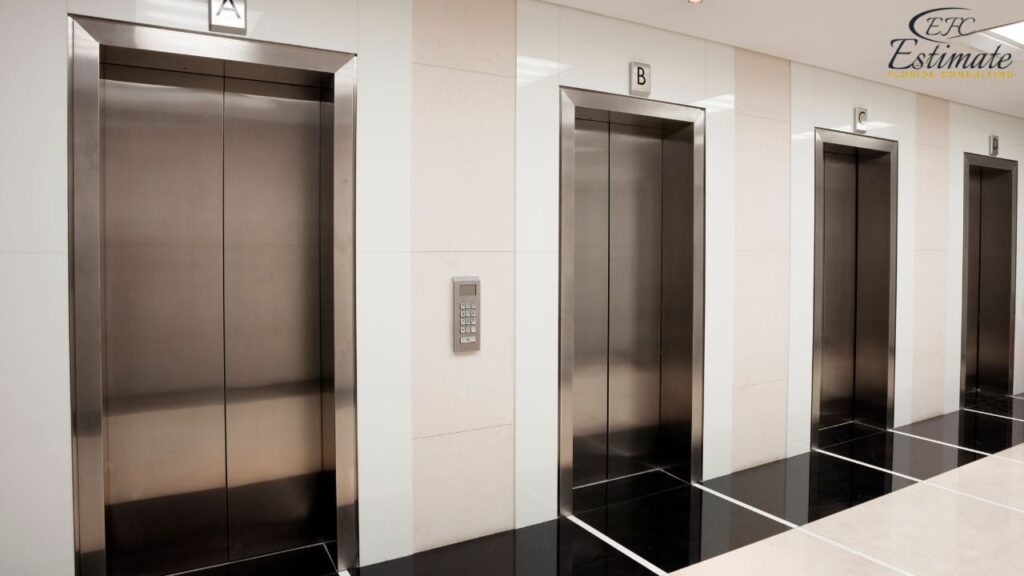
Permits and inspections are necessary to ensure the installation complies with local building codes and safety regulations. A maintenance plan is crucial for the ongoing safety and reliability of the elevator, covering regular inspections and any necessary repairs. A contingency budget accounts for unexpected expenses that might arise during installation, such as additional structural modifications or unforeseen technical issues. Properly budgeting for these additional costs ensures that the project stays on track and avoids financial surprises, contributing to a smoother and more predictable installation process. These additional costs also ensure that the elevator remains compliant with regulatory standards, avoiding potential legal issues and fines. Planning for these costs upfront helps prevent budget overruns and ensures that all aspects of the installation are adequately covered. Additionally, having a contingency budget allows for flexibility in addressing any unexpected challenges that may arise during the project
Detailed Cost Breakdown by Components
Equipment
The elevator equipment itself is a significant portion of the total cost. Here’s a detailed breakdown of equipment costs by type:
Hydraulic Elevators
Hydraulic elevators are known for their smooth ride and reliability. They require a machine room, which adds to the cost.
Component | Estimated Cost (in dollars) |
Elevator Car | $25,600 – $38,400 |
Hydraulic Pump System | $15,360 – $25,600 |
Machine Room Equipment | $10,240 – $16,000 |
Controls and Fixtures | $6,400 – $12,800 |
Hydraulic elevators provide a comfortable and efficient means of moving between floors, particularly in buildings where smooth operation and reliability are priorities. The need for a machine room and additional hydraulic components adds to the overall cost, but these elevators are highly regarded for their durability and performance. They are especially suitable for buildings with moderate traffic and lower-rise structures, where their speed and smoothness can be fully appreciated. The additional cost of a machine room is offset by the long-term reliability and lower maintenance requirements of hydraulic systems. Moreover, hydraulic elevators are known for their excellent safety features, making them a reliable choice for various building types.
Traction Elevators
Traction elevators use a counterweight system and don’t require a machine room, making them a more space-efficient option.
Component | Estimated Cost (in dollars) |
Elevator Car | $20,480 – $32,000 |
Traction Equipment | $12,800 – $20,480 |
Controls and Fixtures | $6,400 – $12,800 |
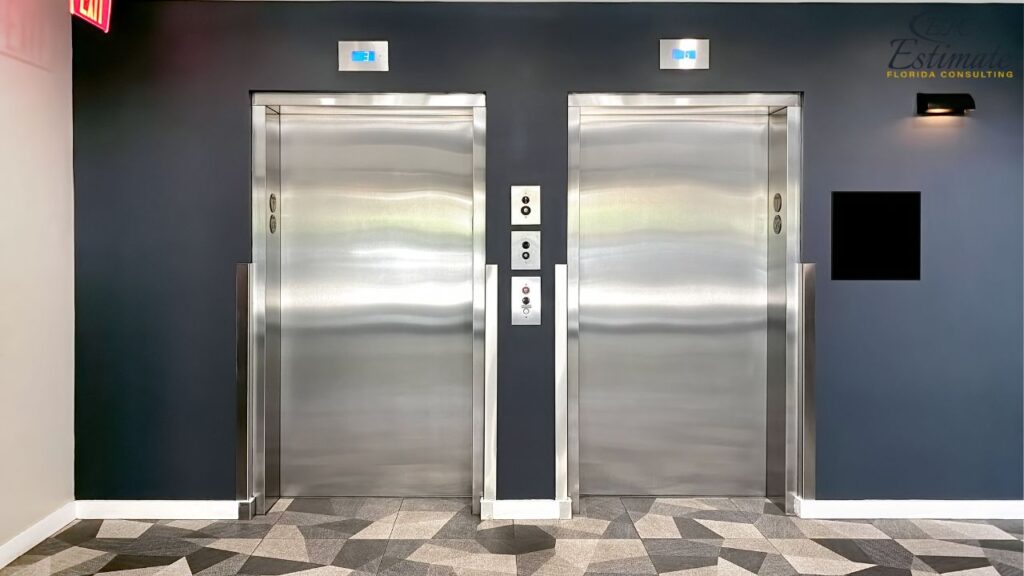
Traction elevators are known for their quiet operation and energy efficiency. These elevators use a counterweight system, eliminating the need for a machine room and making them a space-saving option. Their efficiency and performance make them a popular choice for commercial installations, particularly in buildings where space is at a premium. Traction elevators are ideal for high-rise buildings where speed and energy efficiency are critical, providing a reliable and swift means of transportation across multiple floors. The initial higher cost is often balanced by lower operational expenses due to their energy-efficient design. Their advanced control systems and safety features also contribute to a higher level of performance and reliability, making them suitable for demanding environments. Additionally, traction elevators have a longer lifespan and can handle higher traffic volumes, making them a cost-effective choice in the long run.
Pneumatic Elevators
Pneumatic elevators, or vacuum elevators, are easier to install and don’t require a machine room. They are usually less expensive but might not be suitable for all commercial applications.
Component | Estimated Cost (in dollars) |
Elevator Car | $15,360 – $25,600 |
Vacuum Pump System | $12,800 – $19,200 |
Controls and Fixtures | $7,680 – $12,800 |
Pneumatic elevators offer a modern and innovative design, making them a visually appealing addition to any building. Their ease of installation and lower cost make them a practical choice for many commercial properties, especially those looking to retrofit an existing space with minimal disruption. These elevators are suitable for buildings with lower traffic and height requirements, providing a sleek and efficient solution for vertical transportation. Their transparent cylindrical design can also serve as an architectural feature, adding aesthetic value to the property. The lower weight capacity and speed make them best suited for buildings with specific use cases that align with their capabilities. Additionally, pneumatic elevators are known for their minimal maintenance requirements, which can result in lower long-term costs. Their compact design also allows for easier installation in tight spaces, making them a flexible option for various building layouts.
Machine Room-Less (MRL) Elevators
Machine Room-Less elevators are ideal for buildings with limited space and are typically easier to retrofit into existing structures.
Component | Estimated Cost (in dollars) |
Elevator Car | $22,400 – $38,400 |
Drive System | $11,520 – $19,200 |
Controls and Fixtures | $8,960 – $15,360 |
Machine Room-Less elevators are compact and can be installed with minimal structural changes. They are perfect for small commercial buildings where space is a concern. These elevators provide an economical and efficient solution for enhancing accessibility without the need for extensive construction work. MRL elevators are increasingly popular due to their space-saving design and lower energy consumption, making them a sustainable and cost-effective option for modern buildings. Their integration into the existing structure without requiring a separate machine room translates to lower construction costs and faster installation times, offering significant advantages for both new constructions and retrofits. The compact design also allows for more flexible use of building space, maximizing the utility of available areas. Additionally, MRL elevators offer improved energy efficiency and reduced maintenance needs, further contributing to their overall cost-effectiveness.
Download Template For Elevator Project Breakdown
- Materials list updated to the zip code
- Fast delivery
- Data base of general contractors and sub-contractors
- Local estimators
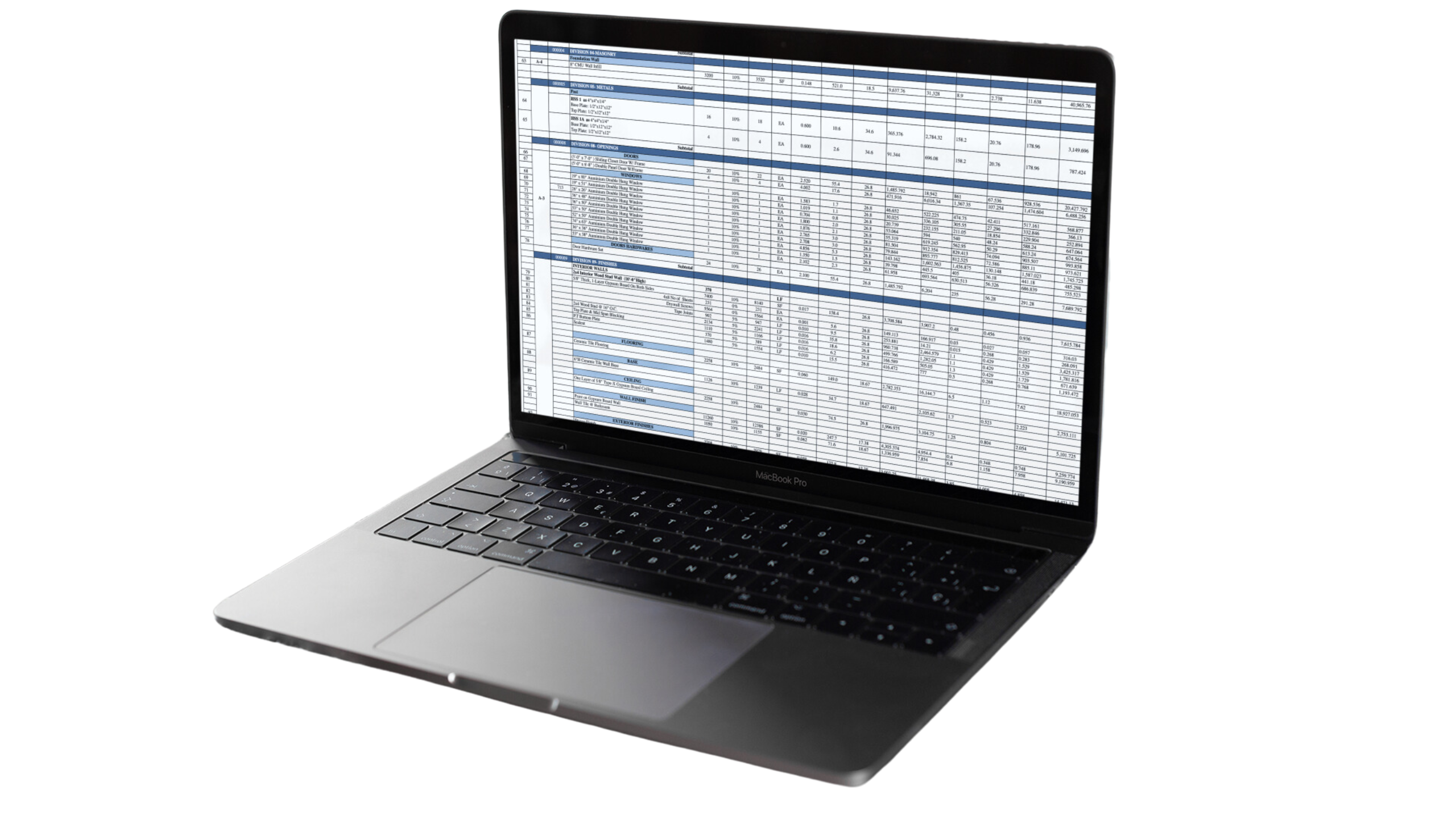
Installation Costs
Installation costs can vary based on the complexity of the project and the specific requirements of your building. Here’s a detailed breakdown of installation costs:
Basic Installation
Basic installation includes setting up the elevator, integrating it into your building, and ensuring it meets all safety standards.
Task | Estimated Cost (in dollars) |
Setup and Integration | $15,360 – $25,600 |
Testing and Safety Checks | $3,840 – $6,400 |
Basic installation involves the fundamental tasks required to get the elevator operational. This includes the physical installation of the elevator, integration with the building’s existing systems, and comprehensive testing to ensure safety and functionality. Proper installation is crucial for the long-term performance and reliability of the elevator. Engaging qualified professionals for the installation ensures adherence to all safety protocols and industry standards, thereby minimizing the risk of future operational issues. The involvement of experienced installers also helps in addressing any unforeseen challenges promptly, ensuring the project stays on schedule and within budget. Proper coordination with other building systems, such as HVAC and plumbing, is also crucial to avoid conflicts and ensure smooth integration.
Structural Modifications
Structural modifications might be necessary to accommodate the elevator, such as reinforcing floors or modifying walls.
Task | Estimated Cost (in dollars) |
Reinforcing Floors | $7,680 – $12,800 |
Modifying Walls | $7,680 – $12,800 |
Structural modifications ensure that the building can safely support the new elevator system. This can involve reinforcing floors to handle the additional weight or modifying walls to create the necessary space for the elevator shaft. These modifications are essential for the safety and stability of the installation. Addressing structural modifications early in the planning process can prevent delays and unexpected costs during installation, ensuring a seamless integration of the elevator into the building’s infrastructure. Proper structural modifications also enhance the overall durability and safety of the elevator system, providing peace of mind to building owners and occupants. Additionally, ensuring that all structural modifications comply with local building codes and regulations is essential for the project’s success.
Electrical Work
Electrical work is essential for powering the elevator and ensuring it operates safely and efficiently.
Task | Estimated Cost (in dollars) |
Wiring and Connections | $2,560 – $4,800 |
Electrical Panel Upgrades | $2,240 – $4,800 |
Electrical work involves connecting the elevator to the building’s power supply and ensuring that all electrical components are installed correctly. This includes wiring, connections, and any necessary upgrades to the electrical panel. Proper electrical installation is critical for the safe operation of the elevator and compliance with building codes. Ensuring that the electrical system is robust and capable of handling the elevator’s power requirements is crucial for preventing operational disruptions and ensuring long-term reliability. Additionally, implementing energy-efficient electrical components can reduce operational costs and enhance the overall sustainability of the building.
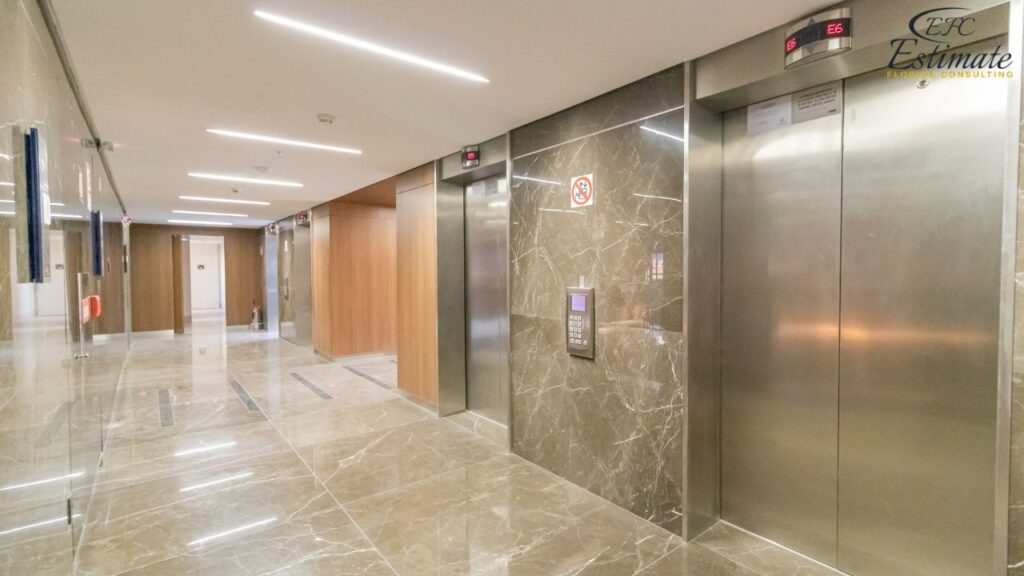
Proper electrical installation also includes integrating the elevator with the building’s emergency systems, such as fire alarms and backup power supplies, to ensure safety during power outages or emergencies.
Additional Costs
Installation costs can vary based on the complexity of the project and the specific requirements of your building. Here’s a detailed breakdown of installation costs:
Additional costs include permits, inspection fees, and a maintenance plan to keep the elevator in good working condition.
Additional Component | Estimated Cost (in dollars) |
Permits and Inspections | $1,200 – $2,400 |
Maintenance Plan (annually) | $1,920 – $3,840 |
Contingency Budget | $4,800 – $7,680 |
Permits and inspections are necessary to ensure that the elevator installation complies with local building codes and safety regulations. Regular maintenance is essential for the long-term reliability and safety of the elevator, covering routine inspections and necessary repairs. A contingency budget accounts for unexpected expenses that may arise during the installation process. Properly budgeting for these additional costs ensures that the project stays on track and avoids financial surprises, contributing to a smoother and more predictable installation process. These additional costs also ensure that the elevator remains compliant with regulatory standards, avoiding potential legal issues and fines. Planning for these costs upfront helps prevent budget overruns and ensures that all aspects of the installation are adequately covered. Additionally, having a contingency budget allows for flexibility in addressing any unexpected challenges that may arise during the project.
Factors Influencing the Cost of an Elevator in a 4-Story Building
Type of Elevator
The type of elevator you choose will significantly impact the cost. There are several types suitable for a 4-story building, each with its own features and installation requirements:
- Hydraulic Elevators: Common in low- to mid-rise buildings, these elevators require a machine room and are known for their smooth ride and reliability. They tend to be more expensive due to their complex installation. Hydraulic elevators use a fluid-driven piston to move the elevator car, providing a smooth and quiet operation, ideal for buildings where noise levels need to be minimized. They are particularly beneficial in environments such as residential buildings, libraries, and healthcare facilities where a quiet and smooth operation is critical. Additionally, hydraulic elevators can handle heavier loads and are relatively easy to maintain, making them a popular choice for various applications.
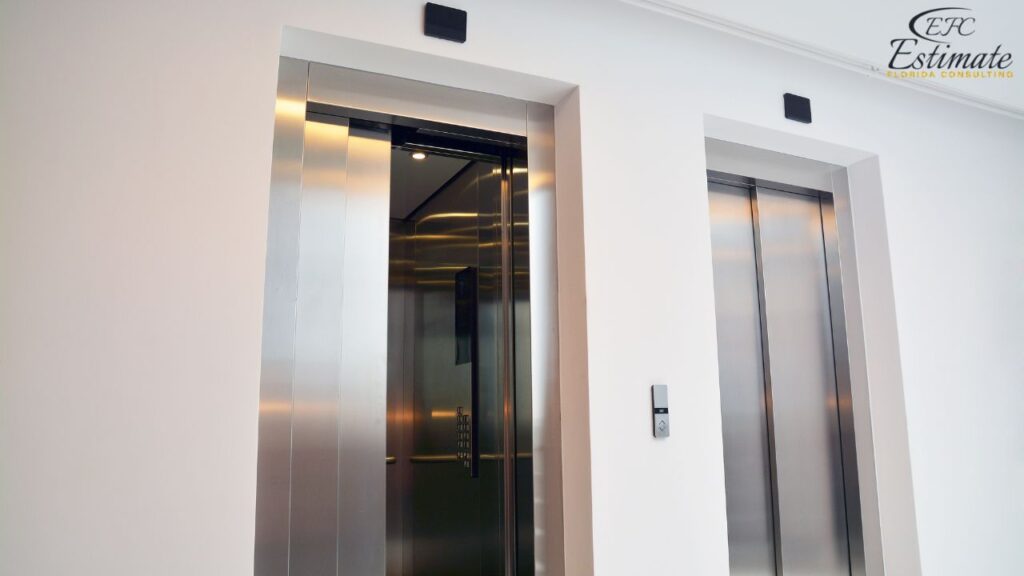
- Traction Elevators: Using a counterweight system, these elevators are more energy-efficient and faster than hydraulic ones, making them suitable for mid- to high-rise buildings. They are driven by electric motors and use steel ropes to lift the elevator car. Their high speed and energy efficiency make them a preferred choice for high-traffic commercial buildings like office complexes and hotels, where quick and reliable vertical transportation is essential. Traction elevators also offer a smoother ride and can reach higher speeds, which is advantageous for taller buildings. Furthermore, their efficient use of space and lower long-term operating costs contribute to their growing popularity.
- Pneumatic Elevators: These vacuum elevators are easier to install and don’t require a machine room. They are typically less expensive but may not be suitable for all applications due to capacity and speed limitations. Pneumatic elevators operate using air pressure to move the car, making them a modern and innovative choice that can be installed quickly with minimal structural modifications. They are ideal for smaller buildings or retrofits where space is limited and construction disruption needs to be minimized. Additionally, their transparent design can serve as an attractive architectural feature, enhancing the aesthetic appeal of the building. Pneumatic elevators are also known for their energy efficiency and low maintenance requirements, making them a cost-effective solution for specific applications.
- Machine Room-Less (MRL) Elevators: These elevators do not require a separate machine room, making them a space-efficient option. They are becoming popular in modern buildings due to their energy efficiency and smaller footprint. MRL elevators have the machinery located within the elevator shaft itself, saving space and reducing installation costs while offering performance comparable to traditional traction elevators. Their compact design allows for more flexible building layouts, making them suitable for a wide range of commercial applications, from retail stores to residential complexes. MRL elevators are also known for their quieter operation and improved energy efficiency, which can lead to lower operating costs over time.
Size and Capacity
The size and capacity of the elevator will also affect the cost. Larger elevators with higher weight capacities will generally cost more. For a 4-story building, a standard size typically supports 8-12 passengers or up to 2,500 pounds. The size and capacity not only impact the equipment cost but also the complexity of the installation and the amount of space required in the building. Larger elevators may also require more powerful motors and additional safety features, further increasing the cost. Ensuring the elevator is appropriately sized for its intended use is crucial for both cost efficiency and operational functionality.
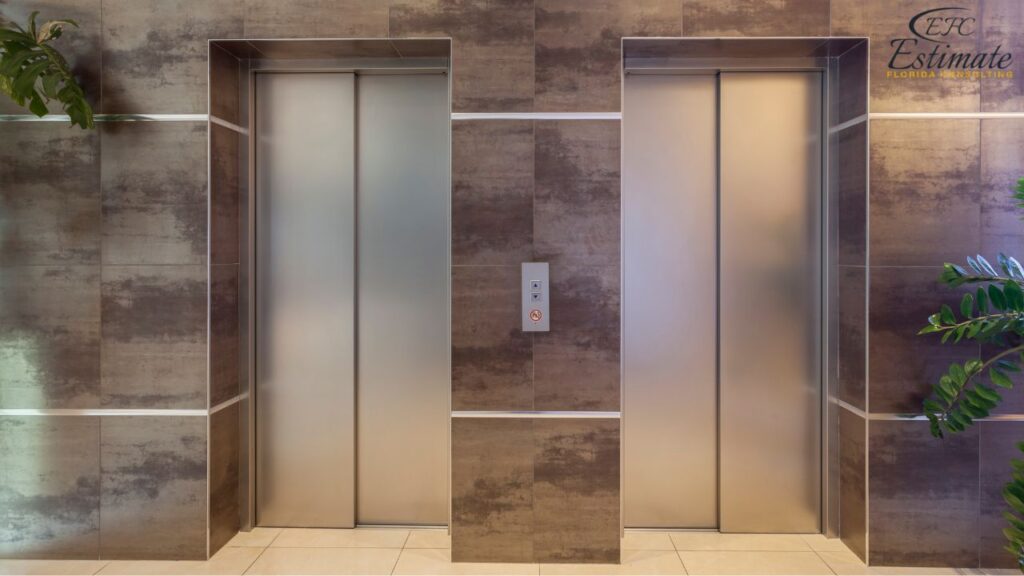
Additionally, the dimensions and layout of the building must accommodate the elevator without compromising other structural elements or functionalities. Properly sizing the elevator ensures that it can handle peak usage periods without causing delays or inconvenience to users.
Customization and Features
Custom features such as high-end cabin finishes, advanced control systems, and additional safety features will add to the cost. Customization can make the elevator blend seamlessly with the building’s decor but will increase the overall price. Features like automatic doors, custom lighting, and high-end materials can significantly enhance the look and functionality of the elevator. Customization options also include advanced safety features such as emergency lowering systems, backup power supplies, and sophisticated control interfaces. Investing in these features can provide long-term benefits, such as improved user experience, increased safety, and enhanced aesthetic appeal, making the elevator a standout feature of the building. Custom finishes like wood paneling, glass walls, and designer flooring can transform the elevator into a luxurious space, adding a touch of elegance that can elevate the overall ambiance of the building. Moreover, incorporating smart technology and automation can further enhance the elevator’s functionality and user convenience.
Installation Complexity
The complexity of the installation can significantly influence the cost. Factors such as structural modifications needed, the location of the elevator, and the difficulty of integrating it into the existing building layout will all play a role. Buildings with challenging layouts or older structures may require more extensive modifications. Installation complexity also affects the time required to complete the project, with more intricate installations potentially taking several weeks or months to finish. Proper planning and site assessment can help mitigate unexpected challenges and ensure a smoother installation process, ultimately saving time and costs. Coordination with other construction activities and minimizing disruptions to building operations are also crucial for a successful installation. Moreover, the necessity to comply with local building codes and regulations might require additional inspections and approvals, adding to the complexity and duration of the project. Ensuring that all stakeholders are involved in the planning process can help identify potential issues early and streamline the installation process.
Get 5 New Leads Next 7 Days With Our System
- Multi-Family House
- Single-Faimly House
- Modern House
- Duplex
- Ranch House
- Bungalow
Maintenance and Operating Costs
Ongoing maintenance and operating costs are important considerations. Regular maintenance ensures the elevator operates safely and efficiently, while operating costs include electricity and potential repair costs. Maintenance plans can help manage these expenses by providing regular service and addressing issues before they become significant problems. Understanding these recurring costs is crucial for long-term budgeting and ensuring the elevator remains a reliable part of the building. Investing in high-quality maintenance services can extend the lifespan of the elevator and prevent costly repairs, ensuring it remains in optimal condition and operates smoothly for years to come. Regular maintenance can also prevent unexpected downtime, which can be particularly disruptive in commercial settings. Additionally, investing in energy-efficient models can reduce long-term operating costs by lowering electricity consumption. Selecting an appropriate maintenance plan that includes routine inspections, emergency repairs, and system upgrades can provide peace of mind and ensure the elevator’s longevity.
Conclusion
The cost of installing an elevator in a 4-story building can range from $64,320 to $176,640, influenced by factors such as the type of elevator, installation complexity, and additional customization. Key expenses include the elevator unit, installation, permits, and necessary structural modifications. For a smooth and cost-effective installation, it is crucial to obtain multiple quotes, select a reliable installer, and plan for ongoing maintenance. A well-chosen elevator enhances accessibility and increases property value, making it a worthwhile investment. Careful planning and budgeting ensure a successful project that meets both functional and financial goals.
FAQs
The cost to install an elevator in a 4-story building typically ranges from $48,000 to $96,000, depending on the type of elevator, size, features, and installation complexity.
Key factors include the type of elevator, size and capacity, number of floors, customization and features, installation complexity, and ongoing maintenance and operating costs.
Different types of elevators have varying costs based on their design and functionality. Hydraulic elevators are generally more expensive due to their complex systems, while pneumatic elevators are typically less costly but may have limitations.
Larger elevators with higher weight capacities cost more due to the additional materials and more powerful systems required to support the increased load. For a 4-story building, a standard size typically supports 8-12 passengers or up to 2,500 pounds.
Each additional floor requires more equipment and installation work, increasing the overall expense. Elevators serving multiple floors will need more complex systems and additional materials.
Custom features such as high-end cabin finishes, advanced control systems, and additional safety features can increase the cost but provide enhanced aesthetics and functionality.
Google Reviews
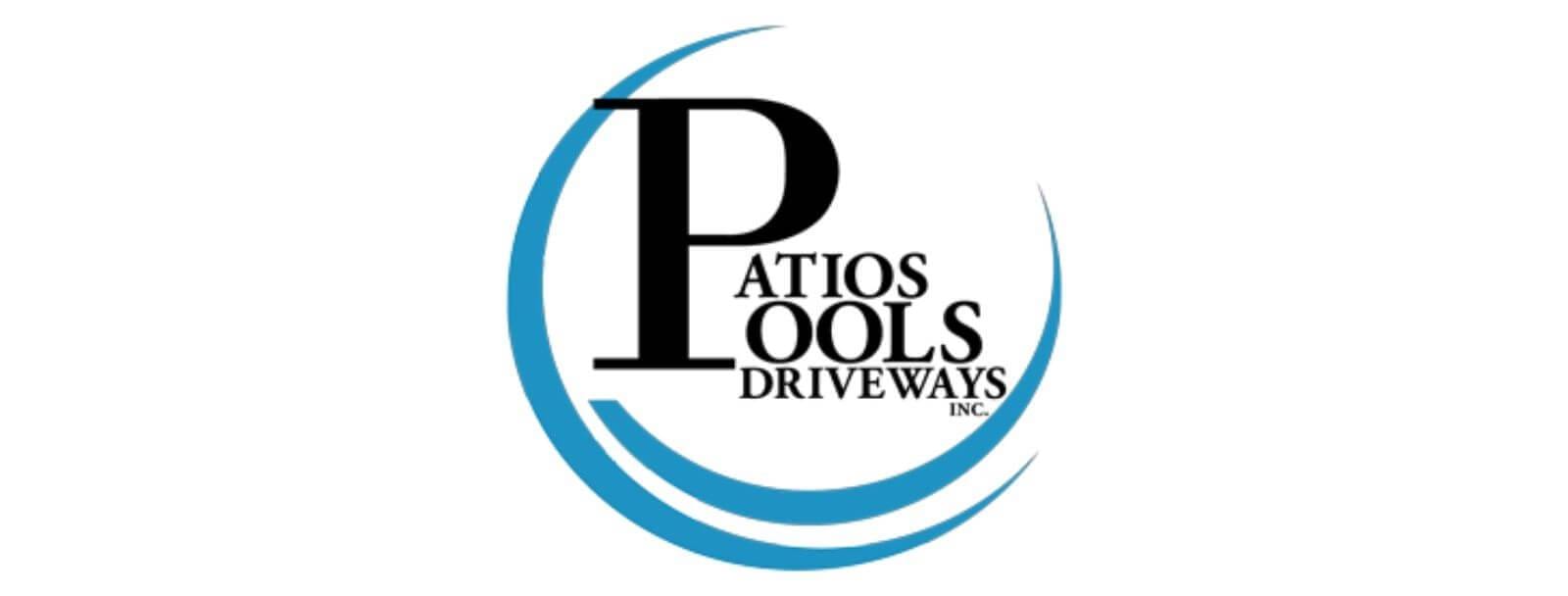
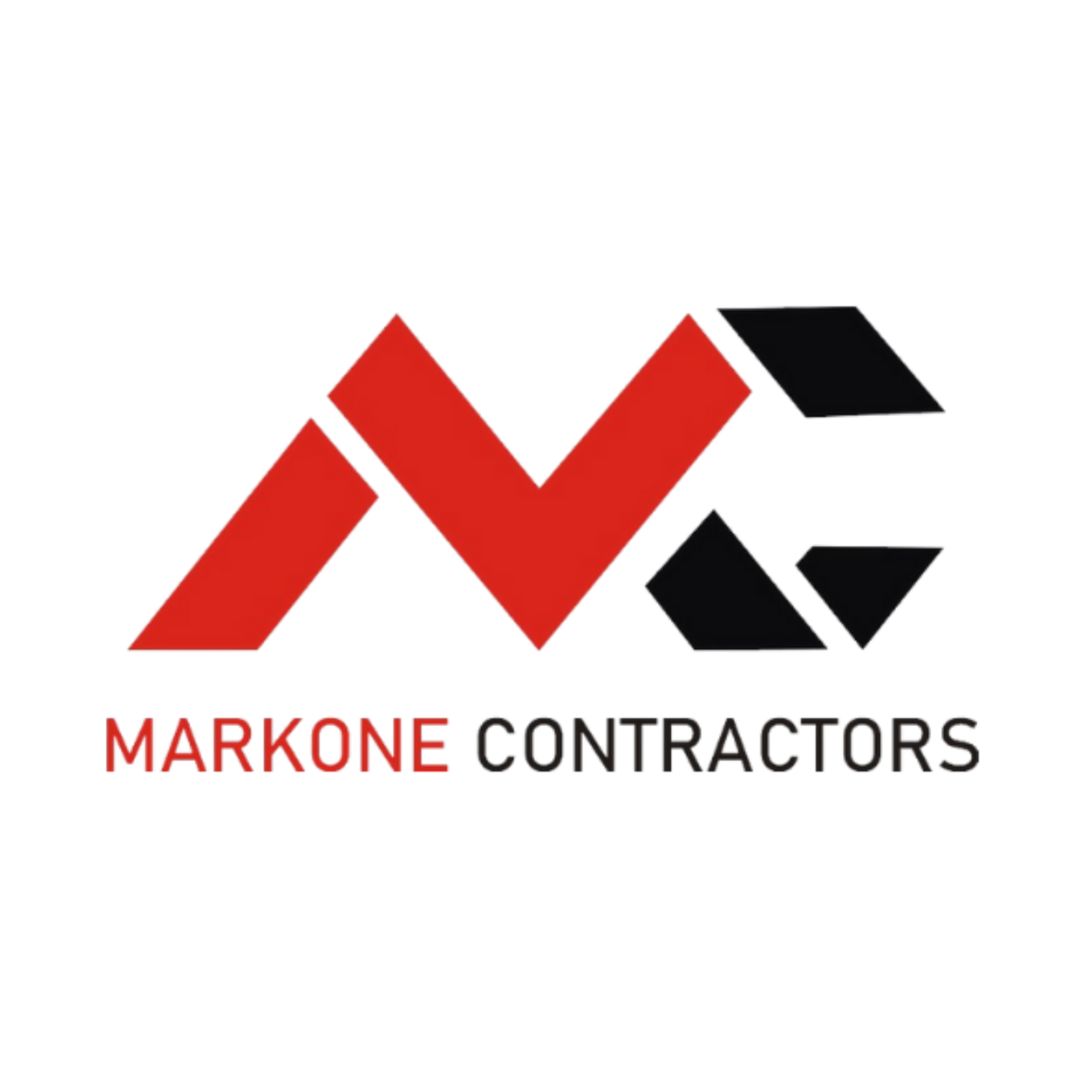

Process To Get Elevator Cost Estimate Report
Here I am going to share some steps to get elevator cost estimate report.
-
You need to send your plan to us.
You can send us your plan on info@estimatorflorida.com
-
You receive a quote for your project.
Before starting your project, we send you a quote for your service. That quote will have detailed information about your project. Here you will get information about the size, difficulty, complexity and bid date when determining pricing.
-
Get Estimate Report
Our team will takeoff and estimate your project. When we deliver you’ll receive a PDF and an Excel file of your estimate. We can also offer construction lead generation services for the jobs you’d like to pursue further.