Millwork Estimator
Millwork, which includes custom woodwork such as trim, molding, cabinetry, and other architectural elements, is an essential aspect of many construction and renovation projects. Whether you’re planning a residential renovation or a commercial build, understanding the costs associated with millwork is crucial for budgeting and planning.
In this blog, we will explore the various factors that contribute to the cost of millwork, providing detailed breakdowns and cost estimates to help you navigate your project effectively.
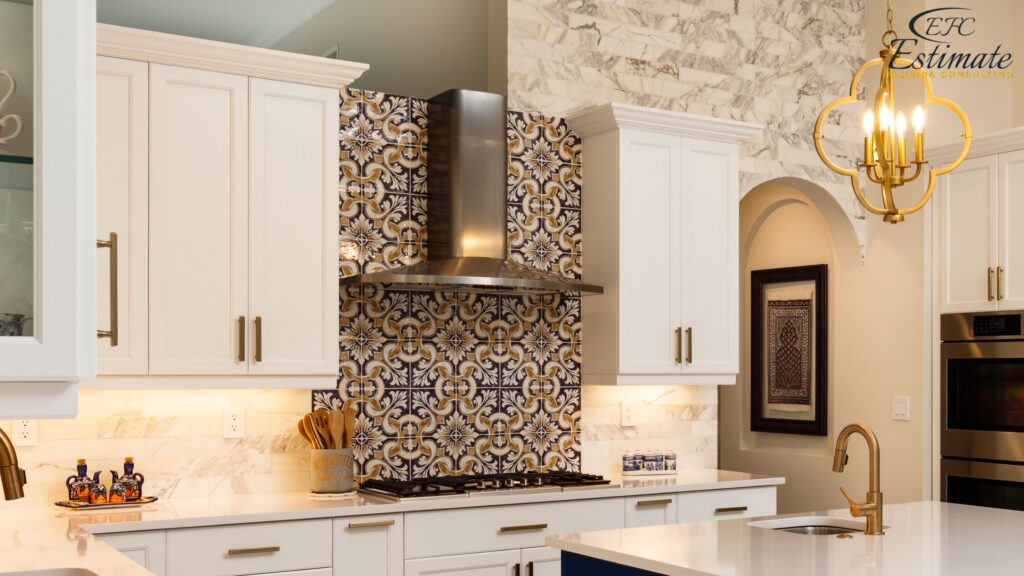
With this information, you can ensure a successful and cost-effective millwork project that enhances the aesthetic and functional value of your space, transforming your property into a unique and personalized environment that reflects your style and needs.
Average Cost Breakdown
The cost of millwork can vary widely based on several factors, including the type of wood, complexity of the design, and size of the project. On average, the cost of custom millwork can range from $4,200 to $70,000 or more for larger projects. Here’s a general cost breakdown:
Component | Estimated Cost (in dollars) |
Materials | $1,680 – $28,000 |
Labor | $2,100 – $35,000 |
Additional Costs | $420 – $7,000 |
Factors Affecting the Cost of Custom Millwork
Several factors can influence the cost of custom millwork, including:
Type of Wood
The type of wood used in the millwork can significantly impact the cost. Common types of wood used in custom millwork include:
- Pine: An affordable and versatile option, pine is often used for trim and basic cabinetry. It typically costs between $1,680 and $7,000 for a small to medium-sized project. Pine is easy to work with and takes paint well, making it a popular choice for various applications. Its affordability does not compromise its quality, making it an excellent choice for budget-conscious projects without sacrificing aesthetics.
- Oak: Known for its durability and attractive grain, oak is a popular choice for cabinets and furniture. Oak millwork can cost between $4,200 and $14,000. Oak’s strength and resistance to wear make it ideal for high-traffic areas and long-lasting installations. Its natural grain patterns add a touch of elegance and timeless appeal to any space.
- Maple: Maple is a hard, durable wood that is often used for high-end cabinetry and furniture. Maple millwork can range from $5,600 to $16,800. Its fine, uniform grain provides a smooth finish, which is perfect for both staining and painting. Maple’s versatility and durability make it suitable for various applications, from kitchen cabinets to custom furniture.
- Cherry: Cherry wood is prized for its rich color and smooth grain, making it a popular choice for luxury millwork. Cherry millwork can cost between $7,000 and $21,000. Over time, cherry wood darkens to a beautiful, deep hue, adding to its charm and elegance. The natural aging process of cherry wood enhances its appeal, making it a favorite for sophisticated and high-end projects.
- Mahogany: Known for its beauty and durability, mahogany is one of the more expensive options, with costs ranging from $8,400 to $28,000 or more. Mahogany’s rich, reddish-brown color and exceptional workability make it a premium choice for fine furniture and detailed woodwork. Its natural resistance to rot and pests also makes it a durable and long-lasting material for both indoor and outdoor applications.
Complexity of the Design
The complexity of the millwork design can also affect the cost. Simple, straightforward designs are less expensive than intricate, detailed work that requires more time and skill. For example, basic trim and molding may cost between $2,100 and $7,000, while custom cabinetry with detailed carvings and inlays can range from $14,000 to $42,000 or more. The level of craftsmanship and time required for complex designs significantly influences the overall cost. Intricate designs may involve additional labor for detailed carving, joining, and finishing, increasing both time and expenses.
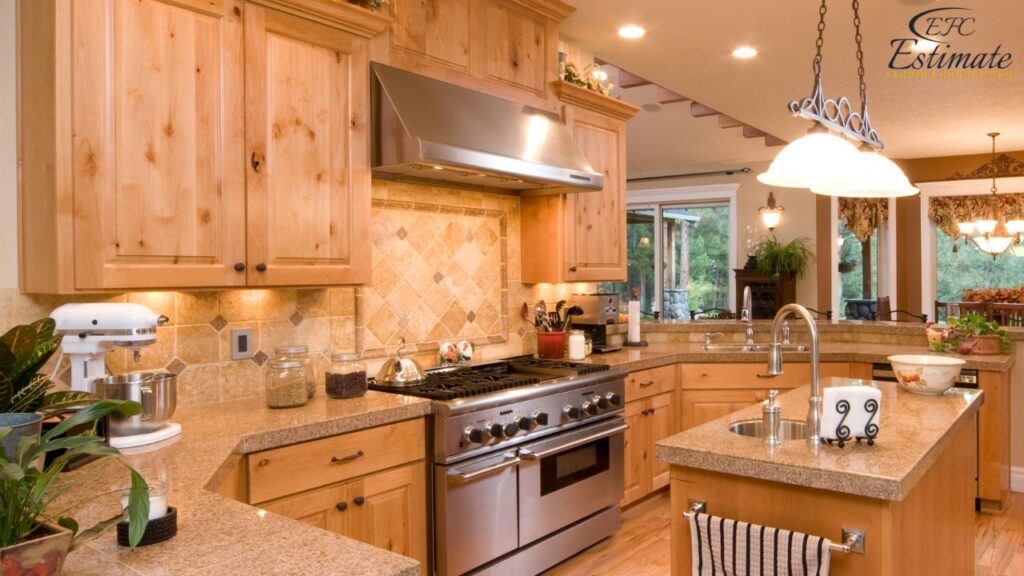
Detailed craftsmanship often requires specialized tools and techniques, contributing to the higher costs associated with complex designs.
Size of the Project
The size of the project is another major factor in determining the cost. Larger projects require more materials and labor, increasing the overall expense. For instance, a small millwork project for a single room may cost between $4,200 and $14,000, while a full-house millwork project could range from $28,000 to $70,000 or more. Accurate measurements and a clear understanding of the project’s scope are essential for obtaining precise cost estimates. Large-scale projects often involve coordinating multiple elements and ensuring consistency across various rooms or areas, adding to the complexity and cost. The scope of the project, including the number of rooms and specific requirements for each area, plays a crucial role in determining the overall cost.
Customization and Features
Adding custom features such as built-in lighting, soft-close drawers, or specialty finishes can increase the cost of the millwork. These features enhance the functionality and aesthetic appeal of the woodwork but also add to the initial investment. Custom features like intricate carvings, unique hardware, and specialized finishes can elevate the final look but require additional time and expertise to execute. Each customization adds a layer of complexity, making the project more labor-intensive and costly. Advanced features and customizations often involve specialized skills and materials, contributing to the higher costs.
Cost Breakdown by Component
Materials
The cost of materials includes the wood, hardware, finishes, and other necessary supplies. High-quality materials can increase the cost but provide better durability and appearance. Investing in premium materials ensures the longevity and beauty of the millwork, adding long-term value to your property. The choice of materials directly impacts the overall look and feel of the finished product, making it a critical aspect of the project.
Cost Breakdown for Materials:
Cost Component | Estimated Cost (in dollars) |
Wood (Pine, Oak, Maple, Cherry, Mahogany) | $1,680 – $21,000 |
Hardware and Accessories | $280 – $2,800 |
Finishes and Sealants | $280 – $4,200 |
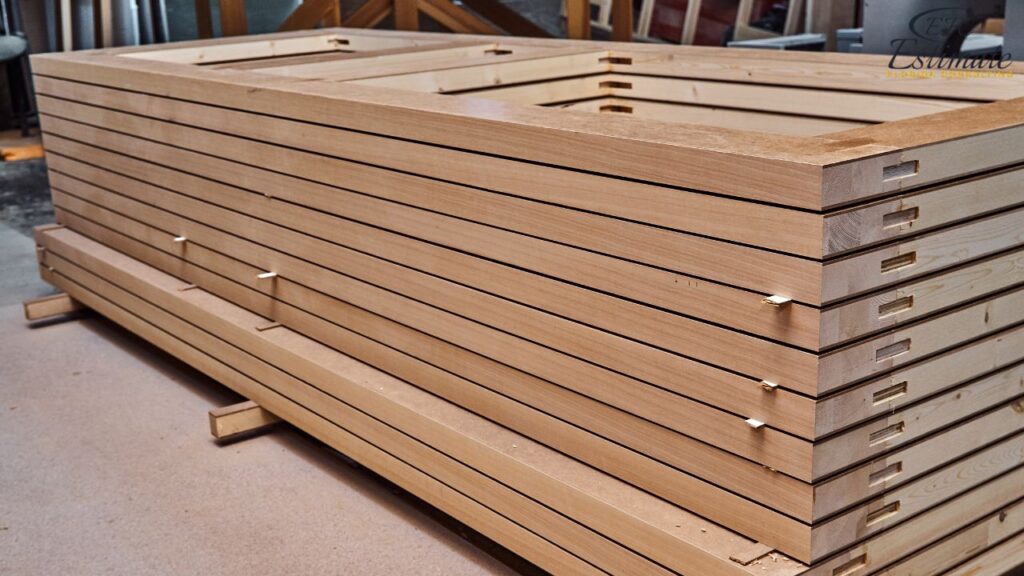
Labor
Labor costs include the time and expertise required to design, construct, and install the millwork. The total labor cost can vary based on the complexity of the project and the rates charged by local craftsmen. Skilled labor ensures the millwork is crafted and installed correctly, providing a high-quality finish. Experienced craftsmen bring a level of precision and artistry that enhances the final product, ensuring that every detail is executed to perfection. Hiring skilled labor is essential for achieving the desired quality and durability of custom millwork.
Cost Breakdown for Labor:
Cost Component | Estimated Cost (in dollars) |
Design and Drafting | $700 – $7,000 |
Construction | $1,120 – $21,000 |
Installation | $280 – $7,000 |
Download Template For Concrete Slab Project Breakdown
- Materials list updated to the zip code
- Fast delivery
- Data base of general contractors and sub-contractors
- Local estimators
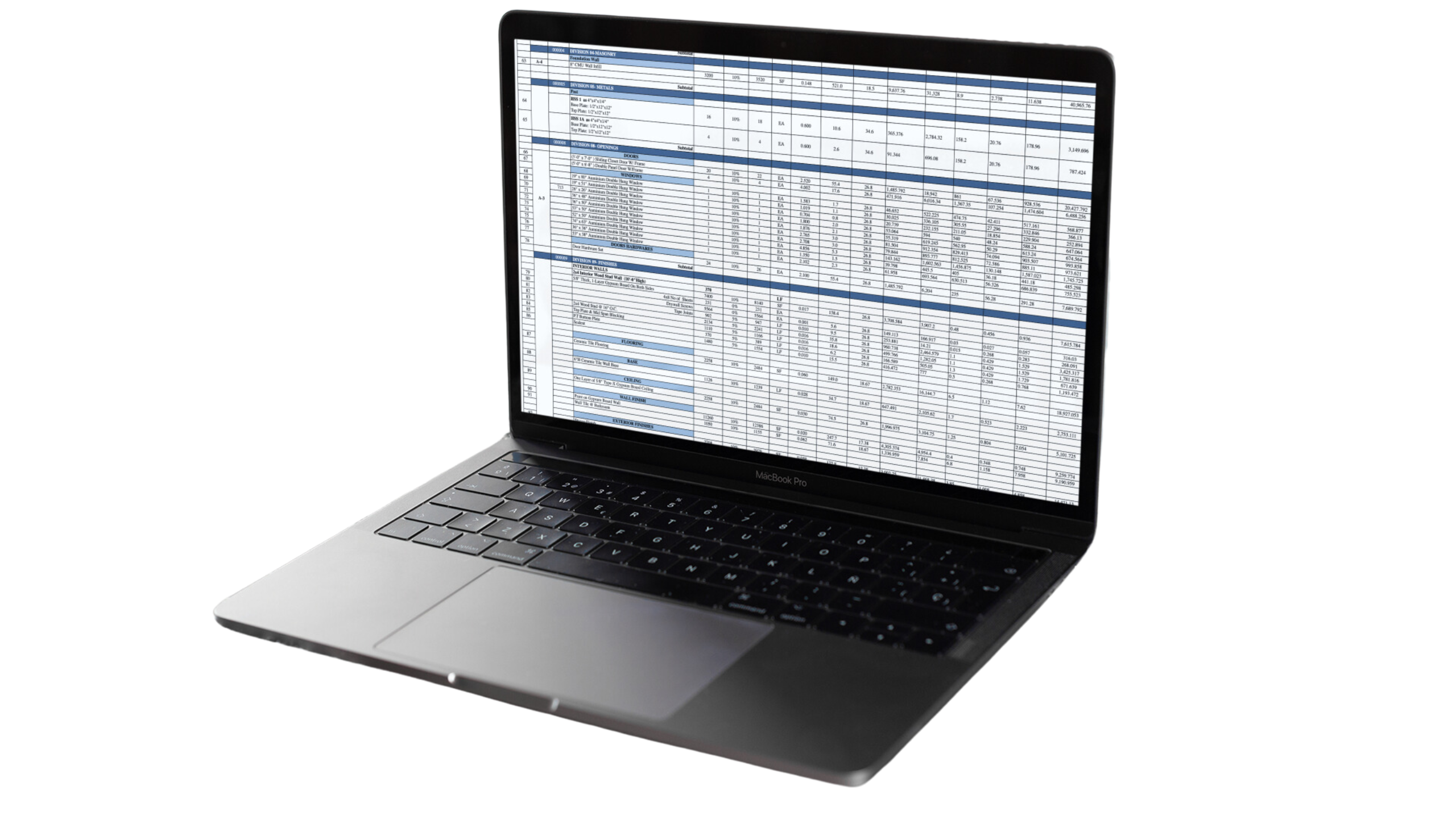
Additional Costs
Additional costs can include permits, inspections, delivery fees, and other related expenses. These costs can vary depending on local regulations and the specific requirements of the project. Planning for these expenses ensures that the project complies with all regulations and operates efficiently. Proper budgeting for additional costs helps avoid surprises and ensures the project stays within financial expectations. Including these costs in the initial budget helps ensure a smooth and successful project completion.
Cost Component | Estimated Cost (in dollars) |
Permits and Inspections | $140 – $1,400 |
Delivery and Handling | $140 – $1,400 |
Miscellaneous Expenses | $140 – $4,200 |
Using a Millwork Cost Estimator
A millwork cost estimator can help you plan and budget your project effectively. Here’s how to use it:
- Input Project Details: Enter the type, size, and scope of the millwork project to get a customized estimate. Accurate information ensures that the estimate reflects the specific needs of your project. Providing detailed information about the design and materials helps generate a more precise estimate. The more specific you are with your project details, the more accurate your estimate will be.
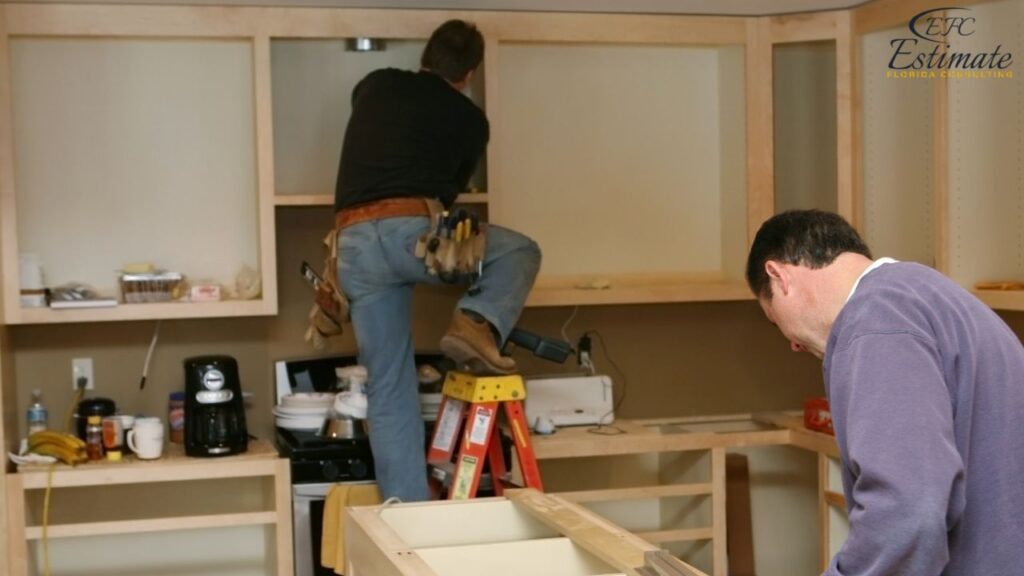
- Select Wood Type: Choose the type of wood you prefer, such as pine, oak, maple, cherry, or mahogany. The estimator will provide cost ranges based on the selected wood type. Understanding the characteristics and costs of different woods helps you make an informed decision that meets your aesthetic and budgetary requirements. Each type of wood has unique properties and price points, so choosing the right one for your project is crucial.
- Customize Features: Add any additional features or customization options to see how they affect the overall cost. This customization helps you balance initial costs with long-term value. Including advanced features like built-in lighting or specialized finishes can enhance the functionality and appearance of the millwork. Custom features can add significant value to your project but also increase the complexity and cost.
- Review Cost Breakdown: Review the detailed cost breakdown, including materials, labor, and additional costs. A clear breakdown helps you understand where your money is going and identify potential areas for savings. This comprehensive view allows you to make informed decisions and manage your budget effectively. Understanding the cost breakdown helps you prioritize spending and ensure you get the best value for your investment.
- Plan and Budget: Use the cost estimate to plan and budget your project, considering any additional costs such as permits and delivery fees. Proper planning ensures that you stay within your budget and avoid unexpected expenses. Thorough budgeting helps prevent financial surprises and ensures the project is completed successfully. A well-planned budget is essential for a smooth and stress-free project.
Example Cost Calculation
Let’s consider an example of custom millwork for a kitchen renovation project with cherry wood:
Component | Estimated Cost (in dollars) |
Materials | $9,800 – $21,000 |
Labor | $12,600 – $28,000 |
Permits and Inspections | $280 – $1,400 |
Delivery and Handling | $420 – $1,400 |
Miscellaneous Expenses | $700 – $2,800 |
Benefits of Custom Millwork
Investing in custom millwork offers several benefits:
- Aesthetic Appeal: Custom millwork can add elegance and sophistication to any space, creating a unique and personalized look. High-quality woodwork enhances the overall design and can become a focal point of a room. Whether it’s intricate crown molding or bespoke cabinetry, custom millwork elevates the visual appeal of your interiors, making them stand out with distinct character. The ability to tailor designs to your specific taste means your home or office can have a one-of-a-kind look that sets it apart from standard, mass-produced options.
- Increased Property Value: Quality millwork can increase the value of your property by adding custom features that appeal to potential buyers. Unique architectural details are often seen as a sign of craftsmanship and quality, making your property more attractive. Investing in high-quality millwork can yield a substantial return on investment, as these custom features can be a significant selling point in the real estate market. Potential buyers often appreciate the added charm and character that custom woodwork brings to a property.
- Functionality and Storage: Custom cabinetry and built-ins provide efficient storage solutions and improve the functionality of your space. Tailored to your specific needs, custom millwork can maximize storage and usability in ways that off-the-shelf solutions cannot. Custom storage solutions can be designed to fit your exact specifications, ensuring that every inch of space is utilized effectively, whether it’s in a kitchen, living room, or office. This tailored approach not only meets your storage needs but also complements the design of the room, blending functionality with aesthetics seamlessly.
- Durability: Custom millwork is typically made from high-quality materials and constructed by skilled craftsmen, ensuring it lasts for many years. The attention to detail and quality of materials used in custom millwork result in products that are built to withstand daily use and wear. High-quality craftsmanship ensures that your millwork not only looks beautiful but also stands the test of time, providing lasting value and durability. Investing in durable materials and expert craftsmanship means fewer repairs and replacements in the long run, saving you money and hassle.
Get 5 New Leads Next 7Days With Our System
- Multi-Family Building
- Hotel Building
- Hospital Building
- Warehouse Building
- High-Rise Building
- Shopping Complex
Conclusion
Investing in custom millwork is a significant decision that requires careful planning and consideration of various factors. The cost can vary widely depending on the type of wood, complexity of the design, size of the project, and additional features. By understanding these factors and using a millwork cost estimator, you can effectively plan and budget your project, ensuring a successful and cost-effective outcome. Investing in high-quality materials and professional craftsmanship can provide durable, beautiful, and functional millwork that enhances your property’s value and appeal. Proper planning and budgeting help ensure that your custom millwork project meets your expectations and provides lasting satisfaction.
Frequently Asked Questions (FAQs)
Millwork includes custom woodwork such as trim, molding, cabinetry, and other architectural elements essential to construction and renovation projects. It enhances both the aesthetic and functional value of spaces.
Several factors influence the cost of custom millwork:
- Type of Wood: Different woods (pine, oak, maple, cherry, mahogany) have varying costs.
- Complexity of Design: Simple designs cost less than intricate, detailed work.
- Size of the Project: Larger projects require more materials and labor.
- Customization and Features: Adding features like built-in lighting or specialty finishes increases costs.
The cost of custom millwork can range from $4,200 to $70,000 or more, depending on the project’s scope and complexity.
- Pine: $1,680 – $7,000
- Oak: $4,200 – $14,000
- Maple: $5,600 – $16,800
- Cherry: $7,000 – $21,000
- Mahogany: $8,400 – $28,000
Simple designs range from $2,100 to $7,000, while complex, custom cabinetry with detailed carvings can cost between $14,000 and $42,000 or more.
- Aesthetic Appeal: Adds elegance and sophistication.
- Increased Property Value: Custom features attract potential buyers.
- Functionality and Storage: Provides efficient storage solutions.
- Durability: Made from high-quality materials, ensuring longevity.
Google Reviews
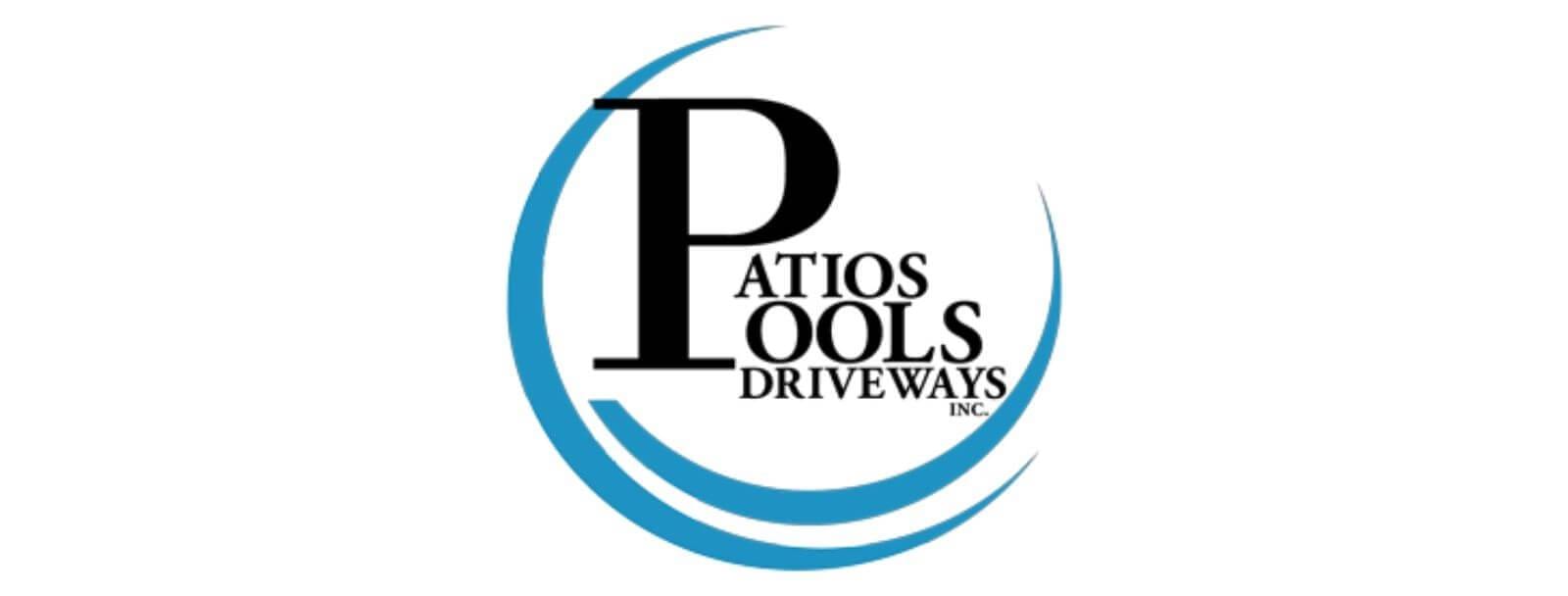
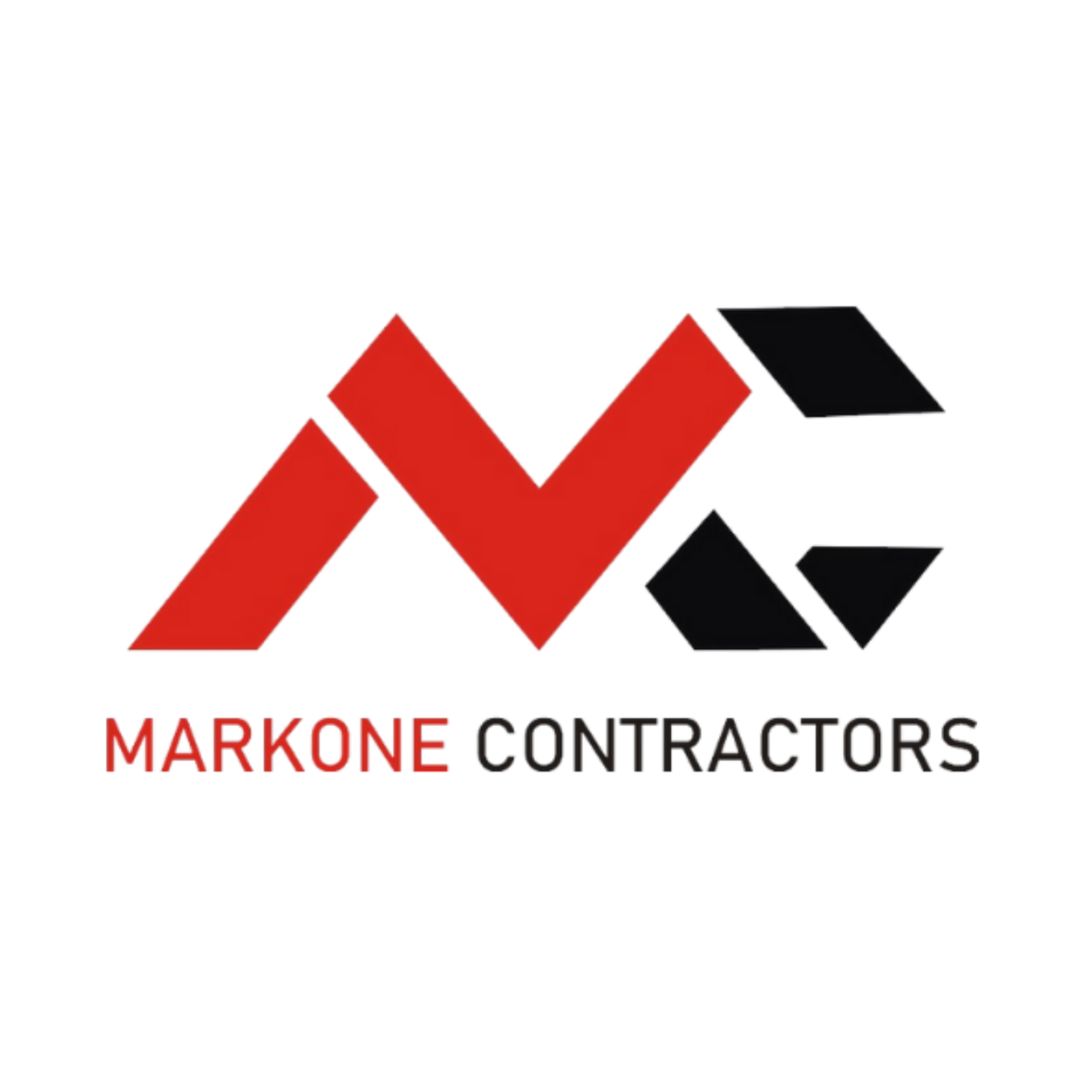

Process To Millwork Slab Cost Estimate Report
Here I am going to share some steps to get your millwork cost estimate report.
-
You need to send your plan to us.
You can send us your plan on info@estimatorflorida.com
-
You receive a quote for your project.
Before starting your project, we send you a quote for your service. That quote will have detailed information about your project. Here you will get information about the size, difficulty, complexity and bid date when determining pricing.
-
Get Estimate Report
Our team will takeoff and estimate your project. When we deliver you’ll receive a PDF and an Excel file of your estimate. We can also offer construction lead generation services for the jobs you’d like to pursue further.